Liquid Silicone Rubber (LSR) injection molding and High Consistency Rubber (HCR) compression are two widely used methods for producing silicone parts. Both have their applications, but LSR injection molding offers several advantages over HCR compression in terms of efficiency, quality, and versatility. Below, we explore these benefits in detail.
1. Automation and Efficiency
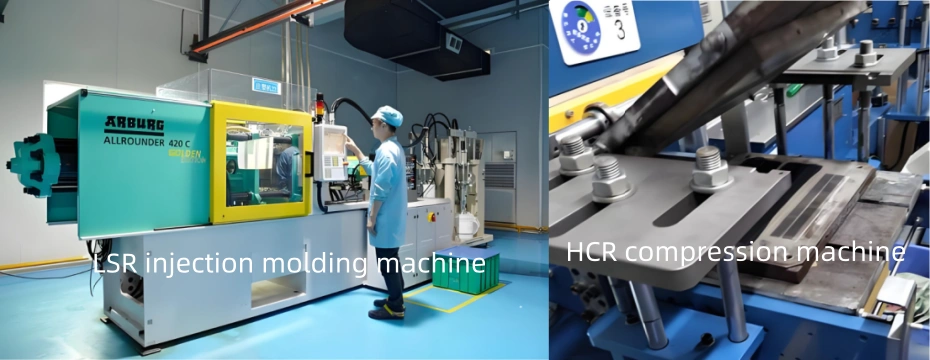
LSR Injection Molding:
LSR injection molding is a highly automated process. It uses sophisticated machinery that integrates functions like material mixing, injection, curing, and demolding. This automation minimizes manual intervention, reduces labor costs, and ensures consistent production cycles. Additionally, cycle times are typically shorter because the system optimizes every stage of the process.
HCR Compression:
HCR compression relies heavily on manual processes, such as material preparation, feeding, and part removal. Operators must often extrude or pre-form HCR before molding, which adds time and complexity to the process. This reliance on manual labor increases production times and the likelihood of variability in output.
Advantage: The automation in LSR injection molding significantly boosts productivity and consistency compared to HCR compression.
2. Material Preparation
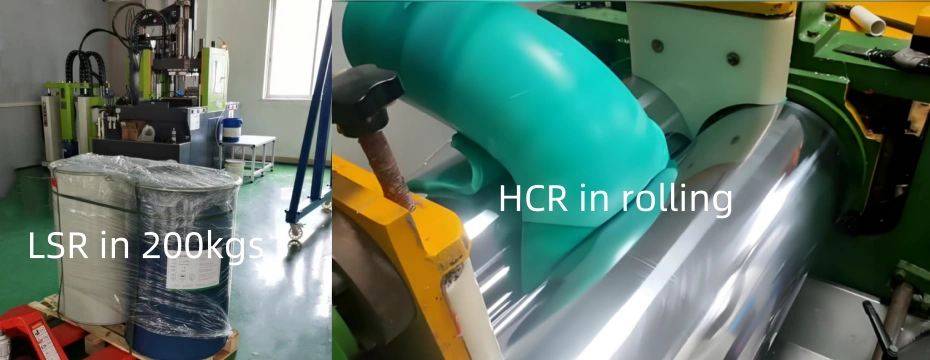
LSR Injection Molding:
LSR is supplied as a two-part liquid system that is pre-formulated to ensure consistent viscosity and curing characteristics. The materials are fed directly into the molding system without additional preparation. This simplifies operations and reduces the risk of contamination.
HCR Compression:
HCR requires extensive preparation, including rolling and blending on a two-roll mill to incorporate additives, pigments, or curing agents. This process is labor-intensive and prone to inconsistencies if not performed precisely.
Advantage: LSR’s ready-to-use formulation eliminates labor-intensive preparation steps required in HCR molding.
3. Part Complexity and Design Freedom
LSR Injection Molding:
LSR flows easily into complex mold geometries, enabling the production of intricate designs with undercuts, thin walls, and fine details. This makes it ideal for manufacturing high-precision parts used in industries such as healthcare, electronics, and automotive.
HCR Compression:
HCR has higher viscosity and lower flow characteristics, limiting its ability to fill intricate molds. As a result, designs must often be simplified or modified to accommodate the material’s limitations.
Advantage: LSR injection molding allows for greater design flexibility and the production of complex parts that are difficult to achieve with HCR.
4. Consistency and Repeatability
LSR Injection Molding:
The automated nature of LSR molding ensures consistent material metering, mixing, and curing. Parameters like temperature, pressure, and cycle time are tightly controlled, resulting in uniform parts with minimal variation.
HCR Compression:
HCR’s manual preparation and molding processes introduce variability in material properties and finished part dimensions. Consistency depends heavily on operator skill and process control.
Advantage: LSR injection molding delivers higher repeatability and quality assurance, which is essential for mass production.
5. Cycle Time
LSR Injection Molding:
LSR cures quickly at elevated temperatures, often completing cycles in seconds or minutes. Its rapid curing allows for high throughput, making it ideal for large-scale production.
HCR Compression:
HCR generally requires longer curing times, especially for thicker parts, due to its slower heat transfer and lower curing efficiency.
Advantage: LSR injection molding significantly reduces cycle times, leading to faster production rates.
6. Waste Reduction
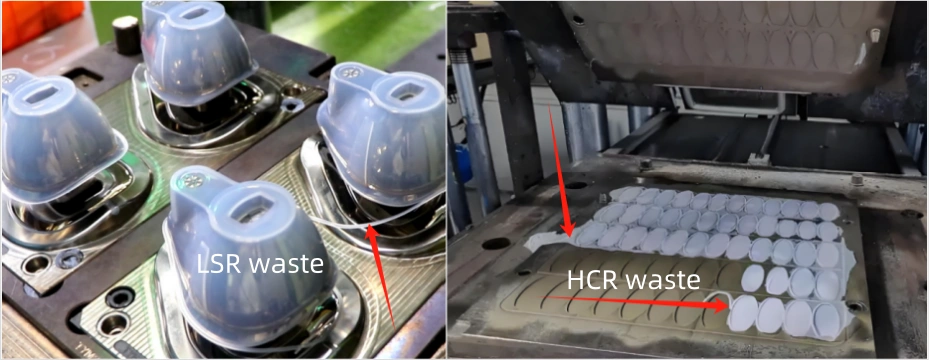
LSR Injection Molding:
LSR systems are designed to minimize material waste. The closed system ensures precise metering and excess material is rarely produced. Scrap rates are typically low, making the process cost-effective and environmentally friendly.
HCR Compression:
HCR molding often involves trimming excess material from parts, resulting in more waste. The open preparation process also increases the likelihood of contamination, which can lead to material being discarded.
Advantage: LSR injection molding generates less waste, contributing to cost savings and sustainability.
7. Hygiene and Cleanroom Compatibility
LSR Injection Molding:
LSR’s closed processing system and minimal human intervention make it well-suited for cleanroom environments, a requirement in medical and food-grade applications. The material’s biocompatibility and purity further enhance its suitability for these industries.
HCR Compression:
HCR’s manual preparation and open processing increase the risk of contamination, making it less ideal for cleanroom settings. Additional cleaning and precautions are often necessary.
Advantage: LSR injection molding is better suited for hygienic production environments, especially in regulated industries.
8. Scalability
LSR Injection Molding:
The high level of automation and repeatability makes LSR injection molding highly scalable. Manufacturers can easily adjust production volumes to meet demand without compromising quality or efficiency.
HCR Compression:
Scaling HCR production requires significant investment in skilled labor and equipment, and it becomes increasingly challenging to maintain consistency as output grows.
Advantage: LSR injection molding offers a more scalable solution for large-scale manufacturing.
9. Cost-Effectiveness
LSR Injection Molding:
Although initial investment in LSR injection molding equipment is higher, the long-term cost benefits outweigh the upfront expense. Automation reduces labor costs, shortens cycle times, and minimizes waste, contributing to lower per-part costs.
HCR Compression:
HCR molding has lower initial equipment costs but higher ongoing expenses due to labor-intensive processes, slower production rates, and higher waste levels.
Advantage: LSR injection molding provides greater cost efficiency over the long term.
10. Performance Characteristics
LSR Injection Molding:
LSR parts exhibit excellent mechanical and thermal properties, including high tear strength, elasticity, and temperature resistance. The material also offers superior biocompatibility and chemical resistance, making it versatile for demanding applications.
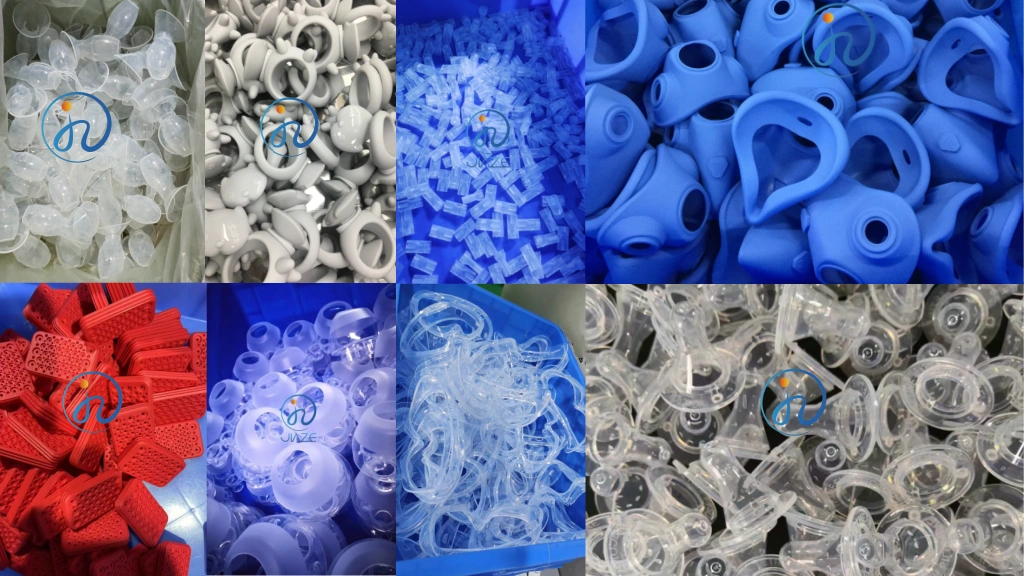
HCR Compression:
While HCR parts also offer good performance, their properties can vary due to inconsistencies in material preparation and processing. This variability can limit their use in critical applications.
Advantage: LSR molding ensures superior and consistent performance characteristics.
Conclusion
LSR injection molding has clear advantages over HCR compression in terms of automation, efficiency, consistency, and scalability. Its ability to produce complex, high-quality parts with minimal waste and faster cycle times makes it the preferred choice for industries that demand precision and reliability, such as medical devices, automotive components, and consumer electronics. While HCR molding remains useful for smaller-scale or less demanding applications, LSR injection molding is optimal for high-volume, high-performance manufacturing.