In the realm of medical manufacturing
The question arises: Why Is Liquid Silicone Rubber (LSR) Ideal for Manufacturing Medical Parts? This article delves into the exceptional properties of LSR, highlighting its flexibility, durability, and biocompatibility. From superior resistance to chemicals and temperatures to its remarkable ability to maintain hygiene, LSR stands out as the premier choice for crafting reliable medical components.
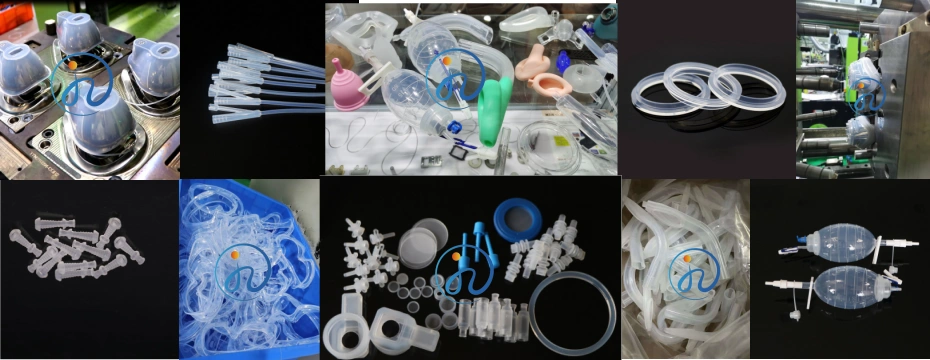
Moreover, we explore how LSR’s precision in molding and cost-effectiveness revolutionize production processes in the medical field. With a focus on sanitation, longevity, and compliance with stringent safety standards, LSR not only enhances the performance of medical devices but also ensures patient safety. Join us as we uncover the multifaceted advantages of using Liquid Silicone Rubber in medical applications.
Benefits of Liquid Silicone Rubber in Medical Parts
Superior Flexibility and Durability
Among the key benefits of Liquid Silicone Rubber (LSR) in medical production is its exceptional flexibility and resilience. LSR can stand up to a vast variety of temperatures and environmental conditions, making it excellent for various medical applications. Its elasticity guarantees that medical components made from LSR can withstand repeated use and anxiety without compromising their honesty.
Outstanding Chemical and Thermal Resistance
LSR displays superb resistance to chemicals, which is vital in the medical field where exposure to various materials prevails. Additionally, LSR’s thermal stability allows it to preserve its residential properties at both low and high-temperature levels, guaranteeing that clinical devices function reliably in diverse problems.
Openness and Colorability
An additional significant benefit is the transparency and colorability of LSR. This attribute is especially helpful for clinical tools that call for clear exposure of inner parts or fluid flow. Moreover, LSR can be easily colored to fulfill certain aesthetic or functional requirements, improving the general energy of clinical components.
Layout Versatility and Complex Geometries
LSR’s capability to be formed right into intricate geometries with high accuracy makes it a suitable material for manufacturing detailed clinical parts. This layout adaptability permits the production of components with comprehensive functions, which is vital for innovative medical tools.
Low Compression Set
LSR has a reduced compression set, suggesting it can return to its initial shape after compression. This residential property is especially important for clinical seals and gaskets that require preserving a limited seal in time to guarantee patient security and device effectiveness.
Data on Key Properties
Home | Worth |
---|---|
Temperature Range | -50 ° C |
to 200 ° C Prolongation Up to 1000% Hardness 20-80 Shore | |
A Compression Set( 5% Biocompatibility | |
and Safety of LSR | for Medical |
Applications When it concerns the manufacturing of clinical parts, the biocompatibility of products is of utmost relevance. Fluid Silicone Rubber( LSR) stands apart as a suitable choice because of its phenomenal compatibility with human tissue. This particular makes certain that LSR can be safely made use of in different medical applications, including implants, gaskets, and seals, without evoking negative reactions in the body. Understanding Biocompatibility refers to the capability of a product to carry out an ideal.
Precision and Consistency in LSR Medical Part Production
Among the most considerable advantages of using Liquid Silicone Rubber (LSR) in the production of medical parts is its unrivaled precision and consistency throughout the manufacturing process. The fundamental buildings of LSR permit for the development of extremely outlined and complex geometries that are typically called for in clinical applications.
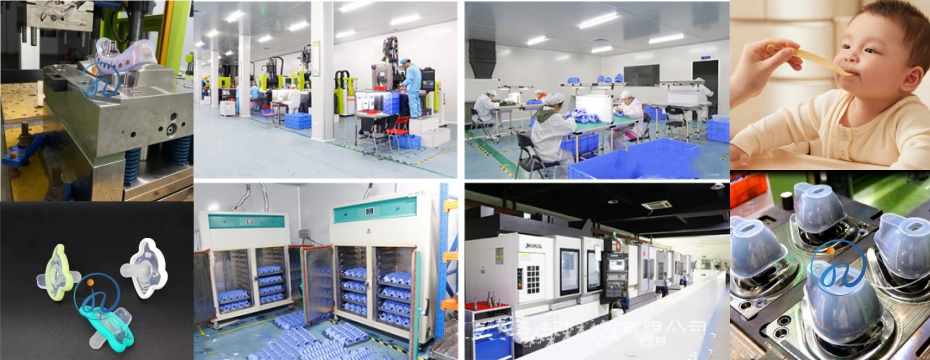
High Precision Molding
LSR is processed making use of advanced shot molding strategies that ensure each part is produced with amazing precision. The precision of LSR molding is critical for medical components, where also the smallest inconsistency can affect capability and security. This high degree of accuracy is attained via:
- Automated shot molding systems that minimize human error.
- Constant product flow and managed temperature settings throughout the treating process.
- Use of premium molds that are developed for detailed layouts.
Uniformity in Production
In enhancement to accuracy, LSR supplies exceptional consistency from batch to set. This is vital in the medical field, where harmony of components can influence the efficiency of medical gadgets. The uniformity in LSR manufacturing can be associated to:
- Stable product homes that stay unmodified across different manufacturing runs.
- Quality assurance actions that keep track of every stage of the manufacturing procedure.
- Ability to replicate styles with very little variation, making certain that each component meets the defined resistances.
Data on Precision and Consistency
The adhering table summarizes vital metrics that highlight the accuracy and uniformity of LSR in medical part manufacturing:
Metric | LSR Performance | Traditional Materials |
---|---|---|
Dimensional Tolerance | ± 0.01 mm | ± 0.1 mm |
Reproducibility Rate | 99.9% | 95% |
Cycle Time | 30-60 seconds | 60-120 secs |
These metrics illustrate that LSR not only meets but frequently exceeds the precision and consistency standards required in the clinical production sector. This ability makes LSR an excellent option for generating vital clinical components, ensuring that each component executes reliably in its desired application.
Sanitation and Hygiene Benefits of LSR Medical Parts
Boosted Sterilization Capabilities
One of the foremost benefits of Liquid Silicone Rubber (LSR) in medical manufacturing is its remarkable sterilization capabilities. LSR can withstand a variety of sterilization techniques, including autoclaving, gamma radiation, ethylene oxide (EtO) gas, and electron beam (e-beam) sterilization. This versatility guarantees that clinical components made from LSR can be extensively disinfected without compromising their structural stability or functionality.
Resistance to Microbial Growth
LSR is inherently resistant to microbial growth, making it an ideal material for clinical applications where hygiene is paramount. The non-porous nature of LSR protects against the absorption of fluids and the proliferation of germs, fungi, and other pathogens. This resistance to microbial development significantly reduces the threat of infections and contamination in clinical environments.
Alleviate of Cleaning
Clinical components made from LSR are remarkably simple to tidy and preserve. The smooth surface of LSR components allows for quick and effective cleansing, guaranteeing that no residues or contaminants remain. This convenience of cleansing is crucial in medical setups where preserving a sterile setting is important to client security and treatment.
Durability and Longevity
LSR medical parts are highly durable and can withstand repeated sanitation cycles without degrading. This durability ensures that the components preserve their hygiene standards with time, providing long-lasting reliability in clinical applications. The longevity of LSR parts also adds to cost-effectiveness, as they do not require to be changed often as a result of damage.
Compliance with Medical Standards
LSR fulfills rigorous medical requirements and policies, including ISO 10993 and USP Class VI. These certifications vouch for the product’s safety security and viability for medical use. Conformity with these standards guarantees that LSR medical parts are safe for use in various medical procedures and atmospheres, even more emphasizing their health advantages.
Cost-Effectiveness and Efficiency of Using LSR in Medical Manufacturing
In the realm of clinical production, the selection of materials significantly influences both the cost-effectiveness and the performance of manufacturing procedures. Liquid Silicone Rubber (LSR) stands apart as an excellent product due to its special buildings that promote streamlined production while maintaining high-quality criteria.
Scalability of Production
LSR manufacturing procedures are highly scalable, allowing producers to readjust production volumes according to market needs without incurring significant added costs. This adaptability is important in the clinical field, where product needs can fluctuate swiftly.
Uniformity and Quality Control
The fundamental properties of LSR facilitate constant manufacturing quality. The product’s accuracy in molding guarantees that each part satisfies rigorous medical standards, lowering the demand for substantial quality control procedures that can be expensive and taxing. Key elements consist of:
Quality Aspect | Advantage |
---|---|
Dimensional security | Decreases the requirement for modifications and revamp |
Uniformity | Makes sure trustworthy efficiency of clinical tools |
Long-Term Economic Benefits
Spending in LSR for medical manufacturing not only yields prompt cost savings but also offers long-term financial benefits. The toughness and longevity of LSR products add to minimized replacement prices and less regular need for maintenance, therefore boosting the general success of clinical manufacturing operations.
To conclude, the usage of Liquid Silicone Rubber in clinical production is not simply a matter of product selection; it is a calculated decision that affects the cost-effectiveness and operational performance of the entire manufacturing procedure. By leveraging the advantages of LSR, makers can attain far better economic end results while providing top-notch clinical items.