Liquid Silicone Rubber (LSR) injection molding is widely used for producing high-precision parts with exceptional durability, flexibility, and resistance to extreme temperatures and chemicals. Proper maintenance of LSR molds is critical to ensure consistent product quality, extend mold life, and minimize downtime. Below is an in-depth guide to LSR injection mold maintenance, covering essential practices, tools, and troubleshooting.
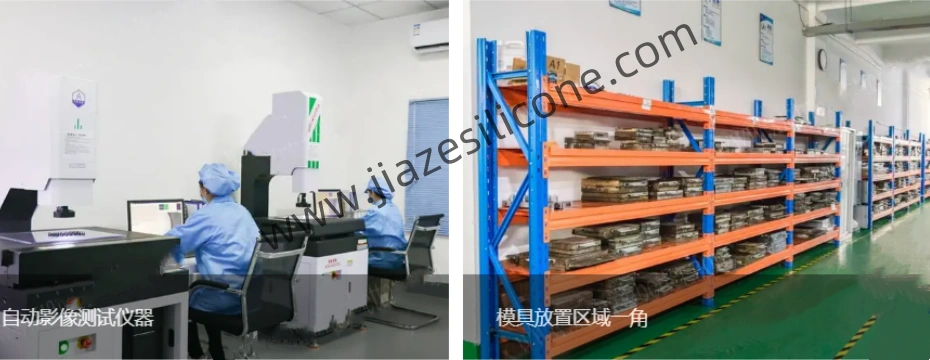
1. Importance of LSR Injection Mold Maintenance
Molds are a significant investment, and their upkeep directly affects production efficiency and cost-effectiveness. Key reasons to prioritize maintenance include:
- Consistent Quality: Maintained molds ensure the accurate production of parts with tight tolerances.
- Extended Mold Life: Regular care reduces wear and tear, extending mold usability.
- Operational Efficiency: Preventive maintenance minimizes unexpected downtimes and costly repairs.
- Cost Savings: Addressing minor issues promptly prevents expensive overhauls or mold replacements.
2. Components of an LSR Mold
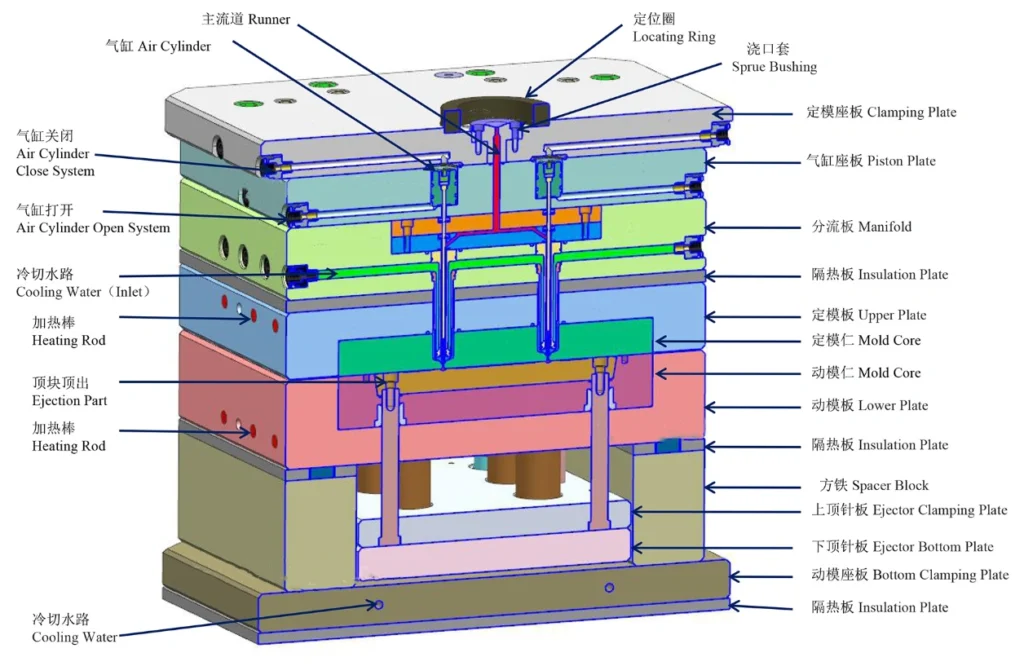
Understanding the structure of an LSR mold is vital for effective maintenance. Key components include:
- Mold Cavity and Core: The primary areas shaping the product. Any surface imperfections here directly affect part quality.
- Sprue and Runner System: Channels that deliver silicone to the cavities.
- Ejector Pins: Responsible for removing finished parts without damage.
- Cooling/Heating Channels: Regulate mold temperature for precise curing.
- Sealing Elements: Prevent material leakage during injection.
Each of these components requires specific attention during maintenance.
3. Types of Maintenance
Maintenance activities are categorized based on frequency and purpose:
a. Preventive Maintenance
Scheduled checks to avoid equipment failure. This includes:
- Cleaning: Remove silicone residues and contaminants using appropriate solvents and tools.
- Lubrication: Ensure moving parts, like ejector pins, are adequately lubricated to reduce friction.
- Inspection: Use magnification tools to identify cracks, burrs, or surface irregularities in cavities and cores.
b. Corrective Maintenance
Addressing issues that arise during production, such as:
- Repairing damaged cavities or replacing worn-out components.
- Removing flash buildup from vent lines or parting lines.
c. Predictive Maintenance
Leveraging technology to forecast potential failures using:
- Sensors to monitor temperature and pressure fluctuations.
- Software to track mold performance and maintenance history.
4. Essential Maintenance Steps
Step 1: Cleaning the mold
- After Every Cycle: Use compressed air or a soft brush to remove silicone debris from the mold surface.
- Periodic Deep Cleaning: Apply mild solvents or ultrasonic cleaning for stubborn residues.
- Avoid abrasive materials that could damage mold surfaces.
Step 2: Inspection
- Visual Check: Look for visible wear, corrosion, or cracks.
- Dimensional Check: Use calipers or gauges to confirm that dimensions meet specifications.
- Thermal Channels: Verify that cooling/heating lines are free from blockages.
Step 3: Lubrication
- Use silicone-compatible lubricants for ejector pins, sliding elements, and guide rails.
- Avoid over-lubrication, as excess grease can attract contaminants.
Step 4: Mold Storage in controlled room
- Clean and dry molds thoroughly before storage.
- Apply a protective anti-corrosion coating to prevent rust.
- Store molds in a controlled environment with stable temperature and humidity.
5. Common Maintenance Challenges and Solutions
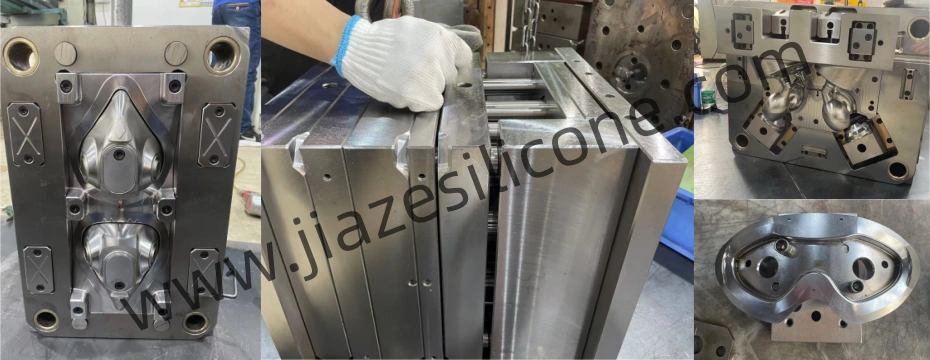
a. Flash Issues
- Cause: Worn parting lines or insufficient clamping force.
- Solution: Repair or polish parting lines and ensure clamping force settings are accurate.
b. Material Build-Up
- Cause: Incomplete cleaning of curing silicone.
- Solution: Schedule regular cleaning sessions and ensure the use of appropriate solvents.
c. Cooling/Heating Inefficiencies
- Cause: Blocked or corroded channels.
- Solution: Flush channels with cleaning agents designed for LSR mold systems.
d. Surface Imperfections
- Cause: Scratches or corrosion on the mold cavity.
- Solution: Polish affected areas or, if severe, replace damaged components.
6. Tools and Equipment for Maintenance
- Cleaning Tools: Brushes, compressed air, ultrasonic cleaners, and mild solvents.
- Inspection Tools: Magnifying glasses, microscopes, calipers, and non-destructive testing devices.
- Repair Tools: Polishing stones, grinding equipment, and laser welding systems for repairs.
- Storage Supplies: Anti-rust sprays, protective wraps, and humidity-controlled storage cabinets.
7. Maintenance Best Practices
- Train Personnel: Equip maintenance staff with proper training on mold handling and care.
- Documentation: Maintain detailed records of maintenance activities, including inspection results and repairs performed.
- Partner with Experts: Work with mold manufacturers for professional inspections and repairs when necessary.
- Use Quality Materials: Employ high-grade lubricants, cleaning agents, and spare parts compatible with LSR systems.
8. Advancements in Maintenance Technology
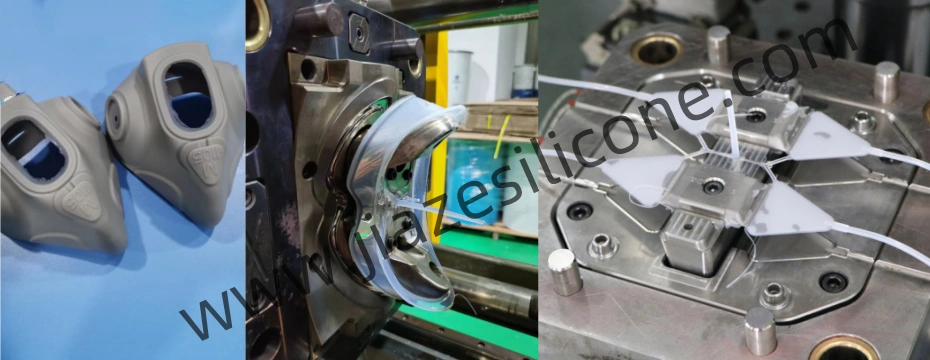
The integration of smart technologies has revolutionized mold maintenance:
- IoT Sensors: Monitor real-time mold performance, detecting anomalies before they cause issues.
- Automated Cleaning Systems: Reduce manual cleaning efforts while ensuring thorough removal of residues.
- Digital Twins: Simulate mold performance under various conditions, predicting maintenance needs accurately.
9. Frequency of Maintenance
The frequency depends on production volume, mold complexity, and material properties:
- Daily Maintenance: Quick cleaning and inspection at the end of each shift.
- Weekly Maintenance: Deeper cleaning, lubrication, and inspection of all components.
- Monthly/Quarterly Maintenance: Comprehensive checks, including thermal channel flushing and surface polishing.
- Annual Maintenance: Complete disassembly for a thorough inspection, repairs, and calibration.
10. Conclusion
Effective maintenance of LSR injection molds ensures sustained production quality, reduces operational costs, and extends mold life. By adopting a proactive approach, leveraging advanced tools, and following industry best practices, manufacturers can optimize their LSR molding processes and maintain a competitive edge.