A silicone sample mold is a critical step in prototyping, product development, and small-scale manufacturing, serving as an essential bridge between design and final production. The purpose of a silicone sample mold goes beyond just making a prototype; it allows for testing, iteration, and refinement in a cost-effective and relatively fast manner. Here’s a deep dive into why silicone sample molds are so vital, focusing on their roles in various industries, their practical applications, and the specific benefits they provide.
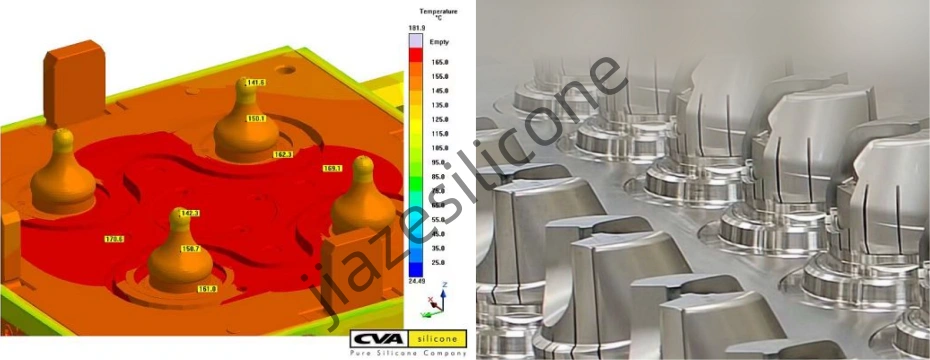
1. Low-cost silicone sample mold and Testing
One of the main reasons for creating a silicone sample mold is to enable low-cost prototyping. Silicone is a versatile and relatively inexpensive material that can be molded with high precision, making it perfect for creating initial prototypes of products. By creating a sample mold, manufacturers can produce prototypes that are close to the final product in terms of shape, texture, and detail. This allows designers and engineers to assess the feasibility of their designs and identify any necessary changes before moving to a more expensive, production-grade mold.
Traditional molds, made from metals like aluminum or steel, are far more expensive and time-consuming to produce. For initial prototyping, these materials are overkill, as designers often need to make numerous adjustments after evaluating the first few samples.
2. Rapid Design Iteration of silicone sample mold
The flexibility of silicone allows for rapid design iteration, which is crucial in fast-paced product development environments. When designing complex shapes or components, minor design adjustments are often needed.
If a company wants to test different design features or incorporate feedback from early testing, a silicone sample mold enables them to make those changes rapidly. This is invaluable for speeding up the product development cycle, which can lead to quicker time-to-market and a competitive advantage.
3. Precision and Detail Replication
Silicone has excellent elasticity and flexibility, allowing it to capture very fine details from the master model. This precision is particularly beneficial in industries like jewelry, medical devices, and consumer electronics, where intricate designs are essential. A silicone sample mold can replicate details as small as fine textures or intricate patterns, providing a near-exact replica of the original model.
Such detailed replication is essential for quality control and design verification. For example, in jewelry making, even the smallest design flaw can impact the product’s aesthetic appeal. By using a silicone sample mold, designers can closely examine the details before committing to a full production run.
4. Material Versatility for Silicone Sample Mold
Silicone molds can accommodate various materials, including resins, waxes, and some types of plastics. This versatility means that a single silicone mold can be used to create samples from different materials, allowing designers to test how the product performs in various materials.
For example, in the automotive industry, a designer may use a silicone mold to produce prototypes from resins to test aesthetics and fit, while testing different mechanical properties with other materials. The flexibility of silicone molds allows designers to test multiple aspects of a product with minimal additional expense or time.
5. Easy De-molding Process
Silicone’s non-stick properties make it incredibly easy to remove prototypes from the mold, even for complex shapes or designs with undercuts. Unlike other types of molds, which can require release agents or special techniques to avoid damage during de-molding, silicone allows for smooth and clean removal of the cast object. This reduces the risk of damaging the prototype, saving both time and material costs.
This ease of de-molding is particularly useful in industries like medical device manufacturing, where products may have intricate designs that require careful handling. Being able to remove prototypes easily without damaging them ensures that the samples are consistent and reliable for testing.
6. Improved Design and Functional Testing
A silicone sample mold allows manufacturers to perform realistic tests on their designs, helping them ensure that products meet the required functional and aesthetic standards. With a silicone mold, manufacturers can produce a sample that closely resembles the final product in terms of texture and design.
For functional testing, the mold enables manufacturers to test key aspects, such as durability, fit, and ergonomics, providing a reliable way to test how the product will perform under real-world conditions. For instance, in consumer electronics, engineers can evaluate how components fit together in a silicone prototype before creating the final mold, allowing them to identify and address any design flaws early on.
7. Cost-Effective Short-Run Production
Silicone molds are not just for prototyping but can also be used in short-run production. This is especially valuable for niche products, custom items, or limited editions where demand does not justify investing in expensive, long-lasting molds. Since silicone molds are inexpensive and fast to produce, they are ideal for small production runs, especially if slight adjustments to the design are required for each iteration.
For instance, in the fashion or accessory industry, designers can use silicone molds to create custom jewelry or small batches of exclusive items. Similarly, in the field of personalized consumer products, silicone molds make it feasible to offer customized or limited-edition items, allowing brands to cater to specific customer requests without a significant investment.
8. User Testing and Market Research
Silicone molds allow companies to produce high-quality, realistic samples for user testing and market research. By providing customers or focus groups with prototypes that closely resemble the final product, companies can gather more accurate feedback. This enables companies to make informed decisions about design and functionality based on user insights.
For instance, in consumer products like kitchenware or personal care items, user feedback on a silicone-molded prototype can reveal valuable insights into how the product is perceived in terms of comfort, usability, and design appeal. Such insights can guide final adjustments to the product, ultimately leading to a better product-market fit.
9. Environmental and Safety Considerations
Compared to one-time-use molds, silicone molds can produce a high number of prototypes or small production runs, reducing waste. Furthermore, silicone is a safe material that does not release harmful byproducts, which makes it suitable for industries requiring high safety standards, such as food production or medical device manufacturing.
This aspect is becoming increasingly important as companies aim to minimize their environmental impact and adopt more sustainable production methods.
10. Preparation for High-Volume Production
Creating a silicone sample mold allows manufacturers to prepare for high-volume production by optimizing the design, materials, and manufacturing processes. By validating the design and functional aspects in a sample mold, companies can identify potential issues before investing in expensive tooling for mass production.
For instance, in the automotive industry, testing parts using silicone molds allows engineers to assess assembly fit and tolerances, which helps in adjusting the design for mass production. This preparatory step reduces the likelihood of costly errors during full-scale manufacturing, ensuring that production lines can operate smoothly.
Conclusion of silicone sample mold
In summary, a silicone sample mold is a powerful tool in the product development process, providing an efficient, cost-effective, and versatile solution for prototyping, testing, and even short-run production. By enabling rapid design iteration, high detail replication, material versatility, and reliable functional testing, silicone sample molds help bring ideas to life in a realistic way, facilitating better decision-making before committing to full-scale production. Their role is pivotal across various industries, from automotive to consumer goods, allowing companies to create products that are refined, market-ready, and capable of meeting customer expectations.