Liquid Silicone Rubber (LSR) injection molding is a specialized manufacturing process used to create flexible, durable, and high-performance silicone parts. It is widely used in medical, automotive, and consumer product industries due to its biocompatibility, heat resistance, and flexibility. Prototyping in LSR injection molding is crucial to ensuring a cost-effective, high-quality final product. This guide explores the essentials of LSR injection molding and best practices for effective prototyping.
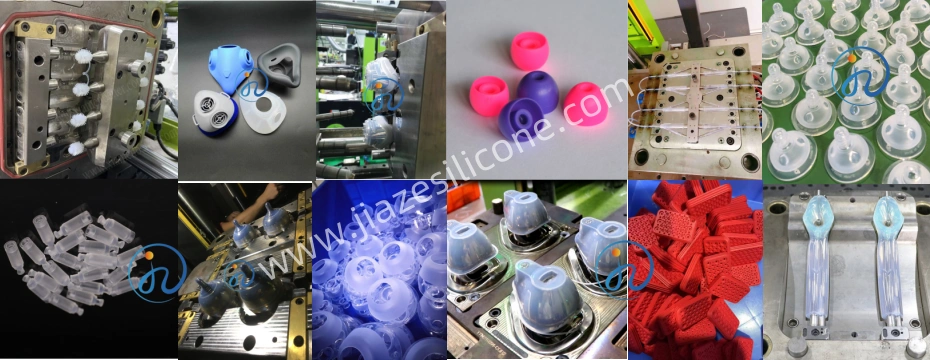
1. Understanding LSR Injection Molding
LSR injection molding is a process where two-part liquid silicone is mixed, injected into a mold, and cured to create a final product. Unlike traditional thermoplastic injection molding, LSR remains in liquid form until it undergoes curing in a heated mold.
Key Components of LSR Injection Molding:
- LSR Material: A two-part liquid mixture (A and B components) that cures into a flexible solid.
- Injection Molding Machine: Designed for LSR processing with a cold runner system and a heated mold.
- Mold (Tooling): Typically made from steel or aluminum, featuring precise cavity designs for accurate part replication.
- Mixing & Metering System: Ensures a precise ratio of A and B components to achieve optimal curing.
The process involves injecting LSR into a mold cavity under controlled conditions, where it is heat-cured into a final shape.
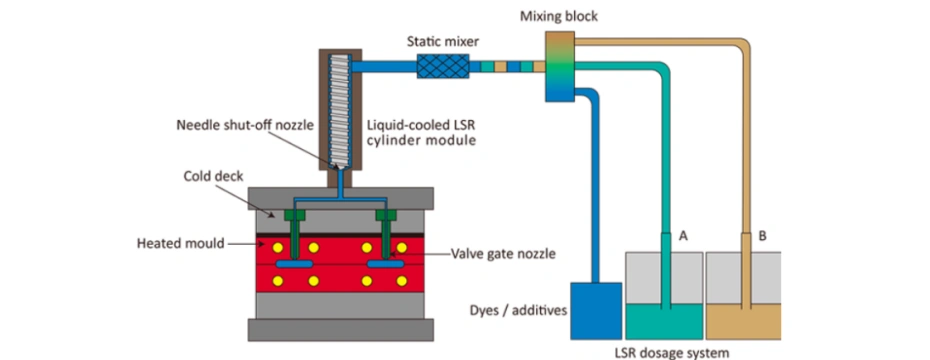
2. Importance of Prototyping in LSR Injection Molding
Prototyping allows engineers to test designs, verify material properties, and refine production processes before mass production. Benefits include:
- Design validation: Ensures the part meets dimensional and functional requirements.
- Material performance testing: Evaluates how LSR behaves under real-world conditions.
- Process optimization: Identifies potential manufacturing issues early.
- Cost reduction: Minimizes expensive mold modifications and production delays.
3. Design Considerations for LSR Injection Molding
Effective design is crucial for achieving high-quality LSR-molded parts. Key considerations include:
a. Wall Thickness
- Maintain uniform wall thickness (typically 0.5 – 3 mm) to prevent air pockets and ensure even curing.
- Avoid sharp transitions; use smooth, gradual thickness changes.
b. Draft Angles
- Add 0.5 to 2 degrees of draft for easy part ejection.
- LSR’s flexibility allows for minimal drafting in some applications.
c. Undercuts & Complex Geometries
- LSR’s high flexibility enables complex shapes and undercuts without expensive tooling.
- Use self-demolding features like collapsible cores to minimize mold complexity.
d. Venting & Gating
- Venting is crucial for avoiding air entrapment and improving flow.
- Gate placement should minimize material wastage and ensure uniform fill.
- A cold-runner system helps prevent material waste.
4. Material Selection for Prototyping
Choosing the right LSR formulation impacts durability, flexibility, and biocompatibility. Common types include:
- Medical-Grade LSR – Biocompatible, used in implants and medical devices.
- High-Temperature Resistant LSR – Suitable for automotive and industrial applications.
- Flame-Retardant LSR – Used in electrical and safety applications.
- Food-Grade LSR – Compliant with FDA regulations for food and beverage products.
Testing multiple formulations during prototyping ensures the best fit for the final application.
5. Prototyping Methods for LSR Injection Molding
Several prototyping techniques allow manufacturers to refine designs before mass production:
a. Soft Tooling (Aluminum Molds)
- Faster and cheaper than steel molds.
- Suitable for low-volume production (100-1,000 units).
- Ideal for design iterations before finalizing a steel mold.
b. 3D Printing with LSR-Like Materials
- Rapid validation of part geometry.
- It is not a perfect substitute for real LSR testing due to its different mechanical properties.
c. CNC Machining of Silicone Parts
- Creates precise prototypes from actual LSR material.
- More expensive and time-consuming than soft tooling.
d. Rapid LSR Injection Molding
- It uses low-cost, quick-turnaround molds to test actual LSR parts.
- Allows real-world evaluation before committing to full-scale production.
6. Common LSR Molding Defects & How to Prevent Them
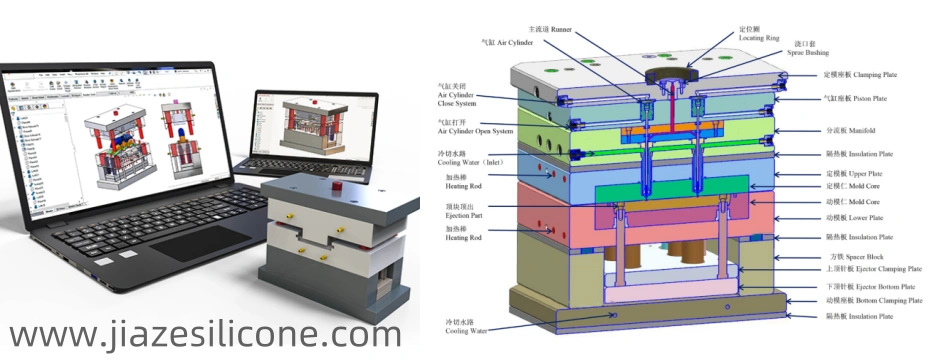
Even with careful prototyping, defects can occur. Below are common issues and their solutions:
Defect | Cause | Solution |
---|---|---|
Air Bubbles | Poor venting, trapped gases | Improve venting, adjust injection speed |
Flashing | Excessive injection pressure, poor mold fit | Optimize clamping force, ensure tight mold fit |
Short Shots | Insufficient material flow | Increase injection pressure, optimize gate location |
Flow Lines | Improper gating, uneven temperature | Adjust gate placement, ensure uniform heating |
Surface Defects | Mold contamination, inconsistent curing | Clean mold regularly, optimize curing time |
Addressing these defects early in prototyping helps prevent costly issues in mass production.
7. Cost Considerations in LSR Prototyping
Prototyping can be expensive, but strategic decisions help control costs:
- Use rapid prototyping methods before investing in full-scale molds.
- Optimize part design to reduce material waste and simplify tooling.
- Select the right LSR formulation to balance performance and cost.
- Work with experienced mold makers to avoid design errors that increase costs.
By refining the prototype process, manufacturers can achieve cost-effective, high-quality production.
8. Transitioning from Prototype to Mass Production
Once the prototype is validated, transitioning to full-scale production involves:
- Finalizing the mold design to enhance durability and efficiency.
- Optimizing process parameters (injection pressure, temperature, and cycle time).
- Implementing strict quality control to ensure consistency.
- Scaling up production efficiently while maintaining performance standards.
A well-executed prototyping phase ensures a smoother transition to high-volume production with minimal risk.
Conclusion
LSR injection molding is a highly versatile and reliable manufacturing process. Effective prototyping is essential for achieving high-quality, functional, and cost-efficient parts. By optimizing design, selecting appropriate materials, leveraging advanced prototyping techniques, and addressing defects early, manufacturers can streamline the process and enhance product success. Whether creating small batches or preparing for large-scale production, investing in robust prototyping methods ensures a superior final product.