Liquid Silicone Rubber (LSR) is a versatile material used across industries for its durability, flexibility, and resistance to extreme conditions. The manufacturing process for LSR products is efficient and highly customizable, making it a preferred choice for medical devices, automotive parts, electronics, and consumer goods. This guide breaks down the LSR product manufacturing process into key stages.
1. Understanding Liquid Silicone Rubber
It is non-toxic, hypoallergenic, and resistant to chemicals, UV light, and weathering. Its properties make it ideal for high-precision and high-volume applications.
2. The Manufacturing Process
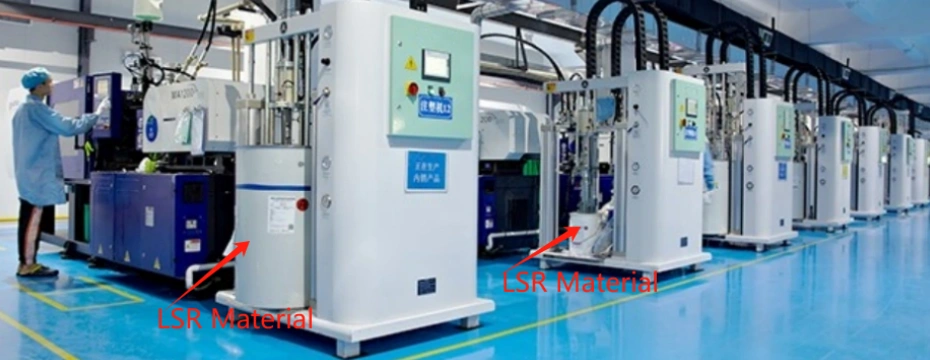
A. Design and Prototyping
The first step in the LSR manufacturing process is product design and prototyping. Engineers and designers collaborate to develop a product that meets functional, aesthetic, and durability requirements.
- 3D Modeling: Computer-aided design (CAD) tools create detailed digital product models.
Design considerations include:
- Wall thickness consistency to avoid uneven curing.
- Draft angles to facilitate easy removal from molds.
- Placement of parting lines and injection points for optimal aesthetics and functionality.
B. Material Selection
Choosing the right grade for LSR is crucial. Different grades of LSR are available for specific applications:
- Medical Grade: Biocompatible and sterilizable.
- Food Grade: Complies with FDA regulations for food contact.
- High-Strength Grade: For applications requiring exceptional durability.
C. Mold Design
Precision mold design is critical for ensuring consistent quality in LSR products.
- Runner Systems: Channels that direct LSR into the mold cavities.
- Vents: To allow air to escape during injection.
- Temperature Control Systems: Maintain consistent mold temperatures for proper curing.
D. LSR Injection Molding
The heart of the LSR manufacturing process is injection molding. Here’s how it works:
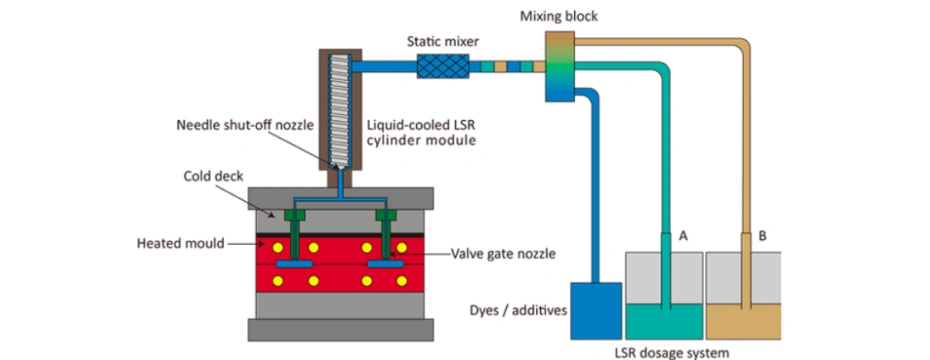
- Preparation:
- LSR comes in two parts: Part A (base silicone) and Part B (curing agent). These components are stored separately to prevent premature curing.
- Color pigments or additives can be mixed during this stage for customization.
- Injection Molding Process:
- Metering: Parts A and B are precisely measured and mixed in a 1:1 ratio.
- Injection: The mixed LSR is injected into the pre-heated mold under high pressure.
- Curing: The mold is maintained at a specific temperature (typically 170–200°C) to cure the material rapidly. Curing time depends on the product’s thickness and complexity but typically ranges from a few seconds to a few minutes.
- Demolding:
- Once cured, the mold opens, and the finished product is ejected, often with the help of automated systems or robotic arms.
E. Post-Processing
After demolding, some LSR products require additional steps to ensure quality and functionality:
- Surface Treatment: Depending on the application, surfaces may be polished or coated.
- Sterilization: Medical-grade products are sterilized using methods like autoclaving or gamma radiation.
F. Quality Control
Quality control ensures the product meets all specifications and industry standards. This includes:
- Dimensional Inspection: Using tools like calipers and coordinate measuring machines (CMMs) to verify dimensions.
- Material Testing: Testing for hardness, tensile strength, and elasticity.
- Functional Testing: Ensuring the product performs as intended under real-world conditions.
3. Automation in LSR Manufacturing
Automation plays a significant role in LSR manufacturing, improving efficiency and consistency. Automated systems handle:
- Material mixing and feeding.
- Mold temperature regulation.
- Product inspection and packaging.
Robotics also enhance safety by minimizing human exposure to hot molds and hazardous materials.
4. Advantages of LSR Manufacturing
The LSR manufacturing process offers numerous benefits:
- Scalability: Suitable for both small and large production volumes.
- Durability: Products are resistant to wear, chemicals, and extreme conditions.
- Sustainability: LSR is recyclable, and the manufacturing process generates minimal waste.
5. Applications of LSR Products
LSR products are ubiquitous in various industries:
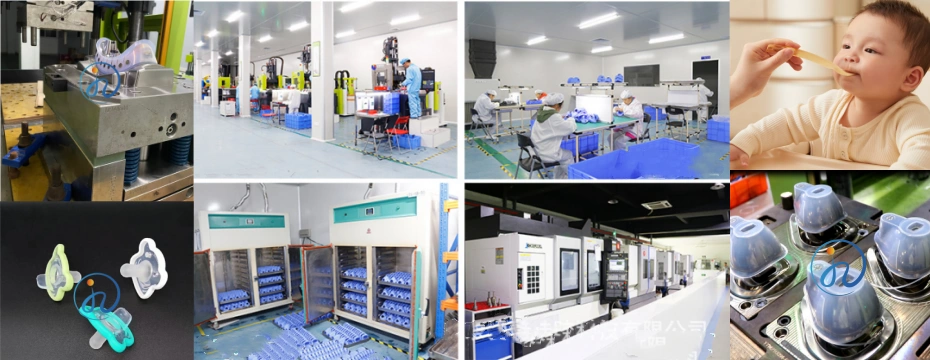
- Medical and Healthcare: Catheters, seals, and baby products.
- Automotive: Gaskets, connectors, and keypads.
- Electronics: Wearable devices and protective covers.
- Consumer Goods: Kitchenware, toys, and seals.
6. Challenges in LSR Manufacturing
While LSR manufacturing is highly efficient, challenges include:
- High Initial Costs: Precision molds and equipment require significant investment.
- Material Handling: Preventing contamination during material mixing and feeding.
- Cycle Time Optimization: Balancing curing time with productivity.
Continuous advancements in equipment and techniques are addressing these challenges.
7. Future Trends in LSR Manufacturing
The LSR manufacturing industry is evolving with new trends:
- Sustainability: Development of bio-based LSRs to reduce environmental impact.
- Miniaturization: Enhanced capabilities for micro-molding applications.
- Smart Manufacturing: Integration of IoT and AI for real-time monitoring and process optimization.
Conclusion
The LSR product manufacturing process is a sophisticated blend of design, material science, and precision engineering. By understanding each step of the process, manufacturers can create high-quality, reliable products that meet the demands of diverse industries. With its growing applications and technological advancements, LSR remains a cornerstone of modern manufacturing.