Liquid Silicone Rubber (LSR) has emerged as a critical material in the automotive industry, particularly for electric vehicles (EVs). As the world transitions toward cleaner, more sustainable forms of transportation, EVs are at the forefront of this revolution. In this transformation, materials like LSR have become vital due to their unique properties that meet the specific demands of EV manufacturing. LSR offers excellent thermal stability, durability, and electrical insulation, making it a preferred choice for components in electric vehicles. In this article, we’ll explore how LSR plays a significant role in EVs and its impact on the broader industry.
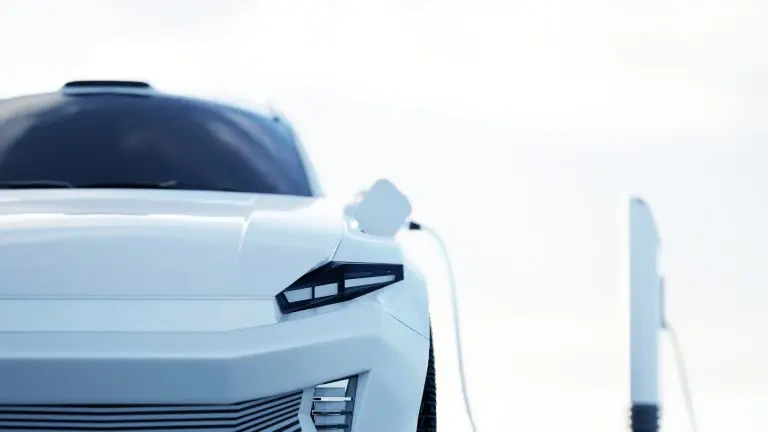
Key Properties of LSR Relevant to Electric Vehicles
LSR is a two-part silicone material that cures when heated, creating a rubber-like substance. It is widely used in manufacturing applications where durability, flexibility, and resistance to environmental factors are essential. Here are some of the properties that make LSR ideal for use in electric vehicles:
- Thermal Stability EV components, particularly batteries and motors, generate significant heat during operation. LSR can withstand high temperatures (typically up to 200°C) without losing its shape or properties, which is critical for components in high-heat environments, such as gaskets, seals, and connectors in EV battery packs.
- Electrical Insulation Electric vehicles rely heavily on electrical systems, and ensuring these systems are safe and efficient is paramount. LSR is an excellent electrical insulator, which helps prevent short circuits, ensuring safety and longevity in high-voltage applications like power connectors, charging systems, and electronic control units (ECUs).
- Chemical Resistance LSR has excellent resistance to chemicals, oils, and coolants, which are prevalent in automotive environments. This makes LSR ideal for seals and gaskets that are exposed to fluids that could otherwise degrade conventional materials, ensuring long-term reliability.
- Flexibility and Elasticity LSR remains highly flexible even under extreme temperatures and stress, making it ideal for dynamic sealing applications. It can withstand repeated stretching, compression, and twisting, which is beneficial in EV components that experience regular mechanical stress, such as connectors and cables.
- Lightweight As electric vehicles focus on maximizing energy efficiency, reducing the overall weight of the vehicle is crucial. LSR is a lightweight material, helping manufacturers reduce the weight of key components without compromising durability or safety.
Applications of LSR in Electric Vehicles
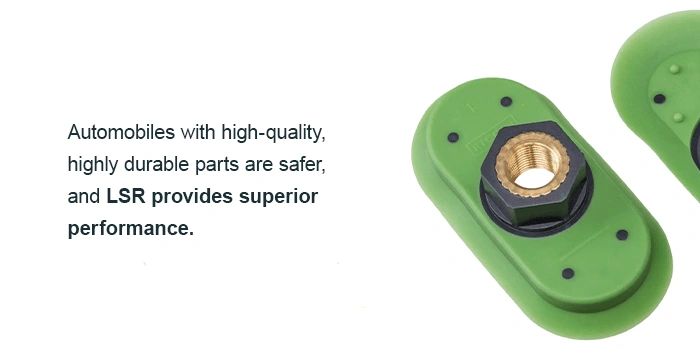
1. Battery Pack Components
The battery pack is the heart of an electric vehicle. It stores and provides the electrical energy necessary to power the motor. LSR plays a vital role in ensuring the reliability, efficiency, and safety of these battery packs.
- Seals and Gaskets: The battery pack requires seals that can withstand high temperatures, pressure, and exposure to chemicals. LSR provides the necessary thermal and chemical resistance, making it ideal for sealing battery compartments to prevent ingress of dust, moisture, and other contaminants.
- Thermal Management: LSR is used in thermal management components, such as thermal interface pads, which help dissipate heat generated during battery operation, maintaining an optimal temperature range and prolonging battery life.
2. Charging Connectors
Electric vehicles rely on charging systems that often expose components to high voltages, external weather conditions, and frequent wear. LSR is used in the production of:
- High-Voltage Connectors: LSR’s electrical insulation properties ensure that high-voltage connectors maintain safety standards and resist degradation over time.
- Cable Insulation: LSR is also employed in insulating charging cables due to its resistance to extreme temperatures and harsh environmental conditions, providing a durable and flexible solution for both the vehicle’s internal and external charging interfaces.
3. Electric Motor and Inverter Components
Electric motors and inverters are key components in EVs, converting electrical energy from the battery into mechanical energy to drive the vehicle. LSR’s ability to insulate and resist heat plays a critical role in these systems.
- Seals for Motor Housings: To prevent contamination and ensure the longevity of electric motors, LSR is used in seals and gaskets for motor housings. These components need to remain flexible and durable under continuous high-temperature operation.
- Inverter Insulation: Inverters convert direct current (DC) from the battery to alternating current (AC) used by the electric motor. LSR is used as an insulative barrier to protect against electrical surges and ensure the safe operation of inverters.
4. Lighting and Display Systems
Electric vehicles often integrate advanced lighting and display systems, which benefit from the properties of LSR:
- Optical LSR: LSR can be used in transparent or translucent applications for optical lenses and light guides in vehicle headlights, taillights, and interior lighting. It provides excellent clarity, flexibility in design, and resistance to UV light and weathering.
- Touchscreen and Control Seals: Many modern EVs feature touchscreens and advanced control panels, which need to be protected from moisture, dust, and other environmental factors. LSR is an ideal material for producing protective seals for these sensitive components.
5. Vibration Dampening
Electric vehicles are often quieter than traditional combustion vehicles, which can make vibrations from electric motors more noticeable. LSR is used in vibration-dampening systems, such as mounts and bushings, to reduce noise, vibrations, and harshness (NVH) levels in EVs. Its elasticity helps absorb shocks and vibrations, contributing to a smoother and quieter ride.
Sustainability and Environmental Impact
One of the key advantages of LSR in electric vehicles is its contribution to the overall sustainability of the vehicle. LSR is a highly durable material, which reduces the need for frequent replacement of components, thereby reducing waste. Additionally, its resistance to heat, chemicals, and wear extends the lifespan of EV components, minimizing environmental impact over time.
Moreover, LSR is produced using environmentally friendly manufacturing processes. The injection molding process for LSR is efficient and produces minimal waste. The recyclability of LSR parts also aligns with the broader goals of reducing waste and improving the sustainability of electric vehicles.
Challenges and Future of LSR in Electric Vehicles
While LSR is becoming increasingly popular in EV manufacturing, there are still challenges to overcome. One key challenge is the high cost associated with high-quality LSR materials. As the demand for electric vehicles grows, the cost of raw materials is likely to increase, potentially impacting the widespread adoption of LSR in mass-produced vehicles.
Another challenge is ensuring that LSR meets the rigorous safety and performance standards required in automotive applications. Continuous research and development are needed to optimize the performance of LSR in emerging EV technologies, such as solid-state batteries and wireless charging systems.
Looking ahead, the role of LSR in electric vehicles is expected to grow. With advancements in material science, new formulations of LSR may be developed to enhance its properties further. Innovations in manufacturing techniques, such as 3D printing with LSR, could also open new possibilities for custom EV components, allowing for greater design flexibility and performance optimization.