Liquid Injection Molding (LIM) is a manufacturing process that produces high-quality, precision rubber and silicone parts by injecting a two-part liquid silicone rubber (LSR) into a mold. Here, we’ll go through the LIM process, its materials, equipment, applications, and benefits, along with some comparisons to related processes.
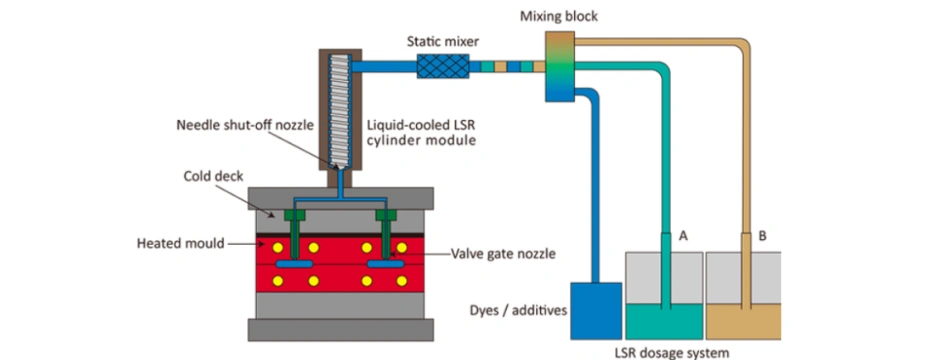
1. Overview of LIM Process
The LIM process involves:
- Material Preparation: Mixing two-part liquid silicone components (typically labeled A and B). The components mix just before injection, creating a chemical reaction that causes the silicone to cure or solidify within the mold.
- Injection and Curing: The liquid silicone mixture is injected into a heated mold cavity under pressure. This controlled environment helps ensure that the material flows smoothly into intricate molds and cures evenly.
- Mold Release and Demolding: Once cured, the part is released from the mold. Special mold-release agents or self-lubricating materials may be used to facilitate easy removal.
2. Materials Used in LIM
The primary material in LIM is Liquid Silicone Rubber (LSR), a versatile and durable elastomer with unique properties like heat resistance, flexibility, and biocompatibility. LSR typically comes in a two-part formulation: Part A contains the base polymer and a platinum catalyst, while Part B contains a cross-linking agent. These components stay stable until mixed, allowing for controlled curing.
Key features of LSR:
- High-temperature stability: LSR can withstand extreme temperatures, making it ideal for automotive and aerospace applications.
- Flexibility and resilience: Even after repeated stretching, LSR maintains its original shape and flexibility.
- Biocompatibility: LSR is often used for medical and food-grade products because it’s hypoallergenic, non-toxic, and complies with various regulatory standards.
- Chemical resistance: It resists degradation from UV light, ozone, and many chemicals, extending the lifespan of LSR products.
3. LIM Equipment and Setup
The LIM process requires several specialized pieces of equipment:
- Injection Molding Machine: This machine injects the mixed silicone material into the mold cavity. It includes an injector, barrel, and mixing head, where the components mix before injection.
- Mixing and Metering System: This system accurately measures and mixes the two-part LSR components. Consistent, precise mixing is essential to maintain product quality and cure times.
- Temperature-Controlled Mold: LIM molds are usually made from durable metals like stainless steel or aluminum to withstand high temperatures and ensure consistent curing.
- Clamping System: The mold must be kept under pressure during curing to prevent air bubbles and ensure complete filling of complex mold geometries.
4. LIM Process Phases
The LIM process follows four main phases:
- Mold Preparation: The mold is preheated to ensure the liquid silicone cures quickly.
- Injection: The mixed LSR is injected under high pressure into the mold cavity. The mixture flows into every detail of the mold, capturing intricate designs.
- Curing: The mold remains closed as the silicone cures. This can take seconds to minutes, depending on the part’s thickness and complexity.
- Demolding and Post-Processing: After curing, the mold opens, and the part is removed. Some parts may require minimal post-processing, like trimming, to remove excess material (flash).
5. Benefits
LIM offers numerous advantages, particularly in industries that require precision, durability, and complex design elements.
- High Precision and Detail: LIM allows for the creation of intricate shapes, thin walls, and tiny features, which are critical for medical devices, seals, and other detailed components.
- Consistency: Automation ensures consistent part quality and repeatability, with tight tolerances achievable in each production cycle.
- Reduced Waste: The precise injection of LSR minimizes material wastage, making it a more environmentally friendly option.
- Fast Production Cycles: Automated LIM processes allow for high-speed production, which is essential for large-scale manufacturing.
6. Applications
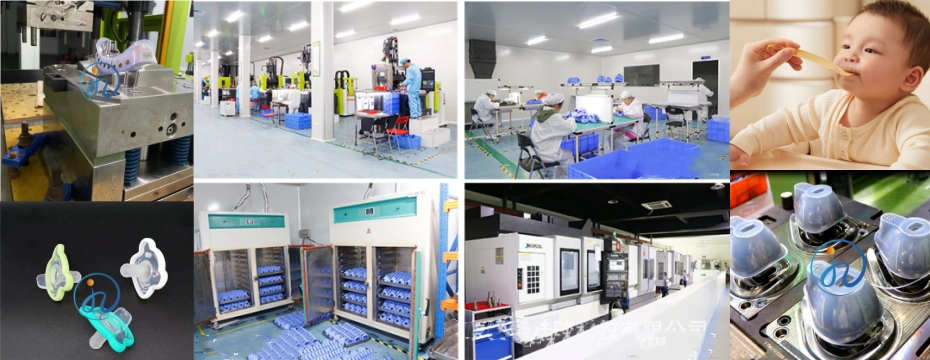
- Medical Devices: LIM is ideal for biocompatible parts like catheters, valves, syringes, and seals. The materials used in LIM are safe for contact with human tissue, and the process meets stringent hygiene and regulatory standards.
- Automotive and Aerospace: LSR parts like gaskets, seals, and shock absorbers are essential in vehicles and aircraft because they withstand temperature extremes and resist wear.
- Consumer Electronics: LIM is used in buttons, keypads, gaskets, and waterproof seals for phones, laptops, and cameras.
- Food and Beverage: LSR’s food-grade quality makes it suitable for kitchenware, bottle nipples, and other items that come in contact with food and drink.
7. Challenges and Considerations
Despite its benefits, LIM has some challenges, particularly in its initial setup and specific production requirements.
- Equipment and Material Costs: LIM machinery and LSR materials can be expensive, requiring a significant upfront investment.
- Expertise Needed: Operators need training to handle the precision of LIM equipment and control the injection and curing parameters.
- Flash and Trimming: While flash is minimal in LIM, intricate parts may require trimming, adding a small amount of post-processing time and labor.
8. Comparison with Other Molding Techniques
LIM shares similarities with other molding processes but stands out due to its specific benefits for silicone parts.
- Injection Molding: Both LIM and traditional injection molding involve injecting material into a mold, but LIM is specialized for liquid silicones, which are mixed and cured differently than thermoplastics.
- Compression Molding: Compression molding is an alternative for rubber products, but it’s slower and less precise than LIM, which is ideal for complex shapes and high-volume production.
- Transfer Molding: This process can handle rubber-like materials, but LIM’s automation and precision make it preferable for large-scale production of intricate silicone parts.
9. Environmental Considerations
LIM is environmentally friendly because it produces minimal waste and energy-efficient parts. The process uses precise injection, reducing excess material, and modern LIM machines often have energy-saving features. Additionally, LSR parts are durable and long-lasting, decreasing replacement frequency and material consumption.
Conclusion
Liquid Injection Molding is an advanced, highly efficient technique for producing high-quality silicone rubber parts. Its applications range from medical devices to automotive components, making it invaluable in industries that demand precision, durability, and complex geometries. As technology advances, LIM is likely to continue evolving, with new materials and methods broadening its applications and enhancing its efficiency.