In modern medical procedures, precision, sterility, and reliability are non-negotiable. Devices and materials used during interventions must meet the highest standards of performance and safety, especially when managing blood flow during catheter-based or minimally invasive procedures. A key component in such systems is the silicone hemostasis valve—a critical device that prevents blood loss while allowing the passage of guidewires, catheters, and other instruments.
Over the years, innovations in material science have led to the emergence of Liquid Silicone Rubber (LSR) as a preferred material for manufacturing hemostasis valves. LSR offers a host of advantages over traditional materials like thermoplastics or general-purpose rubbers. In this article, we’ll explore why LSR silicone hemostasis valves are becoming the gold standard in interventional medical procedures, detailing their properties, benefits, and impact on the medical industry.
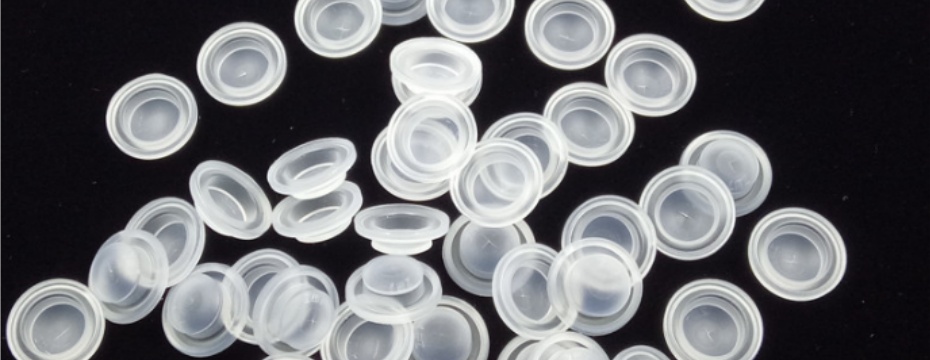
What Is silicone Hemostasis Valves?
A hemostasis valve is a device used in interventional cardiology, radiology, and vascular procedures to maintain a sealed, blood-tight system during catheter-based access to blood vessels. The valve allows the introduction and manipulation of devices like guidewires, catheters, or balloons, while minimizing blood loss and preventing air embolism.
These valves are integral to procedures such as:
- Coronary angioplasty
- Stent placement
- Transradial and transfemoral interventions
- Endovascular aneurysm repair (EVAR)
- Electrophysiology (EP) studies
Given their critical function, the materials used in hemostasis valves must exhibit a balance of biocompatibility, flexibility, resilience, and durability—a combination that LSR silicone excels at delivering.
What Is Liquid Silicone Rubber (LSR)?
Liquid Silicone Rubber (LSR) is a two-part platinum-cured silicone compound that is heat-cured in closed molds through injection molding. It is distinct from traditional high-consistency rubber (HCR) due to its lower viscosity, enabling it to flow easily into intricate molds.
- Biocompatibility (meets ISO 10993 and USP Class VI standards)
- Excellent mechanical performance
- Chemical inertness
- High thermal stability
- Resistance to aging and UV
These properties make LSR especially suitable for medical device components like valves, seals, gaskets, and soft-touch surfaces.
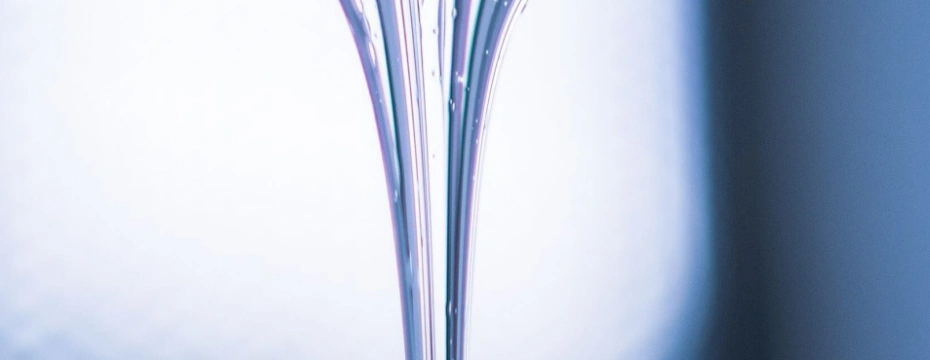
1. Superior Biocompatibility and Safety
In medical applications, patient safety is paramount. LSR is one of the most biocompatible materials available for internal use.
- Non-toxic and non-allergenic: LSR does not leach harmful substances, making it ideal for intravascular contact.
- ISO 10993 and USP Class VI compliant: Medical-grade LSR meets global safety standards for biological compatibility.
- Non-reactive with bodily fluids: It resists interaction with blood, saline, and contrast media, ensuring a neutral interface.
These qualities make LSR valves especially reliable during prolonged procedures or in critical care situations.
2. Exceptional Seal Integrity
The primary role of a hemostasis valve is to create a blood-tight seal around interventional tools without impeding their movement. LSR offers excellent elastic recovery and soft compression characteristics, which allow it to maintain a strong seal without requiring excessive force.
- Elastic memory: After stretching around a catheter or guidewire, LSR quickly returns to its original shape, maintaining seal integrity.
- Conformability: LSR adapts closely to the shape of tools, ensuring minimal gaps for blood leakage.
This ensures reliable performance, reduced procedural complications, and lower operator fatigue.
3. Durability and Resistance to Fatigue
LSR’s molecular structure offers excellent tear strength, compression set resistance, and fatigue resistance, which are crucial for devices subjected to mechanical stress.
- Repeated use performance: LSR valves can undergo numerous cycles of insertion and removal without tearing or losing shape.
- Long-term reliability: Whether used in disposable or reusable devices, LSR maintains functional performance throughout the product’s life.
- Minimal degradation: LSR withstands exposure to temperature changes, pressure, and bodily fluids without material breakdown.
This durability ensures patient safety and reduces the risk of valve failure during critical interventions.
4. Ease of Sterilization
Sterilization is a vital requirement for all surgical and interventional devices. LSR is compatible with various sterilization methods:
- Autoclaving (steam sterilization)
- Ethylene oxide (EtO)
- Gamma radiation
- Electron beam sterilization
LSR retains its physical properties and mechanical integrity even after repeated sterilization cycles, making it suitable for both single-use and reusable valve designs.
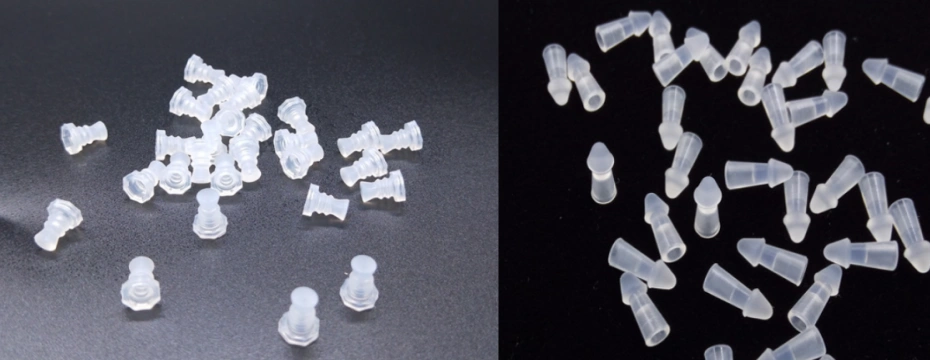
5. Excellent Temperature Resistance
Interventional procedures may expose medical components to a wide range of temperatures—from room temperature handling to sterilization cycles and exposure to internal body heat.
- Thermal range: LSR withstands temperatures from -60°C to 250°C without deformation or chemical change.
- Thermal cycling resistance: Withstands rapid changes in temperature, essential during storage, sterilization, and use.
- No plastic softening or hardening: Unlike thermoplastics, LSR maintains consistent flexibility and softness across temperatures.
This thermal resilience supports device reliability in varied clinical environments.
6. High Transparency for Visual Inspection
In some hemostasis valve designs, transparency is a desirable property, allowing clinicians to visually confirm device alignment, fluid movement, or presence of air bubbles.
- Optical clarity: Medical-grade LSR can be manufactured with high transparency.
- Color customization: LSR can also be tinted or colored for user instructions, visual cues, or branding.
These features aid in quality control, clinician confidence, and procedural safety.
7. Design Flexibility and Precision Molding
LSR is ideally suited for complex, high-precision molding processes, enabling the design of intricate valve geometries that perform reliably under stress.
- Injection molding compatibility: LSR’s flowability allows fine details and tight tolerances to be replicated accurately.
- Multi-component molding: LSR can be co-molded with thermoplastics or metals to form integrated, multi-function parts.
- Miniaturization: Ideal for minimally invasive procedures where small valve sizes are necessary.
This design flexibility supports innovation in catheter systems and next-generation interventional tools.
8. Low Particulate Generation
In vascular access devices, particulate shedding from seals and valves can be a serious concern, potentially leading to embolism or thrombosis. LSR valves offer excellent cleanliness:
- Minimal shedding: LSR does not flake or create particulates during instrument manipulation.
- Cleanroom manufacturable: Can be processed in ISO Class 7 or better environments to maintain sterility and cleanliness.
This enhances patient safety and supports compliance with increasingly strict regulatory standards.
9. Chemical Resistance
LSR is resistant to a wide array of chemicals, which is vital for compatibility with procedural agents like:
- Antiseptics
- Saline solutions
- Contrast media
- Cleaning agents
Unlike some plastics, LSR doesn’t swell, degrade, or lose elasticity when exposed to these fluids, ensuring consistent valve performance throughout procedures.
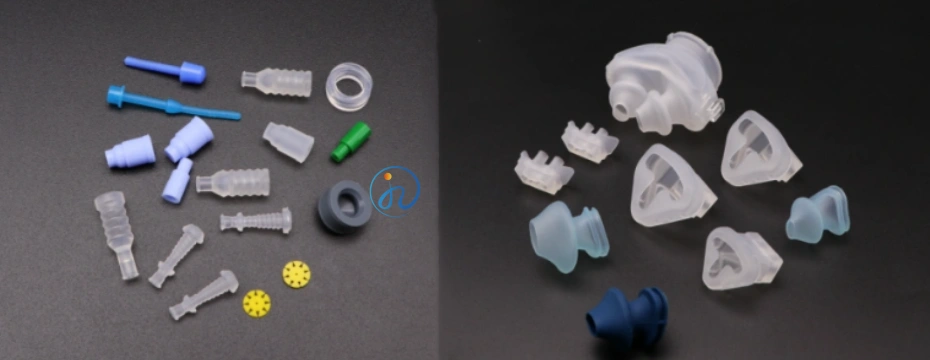
10. Sustainability and Waste Reduction
While most medical devices are still single-use for sterility reasons, LSR supports longer device lifespans in reusable applications and promotes environmental responsibility in several ways:
- Reduced material waste: Injection molding with LSR produces minimal scrap material.
- Longer part life: Durable valves reduce the frequency of part replacement.
In an industry beginning to reckon with its environmental footprint, LSR provides a forward-looking solution.
11. Customization and Branding Potential
In a competitive medical device market, product differentiation is key. LSR provides opportunities for customization:
- Texture and feel: Surface textures can be designed to improve tactile feedback for clinicians.
- Color and labeling: Visual branding, usage cues, and instruction indicators can be integrated directly into the part.
- Functionality integration: LSR can be designed with varying durometers (hardness levels) in different regions of the same valve.
This enhances both form and function, aligning with the needs of device manufacturers and end users.
12. Regulatory Advantages
Medical-grade LSR suppliers often provide comprehensive documentation, including:
- Biocompatibility testing data
- FDA Master Files
- REACH and RoHS compliance
- ISO certifications
This simplifies the regulatory approval process for device manufacturers and accelerates time-to-market for new products.
Conclusion
LSR silicone hemostasis valves represent a significant advancement in medical device engineering. Their superior performance in terms of biocompatibility, durability, sealing ability, sterilizability, and design flexibility makes them the ideal choice for high-stakes clinical environments.
As minimally invasive procedures become more common and sophisticated, the demand for components that combine safety, functionality, and adaptability will only increase. LSR meets and exceeds these demands, supporting innovation in catheterization, cardiology, radiology, and beyond.
For manufacturers, LSR offers the ability to design next-generation valves that stand out in both performance and reliability. For clinicians and patients, it delivers peace of mind through consistent, dependable function. And for healthcare systems and regulators, it presents a material that aligns with modern safety and sustainability standards.