Liquid Silicone Rubber (LSR) injection molding is a sophisticated manufacturing process that has revolutionized the production of components across a wide array of industries. Its appeal lies in the unique properties of LSR—such as excellent temperature resistance, exceptional flexibility, chemical inertness, and biocompatibility—which, when combined with the precision and efficiency of injection molding, enable the production of complex and high-performance parts. In this comprehensive overview, we explore the myriad applications of LSR injection molding, detailing how its properties make it indispensable in industries ranging from medical and automotive to consumer electronics and aerospace.
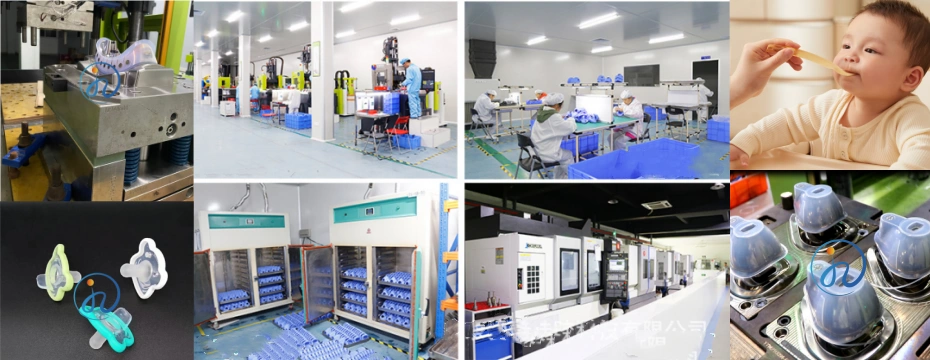
Medical and Healthcare
One of the most significant applications of Liquid Silicone Rubber injection molding is in the medical and healthcare sectors. The medical industry demands materials that can safely interact with the human body and withstand rigorous sterilization procedures, and LSR fits this requirement perfectly. Due to its biocompatibility and resistance to degradation, LSR is commonly used to manufacture components for a variety of medical devices.
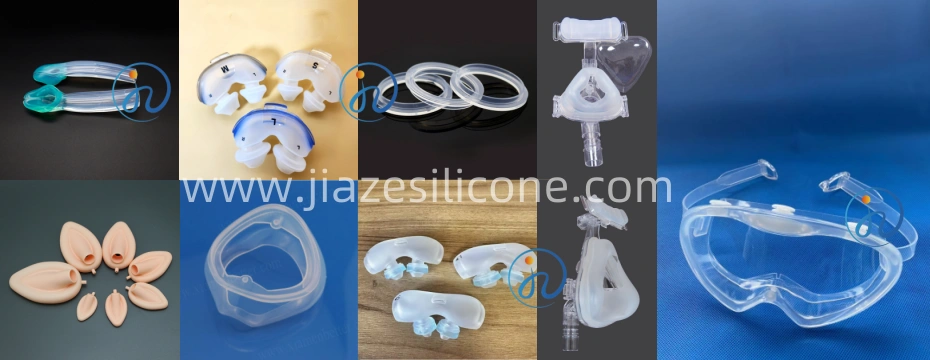
For instance, catheters, surgical seals, and implantable components are often produced using LSR injection molding. Its ability to endure extreme temperatures without losing its properties makes it ideal for repeated sterilization cycles—a crucial factor in ensuring patient safety. Additionally, the flexibility of LSR allows for the creation of intricate shapes and designs, such as soft-touch grips for medical instruments, which enhance usability and comfort for both patients and healthcare professionals.
Automotive Industry
In the automotive sector, the demands for materials that can withstand high temperatures, harsh chemicals, and constant mechanical stress are exceptionally high. LSR injection molding meets these challenges head-on. Automotive manufacturers utilize LSR to produce a variety of components including seals, gaskets, and tubing that are essential for maintaining the integrity and performance of vehicles.
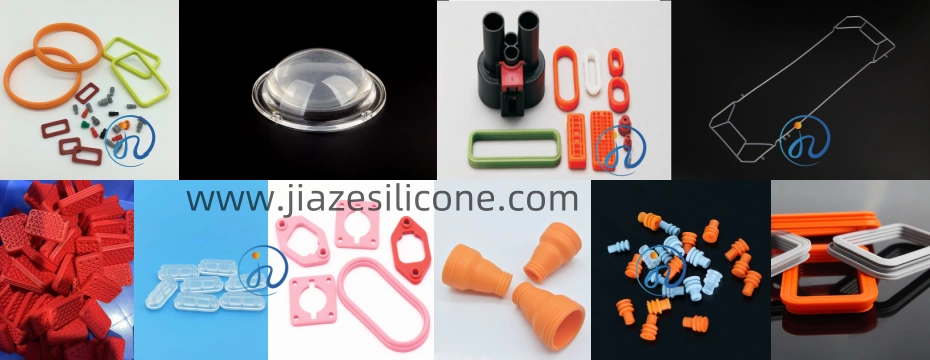
For example, engine components often require materials that can resist degradation from engine fluids and high thermal loads. LSR’s resistance to extreme temperatures ensures that these parts perform reliably under fluctuating conditions, contributing to improved engine efficiency and longevity. As the automotive industry continues to evolve—embracing electric vehicles and advanced driver assistance systems—the need for materials that combine durability with precision will only grow, further solidifying LSR’s role in automotive manufacturing.
Consumer Goods
The versatility and safety profile of LSR makes it a popular choice in the production of consumer goods. Items that require a soft touch, durability, and resistance to wear, such as baby bottle nipples, kitchen utensils, and personal care products, often incorporate LSR components. Consumers are increasingly demanding products that are both high quality and safe, and LSR provides a non-toxic solution that meets these expectations.
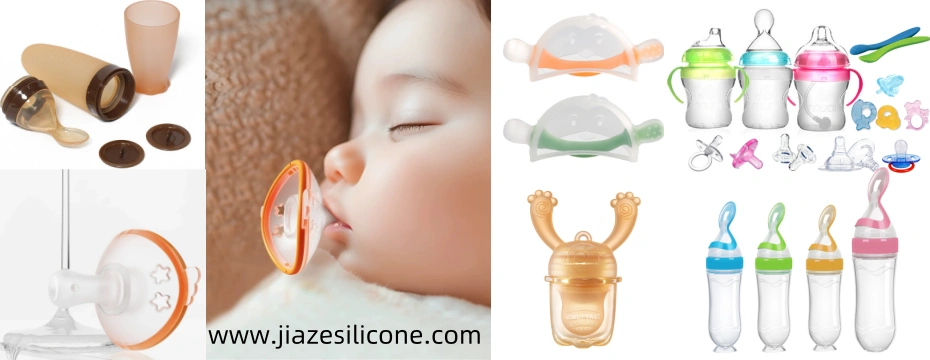
For instance, in the realm of personal care, toothbrush handles, cosmetic applicators, and even parts of electronic personal grooming devices are manufactured using LSR injection molding. Furthermore, the aesthetic qualities of LSR—its smooth finish and the potential for vibrant color integration—allow consumer goods to meet both functional and design standards, making them appealing in a competitive market.
Electronics and Electrical Applications
The electronics industry benefits from LSR injection molding through the production of components that require both precision and high performance in challenging environments. LSR’s excellent dielectric properties make it an ideal material for encapsulating electronic components, protecting them from moisture, dust, and mechanical shock. This encapsulation is crucial in ensuring the longevity and reliability of sensitive electronics.
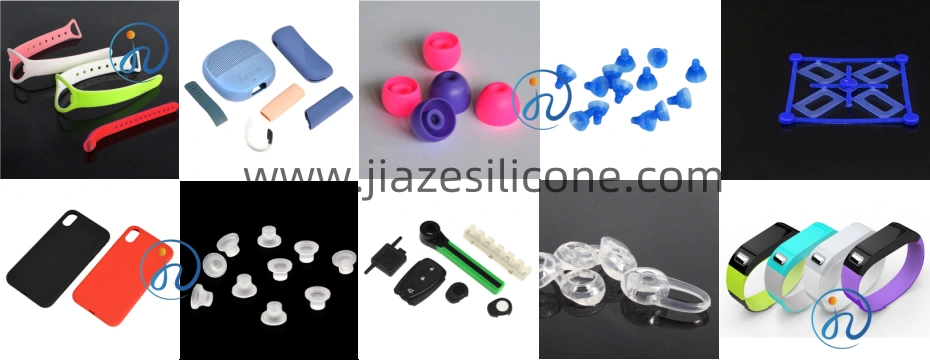
Additionally, LSR is employed in the production of high-temperature connectors and insulators. As electronic devices become more compact and powerful, the thermal management of these components becomes critical. LSR’s inherent heat resistance helps maintain the performance of electronic devices even under strenuous operating conditions. Furthermore, its flexibility allows for the creation of complex geometries that are essential in modern electronic design, where space is at a premium and intricate component layouts are common.
Industrial Applications
Beyond consumer and electronics markets, LSR injection molding plays a pivotal role in various industrial applications. In sectors such as manufacturing and automation, the need for durable, precise, and chemically resistant components is paramount. LSR is frequently used to produce seals, O-rings, and gaskets for machinery and equipment operating under harsh conditions.
For example, in chemical processing plants, components made from LSR must withstand exposure to aggressive chemicals without degrading. The chemical inertness of LSR ensures that these parts maintain their integrity over time, preventing leaks and mechanical failures. The speed and efficiency of injection molding further enhance productivity, making it a cost-effective solution for producing large volumes of industrial components.
Aerospace and Defense
In aerospace and defense, the materials used must meet rigorous standards for performance and reliability. Components used in aerospace applications often face severe temperature variations, mechanical stresses, and exposure to corrosive elements. LSR’s stability under such conditions makes it an excellent choice for parts such as seals, gaskets, and protective covers.
The defense sector also leverages LSR for various applications, including in the manufacture of components for military equipment and vehicles. The resilience of LSR against both physical and chemical wear ensures that equipment remains operational in the most demanding scenarios, contributing to overall mission success.
Conclusion
Liquid Silicone Rubber injection molding has emerged as a critical technology across diverse industries due to its remarkable properties and versatility. Whether it’s enhancing patient safety in the medical field, ensuring the reliability of automotive components, adding durability to consumer products, protecting delicate electronics, or meeting the stringent demands of industrial and aerospace applications, LSR stands out as a material that can adapt to various challenges.
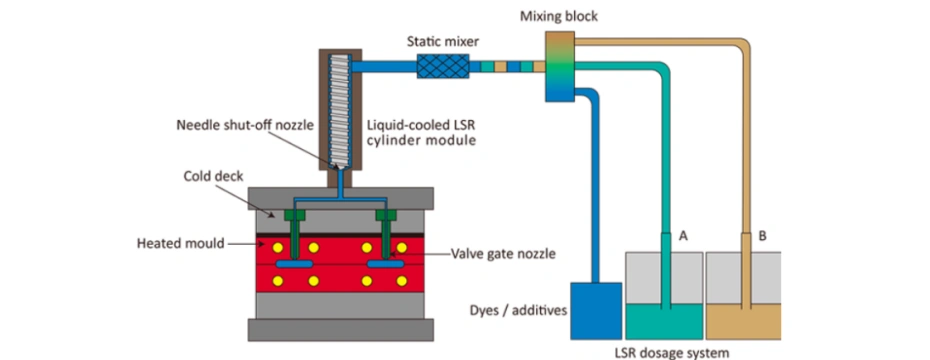
The efficiency of the injection molding process—characterized by high production speeds, precision, and the ability to produce complex shapes—further accentuates the advantages of using LSR.
In summary, the applications of LSR injection molding are as diverse as they are impactful. Its integration into various sectors exemplifies the material’s versatility and underscores the critical role of advanced manufacturing processes in driving industrial progress and innovation.