Liquid Silicone Rubber (LSR) Overmolding is a specialized manufacturing process where a layer of liquid silicone rubber is molded over another material or substrate, typically to create a single, unified part. This process is widely used in various industries, including medical devices, automotive components, consumer electronics, and more, due to its ability to provide durable, biocompatible, and flexible properties. Here’s a deep dive into the process, applications, benefits, challenges, and considerations in over-molding with LSR.
1. Overview of Liquid Silicone Rubber (LSR)
- What is LSR? LSR is a two-part, platinum-cured elastomer that is typically processed through injection molding. It is known for its high thermal stability, low compression set, and ability to withstand extreme environmental conditions.
- Material Properties: LSR is chemically stable, resistant to moisture, and offers excellent electrical insulation properties. It maintains flexibility at low temperatures and is resistant to extreme heat, which makes it ideal for demanding applications.
- Why Use LSR for Overmolding? LSR’s properties, such as biocompatibility, flexibility, and high durability, make it ideal for overmolding applications where it needs to bond with a harder substrate while providing a soft-touch exterior or adding sealing capabilities.
2. What is Overmolding?
- Definition: Overmolding is a process where a secondary material (LSR, in this case) is molded over an initial substrate, which could be made of metal, plastic, or another silicone rubber. The result is a composite part that combines the properties of both materials.
- How It Works: Typically, the base material is injection-molded first, forming a rigid or semi-rigid substrate. The part is then transferred to a second molding station where LSR is injected over or around the base part, forming a seamless bond between the two materials.
3. Process of LSR Overmolding
- Preparation of Substrate: The initial component (substrate) must be prepared by removing any contaminants or oils that could interfere with the bonding process. This may involve cleaning or applying a primer.
- Molding Setup: The prepared substrate is placed into the LSR mold cavity. Precision is crucial during this step to ensure that the part is properly aligned, preventing any misalignment during the injection of LSR.
- Injection of LSR: The LSR is mixed and injected into the mold cavity using specialized LSR injection molding machines. These machines maintain precise temperature control and injection speed to ensure the LSR flows properly and cures without defects.
- Curing: After injection, LSR undergoes a curing process where the platinum-catalyzed reaction takes place, cross-linking the material and giving it its final elastomeric properties.
- Demolding and Finishing: After curing, the overmolded part is removed from the mold. Depending on the complexity of the design, some post-molding finishing processes like trimming or inspection may be required.
4. Applications of LSR Overmolding
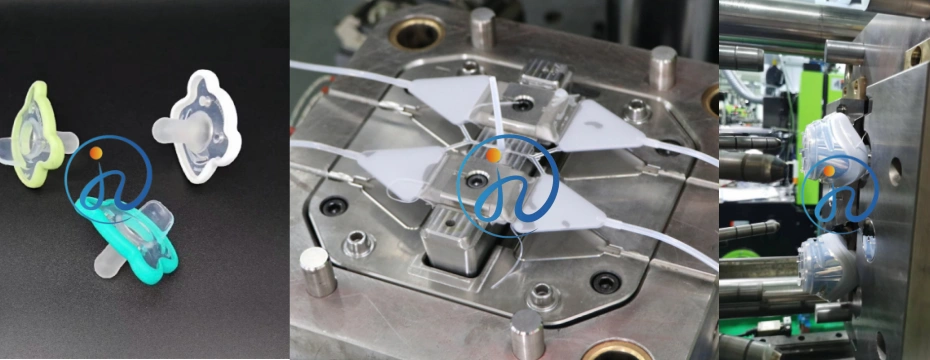
- Medical Devices: LSR overmolding is used to create medical devices that require biocompatibility and skin-safe properties. It can be used for products like syringes, catheters, or wearable medical devices, where a soft-touch, flexible layer is needed.
- Automotive Components: In the automotive industry, LSR is used to overmold parts like seals, gaskets, connectors, and ergonomic grips. Its resistance to heat and chemicals makes it suitable for parts exposed to harsh automotive environments.
- Consumer Electronics: LSR overmolding is ideal for creating shock-absorbing or water-resistant seals for electronic devices such as smartphones, wearable devices, or portable speakers. It can help achieve the desired ergonomic feel while providing a protective layer.
- Household Products: LSR overmolding is often used in kitchenware, like spatulas or handles, where a heat-resistant and easy-to-grip surface is required. It can also be found in children’s toys, thanks to its non-toxic and durable nature.
5. Benefits of LSR Overmolding
- Enhanced Product Functionality: Overmolding with LSR can add new functionalities like waterproofing, sealing, or insulation to existing parts. It provides a soft-touch grip, which enhances user comfort and safety.
- Design Flexibility: The ability to mold LSR over various substrates allows designers to combine rigid and flexible materials in complex geometries. This flexibility can improve product performance and aesthetic appeal.
- Improved Durability: LSR’s resistance to UV light, extreme temperatures, and harsh chemicals extends the lifespan of overmolded products. This makes it an ideal choice for outdoor and industrial applications.
- Cost-Effectiveness: The integration of LSR overmolding into the manufacturing process can reduce the need for secondary assembly steps. Such as gluing or fastening different components together, thereby lowering production costs.
6. Challenges of LSR Overmolding
- Bonding Challenges: Achieving a strong bond between the LSR and the substrate can be challenging. Factors like substrate material, surface roughness, and the use of primers can significantly influence the bond quality. For some substrates, achieving chemical adhesion might require surface treatments or additional bonding agents.
- Tooling and Mold Design: Designing molds for LSR overmolding can be complex due to the precise tolerances required. The mold must accommodate both the initial substrate and the overmolded LSR, ensuring proper alignment and parting lines. The flow characteristics of LSR also need to be carefully managed to prevent defects like flashing or air entrapment.
- Cycle Times: LSR typically has longer curing times compared to thermoplastics. This can impact the cycle time and overall production speed. Advanced LSR injection molding machines with temperature controls can help optimize curing times. But balancing speed with quality remains a key challenge.
7. Considerations for LSR Overmolding
- Material Compatibility: Not all materials are compatible with LSR, so choosing the right substrate is critical. Common substrates include various thermoplastics like polycarbonate (PC), nylon, and ABS, as well as metals. The chemical nature of the substrate affects how well the LSR bonds with it.
- Design for Manufacturability (DFM): Designing the parts with overmolding in mind can help avoid issues during production. This includes accounting for shrinkage, designing appropriate draft angles, and minimizing undercuts that could complicate demolding.
- Regulatory Requirements: For industries like medical and food, regulatory standards (e.g., FDA or ISO certifications) may dictate the choice of LSR material and processing methods. It’s important to ensure that the selected LSR meets the required standards for biocompatibility and safety.
8. Advancements and Trends in LSR Overmolding
- Automation in LSR Injection Molding: Automation has become a significant trend in LSR overmolding. Robots can be used to transfer substrates between different molding stations, increasing precision and reducing labor costs. Automated systems also improve consistency and reduce the risk of contamination, which is crucial in medical applications.
- Multi-Shot Overmolding: Multi-shot overmolding allows for the simultaneous or sequential injection of different materials, creating parts with multiple layers in a single process. This can be used to create products with varying durometers (hardness) or to integrate colored LSR layers for aesthetic purposes.
- Micro-Molding: LSR overmolding is increasingly being used in micro-molding applications, where extremely small parts are required. This is particularly relevant in medical and electronic components, where miniaturization is a trend. Micro-molding with LSR allows for the precise production of tiny, intricate parts that still require flexibility and durability.
9. Case Studies and Real-world Examples
- Medical Syringe Overmolding: A typical application involves over-molding a soft-touch LSR layer over a hard plastic syringe barrel to provide comfort during use. The LSR’s biocompatibility and chemical resistance make it suitable for such applications.
- Automotive Connector Seals: LSR is often used to overmold electrical connectors in automotive applications, providing a durable seal that resists moisture and dust while withstanding temperature variations. This ensures the reliable performance of electrical systems.
- Consumer Device Casings: In products like smartphones, LSR overmolding can create a seamless, protective layer that absorbs shocks and provides a better grip. The LSR layer also helps achieve a waterproof seal, extending the product’s lifespan.
Conclusion
Liquid Silicone Rubber overmolding is a powerful process that combines the flexibility and durability of LSR with the structural properties of other substrates. It allows for the creation of multi-material parts that meet the demanding requirements of various industries, from medical devices to automotive components. While the process presents certain challenges, such as achieving a strong bond and managing cycle times, advances in automation and mold design have significantly expanded its capabilities. Through thoughtful design and careful material selection, manufacturers can leverage LSR overmolding to create innovative products that offer superior performance and aesthetics.