Silicone injection molding is a widely used manufacturing process for producing intricate silicone rubber components with high precision and consistency. The process involves injecting liquid silicone rubber (LSR) into a heated mold cavity under controlled pressure, temperature, and time. The pressure required for silicone injection molding is a critical factor in ensuring the proper filling of the mold, achieving the desired part quality, and optimizing production efficiency. In this article, we will explore the factors influencing pressure requirements, the importance of pressure in the process, and best practices for achieving optimal results in silicone injection molding.
1. Understanding Silicone Injection Moulding
Before delving into the specifics of pressure requirements, it’s essential to understand how the silicone injection molding process works. In this process, liquid silicone rubber (LSR), a two-part material consisting of base and curing agents, is mixed and injected into a mold cavity under pressure. The silicone material cures (vulcanizes) inside the mold, taking the shape of the mold cavity.
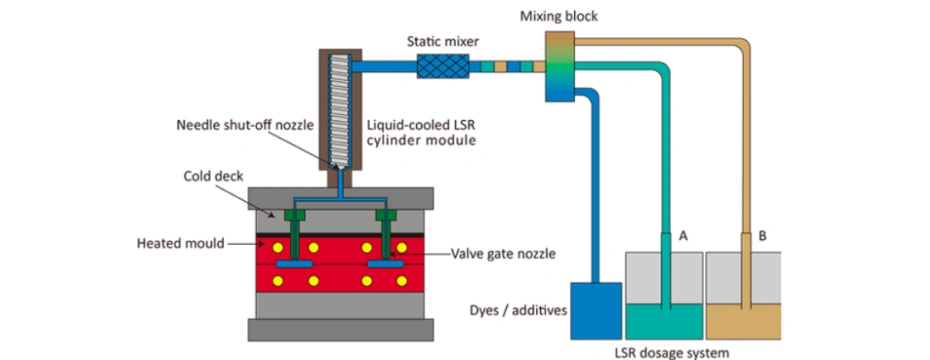
The injection machine typically consists of three key components:
- Injection unit: Responsible for injecting the LSR material into the mold.
- Mold: The cavity into which the LSR is injected, where the part takes shape.
- Clamping unit: Holds the mold together during injection and curing.
The role of pressure in this process is to ensure that the LSR fills the mold cavity completely, eliminates air pockets, and ensures the final part has a uniform and consistent structure.
2. Factors Influencing the Required Pressure
Several factors impact the amount of pressure needed for silicone injection molding. These factors can vary based on the complexity of the part, the type of silicone used, and the specifics of the mold and injection machine. Key factors influencing pressure include:
a. Viscosity of the Silicone Material
The viscosity of the liquid silicone rubber is one of the most critical factors affecting the required injection pressure. LSR materials typically have low viscosity compared to other rubber types, allowing them to flow easily into mold cavities. However, some variations in silicone formulations can affect viscosity, requiring adjustments in injection pressure.
- Low-viscosity silicone generally requires lower injection pressure because it flows easily through the mold.
- High-viscosity silicone requires higher injection pressure to ensure the material flows properly and fills the mold cavity before curing begins.
b. Mold Complexity
The complexity of the mold also plays a significant role in determining the pressure required. Molds with intricate geometries, thin walls, deep cavities, or small features may require higher pressures to ensure uniform material distribution. The pressure needs to overcome any resistance posed by the mold’s design, such as narrow channels or sharp corners.
For example, a mold with thin-walled sections may require more pressure to avoid incomplete filling and air entrapment. On the other hand, simple molds with fewer features might need lower injection pressures.
c. Mold Temperature
The mold’s temperature is another important parameter that can influence injection pressure. Typically, silicone injection molding is done at temperatures ranging from 150°C to 200°C (300°F to 392°F). The higher the mold temperature, the more fluid the silicone becomes, and the less pressure is needed to inject it. If the mold is too cold, the material may become more viscous, requiring higher pressures to achieve proper flow.
d. Injection Speed
The speed at which the LSR is injected into the mold cavity also affects the pressure requirements. Faster injection speeds can increase pressure, especially when the material has a higher viscosity. Additionally, faster injection speeds can sometimes lead to defects such as air entrapment or incomplete filling of the mold, so it is important to balance injection speed with pressure.
e. Mold Cavity Size and Volume
The size and volume of the mold cavity also play a role in determining the required pressure. Larger molds with more material to inject may require higher pressure to ensure that the silicone fills the entire cavity before curing. Smaller molds with less material may require less pressure. The injection pressure also needs to be sufficient to prevent the silicone from backing up or solidifying prematurely.
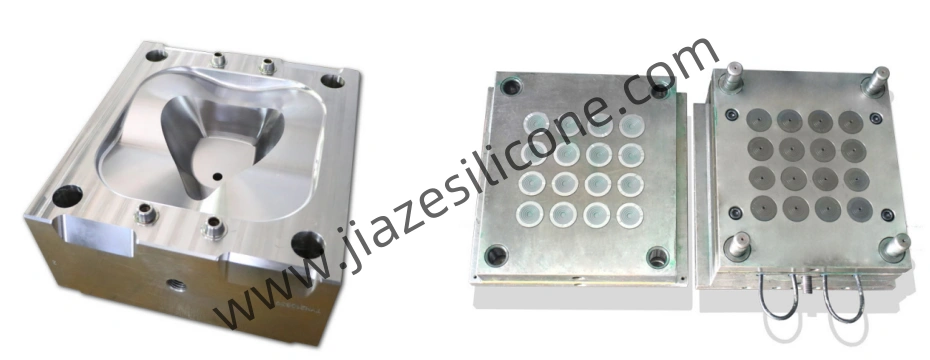
3. Typical Pressure Ranges for Silicone Injection Moulding
The pressure used in silicone injection molding typically falls within a range of 500 to 1500 bar (about 7,500 to 22,500 psi), though this can vary depending on the factors discussed above.
- Low-pressure molding (500 to 1000 bar) is generally used for simpler parts with low-viscosity silicone materials.
- High-pressure molding (1000 to 1500 bar or more) is typically required for parts with complex geometries or for silicones with higher viscosities.
4. Role of Pressure in Part Quality
Pressure plays a significant role in the quality of the final part. Inadequate pressure can result in several issues:
- Incomplete filling: If the pressure is too low, the silicone may not fully fill the mold cavity, leaving voids or incomplete features.
- Air entrapment: Low pressure can cause air pockets or bubbles to form within the silicone, leading to defects in the part.
- Inconsistent curing: If the pressure is insufficient, it may affect the curing process, leading to parts with weak spots or inconsistent hardness.
On the other hand, excessive pressure can lead to other issues, such as:
- Flash formation: Excessive pressure can force silicone to leak out of the mold, creating unwanted excess material around the part (flash).
- Mold wear: Over-pressurizing the system can lead to excessive wear on the mold or even cause damage over time.
- Dimensional distortion: High pressures can distort the shape of the part, especially if it has intricate features or delicate details.
5. Optimizing Injection Pressure
Optimizing injection pressure is essential for ensuring the best balance between part quality, cycle time, and machine efficiency. Here are some best practices for optimizing pressure in silicone injection molding:
a. Proper Mold Design
Designing the mold to accommodate the flow of silicone is critical. Features such as appropriate gate design, venting, and runner systems should be incorporated to ensure the material flows evenly and with minimal resistance. This reduces the need for excessive pressure.
b. Material Selection
Choosing the right silicone formulation can significantly impact the required injection pressure. Opt for materials that have suitable viscosity and flow characteristics for your part’s design. Some formulations are designed to flow more easily, reducing the need for high pressures.
c. Injection Parameters Optimization
Once the mold is designed and materials are selected, optimizing injection parameters such as speed, pressure, and temperature is crucial. Performing trial runs and making adjustments to injection speed and pressure based on results can help you find the optimal settings for your specific application.
d. Regular Machine Maintenance
Proper maintenance of the injection molding machine and components, such as the nozzle, mold, and injection unit, ensures consistent pressure delivery and minimizes the risk of defects due to machine malfunctions.
6. Conclusion
In silicone injection molding, the pressure required to inject the material into the mold is crucial for producing high-quality parts. The right pressure ensures proper filling, eliminates defects like air pockets, and helps achieve uniform curing. Factors such as material viscosity, mold complexity, temperature, and cavity size all influence the optimal injection pressure. By carefully considering these factors and optimizing the process parameters, manufacturers can achieve high-quality silicone parts efficiently and cost-effectively.
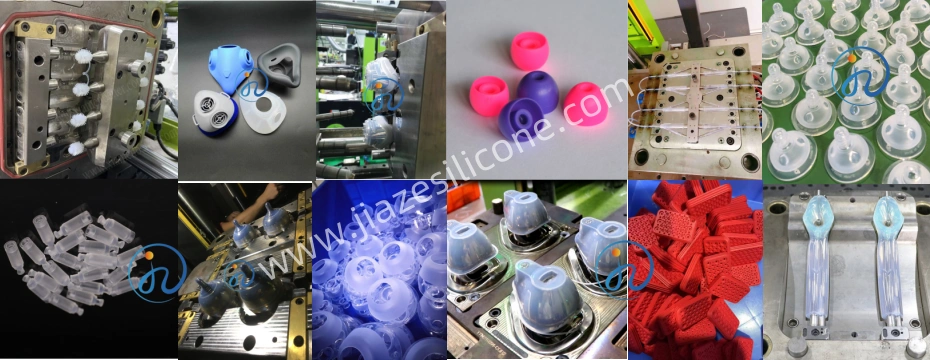
Through careful control of injection pressure and other parameters, manufacturers can maximize production efficiency, reduce waste, and produce consistent, high-quality silicone parts that meet the demands of various industries.