
Choosing Between Liquid Silicone Rubber Injection Molding and High-Consistency Rubber
Choosing between Liquid Silicone Rubber Injection Molding and High-Consistency Rubber can be a pivotal decision for manufacturers. Each material boasts unique properties tailored to different production needs. In this article, I delve into their key differences, applications, and cost implications to guide you in selecting the right one for your project.
Key Differences
Liquid Silicone Rubber offers precision and speed for high-volume production, while High-Consistency Rubber provides durability and flexibility for robust applications. Understanding the nuances of each can significantly impact your manufacturing efficiency and product quality. Let’s explore which material aligns best with your specific requirements.
Key Differences Between Liquid Silicone Rubber and High-Consistency Rubber
When considering the choice between Liquid Silicone Rubber (LSR) Injection Molding and High-Consistency Rubber (HCR), it is important to understand their distinct qualities and applications. Both products supply one-of-a-kind residential properties that accommodate different production needs. Here, I will describe the main differences based on my experience in the field.
Product Composition and Properties
Fluid Silicone Rubber is a two-part platinum-cured elastomer that is known for its low thickness, enabling it to flow conveniently into molds. This characteristic makes it perfect for elaborate and comprehensive designs. On the other hand, High-Consistency Rubber, additionally described as gum tissue stock silicone, is a high-viscosity product that calls for additional handling to achieve the desired shape.
Particular | Liquid Silicone Rubber (LSR) | High-Consistency Rubber (HCR) |
---|---|---|
Viscosity | Low | High |
Healing Method | Platinum-cured | Peroxide or platinum-cured |
Handling | Shot molding | Compression or transfer molding |
Handling Techniques
The handling methods for LSR and HCR vary considerably. LSR Injection Molding is a very automated procedure that permits rapid manufacturing cycles and marginal waste. This technique is particularly valuable for high-volume manufacturing runs. On the other hand, HCR commonly involves compression or transfer molding, which can be extra labor-intensive and is better suited for lower-quantity manufacturing.
Layout Flexibility
Fluid Silicone Rubber supplies higher style flexibility because of its capacity to fill up complex mold and mildew precisely. This makes it an outstanding choice for items needing complex forms and fine information. High-consistency rubber, while still flexible, might require extra tooling and handling actions to achieve comparable results.
Performance Characteristics
Both LSR and HCR provide superb thermal security, chemical resistance, and resilience. However, LSR often provides superior clarity and openness, making it suitable for applications where aesthetic appeals are critical. HCR, with its robust mechanical buildings, is typically favored in applications demanding higher tensile stamina and resilience.
Price Implications
The expense implications of picking in between LSR and HCR can vary based on the project requirements. LSR Injection Molding typically sustains higher preliminary setup costs due to the demand for customized devices, however, it can be more cost-effective for massive production. HCR, with its easier handling needs, might offer expense advantages for smaller production runs.
Applications and Use Cases for Liquid Silicone Rubber Injection Molding
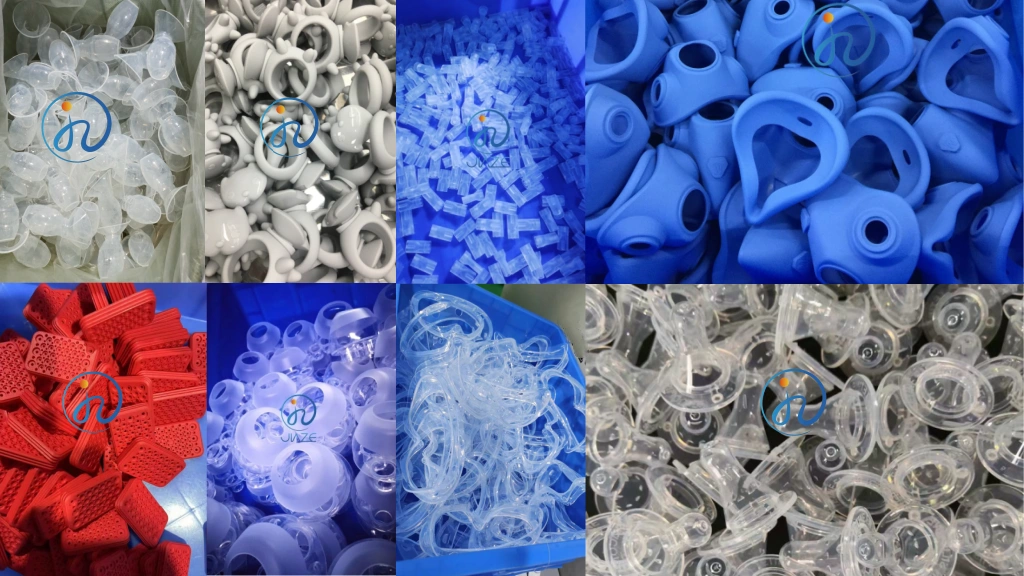
Medical Devices
Liquid Silicone Rubber (LSR) injection molding is thoroughly used in the medical market due to its biocompatibility, adaptability, and durability. Products such as catheters, seals, and gaskets are frequently manufactured utilizing LSR. The product’s capacity to endure sanitation procedures, including autoclaving and gamma radiation, makes it suitable for medical applications.
Consumer Products
In the consumer items sector, LSR is favored for products that need a soft touch and high longevity. Items such as baby container nipples, pacifiers, and kitchen utensils benefit from the product’s non-toxic and hypoallergenic properties. The shot molding process permits complex layouts and detailed details, boosting the capability and visual appeal of these items.
Automotive Components
The automotive sector leverages LSR injection molding for different components that need high efficiency under severe problems. LSR is used to generate parts like gaskets, seals, and ports that need to withstand high-temperature levels and direct exposure to extreme chemicals. The product’s outstanding thermal stability and resistance to maturing make it a trustworthy selection for automobile applications.
Electronics
LSR shot molding is additionally common in the electronic devices market, where it is used for manufacturing elements that require accurate measurements and high electrical insulation properties. Applications consist of keypads, connectors, and safety covers. The material’s ability to preserve its properties over a vast array of temperatures makes sure the long life and integrity of digital devices.
Industrial Applications
In industrial setups, LSR is employed for generating seals, gaskets, and various other components that should perform dependably in difficult environments. The material’s resistance to oils, chemicals, and extreme temperatures makes it suitable for usage in equipment and tools. The injection molding procedure allows for the manufacturing of get rid of regular quality and limited resistances, which are critical for commercial applications.
Applications and Use Cases for High-Consistency Rubber
High-consistency rubber (HCR) is valued for its robust mechanical properties and versatility throughout different sectors. This product is particularly helpful in applications requiring toughness, flexibility, and resistance to severe temperatures.
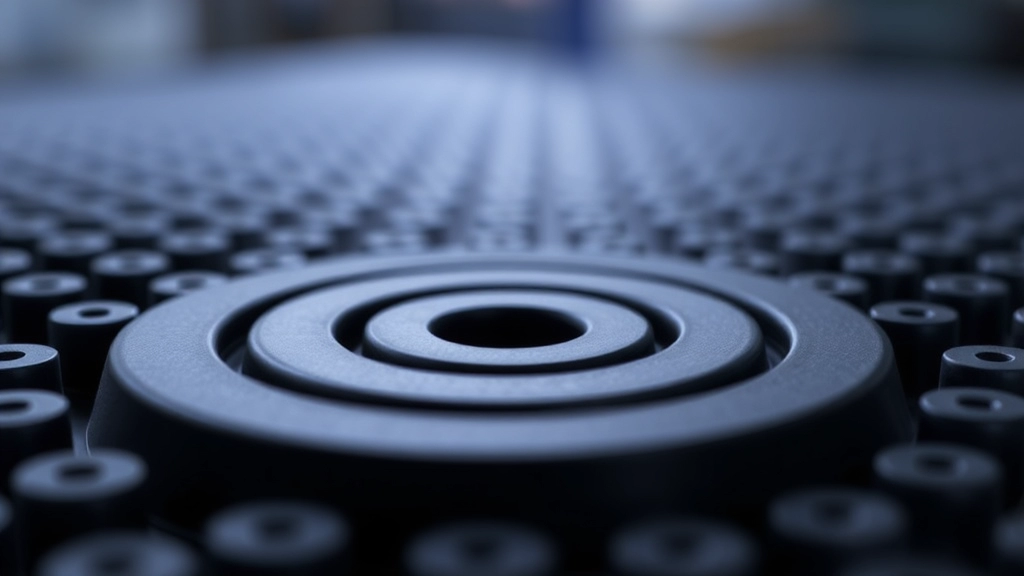
Automotive Industry
HCR is extensively used in the automotive market due to its exceptional thermal security and resistance to oils and chemicals. Typical applications include:
Component | Function |
---|---|
Gaskets | Seal engine parts to avoid leaks |
Tubes | Transportation liquids and stand up to heats |
O-rings | Give closed seals in different engine elements |
Medical and Healthcare Sector
In the medical and healthcare market, HCR is used for its biocompatibility and sanitation capabilities. It is commonly located in:
Product | Usage |
---|---|
Catheters | Versatile tubes for fluid drainage or drug administration |
Seals and Gaskets | Ensure closed and leak-proof seals in clinical devices |
Orthopedic Devices | Provide cushioning and support in prosthetics and braces |
Electrical and Electronics Industry
HCR is likewise widespread in the electrical and electronic devices industry because of its excellent insulating properties and resistance to electric arcing. Secret applications include:
Component | Function |
---|---|
Insulators | Prevent electrical leakage and make sure security |
Connectors | Give reputable connections in electrical circuits |
Keypads | Offer durability and responsiveness in electronic tools |
Customer Goods
In the world of durable goods, HCR is selected for its responsive properties and resilience. It is widely made use of in:
Product | Use |
---|---|
Pots and pans | Heat-resistant deals with and cooking molds |
Infant Products | Pacifiers, container nipples, and teething playthings |
Sports Equipment | Grips and safety equipment |
Advantages and Disadvantages of Liquid Silicone Rubber Injection Molding
Benefits of Liquid Silicone Rubber Injection Molding
Liquid Silicone Rubber (LSR) injection molding deals with numerous crucial benefits that make it a preferred option for numerous applications. Among the most substantial benefits is its precision and consistency. The shot molding process permits for the production of intricate geometries with tight tolerances, ensuring high-quality and repeatable outcomes.
An additional advantage is the rate and efficiency of the process. LSR shot molding can produce huge volumes of parts rapidly, which is suitable for sectors calling for mass manufacturing. The automation involved in this procedure lessens hand-operated intervention, decreasing labor expenses and the potential for human mistakes.
LSR products are known for their superb thermal security and resistance to extreme temperature levels, making them suitable for demanding settings. In addition, they supply remarkable chemical and electrical resistance, improving their applicability in markets like auto, medical care, and electronic devices.
The procedure is likewise eco-friendly, as it creates very little waste contrasted to other molding techniques. The product’s biocompatibility and hypoallergenic residential properties make it ideal for clinical applications, where safety and tidiness are critical.
Negative Aspects of Liquid Silicone Rubber Injection Molding
Regardless of its numerous benefits, LSR shot molding likewise has some downsides. The initial setup costs can be reasonably high due to the need for specific tools and tooling. This can be a barrier for small-scale productions or start-ups with limited budgets.
The material price of LSR can additionally be higher contrasted to various other types of rubber, which might impact the overall production cost. In addition, the procedure calls for precise control and knowledge to ensure optimal outcomes, which could require specialized training for operators.
Another consideration is the capacity for flash formation, a thin layer of excess material that can take place during molding. While this can be reduced with appropriate mold layout and procedure control, it may need additional post-processing to remove, including in the production time and expense.
Lastly, while LSR is functional, it may not be appropriate for all applications, specifically those requiring very high mechanical strength. In such cases, different materials or procedures could be more proper.
Benefits and Disadvantages of High-Consistency Rubber
Advantages of High-Consistency Rubber
High-consistency rubber (HCR) offers numerous notable benefits, making it a prominent option in various applications. Below are several of the vital advantages:
Advantage | Summary |
---|---|
Resilience | HCR is known for its excellent toughness and resistance to deterioration, making it suitable for long-lasting use. |
Temperature level Resistance | HCR can withstand a large range of temperature levels, from really reduced to very high, without shedding its buildings. |
Flexibility | This material keeps its versatility over a variety of temperatures, which is crucial for applications needing elastic buildings. |
Customizability | HCR can be quickly customized in terms of firmness, color, and various other buildings to fulfill certain application needs. |
Cost-Effectiveness | For several applications, HCR is an economical solution as a result of its relatively lower material and processing prices. |
Disadvantages of High-Consistency Rubber
While HCR has a number of advantages, it likewise includes some disadvantages that require to be thought about:
Disadvantage | Description |
---|---|
Handling Time | HCR typically calls for longer handling times compared to Liquid Silicone Rubber (LSR), which can impact production effectiveness. |
Consistency | Making certain constant top quality in HCR items can be challenging as a result of variants in the product’s properties. |
Tools Requirements | Handling HCR often requires customized tools, which can be a substantial investment for suppliers. |
Labor-Intensive | The production procedure for HCR can be much more labor-intensive, requiring knowledgeable operators to make sure quality. |
Limited Automation | The capacity for automation in HCR handling is typically lower contrasted to LSR, which can influence scalability. |
In recap, while High-Consistency Rubber uses many benefits such as resilience, temperature resistance, and customizability, it likewise presents challenges like longer processing times and the need for specialized tools. When choosing in between HCR and Liquid Silicone Rubber Injection Molding, it’s crucial to weigh these variables according to your specific application requirements and manufacturing capabilities.