Liquid Silicone Rubber (LSR) injection mould is a specialized process for producing parts that require high precision, flexibility, and durability. This method has grown in popularity due to its versatility and the unique properties of LSR. When considering the production of rubber parts, LSR injection molding stands out for several reasons. Such as its efficiency, cost-effectiveness, material benefits, and the ability to produce intricate designs. Here is an in-depth look at why LSR injection molding might be the best choice for your manufacturing needs.
1. Material Properties of LSR
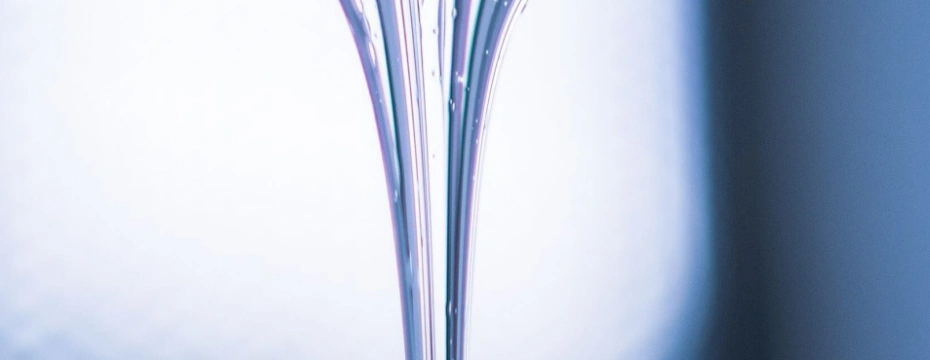
- Durability: LSR is known for its robustness. It can withstand extreme temperatures ranging from -50°C to 250°C, making it ideal for applications that demand high thermal stability.
- Chemical Resistance: LSR offers excellent resistance to a wide range of chemicals, including oils, acids, and alkalis. This makes it suitable for use in harsh environments, such as automotive, medical, and industrial applications.
- Flexibility and Elasticity: LSR retains its elasticity even at lower temperatures, making it perfect for products that require flexibility over a wide range of temperatures. Such as seals, gaskets, and diaphragms.
- Biocompatibility: LSR is biocompatible, hypoallergenic, and does not promote bacterial growth. It makes it an excellent choice for medical devices and applications involving skin contact.
2. Precision and Accuracy of LSR Injection Mould
- Tight Tolerances: LSR injection molding is ideal for manufacturing parts with tight tolerances and intricate designs. The injection process ensures that even complex geometries are reproduced with great precision.
- Consistency: Because the process is highly automated, LSR injection molding offers consistent quality from the first part to the last. This consistency is crucial in industries such as medical devices and consumer electronics, where part accuracy can be critical.
3. Efficient Production Process
- Speed and Cycle Time: LSR injection molding is a fast process with relatively short cycle times, enabling high-volume production runs. Unlike other molding processes, LSR cures quickly, allowing manufacturers to produce more parts in less time.
- Automation: The process is highly automated, reducing the need for manual labor. This automation minimizes errors and ensures uniformity across large production batches, lowering the overall production costs.
- Low Waste: LSR injection molding is efficient in material usage, generating minimal waste during the molding process. This is not only cost-effective but also environmentally friendly, contributing to sustainable manufacturing practices.
4. Design Flexibility
- Complex Geometries: LSR injection molding is capable of producing complex and intricate designs that might be difficult to achieve with other methods. This includes undercuts, thin walls, and intricate features, making it suitable for custom parts and unique design needs.
- Overmolding Capabilities: LSR can be overmolded onto other substrates such as metals, plastics, or other silicone components. This enables the production of multi-material parts in a single process, reducing assembly steps and improving the bond strength between components.
- Color Customization: LSR is available in a variety of colors, and pigments can be added to achieve specific hues. This is particularly useful in industries like consumer electronics, where aesthetics are important.
5. Cost-Effectiveness
- Lower Tooling Costs: While the initial investment in LSR molds can be high, the durability of the molds and the efficiency of the production process often offset these costs over time. Molds used in LSR injection molding can last for many cycles due to the material’s low viscosity.
- Reduced Secondary Operations: Since LSR parts often come out of the mold with smooth surfaces. This reduces the need for secondary operations, such as trimming or deburring, saving both time and labor costs.
- Scalability: LSR injection molding is ideal for both low and high-volume production. For low-volume runs, it offers cost efficiency through minimal waste and reduced manual labor. For high-volume runs, it benefits from rapid cycle times and automation. It allows manufacturers to scale up production without significant changes to the process.
6. Quality and Performance in End-Use Applications
- Heat and Cold Resistance: LSR’s ability to maintain its properties over a wide temperature range makes it suitable for products that are exposed to varying temperatures. This is particularly important for automotive parts, electronics, and outdoor equipment.
- Long-Term Stability: Parts made from LSR are known for their longevity and stability over time. LSR does not degrade quickly under UV light, ozone, or environmental factors, ensuring that products maintain their performance over their intended lifespan.
- Waterproof and Airtight Properties: LSR’s inherent waterproof and airtight properties make it suitable for seals and gaskets in medical devices, consumer electronics (such as smartphones and wearables), and automotive components where protection against moisture is essential.
7. Applications of LSR Injection Mould
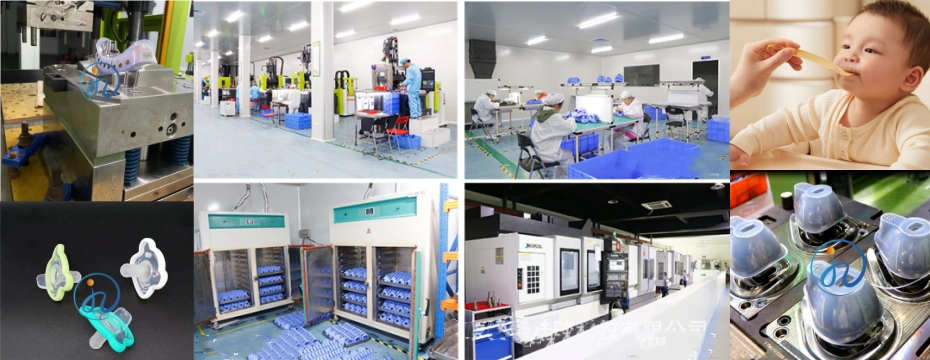
- Medical Devices: Due to its biocompatibility, flexibility, and sterility, LSR is extensively used in medical applications such as catheter components, seals, and medical tubing. It is also used for wearable devices that require prolonged skin contact.
- Automotive Industry: LSR is ideal for automotive applications due to its resistance to heat, oil, and environmental factors. Common parts include gaskets, seals, connectors, and keypads.
- Consumer Electronics: LSR is used for components like buttons, seals, and connectors in electronics due to its flexibility, durability, and ability to form watertight seals.
- Infant Care Products: LSR’s safety and hypoallergenic properties make it ideal for products like baby bottle nipples, pacifiers, and teething rings.
8. Environmental Considerations
- Sustainability: LSR is a non-toxic material and does not produce harmful by-products during manufacturing, making it a more environmentally friendly option compared to some other plastics and rubbers. Additionally, the process minimizes material waste, contributing to a greener manufacturing process.
- Recyclability: While silicone recycling can be more complex than thermoplastic recycling, there are options for recycling silicone materials. LSR parts that have reached the end of their useful life can often be downcycled into industrial applications, reducing the environmental footprint.
Conclusion of LSR Injection Mould
LSR injection molding offers a compelling combination of material advantages, production efficiency, and design flexibility, making it an ideal choice for a variety of industries. Its ability to produce high-precision parts with complex geometries, coupled with the durability and biocompatibility of LSR, makes it especially suitable for the medical, automotive, and electronics sectors. The process’s efficiency and automation further contribute to reduced production costs and faster turnaround times. As industries continue to demand more precise, durable, and cost-effective components, LSR injection molding stands out as a versatile and reliable manufacturing solution.
By opting for LSR injection molding, manufacturers can ensure that their products not only meet but exceed the quality and performance standards required in today’s competitive markets. This method supports high-volume production while maintaining consistency and precision, making it a preferred choice for producing parts that demand high standards of durability, accuracy, and innovation.