Oxygen masks are critical in a variety of fields, including healthcare, aviation, and emergency services. Over time, advancements in materials and manufacturing processes have improved their functionality, comfort, and durability. Two key methods in oxygen mask production are traditional silicone compression and Liquid Silicone Rubber (LSR) injection molding. This essay explores the evolution of these manufacturing techniques, highlighting the advantages and challenges of each and their impact on the final product.
Traditional Silicone Molding: A Proven Method
Overview
Traditional silicone molding has long been a staple in oxygen mask manufacturing. This process typically involves manually pouring silicone into molds, allowing it to cure, and then trimming excess material. It is known for its simplicity and cost-effectiveness for low-volume production.
Advantages
- Flexibility in Small Batches: Traditional molding is well-suited for small production runs due to its low initial setup costs.
- Material Properties: Silicone is biocompatible, heat-resistant, and offers excellent flexibility, making it ideal for medical applications.
- Customization: The manual nature of the process allows for design adjustments and prototyping with relative ease.
Challenges
- Labor Intensity: Traditional silicone molding is labor-intensive, requiring skilled technicians to ensure precision.
- Inconsistent Quality: Manual processes often result in variations between products, leading to potential quality control issues.
- Production Speed: The curing time for silicone in traditional molds is longer, limiting scalability for high-demand situations.
The Shift to Liquid Silicone Rubber (LSR) Injection Molding
Introduction to LSR Technology
Liquid Silicone Rubber (LSR) injection molding is a more advanced manufacturing technique that has revolutionized the production of oxygen masks. LSR is a two-component material that is mixed and cured in a closed system, enabling high precision and automation.
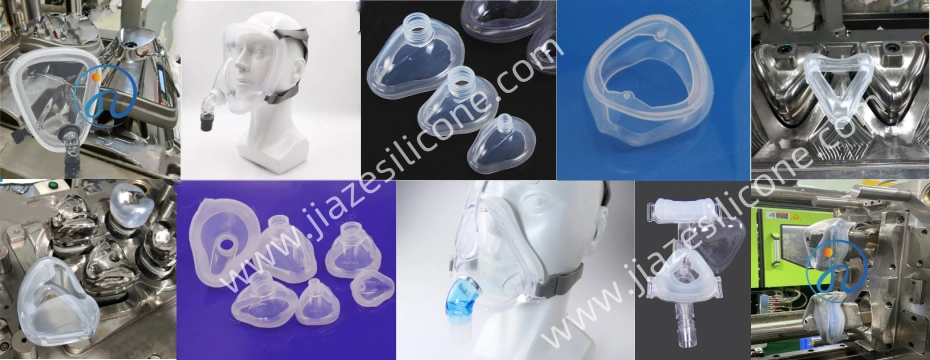
Advantages of LSR Injection Molding
- High Precision: LSR injection molding produces parts with tight tolerances and consistent quality, which is crucial for medical-grade oxygen masks.
- Scalability: The automated nature of the process allows for high-volume production, meeting the demands of global markets.
- Enhanced Durability: LSR materials are more resistant to wear, tear, and environmental factors than traditional silicone.
- Improved Comfort: LSR enables the creation of complex designs, such as ergonomic shapes and thinner profiles, enhancing user comfort.
- Automation: Reduced human intervention minimizes errors, increases efficiency, and lowers long-term labor costs.
- Environmental Benefits: The precision of the process reduces material waste, aligning with sustainable manufacturing practices.
Challenges
- High Initial Costs: Setting up LSR injection molding requires significant investment in specialized machinery and molds.
- Complexity of Design Changes: Modifying molds in LSR processes can be more time-consuming and expensive than traditional methods.
Comparative Analysis
Material Considerations
Both traditional silicone and LSR share many beneficial properties, such as biocompatibility and resistance to high temperatures. However, LSR’s enhanced physical properties, such as higher tensile strength and flexibility, give it an edge for demanding applications.

Manufacturing Efficiency
Traditional silicone molding is advantageous for low-volume or bespoke applications due to its lower upfront costs and design flexibility. Conversely, LSR injection molding excels in large-scale production, where speed, consistency, and automation are priorities.
Quality and Precision
For industries like healthcare and aviation, where precision is non-negotiable, LSR injection molding provides a significant advantage. Traditional molding may suffice for less critical applications but falls short in maintaining uniformity across large batches.
Cost Implications
While traditional silicone molding involves lower initial investment, its labor-intensive nature can increase per-unit costs for larger volumes. LSR injection molding, despite higher upfront costs, becomes more cost-effective over time due to automation and scalability.
Real-World Applications and Trends
Healthcare
In medical settings, where patient safety and comfort are paramount, the precision and hypoallergenic properties of LSR make it the preferred choice for oxygen mask manufacturing. LSR masks are often used in respiratory care devices and surgical settings.
Aviation and Emergency Services
In high-stakes environments, durability and reliability are critical. LSR injection molding ensures that oxygen masks meet stringent industry standards, withstanding extreme conditions without compromising functionality.
Sustainability
The emphasis on sustainable manufacturing is driving a shift toward LSR due to its lower material waste and energy efficiency during production.
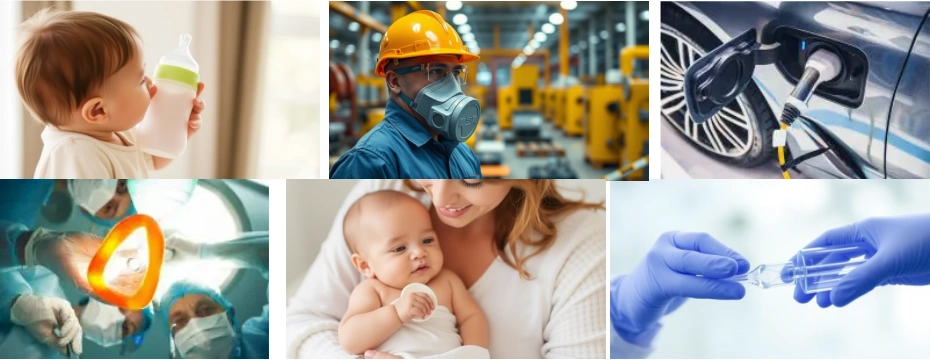
Future Outlook
The transition from traditional silicone molding to LSR injection molding is likely to accelerate with technological advancements and increasing demand for high-quality oxygen masks. Innovations such as 3D printing and smart manufacturing could further refine LSR processes, enhancing customization and reducing costs.
Additionally, the integration of antimicrobial properties and smart sensors into oxygen masks represents a growing trend. These advancements align with the capabilities of LSR injection molding, positioning it as the future of oxygen mask manufacturing.
Conclusion
The evolution of oxygen mask manufacturing reflects the broader trends in material science and industrial engineering. Traditional silicone molding laid the foundation, offering a reliable method for small-scale production. However, the advent of LSR injection molding has transformed the industry, enabling mass production of high-quality, durable, and comfortable oxygen masks. As industries continue to prioritize efficiency, precision, and sustainability, LSR injection molding stands out as the preferred method, meeting the demands of modern healthcare and safety applications.