The advantages of LSR for injection molding are vast and transformative. As an expert in the field, I have witnessed how LSR’s unique properties—such as thermal stability, elasticity, and biocompatibility—make it an optimal choice for various applications. This article delves into the exceptional qualities that set LSR apart, offering insights into its superior performance in demanding environments.
Key Benefits of LSR
- Enhanced Durability: LSR stands out as a premier material for injection molding.
- Cost-Effectiveness: Its ability to withstand extreme temperatures, resist wear and tear, and maintain precision in complex designs makes it invaluable across multiple industries.
Dive into this exploration of how LSR’s properties contribute to efficient, sustainable, and reliable production processes, ensuring high-quality outcomes in medical, automotive, electronics, and beyond.
Trick Properties of Liquid Silicone Rubber (LSR)
Introduction to Liquid Silicone Rubber (LSR)
Liquid Silicone Rubber (LSR) is a versatile material known for its special properties that make it optimal for injection molding. As an expert in the field, I have seen firsthand how the premium attributes of LSR contribute to its prevalent fostering in different industries. This section will look into the vital homes that establish LSR apart.
Thermal Stability
One of the most noteworthy homes of LSR is its phenomenal thermal stability. LSR can stand up to a variety of temperature levels, from as reduced as -60 ° C to as high as 200 ° C, without losing its physical residential or commercial properties. This makes it suitable for applications that need direct exposure to extreme temperature levels.
Elasticity and Flexibility
LSR is renowned for its superior flexibility and adaptability. Unlike various other products, LSR can be stretched and compressed consistently without permanent deformation. This residential or commercial property is particularly helpful in applications where toughness and long-lasting efficiency are vital.
Biocompatibility
An additional essential building of LSR is its biocompatibility. This material is safe and hypoallergenic, making it secure for usage in clinical gadgets and implants. Its inert nature makes sure that it does not respond with body tissues, which is essential for individual safety.
Resistance to Chemicals and UV Light
LSR exhibits excellent resistance to chemicals and UV light. It is unaffected by many solvents, acids, and bases, which makes it suitable for usage in harsh chemical atmospheres. In addition, its resistance to UV light avoids deterioration when exposed to sunshine, making certain longevity in outside applications.
Electric Insulation
LSR is likewise an excellent electric insulator. It has high dielectric stamina and reduced electrical conductivity, making it excellent for usage in electrical and electronic parts. This residential property ensures certain safety and integrity in electric applications.
Openness and Colorability
LSR can be produced to be either clear or tinted. Its intrinsic openness allows for the creation of clear components, which is beneficial in applications such as optical lenses. In addition, LSR can be conveniently colored to achieve a vast array of shades, giving versatility in style.
Cost-Effectiveness and Efficiency in Production
Product Utilization
One of the primary advantages of Liquid Silicone Rubber (LSR) in injection molding is its capability to lessen material wastefulness. Unlike conventional molding products, LSR can be precisely determined and infused, ensuring that just the necessary amount of product is utilized. This accuracy not only reduces the cost of basic materials but likewise decreases the ecological impact.
Cycle Time Reduction
The shot molding process with LSR is known for its fast cycle times. LSR treatments promptly at high-temperature levels, permitting faster manufacturing cycles contrasted to thermoplastic materials. This efficiency converted to greater throughput and reduced labor prices.
Automation Compatibility
LSR shot molding is very compatible with modern automation technologies. Automated systems can take care of the entire process– from product feeding to component ejection– consequently reducing the demand for manual labor and further reducing production costs. This automation also enhances consistency and quality assurance.
Energy Efficiency
Another cost-saving facet is the power effectiveness of the LSR molding procedure. The lower viscosity of LSR permits it to be processed at relatively reduced injection pressures, which suggests less power is needed for the molding process. This power performance equates to reduced functional prices with time.
Tooling and Maintenance
LSR molds often tend to have a longer lifespan contrasted to those used for other products. The product’s properties create less wear and tear on the molds, reducing the frequency and expense of maintenance. Furthermore, the high sturdiness of LSR molds adds to consistent product top quality over prolonged production runs.
Cost-Effectiveness Factors | Effect on Production |
---|---|
Product Utilization | Prolongs mold life-span decreases upkeep costs |
Cycle Time Reduction | Rises throughput, reduces labor prices |
Automation Compatibility | Lowers hands-on labor, improves consistency |
Energy Efficiency | Decreases functional energy expenses |
Tooling and Maintenance | Prolongs mold life-span, decreases upkeep costs |
Applications of Liquid Silicone Rubber in Various Industries
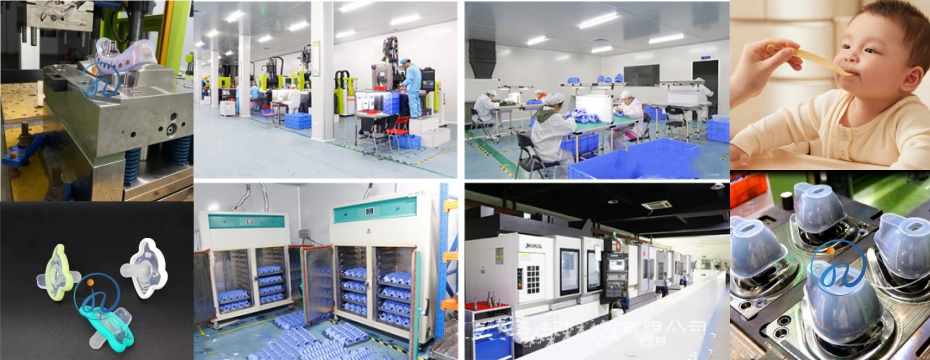
Medical and Healthcare
Liquid Silicone Rubber (LSR) is extensively used in the clinical and healthcare market because of its biocompatibility and resistance to germs. It is suitable for producing medical gadgets such as catheters, seals, and respiratory masks. LSR’s hypoallergenic residential properties make it ideal for applications that need long-term skin calls, such as prosthetics and wearable medical tools.
Automotive
In the automobile sector, LSR is valued for its longevity and capacity to stand up to extreme temperature levels. It is typically used in the manufacturing of gaskets, seals, and port covers. The material’s adaptability and strength make sure that it keeps its honesty under the rough conditions of automotive settings, contributing to the long life and dependability of automobile parts.
Consumer Electronics
LSR plays a vital function in the consumer electronic devices market. Its superb electrical insulation and residential properties make it perfect for making keypads, switches, and protective covers for digital tools. Additionally, LSR’s resistance to environmental factors such as UV light and wetness ensures the sturdiness and performance of electronic components.
Food and Beverage
The food and drink industry takes advantage of LSR’s non-toxic and food-safe attributes. It is used in the manufacturing of baking molds, cooking area utensils, and seals for food handling devices. LSR’s capacity to endure heat and its easy-to-clean nature make it a favored material for applications that call for regular sterilization and hygiene upkeep.
Aerospace
In the aerospace industry, LSR is used for its lightweight and high-performance properties. It is utilized in the manufacturing of seals, gaskets, and insulation parts that are required to be carried out reliably under severe problems of stress and temperature. The product’s capacity to preserve flexibility and functionality in challenging atmospheres makes it important for aerospace applications.
Child Care Products
LSR is likewise preferred in the production of childcare products such as pacifiers, container nipple areas, and teething playthings. Its safe, hypoallergenic, and soft-touch homes ensure the safety security, and comfort of products created for babies. The material’s toughness and simplicity of sterilization further enhance its viability for these sensitive applications.
Environmental and Safety Benefits of Using LSR
Eco-Friendly Material
One of the significant benefits of Liquid Silicone Rubber (LSR) is its environmental friendliness. LSR is a non-toxic product that does not launch harmful compounds during its production or use. This makes it an excellent choice for industries that prioritize sustainability. Additionally, LSR is immune to ozone and UV light, which decreases its ecological effect gradually.
Reduction in Waste
Injection molding with LSR dramatically decreases material waste. Unlike typical rubber molding procedures, LSR shot molding is highly precise, guaranteeing that only the required amount of material is made use of. This accuracy reduces excess material and reduces the need for post-production cutting and waste disposal.
Energy Efficiency
LSR’s handling requires reduced energy usage compared to other products. The shot molding process for LSR runs at lower temperatures, which converts to reduced power usage. This power efficiency not only lowers production expenses but also decreases the carbon footprint linked with production.
Safety and Security in Production and Use
LSR is naturally secure for both production employees and end-users. Throughout the shot molding process, LSR does not release volatile organic compounds (VOCs) or various other harmful by-products, guaranteeing a more secure working setting. Furthermore, items made from LSR are hypoallergenic and biocompatible, making them suitable for medical and food-grade applications.
Conformity with Regulatory Standards
LSR fulfills strict governing needs for environmental safety and security criteria. Its compliance with laws such as REACH, RoHS, and FDA standards ensures that items made from LSR are risk-free for usage in sensitive applications, including healthcare and durable goods.
Benefit | Description |
---|---|
Eco-Friendly | Non-toxic, does not release damaging substances. |
Waste Reduction | Very accurate molding minimizes material waste. |
Power Efficiency | Reduced power intake during processing. |
Security | No VOCs, hypoallergenic, biocompatible. |
Regulatory Compliance | Fulfills REACH, RoHS, FDA standards. |
FAQs: The Advantages of Liquid Silicone Rubber for Injection Molding
What is Liquid Silicone Rubber (LSR)?
Liquid Silicone Rubber (LSR) is a versatile, high-performance material known for its unique properties such as thermal stability, elasticity, biocompatibility, and resistance to chemicals and UV light. These characteristics make it ideal for injection molding applications across various industries.
Why is LSR preferred for injection molding?
LSR is preferred for injection molding due to its superior material properties, including high durability, flexibility, and precision in capturing intricate mold details. Additionally, LSR’s rapid curing times and compatibility with automation technologies enhance production efficiency and cost-effectiveness.
What are the key properties of LSR?
Key properties of LSR include exceptional thermal stability, elasticity, biocompatibility, resistance to chemicals and UV light, electrical insulation, and the ability to be manufactured in transparent or colored forms. These properties make LSR suitable for a wide range of applications.
How does LSR contribute to cost-effective production?
LSR contributes to cost-effective production by minimizing material wastage, reducing cycle times, being compatible with automation, and requiring less energy for processing. Additionally, LSR molds have a longer lifespan, reducing maintenance costs and ensuring consistent product quality.
In which industries is LSR commonly used?
LSR is commonly used in various industries, including medical and healthcare, automotive, consumer electronics, food and beverage, aerospace, and infant care products. Its unique properties make it suitable for applications that require durability, safety, and reliability.
What are the environmental and safety benefits of using LSR?
LSR is an eco-friendly material that does not release harmful substances during production or use. It reduces material waste through precise molding, consumes less energy during processing, and is safe for both production workers and end-users. LSR also meets stringent regulatory standards, ensuring safety and compliance in sensitive applications.
How does LSR enhance product longevity?
LSR enhances product longevity by providing exceptional resistance to wear and tear, maintaining its integrity under extreme temperatures, and offering flexibility and elasticity. These properties ensure that LSR-molded components last longer and require less frequent replacements, reducing overall maintenance costs.
What are the mechanical properties of LSR?
The mechanical properties of LSR include a Shore A hardness range of 10-80, tensile strength of 5-11 MPa, elongation at break of 200-1000%, and tear strength of 20-55 kN/m. These properties can be tailored to meet specific application requirements, providing versatility in design and functionality.
Is LSR suitable for medical applications?
Yes, LSR is highly suitable for medical applications due to its biocompatibility, non-toxic nature, and hypoallergenic properties. It is commonly used in the production of medical devices, implants, and wearable medical products, ensuring safety and comfort for patients.
How does LSR’s resistance to chemicals and UV light benefit its applications?
LSR’s resistance to chemicals and UV light ensures that it remains unaffected by many solvents, acids, bases, and sunlight exposure. This resistance prevents degradation and extends the lifespan of LSR-molded components, making them ideal for use in harsh chemical environments and outdoor applications.