Liquid Silicone Rubber (LSR) injection molding is widely regarded as a leading manufacturing process for producing high-precision, durable, and flexible silicone parts. One of the key components that can significantly impact the efficiency and cost-effectiveness of this process is the runner system used to deliver the material into the mold cavities. Among the options available, cold runner systems stand out as a highly beneficial choice for LSR injection molding. This document explores the benefits of cold runner systems in detail, emphasizing their economic, environmental, and operational advantages.
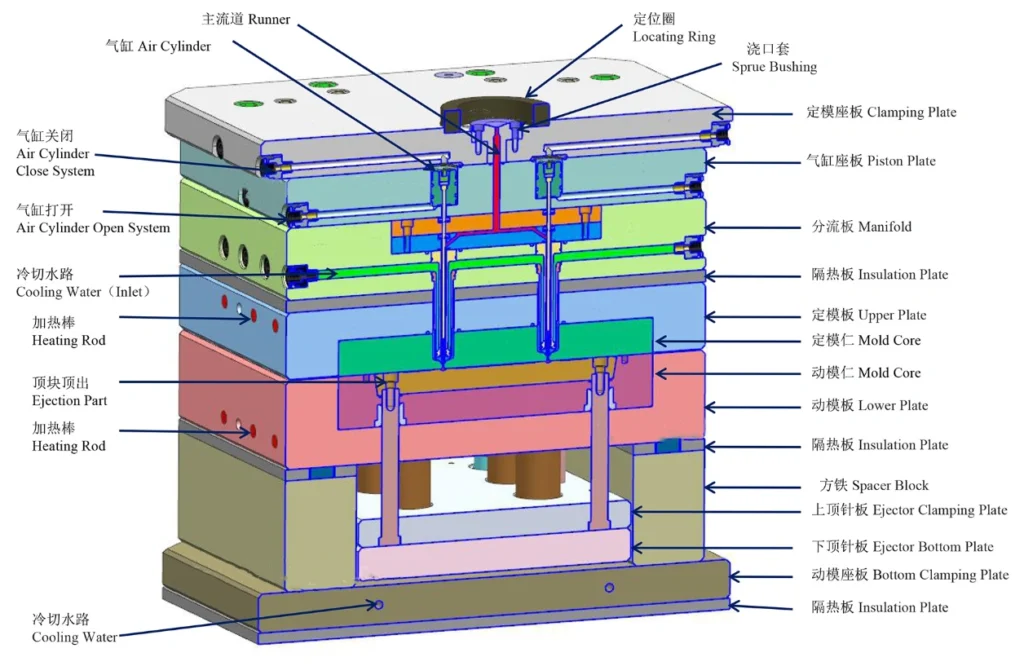
1. Reduced Material Waste
In traditional hot runner or open-gate systems, the liquid silicone material often solidifies in the runner, creating waste that must be removed and discarded or reprocessed. Cold runner systems, however, maintain the material in a liquid state throughout the injection process. By eliminating solidified runners, these systems dramatically reduce material waste. This is particularly important for LSR, as the material is relatively expensive, and waste can significantly impact production costs.
Moreover, reducing waste aligns with environmental sustainability goals. By minimizing the amount of discarded material, manufacturers can reduce their ecological footprint and contribute to a more sustainable production process.
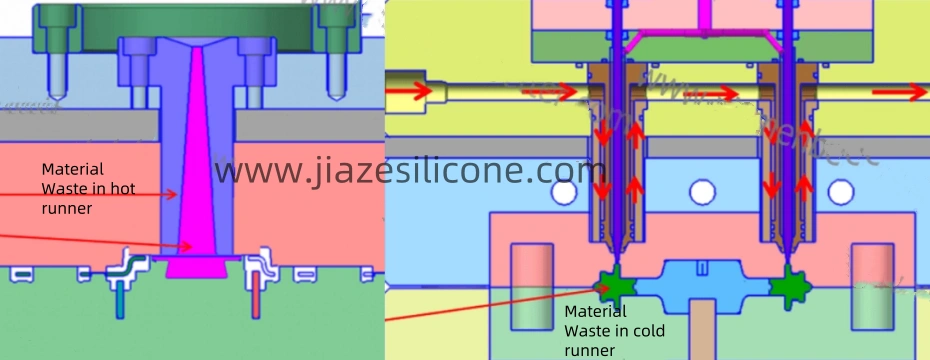
2. Improved Cost Efficiency
The reduction in material waste directly translates into cost savings. In high-volume production scenarios, the savings can be substantial, as less raw material is required to produce the same number of parts. Additionally, cold runner systems reduce the labor and energy costs associated with removing, grinding, and recycling solidified silicone.
The initial investment in a cold runner system may be higher than that for a traditional system, but the long-term operational savings often outweigh this cost. Over time, the return on investment (ROI) becomes evident through reduced material usage and lower waste management expenses.
3. Enhanced Product Quality
Cold runner systems enable precise control over the material flow and injection process, leading to higher-quality finished products. By maintaining consistent material properties and preventing premature curing, these systems ensure that each part meets stringent specifications for dimensional accuracy, strength, and flexibility.
Furthermore, the elimination of runner solidification prevents potential defects such as flow marks or inconsistencies in material distribution. This level of quality assurance is crucial for industries like medical, automotive, and electronics, where LSR components must adhere to strict performance standards.
4. Shorter Cycle Times
Cold runner systems contribute to shorter cycle times by streamlining the injection and curing processes. Without the need to handle solidified runners, manufacturers can focus solely on molding and curing the actual parts. This efficiency not only boosts production rates but also reduces energy consumption, making the entire process more sustainable.
Additionally, shorter cycle times enable manufacturers to respond more quickly to market demands, increasing their competitiveness in fast-paced industries.
5. Flexibility and Design Freedom
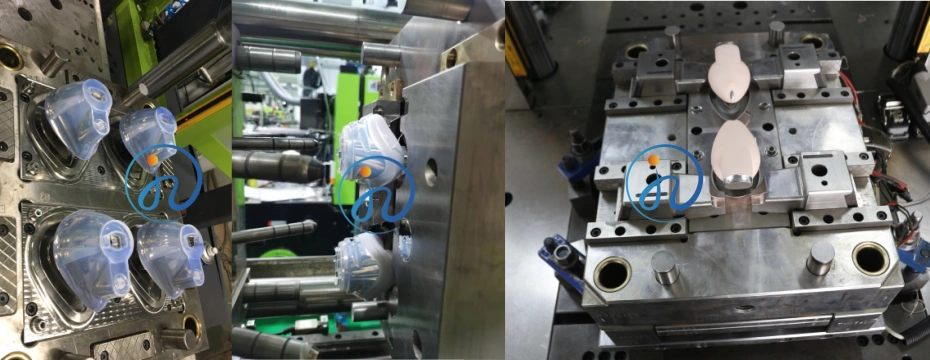
Cold runner systems offer greater flexibility in mold design, allowing manufacturers to produce complex geometries and multi-cavity molds with ease. The system’s ability to deliver material uniformly across multiple cavities ensures consistent quality and reduces the likelihood of defects.
This flexibility is particularly beneficial for producing intricate or miniaturized components, such as those used in medical devices or consumer electronics. The precise control offered by cold runner systems also facilitates the integration of advanced features, such as undercuts or thin walls, which might be challenging with other runner systems.
6. Reduced Post-Processing Requirements
Traditional runner systems often require additional post-processing steps to remove solidified runners and clean the molded parts. Cold runner systems eliminate this need, as the material remains in a liquid state and does not form excess solid parts. This reduction in post-processing saves time, labor, and resources, further enhancing the cost-efficiency of the production process.
The elimination of post-processing steps also minimizes the risk of damaging delicate parts, ensuring that the finished products maintain their integrity and performance characteristics.
7. Environmental Benefits
By significantly reducing material waste and energy consumption, cold runner systems support environmentally friendly manufacturing practices. The lower material usage reduces the demand for raw silicone, conserving natural resources and lowering the carbon footprint associated with material production and transport.
Additionally, the reduced need for post-processing and shorter cycle times decrease the overall energy consumption of the production process. These environmental benefits align with the growing emphasis on sustainability in manufacturing, helping companies meet regulatory requirements and appeal to eco-conscious customers.
8. Improved Operational Efficiency
Cold runner systems streamline the entire injection molding process, reducing downtime and maintenance requirements. The system’s precision and reliability minimize the likelihood of defects and malfunctions, ensuring smooth and uninterrupted production.
The reduced need for cleaning and maintenance also enhances uptime, allowing manufacturers to maximize their operational capacity. This efficiency is particularly valuable in high-volume production environments, where even minor disruptions can lead to significant delays and costs.
9. Compatibility with Automation
Cold runner systems are well-suited for integration with automated production lines, further enhancing their efficiency and scalability. Automated systems can precisely control the injection parameters, monitor the production process, and handle the molded parts with minimal human intervention. This compatibility with automation reduces labor costs and ensures consistent quality across large production runs.
Conclusion
Cold runner systems offer a wide range of benefits for LSR injection molding, from reduced material waste and improved cost efficiency to enhanced product quality and operational flexibility. By addressing key challenges such as material waste, cycle time, and post-processing requirements, these systems enable manufacturers to achieve higher productivity and sustainability. As industries continue to demand high-quality, cost-effective, and environmentally friendly production solutions, cold runner systems are poised to play an increasingly important role in the future of LSR injection molding.