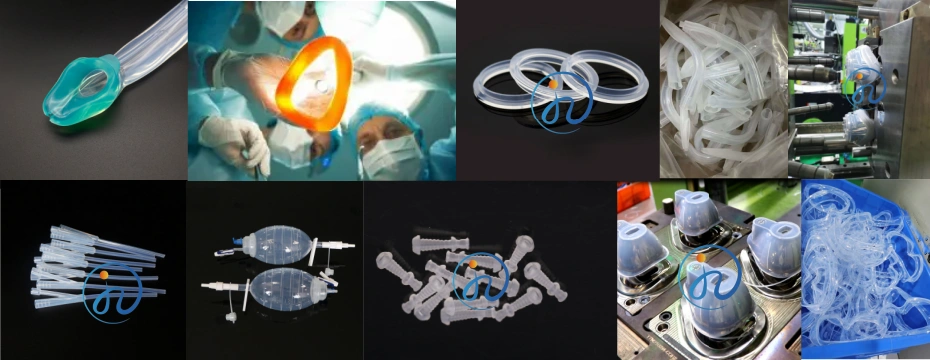
In my comprehensive experience, Liquid Silicone Rubber (LSR) injection molding has emerged as a transformative technology in the medical industry. This innovative manufacturing process involves injecting liquid silicone rubber into a mold cavity under high pressure, resulting in precise and premium components. The unique properties of LSR, combined with the precision of injection molding, offer numerous benefits that are especially valuable for medical applications.
Summary of LSR Injection Molding
In my comprehensive experience, Liquid Silicone Rubber (LSR) shot molding has actually arisen as a transformative modern technology in the clinical sector. This innovative production process entails infusing fluid silicone rubber into a mold cavity under high pressure, resulting in specific and premium components. The one-of-a-kind residential properties of LSR, integrated with the precision of injection molding, deal with numerous benefits that are especially valuable for medical applications.
What is LSR Injection Molding?
LSR injection molding is a customized procedure that uses liquid silicone rubber, a two-part platinum-cured elastomer understood for its outstanding adaptability, resilience, and biocompatibility. The process begins with the mixing of both components of LSR, which are then infused into a warmed mold cavity. The material remedies quickly, permitting rapid production cycles and high-volume production.
Secret Characteristics of LSR
LSR is preferred in the medical sector due to its biocompatibility, resistance to extreme temperatures, and capability to endure sanitation procedures. Some of the crucial residential or commercial properties of LSR include:
Property | Benefit |
---|---|
Biocompatibility | Safe for use in clinical gadgets and implants |
Temperature level Resistance | Runs properly in a wide variety of temperatures |
Longevity | Resilient and resistant to damage |
Flexibility | Maintains shape and feature under tension |
Chemical Resistance | Resistant to a variety of chemicals and sterilization approaches |
Applications in the Medical Industry
LSR injection molding is widely used to make a variety of clinical parts, including:
Component | Application |
---|---|
Catheters | Comfy, sturdy, and safe for long-term usage |
Seals and Gaskets | Making sure impermeable and fluid-tight seals in clinical devices |
Respiratory system Masks | Biocompatible and long-lasting for long-lasting implantation |
Implants | Biocompatible and long lasting for long-lasting implantation |
Clinical Tubing | Adaptable and immune to kinking or clog |
In final thought, the versatility and superior residential or commercial properties of LSR make it a suitable material for the clinical industry. The precision and effectiveness of injection molding further boost its suitability, making sure that clinical tools and components meet the highest possible standards of high quality and security.
Trick Benefits of LSR in Medical Applications
Boosted Biocompatibility and Safety
Liquid Silicone Rubber (LSR) is renowned for its biocompatibility, making it an ideal product for medical applications. Its inert nature guarantees that it does not react with physical tissues or liquids, minimizing the danger of damaging responses. Furthermore, LSR is hypoallergenic and resistant to germ development, which is crucial for preserving sterility in medical atmospheres.
Precision and Consistency in Medical Devices
Among the standout advantages of LSR injection molding is its ability to create components with high accuracy and consistency. The product’s reduced viscosity allows it to load detailed molds accurately, making sure that each part satisfies stringent tolerances required in the clinical area. This precision is essential for applications such as seals, gaskets, and various other parts where precise measurements are critical.
Cost-Effectiveness and Efficiency
LSR shot molding is an extremely efficient procedure that can significantly reduce production prices. The automation of the injection molding procedure lessens labor prices and decreases the capacity for human error. Furthermore, the high resilience of LSR molds implies they can be made use of for lengthy manufacturing runs without destruction, better-boosting cost-effectiveness.
Longevity and Longevity of LSR Components
Parts made from LSR are exceptionally durable and can hold up against extreme temperatures, UV exposure, and different chemicals. This toughness makes sure that medical tools and components have a long life span, which is particularly vital for implants and other crucial applications. The durability of LSR components additionally equates to fewer replacements and upkeep, adding to general cost savings.
Modification and Design Flexibility
LSR injection molding uses considerable design adaptability, allowing for the creation of complicated geometries and personalized services tailored to particular medical demands. The versatility of LSR suggests it can be used to create a large range of clinical devices, from simple tubes to detailed implantable parts. This flexibility is crucial for establishing ingenious modern clinical technologies and improving client end results.
Regulative Compliance and Quality Assurance
Medical-grade LSR fulfills rigid governing standards, ensuring that elements are risk-free and reliable for use in healthcare setups. The regular top quality of LSR components, integrated with strenuous screening and validation procedures, guarantee conformity with global clinical tool regulations. This reliability is essential for preserving a person’s safety and counting on medical items.
Boosted Biocompatibility and Safety
Intro to Biocompatibility
Liquid Silicone Rubber (LSR) shot molding stands apart because of its outstanding compatibility with human cells and bodily fluids. This particular makes LSR a preferred selection for numerous medical applications, consisting of implants, medical tools, and diagnostic equipment.
Non-Toxic and Hypoallergenic Properties
LSR is naturally safe and hypoallergenic, which significantly reduces the threat of unfavorable responses when touching human tissues. These residential or commercial properties are essential for devices that are implanted or entered into prolonged contact with the body. The absence of unsafe ingredients and the stability of LSR at various temperatures additionally improve its safety and security profile.
Resistance to Bacterial Growth
Another significant advantage of LSR is its resistance to bacterial development. This product does not give a conducive environment for microorganisms and other pathogens to grow, consequently decreasing the danger of infections. This attribute is especially important for medical tools that require high degrees of sterility.
Conformity with Medical Standards
LSR used in the clinical industry commonly follows rigorous governing requirements such as ISO 10993 and USP Class VI. These standards make sure that the material is safe for use in clinical applications. Conformity with these guidelines is a testament to the high level of biocompatibility and safety that LSR uses.
Information on Biocompatibility and Safety
Residential property | LSR | Various other Materials |
---|---|---|
Biocompatibility | High | Variable |
Non-Toxicity | Yes | Variable |
Hypoallergenic | Yes | No |
Resistance to Bacterial Growth | High | Low to Medium |
Regulative Compliance | ISO 10993, USP Class VI | Variable |
Precision and Consistency in Medical Devices
In the clinical sector, the precision and consistency of parts are crucial for ensuring the effectiveness and safety of clinical gadgets. Fluid Silicone Rubber (LSR) shot molding stands out in supplying these crucial characteristics, making it an excellent selection for medical applications.
High Precision Manufacturing
LSR shot molding is renowned for its high precision-producing abilities. The procedure enables the production of intricate geometries with tight resistances, which is necessary for clinical gadgets that require exact requirements. The capacity to mold complex layouts with marginal variation ensures that each element meets the rigid demands of the medical field.
Consistency in Production
Among the standout advantages of LSR injection molding is its ability to generate components with exceptional uniformity. This is achieved with automated processes and advanced machinery that preserve harmony throughout huge manufacturing runs. Uniformity is essential in the clinical market, where even the smallest inconsistency can lead to significant issues in tool performance and patient security.
Minimal Waste and Defects
The LSR injection molding process is developed to decrease waste and issues, even more, adding to the uniformity of the last items. The product’s residential properties, combined with the precision of the molding process, result in fewer rejected components and a higher yield of functional elements. This not only improves the performance of the production process yet additionally makes sure that each part meets the required high-quality requirements.
Enhanced Quality Control
The precision and uniformity of LSR shot molding are matched by extensive quality control procedures. Advanced examination strategies and real-time surveillance systems are employed to identify any abnormalities during manufacturing. This proactive strategy for quality control makes certain that every element sticks to the greatest standards, supplying confidence in the dependability and safety of medical gadgets.
In conclusion, the precision and consistency used by LSR injection molding are crucial in the clinical sector. These characteristics make sure that medical gadgets perform dependably and securely, inevitably contributing to much better personal end results.
Cost-Effectiveness and Efficiency
Material Efficiency
Among the key variables adding to the cost-effectiveness of Liquid Silicone Rubber (LSR) injection molding in the medical sector is the effective use of materials. LSR’s unique properties allow for minimal waste throughout the molding procedure. Unlike standard manufacturing techniques, where excess product is frequently disposed of, LSR injection molding makes sure that mostly all of the product is utilized, lowering total costs.
Lowered Labor Costs
LSR injection molding is extremely automated, which considerably minimizes the requirement for manual work. The automation of the procedure not only reduces human error but also speeds up production times. This effectiveness converts straight right into lower labor expenses, making it a more cost-effective option for producing medical parts.
High Production Speed
The quick cycle times of LSR injection molding add to its performance. The process can create complicated shapes and intricate designs immediately, which is crucial for meeting the high need in the medical market. Faster production times suggest that more devices can be created in a much shorter duration, further driving down prices.
Power Efficiency
LSR injection molding is also understood for its energy performance. The procedure requires lower temperature levels and less energy compared to various other molding strategies. This reduction in energy intake not only lowers functional prices but additionally makes the procedure a lot more environmentally pleasant, aligning with the enhancing demand for lasting manufacturing methods.
Maintenance and Longevity
The resilience of LSR mold and mildews makes certain that they have a longer lifespan contrasted to various other types of mold and mildews. This durability minimizes the regularity of mold substitutes and upkeep, which can be a substantial expense in the future. The effectiveness of LSR mold and mildews ensures regular top quality over prolonged production runs, including overall cost-effectiveness.
Price Comparison
Layout Flexibility Aspect | Details |
---|---|
Material Versatility | Various durometers, shades, and formulations |
Layout Adaptability | Thin walls, complex shapes, detailed attributes |
Prototyping and Iteration | Rapid changes and refinements |
Combination with Other Materials | Over-molding onto plastics and steels |
Regulatory Compliance and Quality Assurance
In the medical sector, regulative compliance and top quality assurance are vital. Fluid Silicone Rubber (LSR) shot molding stands out in conference stringent regulatory requirements, ensuring that medical gadgets are risk-free, reputable, and effective.
Governing Standards
LSR shot molding is compliant with different worldwide criteria, consisting of:
Standard | Summary |
---|---|
ISO 10993 | Biological evaluation of medical devices |
FDA 21 CFR 177.2600 | Rules for rubber short articles intended for repeated usage |
USP Class VI | Biocompatibility standards for clinical tools |
Quality Control Processes
To ensure the highest possible quality, LSR injection molding includes rigorous quality control procedures, such as:
- In-process monitoring to discover and fix problems in real-time
- Post-production testing to validate the honesty and performance of the end product
- Traceability of products and processes to make certain compliance with regulative demands
Documentation and Traceability
Comprehensive documentation and traceability are essential elements of governing conformity. LSR injection molding offers comprehensive records of:
Documentation | Description |
---|---|
Product Certificates | Evidence of compliance with material standards |
Refine Validation | Proof that the manufacturing process regularly generates an item conference its established requirements |
Batch Records | Thorough documents of each manufacturing set, consisting of materials utilized and procedure parameters |