Liquid silicone rubber (LSR) injection molding is a specialized process for creating durable, flexible, and heat-resistant products using liquid silicone rubber. It’s a go-to method in industries requiring high-quality, precision silicone parts such as medical devices, automotive components, and consumer products. Let’s dive into the details of the LSR injection molding process, covering its principle, equipment, process flow, and key advantages.
1. Principle of LSR Injection Molding
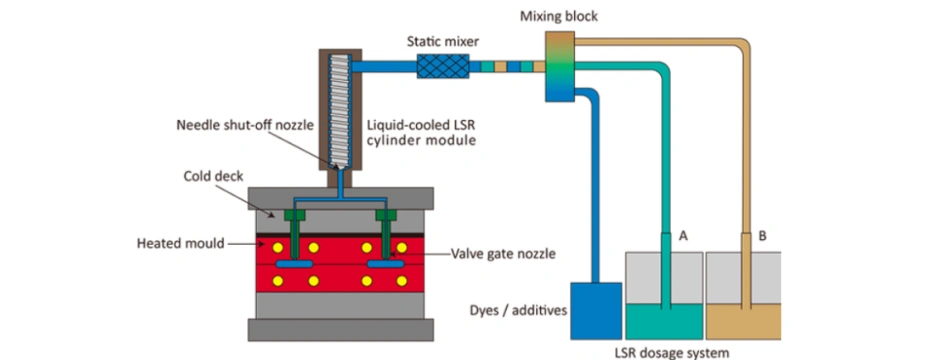
At its core, LSR injection molding is about injecting a two-part, thermoset liquid silicone into a mold cavity where it is heated to solidify into a final part. Thermoset materials differ from thermoplastics in that they irreversibly cure when subjected to heat, creating a strong, permanent bond between the molecular chains. This gives silicone rubber parts exceptional temperature resistance and chemical stability.
The process uses a combination of heat and pressure to cure the silicone, enabling the production of complex, detailed, and durable parts. Key principles that drive LSR molding include precise temperature control, accurate material mixing, and high-pressure injection. These principles ensure consistency in producing parts with the desired characteristics and tight tolerances.
2. Equipment Used in LSR Injection Molding
The LSR injection molding process requires several specialized pieces of equipment, each serving a critical role:
a. Injection Molding Machine
- A specialized LSR injection molding machine uses a reciprocating screw or plunger mechanism to inject the silicone material into the mold cavity. The machine typically has a vertical or horizontal orientation, depending on the production setup.
b. Metering and Mixing Unit
- Liquid silicone rubber comes in two-part material, generally labeled Part A and Part B. The metering unit draws these two parts from separate reservoirs and sends them to the mixing unit, which blends them at a precise 1:1 ratio. Additionally, colorants or additives can be mixed in, depending on the product requirements.
c. Cold-Runner Mold
- LSR molds typically use a cold-runner system to maintain the silicone’s liquid state until it reaches the mold cavity. The cold-runner system helps reduce material waste by minimizing the amount of cured silicone in the runner channels and allows for consistent material flow into each cavity.
d. Heating System in the Mold
- Heating is essential for curing the LSR. The mold itself has built-in heating elements that raise its temperature, typically between 150–200°C (302–392°F), triggering the vulcanization (curing) process that solidifies the silicone. Temperature uniformity across the mold ensures consistent curing and helps prevent defects like under-cured sections.
3. LSR Injection Molding Process Flow
Here’s a step-by-step breakdown of how the LSR injection molding process works:
a. Preparation and Setup
- Parts A and B of the silicone are loaded into the machine’s reservoirs. The operator or automated system sets the correct temperature, pressure, and injection parameters based on the material and product requirements.
b. Material Mixing and Injection
- The machine draws the silicone materials in equal parts and sends them to the mixing chamber. Any desired additives or pigments are blended in at this stage to achieve specific material properties or colors.
- The mixed silicone is injected into the mold cavity using high pressure, ensuring the material fills every part of the mold to achieve the precise details and tolerances needed.
c. Curing in the Mold
- Once the silicone is injected, it sits in the heated mold cavity, where it undergoes a chemical reaction known as vulcanization. The heat from the mold accelerates the curing, causing the liquid silicone to transform into a solid, rubber-like form. This process can take anywhere from a few seconds to several minutes, depending on the part’s complexity and thickness.
d. Demolding
- After curing is complete, the mold opens, and the finished part is ejected, either manually or by automated systems, depending on the production scale. LSR’s inherent flexibility often allows for automatic ejection without damaging the part.
- Since the mold remains hot and the silicone is a thermoset material, the cured part maintains its shape and strength immediately upon ejection.
e. Post-Processing (If Necessary)
- Some LSR molded parts may require secondary processes, like trimming, inspection, or sterilization (especially for medical applications). However, post-processing is minimal in LSR molding due to the high precision and near-flash-free nature of the process.
4. Advantages of LSR Injection Molding
LSR injection molding has several advantages, making it the preferred method for silicone part production:
a. High Precision and Complexity
- LSR injection molding allows for intricate designs with tight tolerances and complex geometries, often without requiring additional machining. The process can produce parts with fine details and undercuts, which are challenging to achieve with other molding methods.
b. Material Properties of Silicone
- Silicone rubber’s heat resistance, flexibility, and biocompatibility make it suitable for diverse applications. It can withstand temperatures from -50°C to 200°C (-58°F to 392°F) and is chemically stable, making it resistant to aging, UV exposure, and many chemicals.
c. High Throughput
- LSR injection molding is a rapid process due to its ability to quickly fill the mold cavity and cure the material. This allows for high-volume production with consistent part quality. Additionally, the cold-runner system reduces waste, helping manufacturers save on material costs and contributing to efficiency.
d. Reduced Waste
- The use of a cold-runner system in LSR injection molding minimizes silicone waste by keeping the runner channels cool and reducing the amount of cured silicone that needs to be trimmed off.
e. Automated Process
- LSR injection molding is highly automated, enabling manufacturers to achieve repeatable, high-quality results with minimal manual intervention. This automation further increases throughput and ensures each part meets stringent quality standards.
f. Biocompatibility for Medical Applications
- Many LSR materials are biocompatible, making them safe for medical devices and implants. The non-reactive, hypoallergenic nature of silicone also makes it ideal for use in skin-contact applications like wearables, orthotics, and baby products.
5. Applications of LSR Injection Molding
LSR injection molding’s versatility makes it popular across numerous industries:
- Medical and Healthcare: LSR’s biocompatibility and ability to withstand sterilization processes make it ideal for implants, medical tubing, and seals.
- Automotive: Components like gaskets, seals, and connectors benefit from silicone’s heat and chemical resistance.
- Consumer Goods: Products like kitchen utensils, baby care items, and electronics are often made from LSR for its safety and durability.
- Electronics: LSR’s insulating properties make it suitable for encapsulating and protecting sensitive electronic components.
6. Challenges and Considerations
While LSR injection molding offers numerous benefits, it also has challenges:
- High Initial Tooling Costs: LSR molds require precise machining, which can be costly upfront, though these costs can be offset by high-volume production.
- Temperature Sensitivity in the Mixing Process: Precise temperature control is essential since LSR materials can prematurely cure if the equipment isn’t properly regulated.
- Shrinkage and Flashing: Silicone can sometimes flash in the mold, although this is minimized with precise mold design and the cold-runner system.
Conclusion
Liquid silicone injection molding is a highly efficient, precise process for manufacturing high-quality silicone rubber parts. The process uses the unique thermosetting properties of silicone, combined with advanced machinery, to produce durable parts suitable for a wide range of industries. From medical devices to automotive and consumer goods, LSR injection molding continues to be an essential process due to its ability to produce complex, biocompatible, and highly resistant silicone parts with minimal waste and high consistency.