Liquid Silicone Rubber (LSR) injection molding is a versatile process used for manufacturing high-precision parts in industries such as medical, automotive, consumer products, and electronics. One critical metric for evaluating the efficiency of the LSR molding process is cycle time, which directly impacts production rates and costs. Understanding the typical cycle time involves examining various factors, including material properties, part geometry, mold design, and process parameters.
Overview of the LSR Injection Molding Process
LSR injection molding is a multi-step process consisting of:
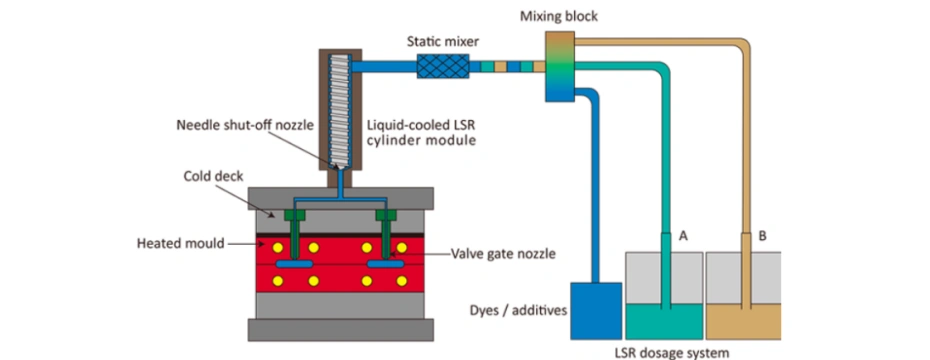
- Material Preparation: LSR is a two-part thermosetting material, typically mixed in a 1:1 ratio of Part A (containing the catalyst) and Part B (containing the crosslinker).
- Injection: The material is injected into a heated mold under high pressure.
- Curing: The LSR crosslinks and solidifies within the mold at elevated temperatures.
- Ejection: The molded part is ejected after curing, often requiring minimal or no post-processing.
The entire cycle time is a sum of these steps, with curing time being the dominant factor.
Typical Cycle Time in LSR Molding
In general, LSR injection molding cycle times range from 15 seconds to 3 minutes per part, depending on the complexity and size of the part, the curing temperature, and other variables. Here’s a detailed breakdown of factors affecting cycle time:
1. Material Properties
- Curing Behavior: LSR is a thermoset material that cures through a crosslinking reaction. The curing time depends on the formulation of the LSR material and the processing temperature. Materials with faster curing properties can significantly reduce cycle time.
- Viscosity: The low viscosity of LSR enables quick mold filling, reducing the injection time in the cycle.
2. Part Geometry and Size
- Thickness: Thicker parts generally require longer curing times because heat must penetrate the entire part for uniform crosslinking. Thin-walled parts cure faster but require precision in mold design to ensure complete filling.
- Complexity: Parts with intricate designs or undercuts may require additional time for mold filling and may also prolong the ejection phase due to the need for careful demolding.
3. Mold Design and Configuration
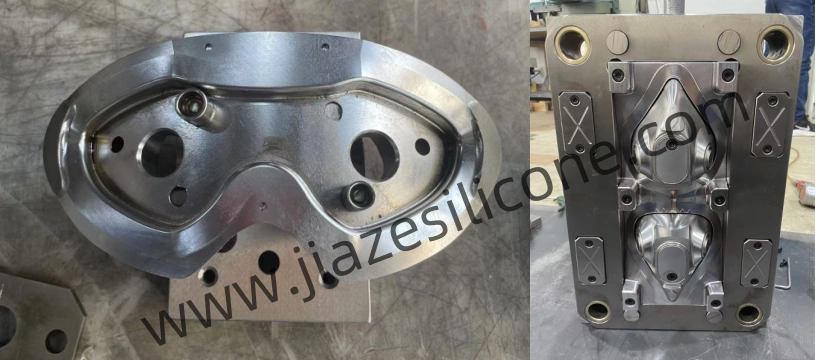
- Cavitation: Multi-cavity molds can produce multiple parts in a single cycle, optimizing production efficiency. However, higher cavitation may demand more robust injection systems, potentially affecting injection and curing times.
- Thermal Management: Mold temperature control is critical. Uniform heating ensures consistent curing and prevents defects. Advanced molds with integrated heating systems can reduce cycle time by maintaining optimal curing temperatures.
- Ejection Mechanism: Automated ejection systems streamline the removal of finished parts, reducing overall cycle time.
4. Processing Parameters
- Injection Speed: Faster injection reduces the filling time. However, the speed must be optimized to prevent defects such as air entrapment or incomplete filling.
- Curing Temperature: Higher mold temperatures accelerate curing but must be within the material’s recommended range to avoid degradation or defects. Typical mold temperatures range from 160°C to 200°C.
- Pressure: Sufficient pressure is necessary to ensure complete filling and compacting of the material. Insufficient pressure can lead to defects, increasing the need for rework and thereby extending production time.
5. Automation and Technology
- Injection Molding Machines: Modern LSR molding machines equipped with precise controls for temperature, pressure, and timing can significantly reduce cycle times.
- Automation: Automated handling systems for material feeding, part ejection, and inspection minimize manual intervention and reduce downtime between cycles.
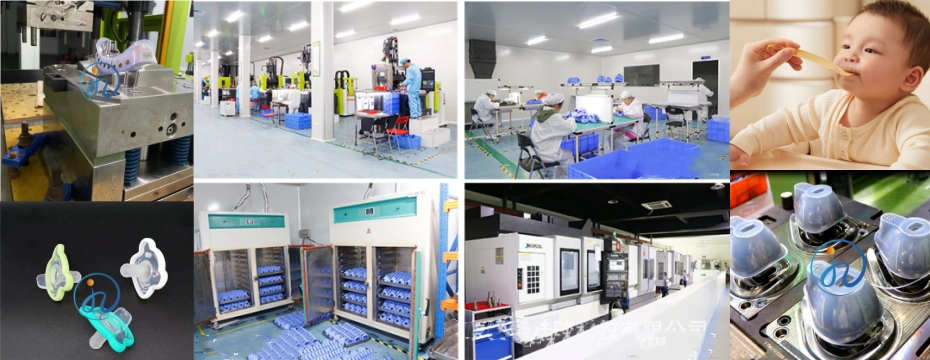
6. Secondary Processes
In many cases, LSR parts require minimal secondary processes, as they are produced flash-free and often meet dimensional specifications right out of the mold. However, additional steps like post-curing (for applications requiring enhanced mechanical or chemical properties) can impact the overall production time.
Optimizing Cycle Time
Manufacturers can adopt several strategies to minimize cycle time without compromising quality:
- Optimized Mold Design: Utilize advanced mold designs with efficient thermal management systems.
- Material Selection: Choose materials with faster curing properties while meeting the application requirements.
- Process Automation: Implement automation for material handling, molding, and ejection processes.
- Process Monitoring and Control: Use real-time monitoring systems to ensure consistency and identify bottlenecks.
- Regular Maintenance: Ensure molds and machines are well-maintained to prevent unexpected downtime.
Typical Applications and Their Cycle Times
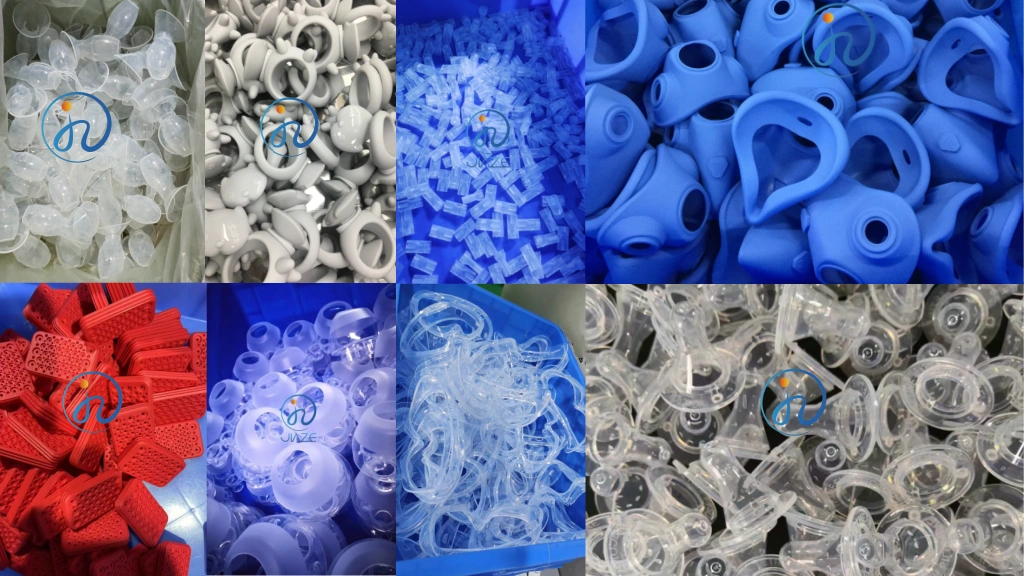
- Medical Devices: Small, precision parts such as seals and valves may have cycle times of 20–30 seconds, as they are often thin-walled and require high precision.
- Automotive Components: Larger and more complex parts like gaskets or connectors can have cycle times of 1–2 minutes due to increased material volume and geometry complexity.
- Consumer Products: Applications like baby bottle nipples or wearable device components may have cycle times of 15–45 seconds, balancing size and complexity.
Challenges in Reducing Cycle Time
- Heat Transfer Limitations: Heat must penetrate the entire part for uniform curing, limiting the amount of cycle time that can be reduced for thick parts.
- Material Constraints: Some applications require specific LSR formulations with slower curing times for enhanced properties.
- Quality Control: Reducing cycle time too aggressively may lead to defects such as incomplete curing, voids, or flashes.
Conclusion
The typical cycle time for LSR injection molding ranges from 15 seconds to 3 minutes, influenced by factors such as material properties, part geometry, mold design, and process parameters. While curing time dominates the cycle, optimizing mold design, material selection, and automation can significantly enhance efficiency. Achieving the optimal balance between speed and quality is critical for manufacturers aiming to maximize productivity while maintaining product integrity.