Liquid Silicone Rubber (LSR) Injection Molding is a process designed to produce highly precise, durable, and heat-resistant parts using liquid silicone rubber. This technique is essential across multiple industries, including automotive, medical, electronics, and consumer goods, where high-quality silicone components are necessary. The following outlines the process in detail, covering the preparation, molding, curing, and post-processing stages.
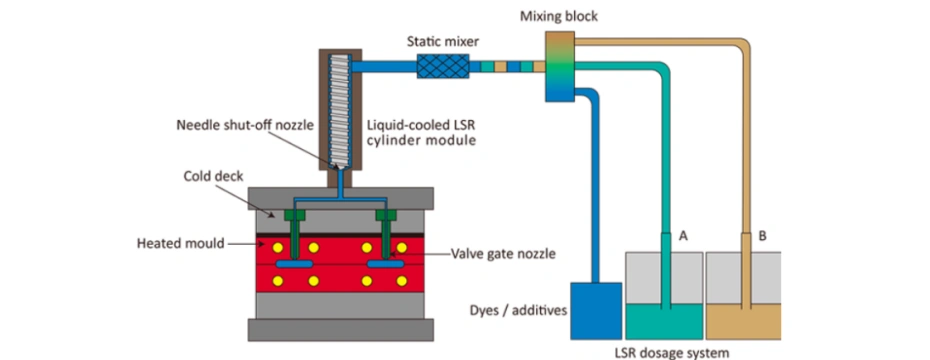
1. Material Preparation and Delivery
LSR material is typically supplied in two parts, Part A and Part B, stored separately to avoid premature curing. In the molding process, these two components must be mixed in precise proportions, usually at a 1:1 ratio. This ratio ensures the right consistency and reaction for a successful molding process.
The mixing process can include pigments or other additives for specific part characteristics, such as color or enhanced material properties. LSR’s low viscosity allows it to flow easily into molds, which is particularly useful for complex shapes and fine details. A metering system feeds the mixed material into the injection molding machine, controlling the flow and maintaining consistency. This precise material delivery system is essential to maintaining part quality and repeatability.
2. Injection Molding Machine Setup
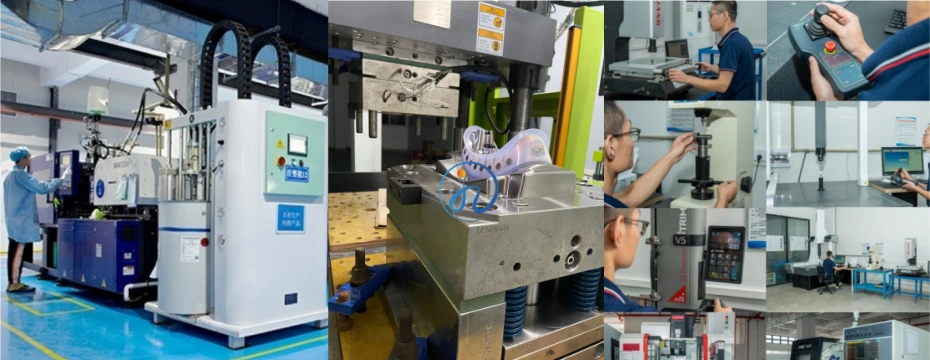
LSR injection molding requires specialized machines tailored to the low viscosity of liquid silicone rubber. Traditional injection molding machines are not suitable for LSR, as the material’s flow characteristics and curing behavior require specific temperature control and injection parameters.
One key component of an LSR molding machine is the cold runner system. This system ensures that the material stays cool in the feed channels and only begins to cure once it reaches the heated mold cavity. Cold runners prevent premature curing and reduce material waste, an important consideration when working with silicone.
Molds used in LSR injection molding are usually made from durable metals like steel, designed to handle the silicone’s unique behavior and the high temperatures needed for curing. The mold design includes both a hot mold and a cold injection nozzle, which work in tandem to deliver material efficiently into the mold cavity and initiate the curing reaction.
3. Injection and Filling of Liquid Silicone
In the injection and filling phase, the LSR mixture (Parts A and B) is injected into the mold cavity, which is preheated to a specific temperature—typically between 120-160°C. This heating ensures that the curing process begins as soon as the material enters the mold.
The mold design and the low viscosity of LSR allow the material to flow into intricate spaces, filling out even the most complex designs. Low viscosity also helps reduce stress on the material, minimizing imperfections such as warping, shrinkage, or air pockets. Silicone’s unique properties make it possible to mold complex parts with undercuts and fine details, which would be challenging with other materials.
Due to the high temperatures and carefully controlled pressure, LSR fills the mold rapidly, reducing the cycle time and ensuring consistent, high-quality production. The controlled filling process is vital for achieving accurate parts with repeatable results.
4. Curing and Solidification
LSR curing involves a chemical cross-linking reaction between the two mixed components, transforming the liquid into a durable, rubber-like solid. The heat from the mold accelerates this cross-linking reaction, making the curing process rapid.
Cycle times for LSR injection molding are relatively short, depending on factors such as part size, material formulation, and mold temperature. For thin parts, curing may take only a few seconds, while larger, thicker parts may require several minutes. The fast curing process of LSR is one of its main advantages, enabling efficient production of large quantities of parts.
LSR’s natural elasticity makes demolding easier, as it is flexible enough to withstand deformation without damage. Additionally, the durable properties of silicone mean that the material can endure repeated molding and demolding without degradation.
5. Post-Molding Operations
Although the mold itself is carefully designed to minimize material waste, some excess material or “flash” may form around the edges of the part. Flash can result from slight material leakage during the injection phase and is common in silicone molding. A cold runner system helps reduce flash, but it’s sometimes necessary to remove excess material with trimming.
Depending on the part’s intended application, secondary processing may also be required. For example, in medical or food applications, the part might need additional sterilization or post-curing to ensure compliance with industry standards. Post-curing further enhances silicone’s mechanical and chemical resistance, making it suitable for harsh environments and critical applications.
Quality control is another critical aspect of post-molding. In highly regulated industries like medical or automotive, parts may also undergo testing to confirm compliance with strict performance standards. Tests may include tensile strength, compression, and thermal resistance, depending on the part’s intended use.
6. Advantages of Liquid Silicone Injection Molding
LSR injection molding offers numerous advantages, which make it a preferred process for many applications:
- Precision and Repeatability: The consistency of the LSR injection molding process allows for tight tolerances and repeatable results, which is essential in applications where precision is critical.
- High Efficiency: The short cycle times associated with LSR curing enable rapid production, making it a cost-effective solution for high-volume manufacturing.
- Versatility: LSR’s low viscosity and high flexibility make it ideal for creating complex parts with intricate details, thin walls, or undercuts.
- Durability and Resistance: Liquid silicone parts are known for their durability and resistance to extreme temperatures, UV rays, and chemical exposure. This makes them suitable for applications in challenging environments.
7. Common Applications of Liquid Injection
The unique properties of LSR make it suitable for a wide range of industries. Common applications include:
- Medical Devices: Due to its biocompatibility, LSR is often used in medical devices like catheters, syringes, and implants. Silicone’s hypoallergenic and sterilizable nature makes it a preferred material for contact with the human body.
- Automotive Components: LSR’s heat and chemical resistance make it ideal for parts like gaskets, seals, and electrical connectors. These components must withstand harsh automotive environments without compromising performance.
- Consumer Goods: Many household and personal care products utilize LSR, including kitchenware, baby products, and electronics. Its softness, flexibility, and resistance to high temperatures make it suitable for such products.
- Electronics: Silicone’s insulating properties are advantageous in electronic components, where it serves as a protective layer or seal to prevent dust, water, or other contaminants from affecting delicate circuitry.
Conclusion
The Liquid Silicone Rubber Injection Molding process is a sophisticated, efficient, and versatile method that enables the production of high-quality, durable, and precise silicone parts. LSR injection molding has transformed various industries by providing reliable solutions for applications requiring durability, flexibility, and biocompatibility, meeting the stringent demands of sectors like automotive, medical, and consumer goods. The precision and repeatability offered by LSR injection molding make it a powerful process for manufacturers seeking both high performance and cost-effectiveness in silicone-based products.