The cost of a liquid silicone injection mold (LSR mold) can vary significantly based on several factors, including mold complexity, production requirements, materials, design intricacies, and the manufacturer chosen. Understanding these factors is crucial to estimating costs accurately, as LSR molds represent a unique segment of the injection molding industry, tailored specifically for liquid silicone rubber (LSR) applications. Below is an in-depth overview that will help clarify the various cost components associated with liquid silicone injection molds.
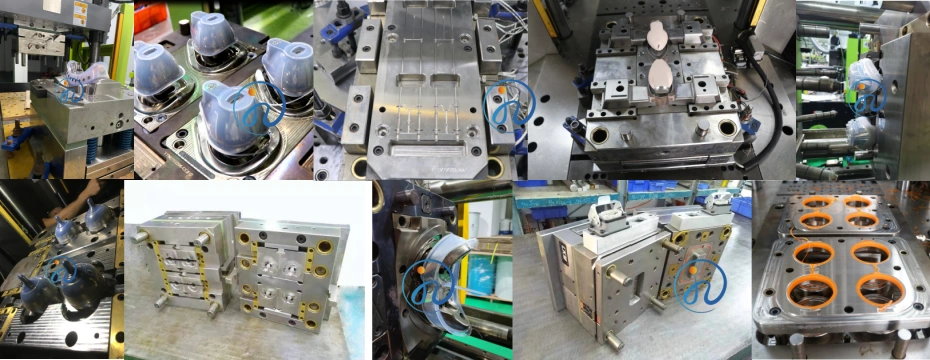
1. Understanding Liquid Silicone Injection Molding
Liquid silicone injection molding is a specialized process where a two-part liquid silicone compound is injected into a heated mold. Unlike thermoplastic molding, LSR molding involves a curing process within the mold, resulting in products with flexibility, high-temperature resistance, and excellent durability. This process is ideal for applications in medical devices, automotive parts, electronics, and even consumer goods. The LSR process is a bit more intricate than regular plastic injection molding, which adds to the mold’s complexity and, subsequently, its cost.
2. Cost Components of LSR Injection Molds
To understand the overall cost, let’s break down the main factors involved:
- Design Complexity: More intricate designs require detailed engineering and more time-consuming manufacturing processes. Features such as thin walls, undercuts, or complex geometries necessitate additional machining and testing. Designs with multiple cavities (to produce multiple parts per cycle) or complex mechanisms like sliding cores will also increase the cost.
- Cavitation: The number of cavities in a mold directly impacts the cost. Single-cavity molds (which make one part per cycle) are cheaper but result in slower production rates. Multi-cavity molds (which can make several parts simultaneously) increase production speed but also add significant costs due to the complexity of mold design and manufacturing.
- Material Choice for the Mold: The mold material is critical as it must withstand the curing temperatures of LSR, which are typically higher than those for plastic molding. Steel (especially high-grade hardened steel) is the preferred material for LSR molds due to its durability and resistance to wear and tear. While softer metals or aluminum may reduce initial costs, these materials are generally unsuitable for LSR due to the high pressures and temperatures involved, making steel the industry standard, albeit a pricier one.
- Surface Finish and Texturing: Many LSR applications, particularly in the medical and consumer goods sectors, require specific surface textures or finishes. Achieving certain textures or smooth finishes requires additional steps, such as electroplating or polishing. These finishing processes can increase costs, especially if specialized textures are needed to improve grip, reduce friction, or enhance aesthetics.
- Engineering and Mold Design Costs: Engineering and design form the foundation of the mold’s functionality and durability. For complex designs, significant time is dedicated to computer-aided design (CAD) and computer-aided manufacturing (CAM) modeling to ensure the mold functions as required.
- Precision and Quality Control: The high level of precision required in LSR molding adds to the mold cost. Since LSR parts are often used in sensitive industries like medical and automotive, strict quality control is necessary. Quality checks, testing, and reworking add to both the time and cost of producing the mold.
- Lead Times: For projects with fast turnarounds, manufacturers may charge a premium for expedited mold production. Standard lead times for LSR molds can range from several weeks to a few months, depending on mold complexity and production backlog. A shorter lead time often comes at a premium, as it may require additional labor shifts or prioritization.
3. Average Cost Range of LSR Molds
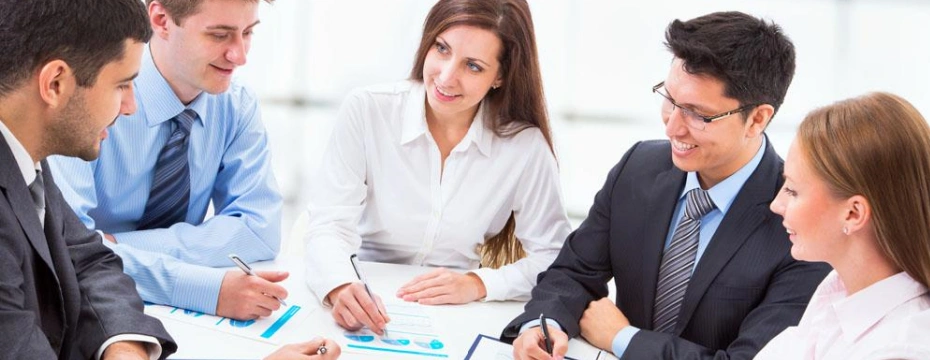
Given the above factors, the cost of a liquid silicone injection mold can vary widely. Here’s a breakdown of typical cost ranges:
- Simple, Single-Cavity Molds: For straightforward applications, such as basic shapes with minimal detail, a single-cavity LSR mold could range from $5,000 to $9,000. These molds are generally used for lower-volume production where intricate designs or high-cavity molds are unnecessary.
- Mid-Level Complexity Molds: For designs with moderate complexity, such as additional cavities, or parts with moderate detailing or undercuts, costs can range between $9,000 to $15,000. These molds are suitable for mid-volume production runs and may incorporate elements like multi-cavity design or enhanced surface textures.
- High-Complexity, Multi-Cavity Molds: Molds for high-volume production, complex parts, or those requiring specific finishes (such as medical-grade parts) can cost $15,000 to $50,000 or more. These molds often include features like multi-cavity design (sometimes with 16 or more cavities), advanced quality control features, and high-grade steel to handle significant wear and tear.
4. Additional Costs in Liquid Silicone Injection
Beyond the initial cost of the mold, other associated costs contribute to the overall price of an LSR injection molding project:
- Setup and Installation: This includes machine calibration, injection machine setup, and alignment checks, which may require specialized technicians and additional fees.
- Testing and Prototyping: Before a mold is ready for full production, it often goes through testing to ensure it meets the required specifications. This can involve producing a small test batch and making adjustments, which may add costs for labor and materials.
- Maintenance and Repairs: Over time, molds may require maintenance or repair, especially if used for high-volume production. Regular maintenance (such as cleaning, polishing, and part replacement) ensures mold longevity but does add to the overall project cost.
- Scrap Rates and Rework: In any injection molding process, there is an anticipated scrap rate—parts that do not meet quality standards and need to be discarded or reworked.
5. How to Optimize Cost in LSR Molding
- Optimize Design Early: By simplifying part design early on, manufacturers can reduce the complexity of the mold, which in turn lowers costs. Streamlining features and avoiding unnecessary undercuts or thin walls can make mold fabrication easier and cheaper.
- Invest in Multi-Cavity Molds for High Volumes: Though multi-cavity molds are more expensive initially, they offer substantial cost savings over large production runs by reducing the per-part manufacturing cost. For high-volume needs, multi-cavity molds can yield a faster ROI.
- Choose the Right Manufacturer: Not all manufacturers have expertise in LSR molding. Selecting a specialized LSR mold maker may come with a higher upfront cost, but it typically leads to better results, fewer rework issues, and longer mold life.
- Consider Overseas vs. Domestic Manufacturing: Some companies opt for overseas manufacturers where labor and material costs are lower. However, this may come with challenges, including longer lead times and potentially lower quality control standards. The choice between domestic and overseas suppliers can impact costs significantly.
6. Cost Comparison with Other Molding Types
Liquid silicone injection molding is generally more expensive than thermoplastic injection molding due to the unique properties of silicone rubber and the need for specialized equipment and processes. While a thermoplastic mold may be cheaper, it does not meet the requirements for LSR, which must withstand higher pressures, temperatures, and longer cycle times. As a result, manufacturers specializing in LSR tend to command a premium due to the specialized knowledge and equipment involved.
In Summary
The cost of a liquid silicone injection mold is influenced by many factors, with prices ranging from around $5,000 for basic single-cavity molds to upwards of $50,000 for high-complexity, multi-cavity molds. By understanding the detailed components and working with experienced mold makers, companies can make informed choices that balance initial mold costs with production efficiency and quality requirements. For applications in industries such as medical, automotive, and consumer electronics, the benefits of LSR molding—durability, flexibility, and temperature resistance—often justify the higher initial investment in specialized molds.