Gate location is one of the most critical decisions in silicone injection molding, directly influencing product quality, manufacturing efficiency, and cost. This choice affects the flow of liquid silicone rubber into the mold cavity, the final part’s mechanical properties, surface finish, and the likelihood of defects such as flash, weld lines, and air entrapment. Here is a detailed guide on how to determine gate location in silicone injection molding, divided into key considerations and practical tips.
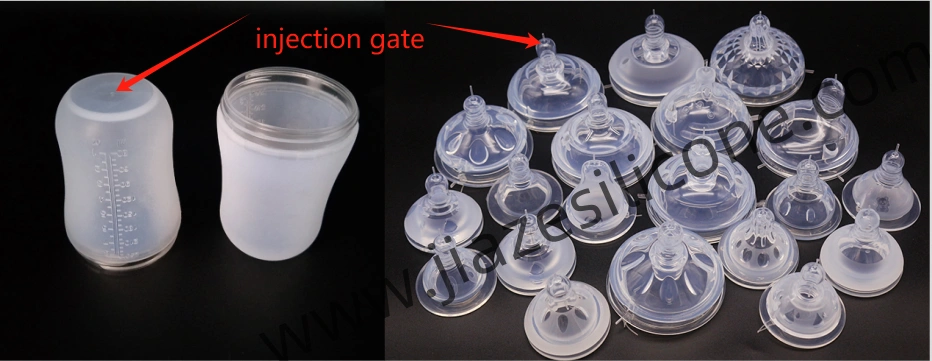
1. Material Properties and Flow Characteristics
Silicone, especially Liquid Silicone Rubber (LSR), exhibits specific flow properties:
- Low viscosity: LSR flows easily, allowing complex geometries to be filled, but it also increases the likelihood of flash.
- High thermal expansion: This impacts shrinkage and cooling considerations.
- Elasticity and curing behavior: Proper flow ensures uniform curing, which is critical for consistent part performance.
When deciding gate location, consider:
- Flow path length: Ensure the silicone can reach all areas of the mold before it begins to cure.
- Pressure drop: A shorter flow path reduces the pressure required to fill the mold, minimizing stress on the material.
2. Part Geometry and Design
Analyze the part’s shape and functional requirements:
- Uniform wall thickness: Position the gate to promote even flow and consistent wall thickness, avoiding areas where material could stagnate and cure prematurely.
- Complex features: Place gates near intricate details to ensure complete filling without defects.
- Symmetry: For symmetrical parts, a centrally located gate promotes balanced flow, reducing internal stresses.
3. Aesthetic Considerations
If the part’s appearance is critical:
- Minimize visible marks: Choose a gate location on a non-visible surface or one that can be easily trimmed.
- Avoid flow marks: Improper gate placement can lead to flow lines or streaks, especially in areas of rapid flow transition.
4. Mold Design and Manufacturing Constraints
The mold design significantly influences gate placement:
- Ease of de-molding: Gates should not obstruct ejection or cause material to stick in the mold.
- Cooling channels: The gate location should not interfere with efficient cooling or heating systems within the mold.
- Multiple cavities: In multi-cavity molds, ensure balanced filling across all cavities by symmetric gate placement.
5. Type of Gate
Different gate types suit different scenarios, influencing where the gate can be located:
- Direct gate: Often used for large parts, it requires careful placement to minimize marks and flow imbalances.
- Edge gate: Common for smaller parts, allowing easy trimming and good flow control.
- Submarine gate: Positioned below the parting line, ideal for automated operations but requires precise design.
- Fan gate: Helps distribute material evenly over a wide area, suitable for large, thin parts.
6. Defect Prevention
Gate placement can mitigate common defects:
- Weld lines: Avoid placing gates where material flows converge, as this can lead to weak spots.
- Air traps: Place gates to allow air to escape through vents, especially in deep or complex molds.
- Flash: Minimize flash by positioning gates where clamp pressure is maximized and mold parting surfaces align tightly.
7. Flow Simulation and Analysis
Modern molding simulations provide invaluable insights:
- Mold flow analysis: Use software to visualize flow patterns, predict pressure and temperature distribution, and identify potential defects.
- Iterative optimization: Test multiple gate locations virtually to determine the best option before committing to a physical mold.
8. Practical Tips for Gate Placement
- Start from thick to thin sections: Place gates in thicker sections, as silicone flows more easily from thick to thin areas.
- Avoid placing gates on sharp corners or edges: This prevents excessive stress and flash in these regions.
- Account for shrinkage: Position the gate to minimize distortion during cooling.
9. Consider the Post-Processing Requirements
Gate removal and finishing processes can affect production efficiency:
- Accessibility: Gates should be easily accessible for trimming, particularly in manual operations.
- Minimize material waste: Position gates to reduce sprue length and minimize waste.
10. Collaboration with Stakeholders
Successful gate placement requires input from:
- Design engineers: Ensure the part design aligns with functional and aesthetic goals.
- Toolmakers: Leverage their expertise in mold construction and feasibility.
- Process engineers: Optimize placement based on manufacturing efficiency and defect prevention.
Case Study: A Practical Example
Consider a silicone gasket with a complex shape and critical sealing properties.
- Flow Requirements: The gate is placed centrally to ensure even filling.
- Wall Thickness: The thickest section, typically the base, is gated to allow smooth material flow to thinner sections.
- Aesthetic Needs: The gate is positioned on a non-visible surface, avoiding areas that would compromise the seal or appearance.
- Simulation and Testing: Mold flow analysis reveals potential weld lines at the corners, prompting a secondary vent near these regions.
Conclusion
Deciding on gate location in silicone injection molding requires a balance of material behavior, part design, mold construction, and production goals. By carefully considering factors like flow characteristics, aesthetics, mold constraints, and defect prevention, and utilizing modern simulation tools, you can optimize gate placement to ensure high-quality parts and efficient manufacturing. Collaboration across teams ensures that the chosen gate location aligns with both design and production requirements.