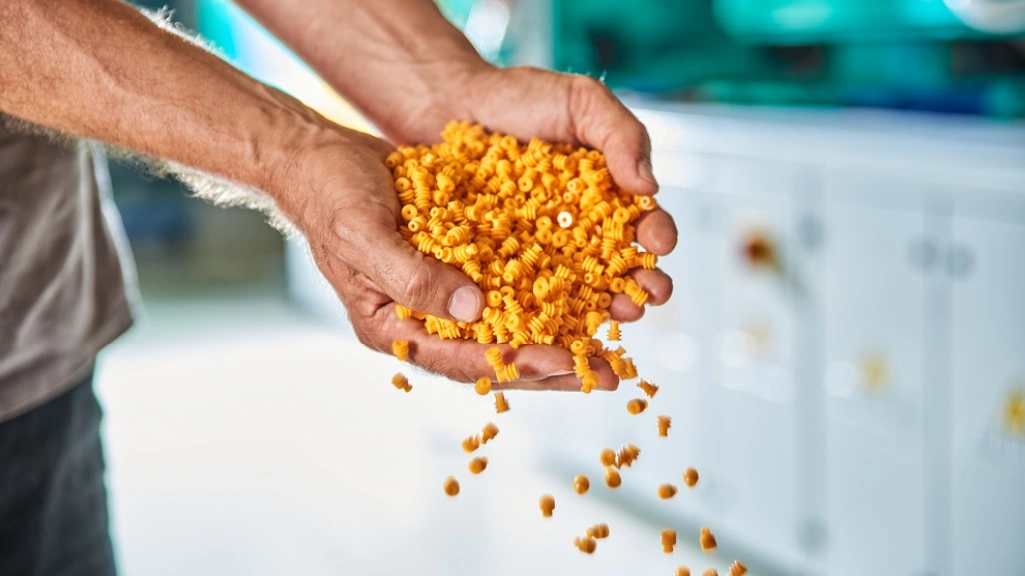
Welcome to the fascinating world of Liquid Silicone Rubber Custom Component Solutions!
This article delves into the myriad benefits of Liquid Silicone Rubber (LSR) in creating custom components. From its outstanding versatility and superior durability to its biocompatibility and cost-effectiveness, LSR stands out as a material of choice across various industries. We will explore how LSR meets the stringent demands of sectors like medical, automotive, and consumer electronics, offering unparalleled precision and reliability.
Benefits of Liquid Silicone Rubber in Custom Components
Outstanding Versatility and Flexibility
From my considerable experience in the area, I can with confidence mention that Liquid Silicone Rubber (LSR) offers exceptional convenience and adaptability. This product is extremely adaptable to numerous forms and dimensions, making it a suitable selection for customized element services. Its capability to preserve its residential or commercial properties across a vast array of temperatures and environmental problems is specifically valuable for sectors requiring precise and reputable parts.
Superior Durability and Longevity
One of the standout advantages of LSR is its extraordinary longevity. Unlike various other products, LSR does not weaken conveniently when exposed to rough environmental conditions such as UV light, ozone, and extreme temperatures. This ensures that the custom parts have a longer life expectancy, lowering the demand for regular substitutes.
Biocompatibility and Safety
Another substantial advantage of LSR is its biocompatibility, making it appropriate for clinical and food-grade applications. The product is non-toxic, hypoallergenic, and can be decontaminated without losing its buildings. This makes it a preferred option for custom parts in the medical care and food markets.
High Precision and Consistency
In the realm of custom-made element production, precision and consistency are critical. LSR provides excellent moldability, permitting the production of elaborate layouts with limited resistances. This high degree of precision ensures that each component satisfies the exact specs needed for its application.
Cost-Effectiveness
While the initial expense of LSR may be greater compared to various other materials, its long-lasting benefits make it a cost-effective option. The sturdiness and lowered need for substitutes convert to lower maintenance prices. Additionally, the efficient manufacturing process of LSR elements can lead to significant expense savings in time.
Environmental Resistance
LSR is extremely immune to different ecological elements, consisting of water, chemicals, and extreme temperatures. This resistance makes it an excellent option for parts that need to perform reliably in difficult environments. The product’s capability to stand up to such problems without weakening makes sure constant efficiency and long life.
Advantage | Description |
---|---|
Adaptability and Flexibility | Adaptable to numerous sizes and shapes, keeps residential or commercial properties throughout temperature arrays. |
Longevity and Longevity | Excellent moldability for elaborate designs with tight resistance. |
Biocompatibility | Safe, hypoallergenic, and sterilizable, ideal for medical and food applications. |
Precision and Consistency | Excellent moldability for elaborate designs with tight resistances. |
Cost-Effectiveness | Lasting benefits and decreased upkeep prices balance out initial greater expenses. |
Environmental Resistance | Resistant to water, chemicals, and severe temperatures, ensuring constant efficiency. |
The Customization Process for Liquid Silicone Rubber Components
First Consultation and Requirement Analysis
The customization process for Liquid Silicone Rubber (LSR) components starts with a thorough appointment. During this stage, we gather comprehensive requirements from the customer, consisting of the preferred requirements, application, and efficiency assumptions. This first action is vital for guaranteeing that the end product satisfies all essential standards and features as intended.
Layout and Prototyping
Once the needs are clearly defined, the following action involves the style and prototyping of the LSR elements. Utilizing sophisticated CAD software applications, our designers produce thorough layouts that are tailored to the client’s specifications. Prototyping adheres to, enabling us to produce first samples that can be checked for fit, kind, and feature. This stage typically entails numerous iterations to improve the layout and satisfy the precise requirements of the application.
Product Selection
Picking the best kind of Liquid Silicone Rubber is a vital part of the modification procedure. LSR is readily available in various grades, each with distinct residential or commercial properties such as firmness, tensile toughness, and temperature resistance. The option relies on the certain requirements of the part, including its operating setting and mechanical tensions. Our material experts provide guidance to make sure the optimum LSR grade is picked.
Mold And Mildew Design and Manufacturing
Complying with the authorization of the prototype, the emphasis changes to mold and mildew design and production. Accuracy molds are necessary for generating high-grade LSR components. Our mold designers use modern technology to create mold and mildew that ensure regular and exact manufacturing. The molds are then manufactured utilizing top-quality materials to hold up against the roughness of the molding process.
Shot Molding Process
The core of the personalization procedure is the shot molding of the LSR elements. This process includes infusing the liquid silicone rubber right into the mold and mildew under controlled conditions. Trick specifications such as temperature, stress, and treating time are meticulously taken care of to achieve the desired residential or commercial properties in the last item. The shot molding procedure is extremely efficient and enables the production of intricate forms with limited resistance.
Post-Processing and Finishing
After molding, the parts undergo post-processing to get rid of any excess product and attain the final dimensions. This may include trimming, deburring, and surface therapy. Depending upon the application, additional completing processes such as painting, layer, or assembly may be required to satisfy the customer’s requirements.
Quality Control and Inspection
Quality assurance is integrated throughout the customization procedure to make certain that each part fulfills the highest possible standards. Rigorous assessment treatments are applied, consisting of dimensional checks, material testing, and functional testing. This makes sure that the final LSR components are trustworthy and perform as expected in their desired applications.
Future Trends in Liquid Silicone Rubber Custom Component Solutions
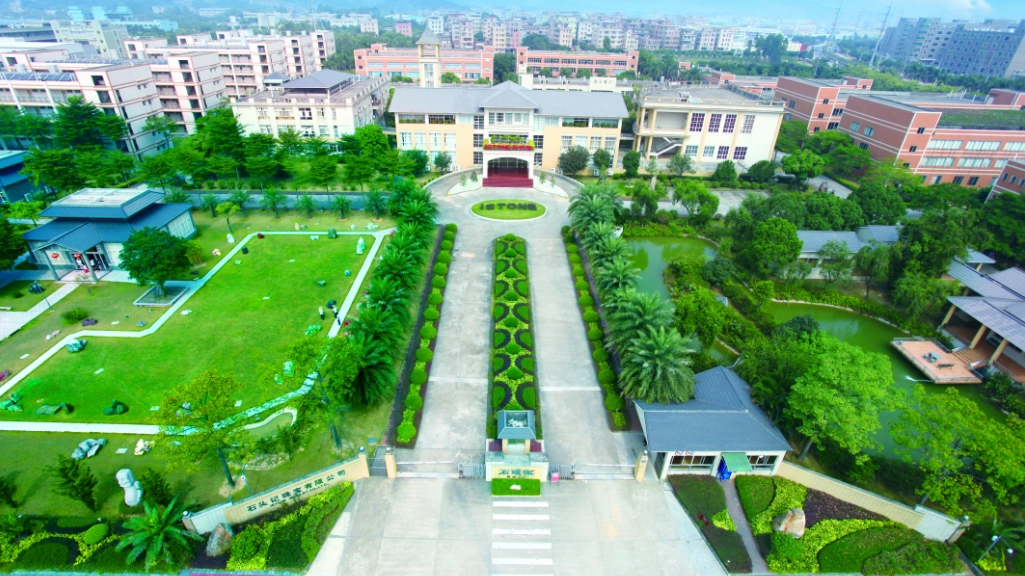
Innovations in Material Science
The future of Liquid Silicone Rubber (LSR) customized element services is positioned for substantial advancements driven by ongoing technologies in material science. Scientists are constantly developing brand-new solutions that enhance the integral residential properties of LSR, such as its versatility, durability, and resistance to extreme temperature levels. Arising products aim to boost biocompatibility, making LSR a much more attractive selection for clinical and medical care applications.
Combination with Smart Technologies
Another interesting fad is the assimilation of LSR elements with smart innovations. As the need for clever gadgets and wearables expands, LSR is being significantly utilized in the manufacturing of versatile sensing units, digital skin, and other smart elements. This integration not only leverages the physical homes of LSR but also boosts the performance and user experience of smart products.
Sustainability and Eco-Friendly Solutions
The push in the direction of sustainability is influencing the LSR sector as well. Makers are discovering environment-friendly LSR formulations that reduce environmental impact. This consists of the development of recyclable and biodegradable LSR materials. In addition, the production processes are being maximized to minimize waste and power consumption, lining up with worldwide sustainability objectives.
Improved Customization Capabilities
Future trends indicate a significant renovation in the personalization capacities of LSR elements. Advanced production methods, such as 3D printing and injection molding, are being improved to enable even more elaborate and specific layouts. These technologies allow producers to create extremely customized elements that satisfy specific requirements, leading to a wider series of applications across numerous markets.
Industry-Specific Innovations
Numerous industries are likely to see customized advancements in LSR services. For circumstances:
Industry | Technology |
---|---|
Automotive | Boosted securing remedies and high-performance gaskets |
Clinical | Biocompatible implants and wearables |
Consumer Electronics | Flexible and sturdy parts for wearables |
Aerospace | Heat-resistant and lightweight elements |
Collective Innovations
The partnership between product researchers, designers, and industry experts is vital for driving future innovations in LSR custom-made element solutions. Such collaborations cultivate the exchange of expertise and know-how, leading to the development of sophisticated applications and solutions that address developing market requirements.
Conclusion
The future of Liquid Silicone Rubber personalized element solutions looks encouraging, with advancements in material science, smart innovation assimilation, sustainability initiatives, boosted modification, and industry-specific technologies. These trends are readied to revolutionize the means LSR components are developed, produced, and utilized, leading the way for new applications and improved performance throughout numerous sectors.