Medical-grade liquid silicone rubber (LSR) is an essential material in the medical device manufacturing industry. Known for its superior biocompatibility, durability, and flexibility, LSR is widely used in applications such as implants, tubing, seals, and prosthetic devices. This article explores the properties, applications, advantages, regulatory considerations, and future trends of medical-grade liquid silicone in the healthcare sector.
What is Medical Grade Liquid Silicone?
Medical-grade liquid silicone rubber (LSR) is a high-purity silicone elastomer designed specifically for medical applications. It is a two-part platinum-cured silicone that offers excellent consistency, high-temperature resistance, and superior mechanical properties.
Key Properties of Medical-Grade LSR
Medical-grade LSR possesses unique characteristics that make it ideal for medical applications:
- Biocompatibility – It is non-toxic, hypoallergenic, and does not cause adverse reactions when in contact with human tissue.
- Chemical and Thermal Stability – Resistant to extreme temperatures, sterilization processes, and exposure to bodily fluids.
- Flexibility and Softness – Ideal for applications requiring elasticity and conformability.
- Durability and Longevity – Retain its physical properties over extended use, even in harsh environments.
- Serializability – Compatible with autoclaving, gamma radiation, ethylene oxide (EtO), and other sterilization methods.
- Hydrophobicity – Resists moisture absorption, reducing the risk of bacterial growth.
- Transparency and Customization – This can be formulated in different colors or remain clear for specific applications.
Applications of Medical Grade Liquid Silicone in Medical Devices
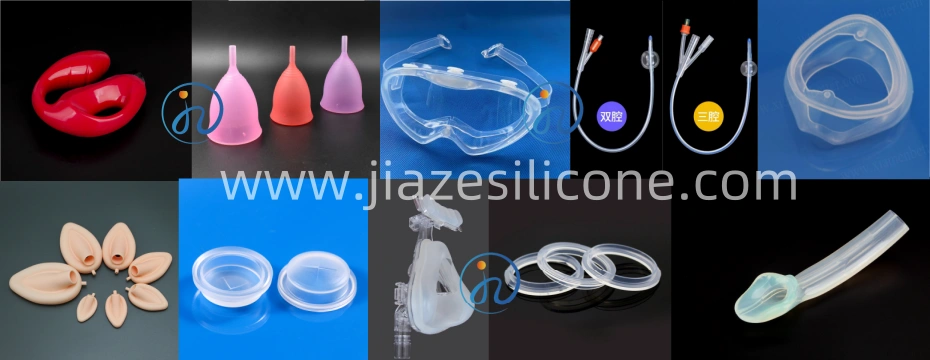
1. Implantable Devices
LSR is frequently used in long-term and short-term implantable medical devices due to its biocompatibility and durability:
- Pacemaker leads and components – Providing insulation and protection for electrical connections.
- Breast implants and soft tissue implants – Offering a natural feel and resilience.
- Joint replacement components – Used in artificial joints and cushioning applications.
2. Medical Tubing and Catheters
- Intravenous (IV) and drug delivery systems – Ensuring smooth fluid transfer without contamination.
- Respiratory and anesthetic equipment – Providing a flexible, kink-resistant structure.
- Urinary and enteral feeding catheters – Offering patient comfort and biocompatibility.
3. Seals, Gaskets, and Valves
- Syringe plungers and pump seals – Ensuring precise fluid control.
- Medical device housings and gaskets – Protecting sensitive electronic components from moisture and contaminants.
4. Prosthetics and Orthopedic Components
LSR is a key material in:
- Prosthetic liners and cushions – Enhancing comfort and wearability for amputees.
- Orthopedic braces and supports – Providing flexibility and durability.
5. Wearable and Diagnostic Devices
Medical wearables and diagnostic tools benefit from LSR’s skin-friendly properties:
- ECG and biosensor patches – Ensuring secure adhesion without skin irritation.
- Silicone-based smart patches – Used in glucose monitoring and drug delivery systems.
6. Surgical Instruments and Disposable Medical Components
- Silicone-coated needles and scalpels – Reducing friction and enhancing precision.
- Surgical instrument grips and handles – Providing ergonomic comfort and slip resistance.
- Single-use medical device components – Ensuring sterility and reducing cross-contamination risks.
Advantages of Using Medical-Grade Liquid Silicone
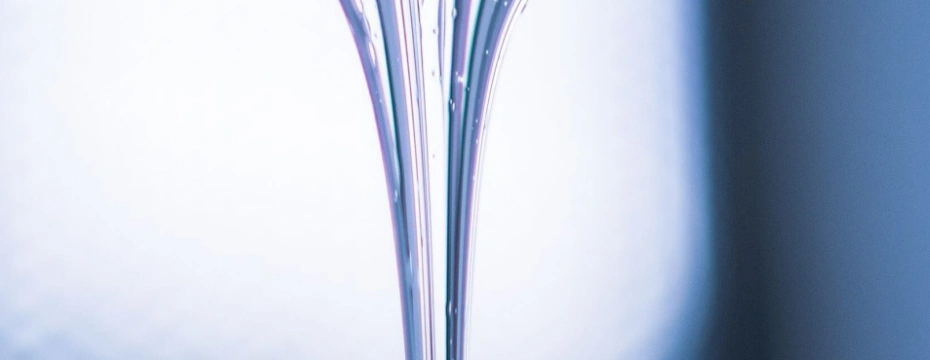
1. High Precision and Design Flexibility
LSR is ideal for producing intricate medical components due to its ability to be injection molded with high precision. This enables the manufacturing of complex geometries with tight tolerances.
2. Enhanced Patient Safety and Comfort
With its hypoallergenic nature and soft texture, LSR minimizes the risk of skin irritation and allergic reactions, making it ideal for direct-contact medical applications.
3. Long-Term Reliability
LSR does not degrade over time when exposed to bodily fluids, UV light, or sterilization processes, ensuring that medical devices remain effective for long durations.
4. Sterilizability and Resistance to Contaminants
LSR can be sterilized using various methods, including autoclaving and gamma radiation, without losing its properties. Its hydrophobic nature also prevents microbial growth and contamination.
5. Cost-Effectiveness and Efficiency
Although medical-grade LSR has a higher upfront material cost, its durability, low maintenance requirements, and manufacturing efficiency make it a cost-effective choice for medical device manufacturers.
Regulatory Considerations for Medical-Grade LSR
Medical-grade LSRs must comply with stringent regulatory requirements to ensure safety and efficacy. Some of the key regulatory standards include:
- U.S. FDA (Food and Drug Administration) Approval – Medical-grade LSRs must meet FDA regulations for medical device applications.
- ISO 10993 Biocompatibility Testing – Ensures that the material does not cause cytotoxicity, irritation, or sensitization.
- USP Class VI Certification – Evaluate the toxicity and safety of medical-grade silicone.
- European Union Medical Device Regulation (EU MDR) – Governs the use of silicone in medical devices in Europe.
Compliance with these regulatory standards ensures that medical devices made from LSR are safe for both short-term and long-term use.
Challenges and Limitations of Medical-Grade Liquid Silicone
While LSR offers numerous advantages, it also comes with some challenges:
- Higher Initial Costs – The cost of raw materials and specialized processing can be higher compared to traditional thermoplastics.
- Processing Complexity – Requires precise temperature and pressure control during injection molding.
- Strict Regulatory Compliance – Extensive testing and certification processes add time and cost to product development.
- Potential Allergic Reactions – Although rare, some individuals may have sensitivities to silicone materials.
Conclusion
Medical-grade liquid silicone rubber (LSR) plays a critical role in the medical device industry due to its biocompatibility, durability, and versatility. From implants and prosthetics to wearable sensors and surgical tools, LSR continues to be the material of choice for manufacturers aiming to develop safe, reliable, and innovative medical devices.