Silicone rubber is a widely used elastomer known for its flexibility, heat resistance, and durability. It comes in various forms, but two of the most common are Liquid Silicone Rubber (LSR) and Solid Silicone Rubber (HTV – High-Temperature Vulcanized Silicone Rubber). While both materials share similar chemical compositions, they differ significantly in processing, properties, and applications. Understanding these differences is crucial for selecting the right material for a given application.
1. Overview of LSR and Solid Silicone Rubber
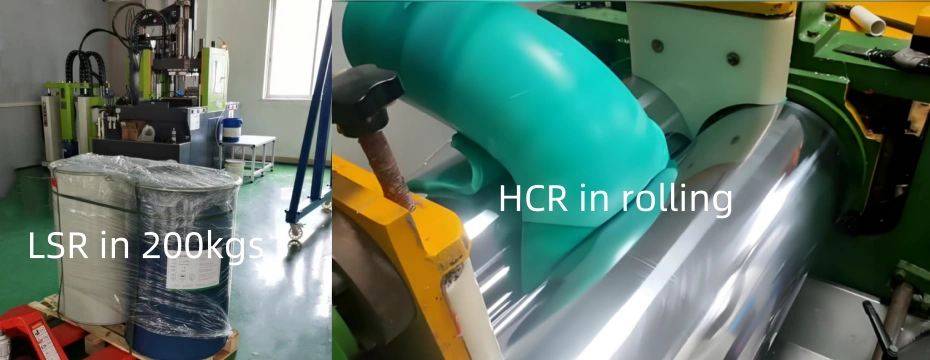
Liquid Silicone Rubber (LSR)
LSR is a two-part, platinum-cured elastomer that remains liquid until it undergoes heat curing. It is processed using liquid injection molding (LIM), making it ideal for high-volume production of precision parts.
Solid Silicone Rubber (HTV)
Solid silicone rubber is a gum-based material that requires heat curing with a peroxide or platinum catalyst. It is processed using compression molding, extrusion, or transfer molding. This form is commonly used for applications requiring greater mechanical strength and durability.
2. Key Differences Between LSR and Solid Silicone Rubber
2.1 Processing and Manufacturing
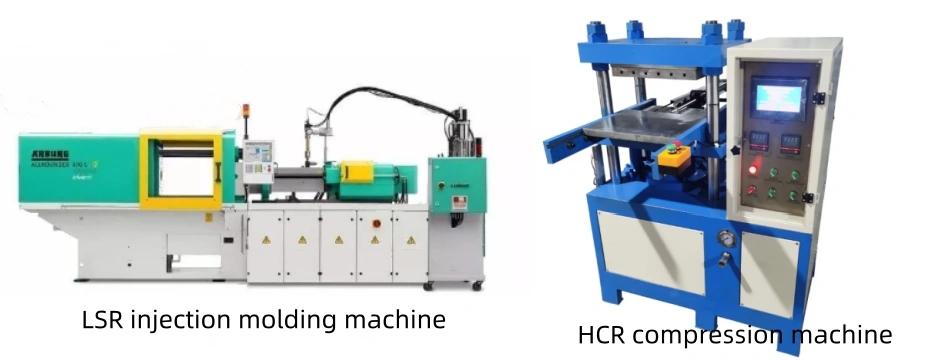
- LSR Processing:
- Requires liquid injection molding (LIM), which is automated and efficient.
- The two liquid components (base polymer and catalyst) mix just before molding.
- Cures rapidly at high temperatures (150-200°C).
- Produces parts with tight tolerances and intricate geometries.
- Solid Silicone Rubber Processing:
- Processed using compression molding, extrusion, or transfer molding.
- Requires milling before molding, making it labor-intensive.
- Cures at lower temperatures compared to LSR but takes longer.
- Less automated, resulting in longer production cycles and higher labor costs.
2.2 Material Properties
- LSR Properties:
- Lower viscosity, enabling easy flow into complex molds.
- High precision and consistency due to automated processing.
- Excellent resistance to extreme temperatures (-50°C to 250°C).
- Superior biocompatibility, making it suitable for medical applications.
- Naturally transparent and easy to pigment.
- Solid Silicone Rubber Properties:
- Higher mechanical strength and durability.
- Better tear resistance, making it ideal for industrial applications.
- Offers greater resistance to compression set compared to LSR.
- More suited for applications requiring thick or bulky parts.
2.3 Curing Mechanism
- LSR: Uses platinum-catalyzed addition curing, which is faster and does not produce byproducts.
- Solid Silicone Rubber: Uses peroxide or platinum curing, with peroxide-cured rubber producing volatile byproducts that require post-curing.
2.4 Cost and Production Efficiency
- LSR: Higher initial tooling costs but more cost-effective for high-volume production due to automation.
- Solid Silicone Rubber: Lower tooling costs but higher labor costs, making it less efficient for mass production.
3. Applications of LSR and Solid Silicone Rubber
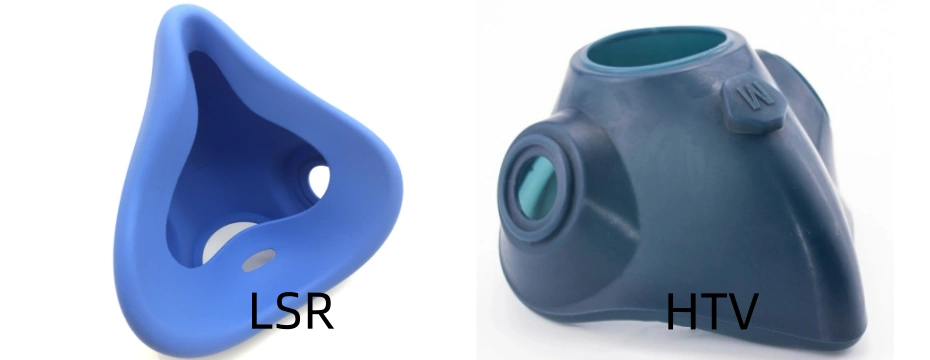
3.1 Medical and Healthcare Applications
- LSR:
- Used in medical tubing, catheters, and implants due to its biocompatibility.
- Ideal for baby products like bottle nipples and pacifiers.
- Applied in wearable medical devices due to its skin-friendly nature.
- Solid Silicone Rubber:
- Common in prosthetic applications where durability is required.
- Used in surgical instruments and equipment seals.
3.2 Automotive Industry
- LSR:
- Used in gaskets, seals, and connectors for engines due to high heat resistance.
- Ideal for LED headlight lenses due to their optical clarity.
- Solid Silicone Rubber:
- Preferred for durable hoses and vibration dampeners.
- Used in ignition cables and radiator seals.
3.3 Consumer Goods and Electronics
- LSR:
- It is found in soft-touch keypads and waterproof seals in electronic devices.
- Used for cookware and baking molds due to food-grade safety.
- Solid Silicone Rubber:
- Applied in oven door seals and high-temperature insulation components.
- Used in electrical insulation for power cables.
3.4 Industrial and Aerospace Applications
- LSR:
- Used for precision seals in aircraft and space applications.
- Ideal for gaskets in high-pressure environments.
- Solid Silicone Rubber:
- Used in heavy-duty industrial rollers and vibration isolators.
- Preferred for weather-resistant seals in construction.
4. Choosing Between LSR and Solid Silicone Rubber
Factors to Consider
- Production Volume: LSR is more efficient for high-volume automated production, whereas solid silicone is better for low to medium-scale production.
- Design Complexity: LSR is superior for intricate designs, while solid silicone works best for robust, thicker parts.
- Cost: Initial tooling costs are higher for LSR but reduce costs per unit in large-scale manufacturing.
- Performance Requirements: LSR offers high precision and biocompatibility, while solid silicone provides better mechanical strength.
5. Conclusion
Both LSR and solid silicone rubber offer excellent material properties but cater to different application needs. LSR excels in high-precision, automated, and biocompatible applications, while solid silicone rubber is the go-to choice for durability and mechanical strength in industrial settings. Selecting the right type depends on factors like production scale, cost efficiency, and specific performance requirements.