In the realm of hearing technology, the benefits of using Liquid Silicone Rubber (LSR) in hearing components are profound. This versatile material not only enhances comfort and acoustic performance but also ensures durability and biocompatibility. This makes it an ideal choice for modern hearing aids.
Advantages of LSR
As we delve deeper into the advantages of LSR, we uncover its exceptional flexibility, longevity, and cost-effectiveness. From improved acoustic properties to innovative manufacturing techniques, paving the way for future advancements in hearing technology.
Benefits of Using Liquid Silicone Rubber (LSR) in Hearing Components
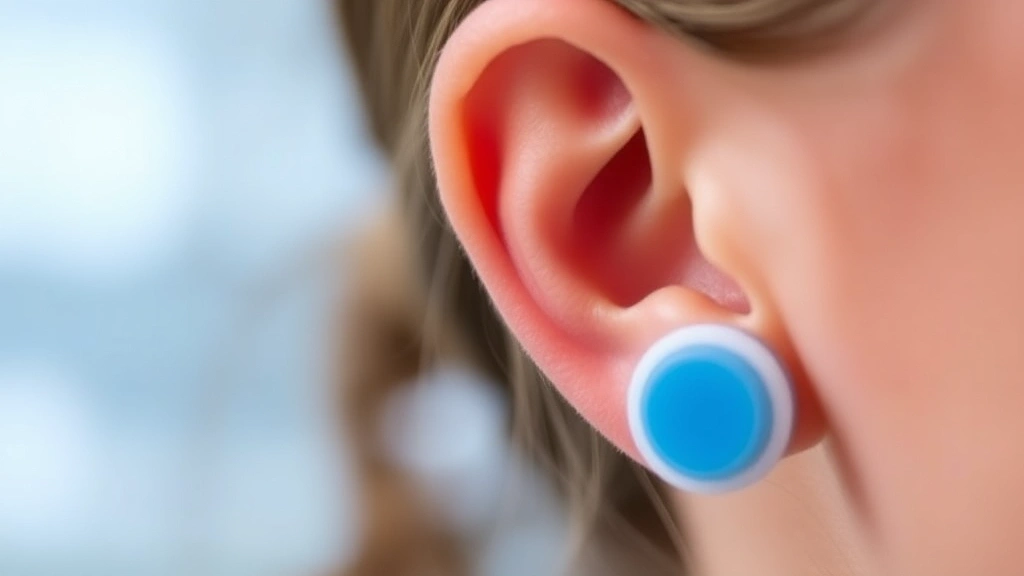
Introduction to LSR
As a professional in the area, I have actually seen the transformative influence of LSR in the growth of hearing elements. LSR has become a recommended material because of its one-of-a-kind buildings that improve the capability and toughness of hearing gadgets.
Superior Flexibility and Comfort
One of the main benefits of utilizing LSR in hearing parts is its exceptional versatility. This flexibility enables a snug fit, which is critical for both convenience and acoustic performance. The soft appearance of LSR makes certain that hearing help can be put on for extended periods without triggering discomfort.
Longevity and Resistance
LSR is renowned for its durability and resistance to ecological factors. It is resistant to UV light, wetness, and temperature variations, making it optimal for hearing tools. This resistance dramatically extends the lifespan of hearing components.
Biocompatibility
The biocompatibility of LSR is an additional essential advantage. It is hypoallergenic and risk-free for extended skin contact, which is vital for users with sensitive skin. This building decreases the danger of irritation and sensitive reactions, making sure of an enjoyable customer experience.
Improved Acoustic Properties
LSR adds to improved acoustic performance by minimizing audio distortion. Its capability to wet resonances and lower noise disturbance enhances the quality and high quality of sound. It gives users a more all-natural listening experience.
Cost-Effectiveness
In regards to production, LSR uses a cost-effective option. Its simplicity of molding and handling decreases manufacturing expenses, allowing producers to generate top-quality elements at a reduced rate point. This cost efficiency can be handed down to customers, making sophisticated hearing innovation extra accessible.
Recap of Advantages
Benefit | Description |
---|---|
Versatility | Ensures comfort and a tight fit |
Durability | Resistant to ecological elements |
Biocompatibility | Safe for long term skin contact |
Acoustic Performance | Decreases sound distortion |
Cost-Effectiveness | Reduces production costs |
Secret Properties of LSR for Acoustic Performance
When taking into consideration products for listening to elements, Liquid Silicone Rubber (LSR) stands out. These properties are essential for making certain that hearing tools provide clear and exact audio. One of the key benefits of LSR is its fundamental flexibility. It permits efficient vibration transmission, a critical factor in sound high quality.
Acoustic Transparency
LSR displays exceptional acoustic transparency, meaning it enables acoustic waves to pass through with very little distortion. This characteristic is vital in listening to components, where the clarity of sound is extremely important. The product’s consistent thickness and uniformity add to its capability to maintain sound integrity.
Sturdiness and Stability
One more vital home of LSR is its durability and stability over a wide variety of temperatures and ecological problems. This stability ensures that the acoustic performance of hearing components remains consistent gradually, despite having constant usage. LSR’s resistance to dampness and UV light further boosts its durability, making it an ideal option for wearable hearing devices.
Vibration Damping
The resonance-damping capabilities of LSR are likewise significant. By properly soaking up and dissipating unwanted resonances, LSR minimizes noise disturbance, consequently boosting the overall sound quality of the hearing tool. This residential property is particularly beneficial in environments with high ambient sound levels.
Biocompatibility
Along with its acoustic benefits, LSR is extremely biocompatible, making it risk-free for extended calls with human skin. This function is important for listening to parts that are used for prolonged durations. The hypoallergenic nature of LSR minimizes the threat of inflammation, guaranteeing customer comfort and security.
Manufacturing Techniques for LSR Hearing Components
The manufacturing of hearing tool parts utilizing Liquid Silicone Rubber (LSR) includes a collection of sophisticated production strategies. They ensure the end products satisfy the premium criteria needed for clinical devices. The inherent residential properties of LSR make it an excellent material for generating parts. In this section, we explore the numerous methods utilized in the construction of LSR hearing parts.
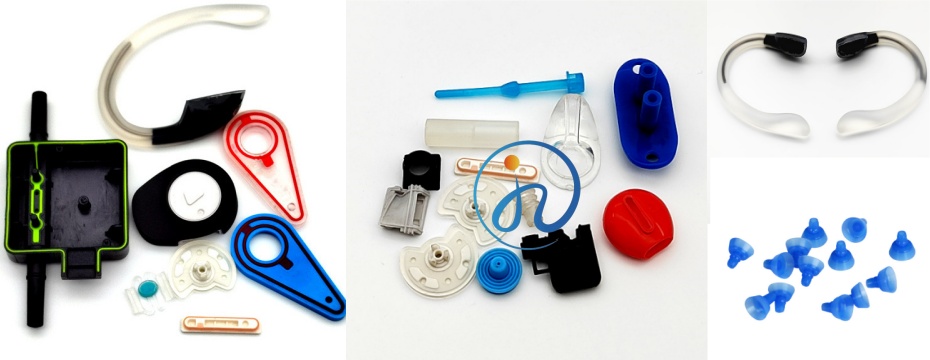
Injection Molding
Injection molding is a primary process used for making LSR components for listening to devices. This method includes infusing the LSR product right into a heated mold tooth cavity. The procedure is very automated and can produce complex geometries with accuracy. The essential advantages of shot molding include its ability to generate elements with tight tolerances.
Overmolding and Insert Molding
Insert molding includes placing an insert, such as an electronic component, right into the mold dental caries and after that infusing LSR around it to envelop the insert within the silicone. These strategies are helpful for integrating extra capability into hearing gadget elements, such as improved acoustic securing or shock absorption.
Two-Component Molding
Two-component molding, additionally called 2K molding, is a process where 2 various sorts of products are simultaneously infused into the very same mold to produce and get rid of several properties. In the context of LSR, this usually involves the combination of various grades or shades of silicone to accomplish the desired attributes in the last component. This method is particularly beneficial for producing hearing tool components that require distinctive areas with different adaptability or hardness.
Prototyping
Quick prototyping methods, including 3D printing, are significantly being used in the advancement of LSR hearing elements. These modern technologies enable fast modeling and testing of design ideas prior to dedicating to automation. Although 3D printing of LSR is much less common than various other products as a result of its special curing buildings, improvements in additive production are expanding the opportunities for prototyping with silicone.
Quality Assurance and Post-Processing
Quality assurance is critical in the manufacturing of LSR hearing components. Each component needs to undertake an extensive evaluation to guarantee it fulfills the required requirements. Post-processing actions, such as precision cutting or surface ending up, are also utilized to fine-tune the parts further and prepare them for setting up into the last hearing tool.
In summary, the production methods for LSR hearing parts vary and call for a deep understanding of both the material properties and the end-user demands. With the appropriate method, these approaches can produce very efficient and trustworthy components that substantially improve the efficiency and comfort of hearing devices.
Conclusion
The future of LSR in hearing innovation is bright, with various possibilities for technology and renovation. By concentrating on improvements in product science, clever combination, sustainability, and modification, the sector can proceed to improve the lifestyle for people with hearing problems.