This question delves into a fascinating realm of manufacturing technology that combines precision, versatility, and durability. Liquid Silicone Rubber (LSR) Injection Molding is a specialized process designed to produce high-quality silicone parts. From medical devices to automotive components, this technique offers unmatched performance and reliability.
Article Overview
In this article, we explore the intricate details of LSR Injection Molding, including its key characteristics, historical context, and how it compares to traditional injection molding. We also delve into the critical components of LSR injection molding machines, the step-by-step process, and the numerous advantages they offer. Additionally, we examine common applications, material considerations, challenges, and future trends in this ever-evolving field.
What is LSR Injection Molding?
Liquid Silicone Rubber (LSR) Injection Molding is a customized production procedure used to generate adaptable, sturdy, and high-precision silicone parts. This strategy includes infusing liquid silicone rubber right into a mold of dental caries under high stress and afterward healing it to form the wanted shape. The process is very automated and is recognized for its capability to create complex layouts with consistent top quality.
Meaning and Overview
LSR Injection Molding is a process where a two-component fluid silicone rubber is blended and injected right into a mold and mildew. The product is warmed and healed, resulting in a solid, versatile silicone part. This method is specifically appropriate for applications needing high accuracy, longevity, and resistance to extreme temperatures and chemicals.
Trick Characteristics
Some of the crucial characteristics of LSR Injection Molding consist of:
Characteristic | Summary |
---|---|
Product Properties | LSR is recognized for its adaptability, longevity, and resistance to extreme temperatures and chemicals. |
Precision | The process enables for the production of extremely complex and specific components. |
Automation | The procedure is extremely automated, which ensures regular high quality and lowers labor prices. |
Historic Context
The growth of LSR Injection Molding dates back to the mid-20th century when the requirement for high-performance materials in numerous sectors brought about the evolution of silicone rubber modern technologies. For many years, improvements in equipment and materials have actually made LSR Injection Molding a critical procedure in markets such as clinical gadgets, automotive, and consumer electronics.
Comparison with Traditional Injection Molding
While typical shot molding usually uses polycarbonate materials, LSR Injection Molding makes use of fluid silicone rubber, which offers distinctive advantages such as better heat resistance and flexibility. In Addition, LSR Injection Molding can produce parts with even more complex geometries and better details.
Trick Components of LSR Injection Molding Machines
Injection Unit
The injection unit is a vital part of LSR shot molding machines. It makes up a barrel, screw, and nozzle, which operate in unison to blend and infuse the fluid silicone rubber into the mold. The screw revolves around blending the LSR components extensively, making certain a regular and uniform product prior to it being infused.
Securing Unit
The clamping device is in charge of holding the mold and mildew securely in position during the shot process. It contains a fixed platen and a relocating platen, which close and open the mold and mildew. The securing force should suffice to counteract the shot pressure, ensuring that the mold continues to be closed and the LSR does not leakage out.
Mold and mildew
The mold is where the magic occurs. It is custom-designed to form the preferred form of the end product. The mold is usually made from high-grade steel to withstand the heat and pressures associated with the process. It contains 2 halves that come with each other to develop a dental caries, into which the LSR is infused. The mold and mildew also includes air conditioning networks to help solidify the LSR swiftly.
Metering Units
The metering devices are crucial for making sure the precise mixing of the two-part LSR product. These devices procedure and control the proportion of the silicone elements, making certain that the mix is precise and regular. This precision is crucial for keeping the top quality and efficiency of the end product.
Control System
The control system is the brain of the LSR injection molding maker. It takes care of and checks the whole procedure, from the blending of the LSR elements to the shot and curing phases. Advanced control systems use real-time surveillance and adjustments, guaranteeing optimal performance and product quality. They additionally offer valuable information for troubleshooting and process optimization.
Heater
The heating unit is responsible for maintaining the proper temperature level of the barrel and mold. Appropriate temperature level control is vital for the LSR to flow properly and heal correctly. The heating unit commonly consists of electric heaters and temperature level sensors that work with each other to keep the desired temperature level array.
Air conditioning System
The air conditioning system is equally essential as the heating unit. It assists in strengthening the LSR quickly as soon as it has been infused right into the mold and mildew. Cooling channels within the mold and mildew circulate coolant, typically water, to get rid of heat and increase the treatment process. Efficient air conditioning ensures much faster cycle times and boosts overall efficiency.
The LSR Injection Molding Process: Step-by-Step
Preparation
The initial step in the LSR Injection Molding process involves preparing the liquid silicone rubber (LSR) product. LSR is typically provided in two-part sets that are mixed with each other before molding. These parts are blended in an exact proportion to make certain the final item has actually the preferred homes. The mix is then fed into the injection molding machine.
Shot
Once the LSR product is prepared, it is infused into the mold and mildew. The injection unit of the machine is accountable for ensuring that the product is supplied to the mold at the right temperature level and pressure. This action is crucial as it establishes the top quality and uniformity of the shaped parts.
Mold and mildew Filling
During the mold and mildew loading phase, the LSR product is injected right into the mold dental caries. The style of the mold and the accuracy of the shot process make sure that the product fills up the dental caries entirely, without any kind of air bubbles or gaps. This is important for attaining premium, defect-free components.
Healing
After the mold and mildew are loaded, the LSR material goes through a curing process. The mold is heated up to a particular temperature level, which causes the LSR to cross-link and solidify. The treating time can vary depending on the product and the intricacy of the component being molded. Appropriate curing is essential for accomplishing the desired mechanical residential properties of the end product.
Air conditioning and Demolding
Once the LSR product has actually healed, the mold and mildew are cooled to a temperature level that enables the component to be safely eliminated. The cooling process has to be carefully managed to avoid any deformation or damage to the part. After cooling down, the mold is opened, and the completed component is expelled.
Post-Processing
In many cases, added post-processing actions might be required. These can consist of trimming excess material, doing top-quality evaluations, and using any kind of necessary surface treatments. Post-processing makes certain that the end product meets all specifications and is prepared for use.
Step | Description |
---|---|
Prep work | Blending the two-part LSR product in exact proportions. |
Injection | Delivering the mixed LSR material to the mold and mildew at the appropriate temperature level and pressure. |
Mold Filling | Ensuring the mold dental caries is totally filled up without air bubbles or gaps. |
Curing | Heating the mold to solidify the LSR material through cross-linking. |
Air conditioning and Demolding | Cool down the mold and safely remove the completed part. |
Post-Processing | Trimming, examining, and applying surface area therapies as needed. |
Advantages of LSR Injection Molding
High Precision and Consistency
One of the primary benefits of LSR injection molding is its capability to create parts with high accuracy and uniformity. The fluid silicone rubber (LSR) product flows conveniently right into mold and mildews, ensuring elaborate designs and tight tolerances are accomplished. This degree of accuracy is vital for applications needing precise requirements, such as medical devices and vehicle elements.
Convenience in Design
LSR injection molding supplies extraordinary style flexibility. The process sustains intricate geometries and can produce components with differing wall surface densities, damages, and elaborate information. This convenience permits the creation of cutting-edge and useful designs that might not be possible with other molding strategies.
Resilience and Performance
Components created through LSR injection molding are known for their durability and high efficiency. LSR exhibits superb resistance to extreme temperature levels, chemicals, and UV radiation, making it ideal for requiring atmospheres. Furthermore, LSR components preserve their properties gradually, ensuring long-lasting dependability and performance.
Biocompatibility
LSR is inherently biocompatible, making it an optimal product for clinical and healthcare applications. It is hypoallergenic, safe, and resistant to bacterial growth. This makes LSR shot molding a favored selection for making clinical gadgets, implants, and various other products that enter call with the body.
Short Cycle Times
The LSR injection molding procedure is defined by short cycle times, which converts to raised production performance. The fast curing of LSR enables faster mold and mildew cycles, reducing overall production time and expenses. This effectiveness is particularly helpful for high-volume manufacturing situations.
Cost-Effectiveness
While the first investment in LSR injection molding devices might be higher, the long-lasting expense benefits are considerable. The process minimizes product waste and reduces labor expenses due to its high degree of automation. Furthermore, the sturdiness and longevity of LSR components result in fewer replacements and upkeep, further adding to setback savings.
Ecological Benefits
LSR injection molding is an eco-friendly process. The product itself is safe and can be recycled. Additionally, the accuracy of the procedure decreases material waste, and the energy-efficient nature of modern-day LSR shot molding devices decreases the overall environmental footprint.
Common Applications of LSR Injection Molding
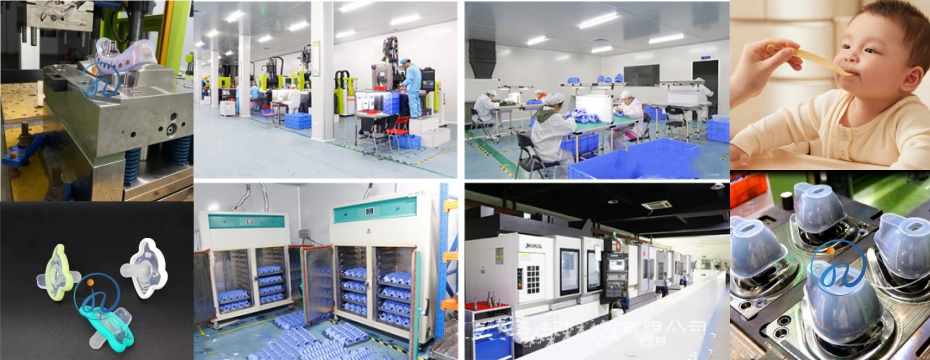
Medical Devices
Among the most substantial applications of LSR Injection Molding remains in the clinical industry. Because of its biocompatibility, LSR is extensively used of for manufacturing clinical tools and parts such as:
Medical Devices | Elements |
---|---|
Catheters | Seals and gaskets |
Respiratory masks | Valves |
Implants | Connectors |
Automotive Industry
The automobile industry benefits considerably from LSR Injection Molding as a result of the material’s longevity and resistance to severe temperatures. Usual applications consist of:
Automotive Parts | Components |
---|---|
Gaskets | Seals |
O-rings | Connectors |
Engine parts | Membrane layers |
Consumer Goods
In the durable goods field, LSR Injection Molding is prized for its adaptability and security. Typically molded things consist of:
Consumer Goods | Elements |
---|---|
Kitchenware | Hardware |
Infant items | Pacifiers |
Electronics | Keypads |
Electrical and Electronics
LSR Injection Molding is likewise essential in the electrical and electronic devices industries, mainly for parts that call for high precision and insulation in residential or commercial properties. Examples consist of:
Electrical and Electronics | Elements |
---|---|
Insulators | Connectors |
Sealers | Changes |
Keypads | Gaskets |
Industrial Applications
In industrial settings, the robustness and convenience of LSR Injection Molding make it perfect for different applications, such as:
Industrial Applications | Elements |
---|---|
Seals | Gaskets |
Valves | O-rings |
Hoses | Membrane layers |
Challenges and Solutions in LSR Injection Molding
Material Handling Challenges
Among the primary difficulties in LSR injection molding is the handling of the liquid silicone rubber itself. LSR is a two-component material that needs exact blending to guarantee uniformity and high quality. The elements must be kept and handled under specific conditions to avoid contamination and destruction.
Temperature Control
Maintaining the right temperature is vital throughout the LSR injection molding process. The material must be kept at a secure temperature level to prevent premature treatment, which can cause issues in the last product. Exact temperature level control in both the injection unit and mold and mildew is crucial.
Tooling Design and Maintenance
Tooling for LSR injection molding presents distinct obstacles due to the material’s reduced viscosity and high healing temperature levels. Mold layout should accommodate these variables to prevent flash and make certain proper airing vents. Routine maintenance is called for to maintain mold integrity and efficiency.
Cycle Time Optimization
Optimizing cycle time is crucial for maximizing effectiveness and minimizing costs. The curing time of LSR can vary based on component geometry and product formulation. Modifications in mold and mildew temperature level, shot speed, and stress are essential to accomplish ideal cycle times without compromising top quality.
Solutions to Challenges
Challenge | Option |
---|---|
Material Handling | Use automated systems for exact mixing and giving. |
Temperature level Control | Implement advanced temperature monitoring and control systems. |
Tooling Design | Style mold and mildews with proper airing vent and use high-grade materials. |
Cycle Time | Conduct thorough testing to discover the ideal equilibrium of criteria. |
Top quality Assurance
Guaranteeing constant top quality in LSR shot molding needs robust top quality guarantee protocols. Routine assessments and screening are essential to spot defects early and guarantee that the end products meet the needed specifications.
Training and Expertise
The complexity of LSR injection molding needs competent operators and designers. Continuous training and growth of personnel are important to address the advancing obstacles and innovations in the area.