When designing and manufacturing baby food feeders, one of the most critical considerations is ensuring the highest safety, functionality, and quality standards. Liquid Silicone Rubber (LSR) injection molding has emerged as an optimal solution for producing these essential baby care products. Below, we delve into why LSR injection molding is the preferred manufacturing process for baby food feeders, considering its material benefits, process efficiency, and suitability for sensitive applications like baby products.
1. Superior Material Properties of LSR
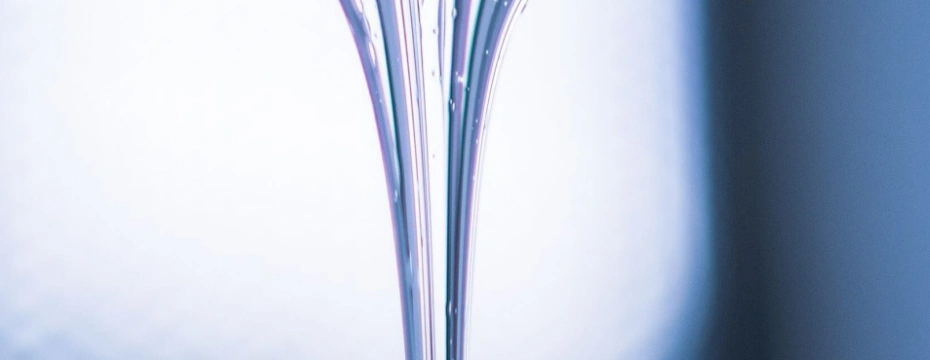
LSR (Liquid Silicone Rubber) is a high-performance elastomer that offers a unique combination of properties, making it ideal for baby food feeders:
a. Biocompatibility and Safety
- Non-toxic: LSR is free from harmful chemicals like BPA, phthalates, and other potential toxins. This is essential for products in contact with baby food and sensitive areas like a baby’s mouth.
- Hypoallergenic: The material is inert and does not react with food substances, ensuring no irritation or allergic reactions for babies.
- Medical-grade options: LSR is available in medical-grade formulations that comply with FDA and ISO standards for use in healthcare and baby products.
b. Durability and Flexibility
- High elasticity: LSR provides the flexibility needed for baby food feeders, ensuring comfort for infants during feeding.
- Temperature resistance: The material can withstand extreme temperatures (-50°C to 250°C), making it suitable for sterilization in boiling water or dishwashers.
- Tear resistance: It offers excellent tear strength, ensuring the product’s durability and longevity despite frequent use and cleaning.
c. Tasteless and Odorless
Babies are highly sensitive to odors and tastes. LSR does not retain or transfer any taste or smell, preserving the natural flavor of baby food.
2. Advantages of LSR Injection Molding
The manufacturing process plays a vital role in ensuring the quality and safety of baby food feeders. LSR injection molding offers numerous advantages over traditional manufacturing techniques.
a. Precision and Consistency
- High precision: The process allows for the creation of intricate designs and consistent dimensions, ensuring a perfect fit and function for every feeder.
- Repeatability: Automated injection molding guarantees uniformity across large production volumes, eliminating defects and inconsistencies.
b. Efficiency in Production
- Fast cycle times: LSR injection molding involves rapid curing times, enabling manufacturers to produce large quantities efficiently.
- Minimal waste: The process generates very little material waste, contributing to cost-effectiveness and environmental sustainability.
c. Design Versatility
LSR injection molding supports complex designs and features, including:
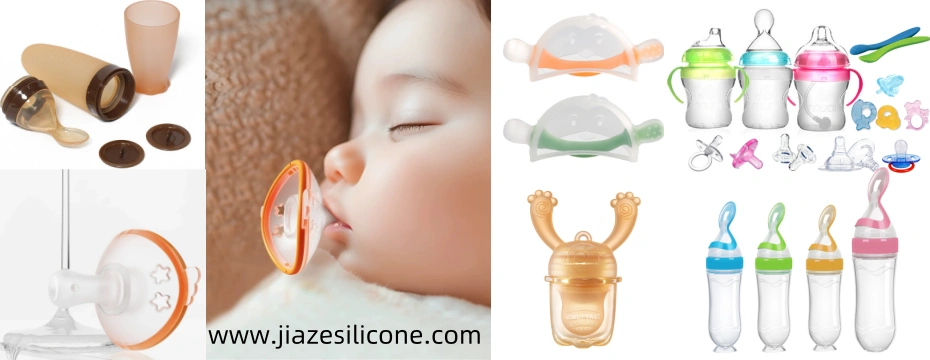
- Seamless construction for easy cleaning.
- Integrated soft-touch grips for ergonomic handling.
- Innovative shapes that enhance feeding experiences.
d. Scalability
The process is highly scalable, making it suitable for small batches of custom feeders or large-scale production to meet high market demands.
3. Hygiene and Cleanability
Maintaining hygiene is a top priority in baby care products. LSR and its associated molding process provide significant benefits in this regard:
a. Non-porous Surface
- LSR has a naturally non-porous surface, preventing the growth of bacteria, mold, and fungi. This is crucial for products in direct contact with food and a baby’s mouth.
b. Easy Sterilization
- Baby food feeders made with LSR can be sterilized through various methods, including boiling, autoclaving, and UV sterilization, without degrading the material.
c. One-piece Construction
- The injection molding process allows for the creation of one-piece designs without seams or joints, eliminating potential crevices where food residue or bacteria might accumulate.
4. Environmental Sustainability
As consumers become increasingly conscious of sustainability, LSR stands out as an eco-friendly choice:
- Long product lifecycle: LSR feeders are durable and resistant to wear, reducing the need for frequent replacements.
- Recyclability: LSR waste from manufacturing can often be recycled, contributing to a lower environmental footprint.
- Safe disposal: Unlike plastics, LSR does not release harmful toxins when disposed of or incinerated.
5. Enhancing Baby Safety and Comfort
Beyond functional benefits, LSR injection molding ensures baby food feeders meet the highest safety and comfort standards.
a. Soft and Gentle on Gums
- The flexible and soft texture of LSR is ideal for soothing teething babies and protecting delicate gums.
b. Ergonomic Designs
- LSR’s molding capabilities enable ergonomic shapes that are easy for parents and babies to handle, improving the overall feeding experience.
c. Customization
- Manufacturers can incorporate bright, baby-friendly colors or fun designs using FDA-compliant pigments, enhancing product appeal while maintaining safety.
6. Regulatory Compliance
Baby food feeders must comply with stringent safety regulations. LSR injection molding aligns seamlessly with these requirements:
- Compliance with FDA, LFGB, and other international standards for food-grade materials.
- Support for traceability and documentation, ensuring accountability in production.
7. Cost-Effectiveness for Manufacturers
While LSR may have higher upfront material and tooling costs compared to some alternatives, its long-term benefits outweigh initial expenses:
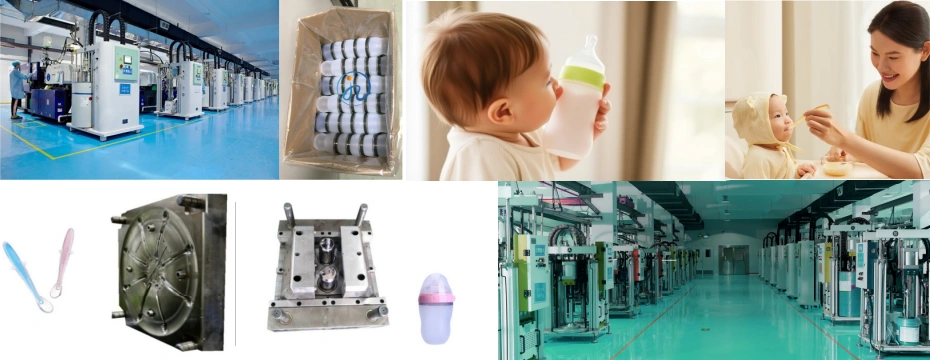
- Reduced defect rates: Automated molding ensures fewer rejects, minimizing wasted materials and costs.
- Lower maintenance costs: Durable molds and a clean production process reduce equipment wear and maintenance requirements.
- High-volume efficiency: For large-scale production, the per-unit cost of LSR feeders becomes highly competitive.
8. Market Trends and Consumer Preferences
With parents prioritizing safety and sustainability, LSR injection molding aligns perfectly with current market demands:
- Growing preference for silicone products: Silicone is increasingly favored over plastics for its non-toxic and eco-friendly properties.
- Rising demand for durable and reusable baby products: LSR feeders meet these needs, appealing to environmentally conscious consumers.
Conclusion
Choosing LSR injection molding for baby food feeders is a forward-thinking decision that benefits manufacturers, parents, and, most importantly, babies. The superior material properties of LSR—combined with the precision, efficiency, and scalability of the injection molding process—ensure the production of high-quality feeders that meet the highest safety, hygiene, and functionality standards. As market trends favor non-toxic, sustainable, and durable baby products, LSR injection molding remains the optimal manufacturing solution for baby food feeders.