Silicone baby pacifier have become an essential product in infant care due to their safety, durability, and comfort. As a manufacturer specializing in custom-designed silicone baby pacifiers, the process involves extensive research, material selection, design innovation, and precision production techniques. This article explores the intricacies of silicone pacifier manufacturing, from design considerations to production and quality assurance.
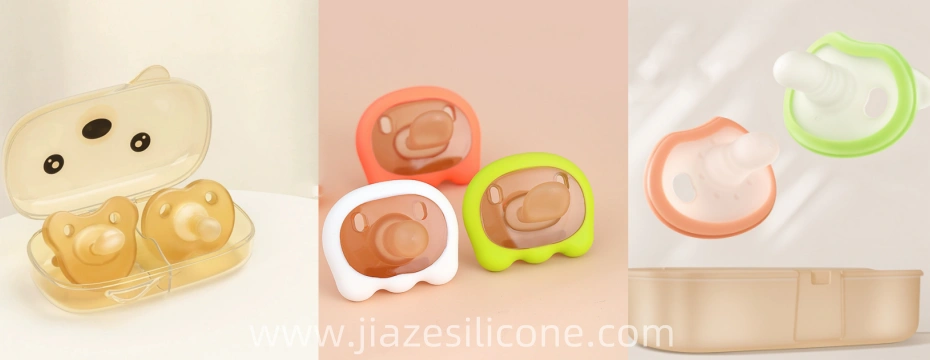
The Importance of Silicone in Baby Pacifiers
Liquid Silicone Rubber is widely preferred in baby pacifiers for several reasons:
- Non-Toxic and BPA-Free: Ensuring safety for infants.
- Durability: Resistant to heat, chemicals, and wear.
- Soft and Flexible: Mimics the natural feel of a mother’s nipple, providing comfort.
- Easy to Clean: Can withstand high-temperature sterilization.
Custom Design Considerations
1. Material Selection
The choice of high-quality, food-grade liquid silicone rubber ensures compliance with international safety standards. The material should be:
- Free from BPA, PVC, and phthalates.
- FDA-approved or comply with similar regulatory standards.
- Hypoallergenic and odorless.
2. Shape and Size Variations
Pacifiers come in various shapes to suit different age groups:
- Orthodontic Pacifiers: Designed to support oral development.
- Round/Cherry-Shaped Pacifiers: Mimic a natural nipple for better acceptance.
- Flat Pacifiers: Preferred by some infants for easy latching.
Manufacturers must tailor pacifier sizes based on age groups:
- 0-3 months: Small and soft nipples.
- 3-6 months: Medium size with enhanced durability.
- 6+ months: Larger pacifiers for teething support.
3. Handle and Shield Design
The shield should have ventilation holes to prevent skin irritation and choking hazards. Handles can be:
- Ring-shaped: Easy for babies to grasp.
- Button-type: Prevent interference with sleep.
4. Customization Options
Brands often require:
- Unique colors and patterns.
- Company logos and branding.
- Personalized engravings.
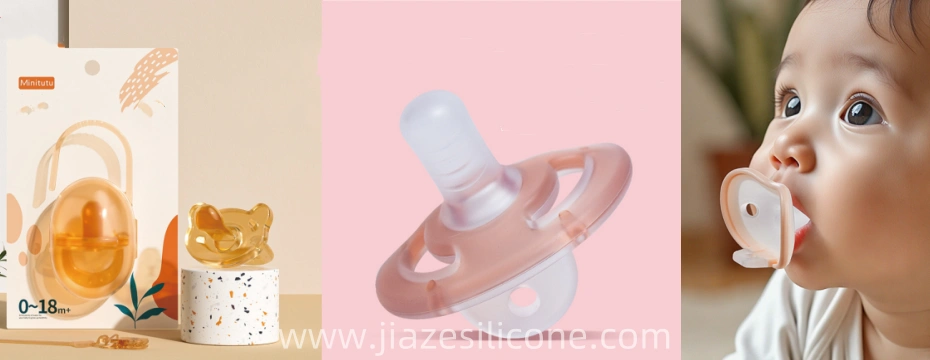
The Manufacturing Process
1. Design & Prototyping
- Computer-Aided Design (CAD) software is used to create 3D models.
- Prototypes are 3D-printed or molded for testing.
- Adjustments are made based on ergonomic and safety assessments.
2. Mold Development
- Precision molds are created to achieve accurate shapes.
- Stainless steel is suit for lsr molds which is long term use.
3. Silicone Injection Molding
- The liquid silicone rubber is injected into heated molds under high pressure.
- The process ensures consistent shape and strength.
4. Vulcanization & Curing
- Heat treatment strengthens the silicone structure.
- The curing process removes residual chemicals and enhances durability.
5. Trimming & Polishing
- Excess material is trimmed to achieve a smooth finish.
- Surface polishing enhances texture and aesthetics.
6. Printing & Branding
- Logos and patterns are applied using laser engraving, pad printing, or embossing.
7. Sterilization & Quality Control
- Each batch undergoes sterilization using steam or UV light.
- Strength and flexibility.
- Resistance to wear and tear.
- Compliance with safety standards.
8. Packaging & Distribution
- Hygienic, tamper-proof containers is perferring to pack baby pacifiers.
- Custom packaging includes brand labels and product information.
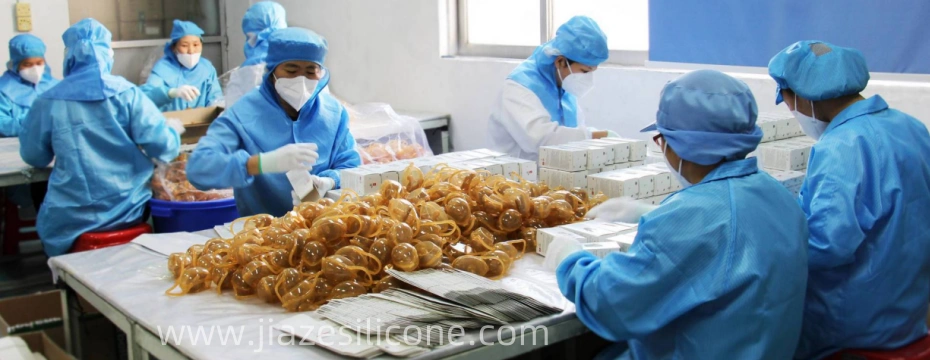
Regulatory Compliance & Safety Standards
Manufacturers must adhere to global safety regulations:
- FDA (USA)
- EN 1400 (Europe)
- ASTM F963 (International)
- ISO 10993 (Biocompatibility)
Conclusion
Silicone baby pacifier manufacturing requires precision, high-quality materials, and adherence to safety standards. Custom-designed pacifiers offer brands a competitive edge while ensuring infant comfort and well-being. By leveraging advanced technology and rigorous quality control, manufacturers can produce safe, durable, and aesthetically appealing pacifiers for global markets.