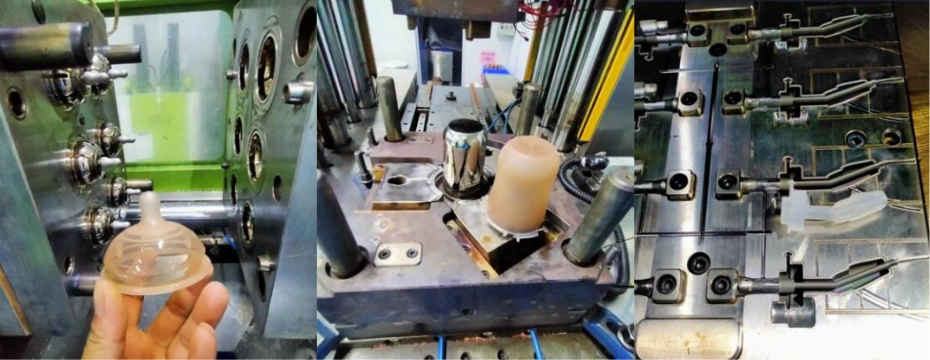
Liquid Silicone Rubber (LSR) has become increasingly popular in injection molding due to its unique set of characteristics and versatility in a wide range of applications. From medical devices and automotive components to consumer goods and electronics, LSR is often the go-to material for manufacturers who need reliable, durable, and flexible solutions. This blog will explore the reasons why Liquid Silicone Rubber should be your material of choice for injection molding, discussing its benefits, applications, and the technical reasons behind its growing popularity.
What is Liquid Silicone Rubber?
Liquid Silicone Rubber is a high-performance elastomer that is known for its excellent flexibility, durability, and resistance to extreme temperatures. Unlike traditional thermoplastic materials, LSR remains stable and retains its properties over a wide temperature range. It’s a two-part system composed of a silicone base and a catalyst, which, when mixed together, form a thermosetting material. Once cured, LSR forms a strong, flexible, and heat-resistant material that is perfect for a range of challenging applications.
Injection molding using LSR is different from conventional thermoplastic injection molding due to the nature of silicone rubber. However, the technology behind it has evolved rapidly, offering new capabilities that allow manufacturers to produce more intricate and complex components with greater efficiency.
Key Benefits of Using Liquid Silicone Rubber
- Temperature Resistance LSR is highly resistant to both high and low temperatures, withstanding extremes that range from -50°C to over 200°C. This temperature stability makes it an ideal choice for applications such as automotive components, electronics, and even kitchenware that are regularly exposed to temperature fluctuations. Unlike some plastics that degrade, crack, or lose flexibility in extreme conditions, LSR maintains its integrity and functionality.
- Durability and Longevity One of the most significant advantages of LSR is its durability. It resists aging, wear, and tear better than many other materials. This long life span makes LSR an economical choice for manufacturers since the parts do not need to be replaced as frequently. For applications that require reliability over time—like medical devices, electronics, and automotive seals—LSR offers a significant advantage.
- Flexibility and Elasticity LSR has excellent elasticity and flexibility, even in challenging environments. Unlike many other materials, which can become brittle or stiff at low temperatures, LSR remains pliable and elastic. This makes it ideal for products like gaskets, seals, and other components that require a tight, flexible fit. Moreover, LSR can be stretched significantly without tearing, which adds to its versatility in applications where flexibility is key.
- Biocompatibility A significant advantage of LSR, particularly for medical applications, is its biocompatibility. It’s non-toxic, hypoallergenic, and can be sterilized using various methods, such as autoclaving, gamma irradiation, and ethylene oxide. This makes LSR an excellent choice for medical devices that require direct contact with human skin or internal tissues, such as catheters, seals, and surgical tools.
- Design Flexibility and Complex Geometries LSR’s flowability makes it suitable for creating complex geometries and intricate designs. In injection molding, LSR can fill even the smallest cavities with precision. This means manufacturers can design and produce complex parts that would be difficult or impossible to achieve using other materials. Additionally, its low shrinkage rate during curing ensures a high level of dimensional stability, which is critical in precision parts.
- Fast Cycle Times LSR injection molding processes are known for their fast cycle times. Due to its rapid curing characteristics, manufacturers can produce parts quickly, increasing production efficiency. The reduced cycle times also lower energy costs and overall production expenses. Furthermore, LSR molds have a long lifespan, allowing manufacturers to achieve a higher return on investment over time.
Common Applications of LSR Injection Molding
Liquid Silicone Rubber is widely used in many industries due to its versatility. Some of the most common applications include:
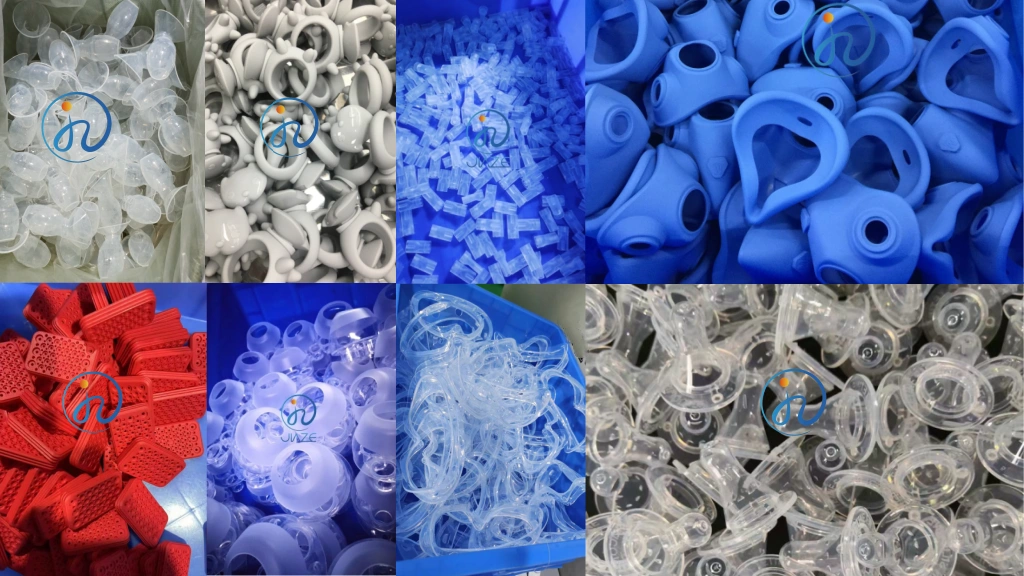
- Medical Devices: Because of its biocompatibility and ability to be sterilized, LSR is commonly used in medical applications such as seals, gaskets, valves, and implantable devices.
- Automotive Components: LSR’s heat and chemical resistance make it an ideal choice for under-the-hood applications, such as gaskets, seals, and O-rings, as well as for interior parts like keypads and switches.
- Electronics: In electronics, LSR is used for connectors, seals, and insulating components due to its excellent electrical insulation properties and its ability to withstand harsh environments.
- Consumer Goods: LSR is also popular in consumer products like kitchenware (bakeware, spatulas), baby products (pacifiers, bottle nipples), and wearable technology (wristbands, buttons) due to its flexibility, durability, and ability to be molded into complex shapes.
- Aerospace Industry: The material’s stability in extreme temperatures, combined with its lightweight and durable properties, make LSR a suitable material for various aerospace applications, including seals and gaskets.
The LSR Injection Molding Process
LSR injection molding involves several steps, including the mixing of the two-part LSR, injection into the mold, and curing. Since LSR is a thermosetting polymer, it must be kept cool until injected into a heated mold. The curing process happens quickly, and the final product is ejected from the mold once the material has set.
One of the key differences between LSR injection molding and traditional plastic injection molding is that LSR flows easily and fills the mold cavities completely, even with complex designs. The high precision and efficiency of LSR molding allow manufacturers to produce high-quality parts with tight tolerances.
Conclusion
Liquid Silicone Rubber’s resistance to extreme temperatures, flexibility, biocompatibility, and chemical resistance make it an ideal choice for a wide range of industries, from medical devices to automotive components. Additionally, LSR’s fast cycle times and ability to create complex geometries make it an attractive option for manufacturers looking to optimize their production processes.
As technology advances and the demand for high-quality, reliable materials continues to grow, LSR is likely to become even more integral to the future of injection molding. For manufacturers looking to improve product quality, production efficiency, and overall performance, switching to Liquid Silicone Rubber for injection molding is a smart move.