Liquid Silicone Rubber (LSR) injection molding is widely used in medical, automotive, and consumer goods due to its high precision, flexibility, and durability. However, like any manufacturing process, it comes with challenges. Two of the most common issues are flash and burrs, which can compromise product quality, increase costs, and delay production timelines. Preventing these defects requires a combination of optimized design, precise processing, and effective maintenance.
Here’s a detailed guide on how to prevent flash and burrs in LSR injection molding.
1. Understanding Flash and Burrs
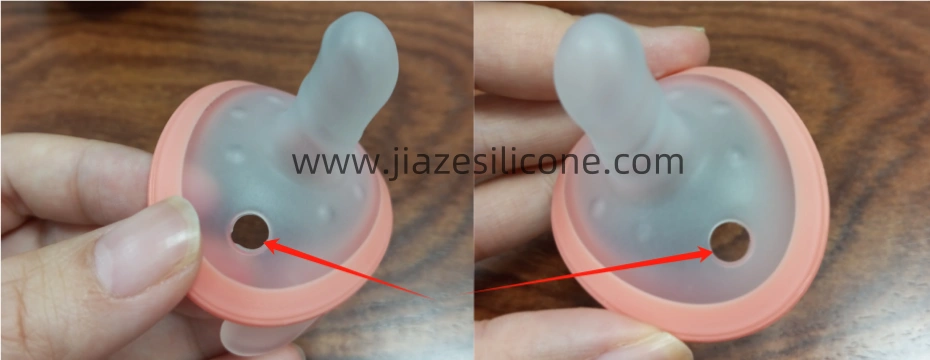
Flash refers to thin, unwanted material that leaks out of the mold cavity and solidifies along the parting line or ejector pin areas. Burrs are similar but often finer and occur at edges or transitions.
- Causes:
- Excessive injection pressure.
- Poor mold alignment or damage.
- Gaps between mold components.
2. Design Considerations
Good design is the foundation for preventing flash and burrs.
a. Mold Design
- Tight Tolerances: Ensure all mold components fit together precisely. Tolerances as low as ±0.01 mm are often required for LSR molds.
- Parting Line Precision: Design smooth and consistent parting lines to minimize the risk of gaps. Avoid abrupt transitions or undercuts along these lines.
- Vent Design: Incorporate microvents to allow air to escape during injection. Ensure vents are small enough (usually 0.01–0.03 mm deep) to prevent material leakage.
b. Part Design
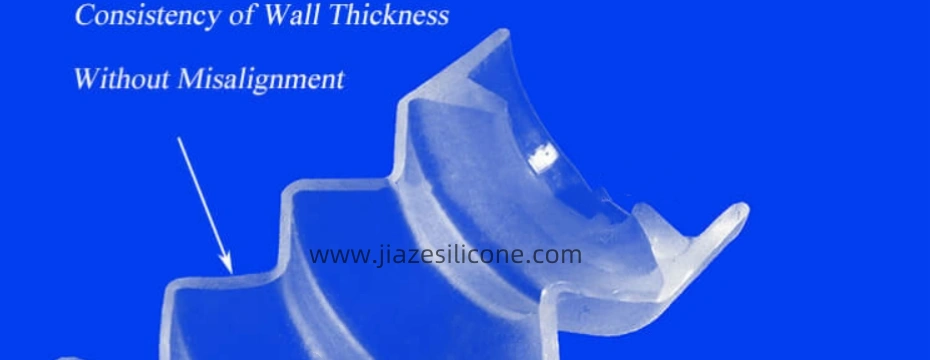
- Uniform Wall Thickness: Variations in thickness can cause uneven filling, leading to flash formation.
- Avoid Sharp Edges: Sharp transitions increase the likelihood of material seepage and burrs.
c. Gate and Runner System
- Gate Placement: Position gates strategically to ensure even filling and reduce injection pressure on the mold’s edges.
- Cold Runner Systems: Optimize cold runners to prevent material buildup that could increase pressure.
3. Material Selection
LSR materials have unique flow properties that can impact flash and burr formation.
- Viscosity Control: Choose an LSR grade with suitable viscosity for your application. Lower-viscosity materials flow easily but may increase flash risks.
- Shrinkage Behavior: Use materials with predictable shrinkage characteristics to ensure a snug fit between mold components.
4. Injection Molding Process Optimization
Optimizing processing parameters is crucial for minimizing flash and burrs.
a. Clamping Force
- Ensure Proper Clamping: Use sufficient clamping force to hold the mold halves together and prevent material from escaping. Over-clamping, however, can damage the mold or equipment.
b. Injection Pressure
- Adjust Injection Pressure: High pressure can force material into gaps, causing flash. Maintain a balance between pressure and flow rate to fill the cavity without excessive force.
c. Temperature Control
- Mold Temperature: Keep mold temperatures consistent to avoid warping and misalignment. Hotter molds may cause material to flow too easily into gaps.
- Barrel Temperature: Monitor LSR material temperatures in the injection unit to avoid excessive flowability.
d. Shot Size
- Calibrate Shot Volume: Overfilling the mold cavity increases pressure and the risk of flash. Precisely calculate and set the required shot size for each part.
5. Tooling Maintenance and Inspection
Regular maintenance is critical to ensuring mold performance.
a. Mold Condition
- Inspect for Wear and Damage: Over time, mold components can wear down, creating gaps that allow material leakage. Regularly inspect for scratches, warping, or corrosion.
- Polish Parting Lines: Keep parting lines smooth and free of debris to maintain a tight seal.
b. Alignment
- Verify Mold Alignment: Misaligned mold halves are a primary cause of flash. Check alignment during each setup and recalibrate as needed.
c. Cleaning
- Remove Residual LSR: Leftover material can prevent proper sealing of the mold, leading to flash and burrs. Clean molds thoroughly between production cycles.
6. Automation and Advanced Techniques
Modern technologies can help enhance precision and reduce defects.
a. Automated Mold Closing
- Consistent Force Application: Automated systems are used to apply uniform closing force, reducing the risk of human error during setup.
b. Compression Molding Assistance
- Pre-Compression: A slight pre-compression step before full injection ensures the mold is sealed tightly before material flows into the cavity.
c. CAE Simulation
- Mold Flow Analysis: Use software tools to simulate the molding process. This helps predict and prevent potential issues like flash and uneven flow.
7. Quality Control
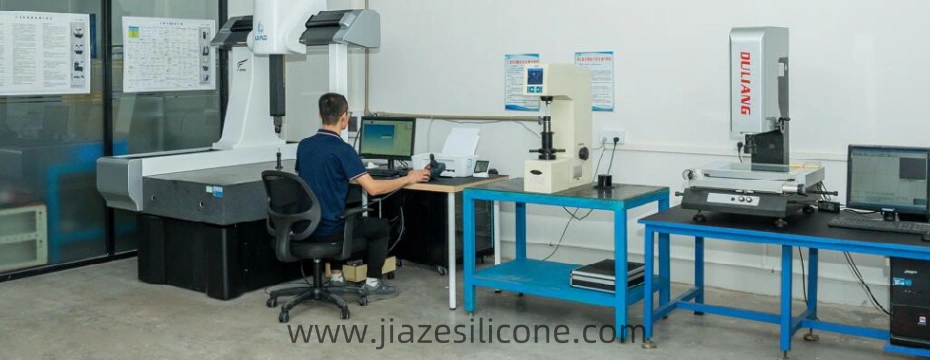
Implement stringent quality checks to identify and address issues early.
a. Process Monitoring
- Sensors and Data Logging: Equip machines with sensors to monitor key parameters like pressure, temperature, and clamping force. Immediate feedback allows operators to adjust settings in real-time.
b. Post-Molding Inspection
- Visual and Dimensional Checks: Inspect parts for flash and burrs after each cycle. Automated vision systems can improve detection accuracy.
8. Troubleshooting Common Issues
When flash or burrs occur despite preventive measures, systematic troubleshooting is key.
a. Flash Troubleshooting
- Check Injection Pressure and Clamping: Ensure both are within the recommended range.
- Inspect Mold Sealing Surfaces: Look for wear or misalignment.
- Reduce Mold Temperature: Lowering the temperature may increase material viscosity and reduce flash.
b. Burr Troubleshooting
- Refine Part Design: Modify sharp edges or thin sections that may create burrs.
- Optimize Gate Position: Move gates to reduce uneven material flow.
Conclusion
Preventing flash and burrs in LSR injection molding requires a holistic approach, combining well-designed molds, precise processing, and meticulous maintenance. By addressing each stage of the process—design, material selection, equipment setup, and quality control—you can minimize defects and produce high-quality parts. Regular monitoring and adopting advanced techniques, such as automation and simulation, can further enhance consistency and efficiency in production.