The Benefits of LSR Injection Molding in the Aerospace Industry
Liquid Silicone Rubber (LSR) injection molding has become an essential manufacturing process for various industries, including aerospace. The aerospace sector demands components that are lightweight, durable, reliable, and capable of withstanding extreme environmental conditions. LSR injection molding offers numerous advantages, aligning perfectly with these requirements. This article delves into the benefits of LSR injection molding in the aerospace industry, exploring its properties, applications, and why it is a preferred choice for many manufacturers.
What is LSR Injection Molding?
LSR injection molding involves the use of a two-part liquid silicone rubber compound that is injected into a mold cavity under high pressure. The material is cured using heat, transforming it into a solid elastomer with excellent physical properties. This process enables the production of complex, high-precision parts with consistent quality.
Key Benefits of LSR injection molding in Aerospace
- Superior Material Properties
- Temperature Resistance: LSR can endure extreme temperatures, ranging from -50°C to over 200°C, making it ideal for aerospace components exposed to high altitudes and varying atmospheric conditions.
- Durability: LSR is highly resistant to wear and tear, ensuring longevity even in harsh environments.
- Chemical Resistance: Its resistance to fuels, oils, and other chemicals commonly found in aerospace applications ensures parts remain unaffected by chemical exposure.
- Flexibility: LSR maintains elasticity and flexibility even under extreme stress, allowing it to absorb vibrations and maintain structural integrity.
- Lightweight Design
- Aerospace components must be lightweight to reduce overall aircraft weight and improve fuel efficiency. LSR parts are significantly lighter than metal alternatives, contributing to energy savings without compromising performance.
- Precision and Complexity
- LSR injection molding allows the creation of intricate designs and complex geometries with tight tolerances. This precision is critical for aerospace components where even minor deviations can have significant consequences.
- The process also supports over-molding, enabling the integration of multiple materials or the addition of LSR to metal or plastic components.
- Consistency and Repeatability
- The automated nature of LSR injection molding ensures consistent part quality across large production runs. This repeatability is essential in aerospace manufacturing, where uniformity and reliability are non-negotiable.
- Heat and Fire Resistance
- LSR materials meet stringent flame retardancy standards, including UL 94 V-0. This fire resistance makes them suitable for components used in the engine compartment or cabin interiors where safety is paramount.
- Vibration Dampening
- Aerospace systems often encounter high levels of vibration during flight. LSR’s excellent shock absorption properties help protect sensitive electronic components and mechanical systems, extending their lifespan and ensuring functionality.
- Environmental and Aging Resistance
- LSR is resistant to UV radiation, ozone, and oxidation, ensuring that parts remain functional even after prolonged exposure to outdoor elements. This durability is crucial for aerospace components that must endure extended service life cycles.
- Cost Efficiency
- Although the initial investment in molds can be high, the overall manufacturing costs decrease with LSR injection molding due to:
- Faster production cycles.
- Reduced material waste.
- Minimal need for secondary operations such as trimming or finishing.
- Although the initial investment in molds can be high, the overall manufacturing costs decrease with LSR injection molding due to:
- Customization
- LSR formulations can be tailored to meet specific aerospace requirements, such as enhanced thermal conductivity, electrical insulation, or flame retardancy. This flexibility ensures that components meet exact performance specifications.
Applications of LSR Injection Molding in Aerospace
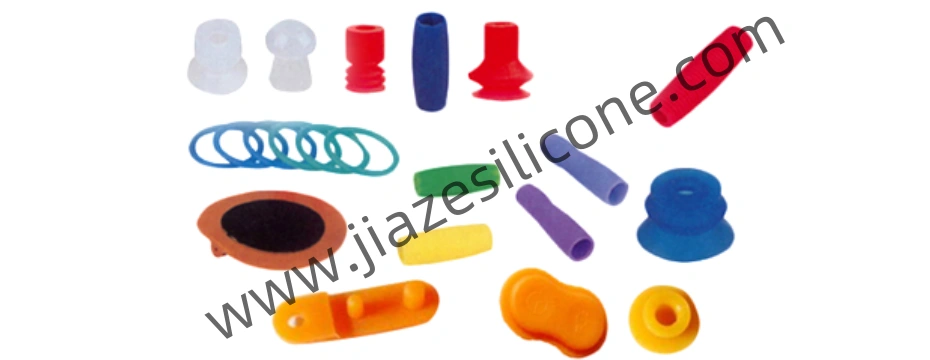
- Seals and Gaskets
- LSR’s elasticity, durability, and resistance to extreme conditions make it an excellent material for seals and gaskets used in aircraft engines, fuel systems, and cabin pressurization systems.
- Insulators and Connectors
- LSR’s electrical insulation properties are ideal for manufacturing connectors, wire harnesses, and cable assemblies. These components ensure reliable electrical performance even in demanding aerospace environments.
- Vibration and Noise Dampening Components
- LSR is used for bushings, mounts, and other parts designed to absorb vibrations and reduce noise, enhancing the comfort and safety of passengers and crew.
- Aerodynamic Components
- The lightweight nature of LSR makes it suitable for aerodynamic components that must withstand wind resistance and other environmental stresses.
- Cabin Interior Parts
- LSR is commonly used for flexible, durable parts within aircraft interiors, such as armrest pads, tray table seals, and window seals, meeting both functional and aesthetic requirements.
- Protective Covers and Caps
Why LSR Injection Molding is Superior for Aerospace Manufacturing
- Compliance with Industry Standards
- Aerospace components must meet rigorous industry standards for safety and performance, such as AS9100 or ISO 9001 certifications. LSR’s properties and the precision of injection molding processes make compliance more achievable.
- Scalability
- LSR injection molding is well-suited for both low-volume prototyping and high-volume production, catering to the needs of aerospace manufacturers at different stages of development.
- Sustainability
- The process generates minimal material waste, aligning with the aerospace industry’s increasing focus on sustainability. Furthermore, many LSR materials are recyclable, contributing to eco-friendly manufacturing practices.
- Innovation Potential
- The versatility of LSR injection molding fosters innovation, allowing designers to explore new component designs and functionalities that were previously unattainable with traditional materials.
Challenges and Considerations
While LSR injection molding offers numerous advantages, certain challenges must be addressed in aerospace applications:
- High Initial Investment: The upfront costs for tooling and mold design can be significant.
- Material Selection: Choosing the right LSR formulation is crucial to ensure compatibility with aerospace requirements, such as temperature resistance and flame retardancy.
- Precision Engineering: The process requires expertise in mold design and production to achieve the desired results.
Conclusion
LSR injection molding has revolutionized the aerospace industry by providing a reliable, cost-effective solution for manufacturing high-performance components. Its unique material properties, combined with the precision and efficiency of the injection molding process, make it a preferred choice for aerospace applications ranging from seals and gaskets to vibration-dampening systems and electrical insulators.
As the aerospace sector continues to push the boundaries of technology, the role of advanced manufacturing processes like LSR injection molding will become even more critical. Its ability to deliver lightweight, durable, and customizable components ensures that it remains a cornerstone of innovation in aerospace engineering. By embracing LSR injection molding, manufacturers can meet the industry’s stringent demands while driving efficiency and sustainability, paving the way for a more advanced and reliable future in aviation.