This sophisticated manufacturing technique involves applying liquid silicone rubber overmolding substrates like plastics, metals, or other silicones. The process creates a robust, durable bond, combining the beneficial properties of both materials and making it invaluable in various industries.
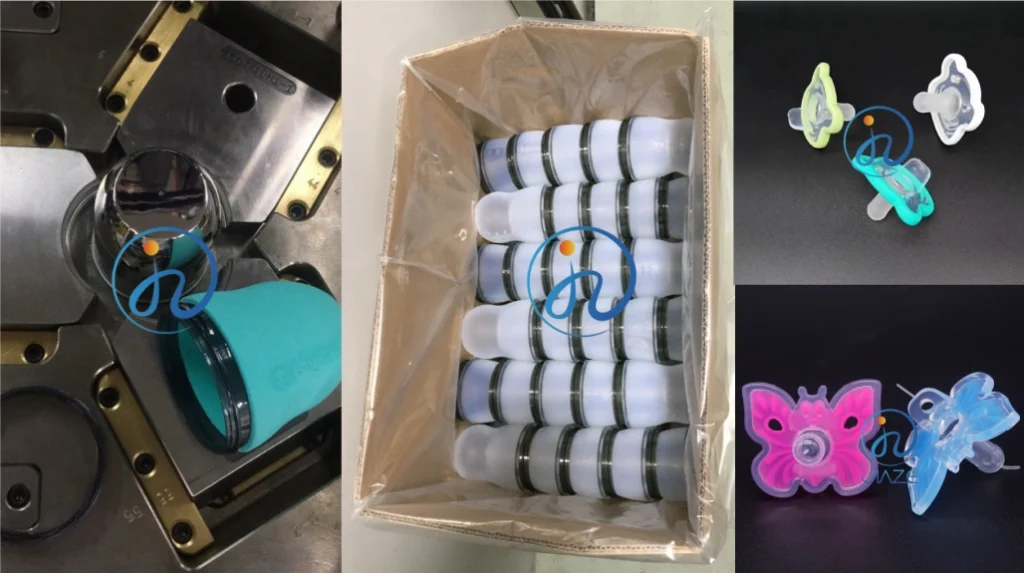
Overview of LSR Overmolding
In this article, we delve into the intricacies of LSR overmolding, exploring its key steps, material selection, and significant benefits.
Benefits of LSR Overmolding
- Enhances product performance
- Improves aesthetics
- Offers cost-effective solutions
- Provides environmentally friendly options
LSR overmolding stands out as a versatile and indispensable process in modern manufacturing.
Intro to LSR Overmolding
Fluid Silicone Rubber (LSR) overmolding is a sophisticated production strategy that involves the application of fluid silicone rubber onto a substratum, which can be composed of numerous materials such as plastics, steels, or various other silicones. This method is particularly valued for its ability to develop a solid, long-lasting bond between the LSR and the substrate, causing an item that integrates the helpful homes of both products.
Comprehending the Basics
Fundamentally, LSR overmolding is a two-step procedure. Originally, a substrate is generated, usually through shot molding or one more developing process. Following this, the substrate is placed right into a mold and mildew where liquid silicone rubber is infused onto or around it. The LSR then cures and strengthens, forming a natural system with the substrate.
Secret Characteristics of LSR Overmolding
Particular | Description |
---|---|
Product Compatibility | LSR can bond with a range of products, consisting of plastics, metals, and other elastomers. |
Resilience | The resulting bond is solid, resilient, and resistant to environmental aspects such as temperature level and chemicals. |
Flexibility | LSR maintains flexibility even after curing, making it optimal for applications needing flexibility. |
Accuracy | Overmolding permits specific control over the thickness and placement of the silicone layer. |
Significance in Modern Manufacturing
The importance of LSR overmolding in modern manufacturing can not be overstated. This procedure enables the development of facility, multi-material components that are else hard or difficult to generate. By leveraging the distinct buildings of liquid silicone rubber, makers can enhance the functionality, looks, and resilience of their products.
Common Industries Utilizing LSR Overmolding
Several industries often use LSR overmolding because of its flexibility and performance. These consist of:
- Automotive: For creating durable, heat-resistant components.
- Medical: For generating biocompatible and sterilizable tools.
- Consumer Electronics: For producing components that need exact, flexible seals.
- Industrial: For establishing elements that hold up against extreme environments.
Secret Benefits of LSR Overmolding in Manufacturing
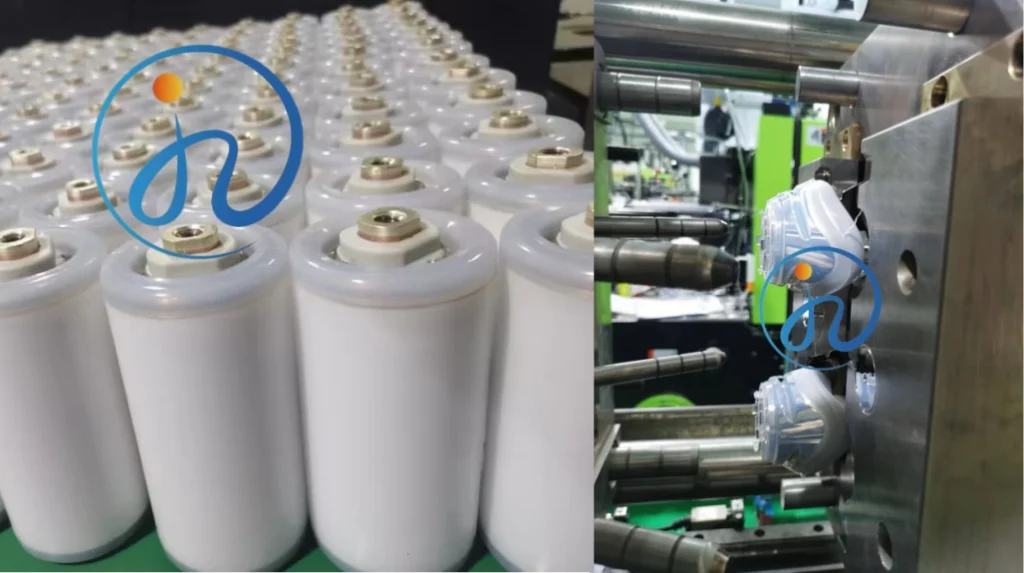
Improved Product Performance
One of the primary benefits of Liquid Silicone Rubber (LSR) overmolding is its capability to dramatically enhance the performance of products. LSR offers exceptional thermal stability, adaptability, and resistance to chemicals and UV radiation. These buildings make it a suitable selection for applications that require high longevity and reliability.
Enhanced Aesthetics and Ergonomics
LSR overmolding permits producers to produce products with superior aesthetics and ergonomics. The product can be molded into complex forms and layouts, providing smooth surfaces and vibrant shades. This not only enhances the visual allure of the items but likewise improves the user experience by giving a comfortable safe and secure grasp.
Cost-Effectiveness
Despite its high-performance characteristics, LSR overmolding can be a cost-efficient remedy for several producing needs. The procedure enables effective manufacturing cycles and decreased material waste. Furthermore, the longevity of LSR minimizes the need for frequent replacements, leading to long-lasting expense financial savings.
Flexibility in Applications
LSR overmolding is highly functional and can be used in a wide variety of applications across different sectors. From automobile and medical tools to customer electronics and family items, the adaptability of LSR makes it a valuable material for diverse manufacturing needs. This versatility makes certain that makers can fulfill particular demands and criteria for various items.
Enhanced Safety and Compliance
Security is an essential consideration in manufacturing, and LSR overmolding excels in this area. The material is biocompatible and hypoallergenic, making it ideal for clinical and food-grade applications. Furthermore, LSR follow stringent sector criteria and policies, guaranteeing that items are risk-free for end-users and fulfill quality criteria.
Ecological Benefits
In today’s eco-conscious world, the sustainability of production processes is more crucial than ever before. LSR overmolding supplies ecological benefits as a result of its recyclable nature and reduced power consumption during production. By choosing LSR, manufacturers can add to decreasing their ecological footprint and promote sustainable practices.
The Process of Liquid Silicone Rubber Overmolding
Fluid Silicone Rubber (LSR) overmolding is a sophisticated production process that entails the combination of 2 products to develop a single, cohesive product. This procedure is particularly valued for its capability to enhance the properties of the base material with the one-of-a-kind advantages of LSR. Listed below, I will certainly detail the crucial actions associated with the LSR overmolding procedure, along with crucial considerations to ensure optimal outcomes.
Mold Design and Preparation
The initial step in the LSR overmolding process is the design and preparation of the mold. This entails producing an accurate mold that can accommodate both the substratum (the base product) and the LSR. The mold should be made to make certain appropriate placement and fit of the two products.
Substrate Preparation
The substrate, or the preliminary component, needs to be thoroughly cleaned and prepared before the overmolding procedure starts. This action is essential to make sure that the LSR sticks correctly to the substratum, protecting against any type of defect or weak bonding.
Injection Molding
As soon as the mold and substrate are prepared, the LSR is injected into the mold and mildew utilizing a shot molding maker. This device specifically regulates the temperature level and pressure to ensure that the LSR flows uniformly and fills the mold and mildew completely. The shot process generally includes the adhering to stages:
Stage | Description |
---|---|
Shot | The LSR is infused into the mold and mildew tooth cavity. |
Holding | The LSR is held under pressure to make sure total dental filling and to get rid of air pockets. |
Cooling | The LSR is held under pressure to ensure total dental filling and to get rid of air pockets. |
Demolding
After the LSR has cooled and strengthened, the end product is thoroughly gotten rid of from the mold. This step requires precision to prevent harming the newly developed over-molded part. Unique treatment is taken to guarantee that the bond between the substratum and the LSR is undamaged.
Post-Processing
Once the element is demolded, it might go through extra post-processing actions such as trimming, examination, and testing. These steps are vital to ensure the high quality and performance of the overmolded item. Any type of excess material, referred to as flash, is removed, and the product is examined for defects.
Top quality Control
Quality control is an important element of the LSR overmolding process. Extensive screening and inspection are conducted to validate that the item meets all specs and performance requirements. This might consist of visual evaluations, dimensional checks, and useful screening.
Finally, the procedure of Liquid Silicone Rubber overmolding is a thorough and very controlled procedure that supplies many benefits in production. By complying with these steps, producers can develop high-quality, sturdy items that leverage the distinct properties of LSR.
Applications of LSR Overmolding Across Industries
Medical and Healthcare
Among the most considerable applications of Liquid Silicone Rubber (LSR) Overmolding remains in the clinical and healthcare field. The material’s biocompatibility, adaptability, and resistance to bacteria make it excellent for producing medical tools, such as catheters, syringe parts, and respiratory system masks. The overmolding process ensures that these devices are both comfortable for individuals and long lasting enough to endure repeated use and sterilization.
Customer Electronics
In the realm of customer electronics, LSR overmolding is used to enhance the resilience and comfort designs of different gadgets. For circumstances, it is frequently put to produce protective coverings and seals for smart devices, tablet computers, and wearable innovation. The soft-touch coating offered by LSR not only improves the individual experience but likewise provides exceptional shock absorption and resistance to ecological elements such as moisture and dirt.
Automotive Industry
The auto sector advantages greatly from the application of LSR overmolding. Parts such as gaskets, seals, and ports are typically produced utilizing this method to ensure they can stand up to extreme temperature levels and extreme conditions. In addition, LSR is utilized in the interior parts of lorries to offer a comfortable and cosmetically pleasing coating, such as on buttons, knobs, and takes care of.
Industrial and Mechanical Applications
LSR overmolding is additionally prevalent in industrial and mechanical applications. The product’s resistance to chemicals, oils, and extreme temperature levels makes it ideal for creating seals, gaskets, and other elements that are critical in production and equipment. This guarantees the long life and integrity of equipment, reducing downtime and maintenance prices.
Home Goods and Appliances
In the production of house goods and home appliances, LSR overmolding is utilized to develop components that are both functional and aesthetically pleasing. Products such as kitchen area tools, seals for dishwashing machines, and switches for various devices gain from the sturdiness and flexibility of LSR. This not only boosts the product’s lifespan but likewise improves user convenience and safety.
Aerospace and Defense
The aerospace and defense markets additionally utilize the advantages of LSR overmolding. Components utilized in these sectors should meet rigid criteria for efficiency and dependability. LSR’s capability to endure extreme conditions and its superb shielding buildings make it an ideal product for generating seals, gaskets, and safety covers used in airplanes and protection tools.
LSR Material Choices
LSR itself comes in various formulas, each customized to specific applications. Variables such as hardness, viscosity, and curing time has to be thought about. The table below outlines some common LSR kinds and their typical uses:
LSR Type | Common Uses |
---|---|
Requirement LSR | General-purpose applications, seals, gaskets |
Medical-grade LSR | Clinical tools, implants, wearables |
High-Temperature LSR | Automotive components, commercial elements |
Compatibility and Testing
Making certain the compatibility of the selected products is necessary. This involves extensive screening to review the bond in between the LSR and the substratum. Secret tests include:
- Peel Strength Test
- Shear Strength Test
- Thermal Cycling Test
These examinations assist in identifying the robustness of the bond under different functional problems. In addition, surface area therapies such as plasma or corona therapy can enhance the bond’s residential or commercial properties.
Ecological and Regulatory Considerations
Depending on the application, materials need to conform to environmental and regulatory requirements. For circumstances, medical-grade LSR needs to meet strict biocompatibility criteria, while automotive-grade LSR ought to stand up to severe temperature levels and chemical exposure.
Finally, the success of LSR Overmolding greatly depends on the careful selection of both the substratum and the LSR material. By recognizing the material’s residential or commercial properties, compatibility, and regulatory demands, makers can guarantee the production of top notch, long-lasting over-molded products.
What are the benefits of LSR overmolding in manufacturing?
LSR overmolding offers numerous benefits, including:
- Enhanced product performance with excellent thermal stability, flexibility, and resistance to chemicals and UV radiation.
- Improved aesthetics and ergonomics with smooth finishes and vibrant colors.
- Cost-effectiveness due to efficient production cycles and reduced material waste.
- Versatility in applications across various industries.
- Enhanced safety and compliance with biocompatibility and hypoallergenic properties.
- Environmental benefits due to its recyclable nature and low energy consumption during production.
How does LSR overmolding enhance product performance?
LSR overmolding enhances product performance by providing excellent thermal stability, flexibility, and resistance to chemicals and UV radiation. These properties make it ideal for applications demanding high durability and reliability.
What are the environmental benefits of using Liquid Silicone Rubber overmolding?
LSR overmolding offers environmental benefits due to its recyclable nature and low energy consumption during production. By choosing LSR, manufacturers can reduce their environmental footprint and promote sustainable practices.
How do you ensure the compatibility of materials in LSR overmolding?
Ensuring material compatibility involves rigorous testing to evaluate the adhesion between the LSR and the substrate. Key tests include Peel Strength Test, Shear Strength Test, and Thermal Cycling Test. Surface treatments like plasma or corona treatment can enhance adhesion properties.
What are the key considerations for mold design in LSR overmolding?
The mold must be designed to ensure proper alignment and fit of both the substrate and the LSR. Precise mold design is crucial for achieving optimal results and preventing defects or weak bonding.