Liquid Silicone Rubber (LSR) overmolding on nylon is a widely used manufacturing process, particularly in industries like automotive, medical devices, consumer electronics, and industrial applications. This technique enhances product durability, improves grip, provides sealing capabilities, and increases resistance to chemicals and extreme temperatures. However, the LSR overmolding nylon cost varies significantly depending on multiple factors. This article explores the key cost drivers, material selection, tooling expenses, production methods, and overall cost estimations to help manufacturers optimize their production budget.
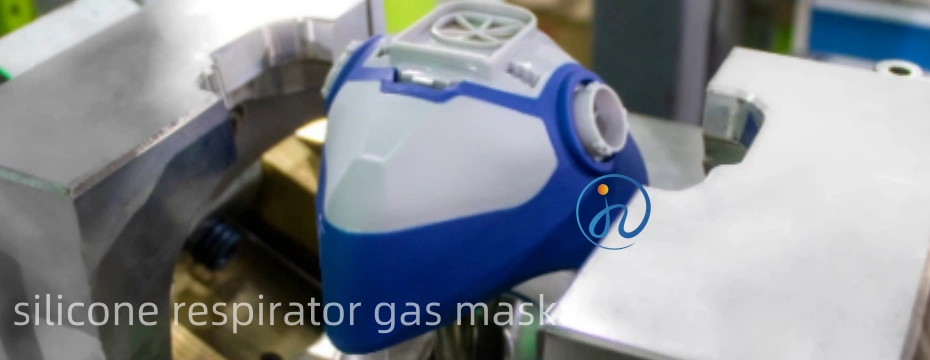
Key Cost Drivers
Several factors influence the cost of LSR overmolding on nylon, including:
- Material Costs – Both nylon and LSR materials come in different grades, affecting overall expenses.
- Tooling and Mold Costs – Custom molds and tooling design significantly impact initial investment.
- Manufacturing Process – Injection molding equipment, cycle time, and automation level influence pricing.
- Labor and Overhead – Facility costs, labor rates, and operational efficiencies contribute to total production cost.
- Quality Control and Testing – Ensuring high-quality standards adds to costs.
- Production Volume – Higher volumes usually reduce per-unit cost due to economies of scale.
- Secondary Operations – Additional finishing, assembly, or packaging costs can impact total expenditure.
Material Considerations
Nylon Selection
Nylon, also known as polyamide, is available in multiple variants, such as PA6, PA66, and reinforced nylons. The choice depends on the application, with prices varying accordingly. Typical cost per kilogram for unfilled nylon ranges from $3 to $7, while reinforced variants with glass or carbon fibers can cost between $5 and $12 per kilogram.
LSR Selection
Liquid Silicone Rubber is preferred for its flexibility, biocompatibility, and heat resistance. The cost of LSR material depends on its grade and application. Standard LSR costs range from $5 to $20 per kilogram, with medical-grade and specialized formulations at the higher end.
Tooling and Mold Costs
LSR overmolding requires specialized tooling, which can be expensive due to the complexity of achieving precision molding.
- Prototype molds: $5,000–$20,000
- Production molds: $20,000–$100,000 (depending on cavity count and complexity)
- Multi-cavity molds reduce per-part cost but require higher upfront investment.
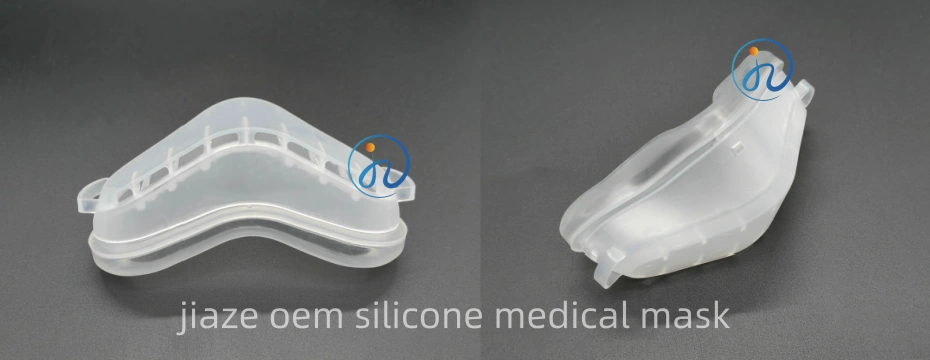
Manufacturing Process and Costs
The production process includes:
- Injection Molding Setup: Typically $50,000–$200,000 for high-precision equipment.
- Cycle Time: Shorter cycle times (~30–60 seconds per part) reduce per-unit costs.
- Labor & Automation: Manual operations increase costs, while automation optimizes efficiency.
- Material Wastage: LSR requires precise control to minimize material loss, which can increase costs.
Estimated Per-Unit Costs
For a standard LSR overmolded nylon part:
- Small parts (5–50g): $0.50–$5 per unit (high-volume production)
- Medium parts (50–200g): $5–$20 per unit
- Large parts (>200g): $20–$50 per unit
Cost Reduction Strategies
To optimize costs, manufacturers can:
- Select cost-effective material grades
- Invest in multi-cavity molds for high-volume runs
- Implement automation to reduce labor costs
- Optimize part design to minimize material waste
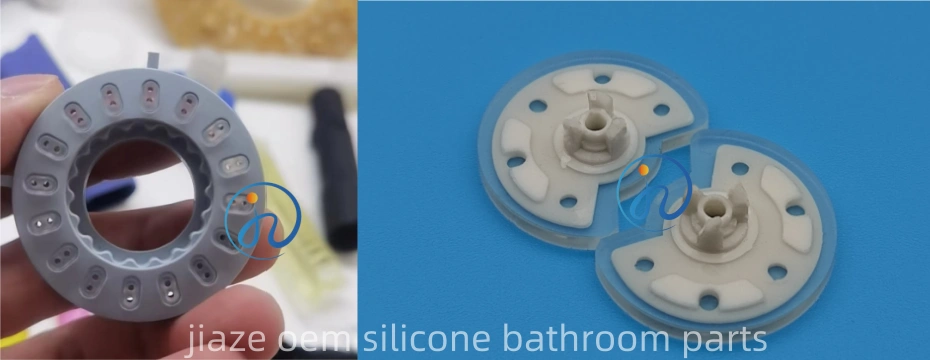
Conclusion
LSR overmolding on nylon provides significant functional benefits but requires careful cost analysis. By understanding the key cost factors and employing optimization strategies, manufacturers can achieve cost-efficient production while maintaining product quality. Proper planning in material selection, tooling, and automation can help balance upfront investment and long-term profitability.