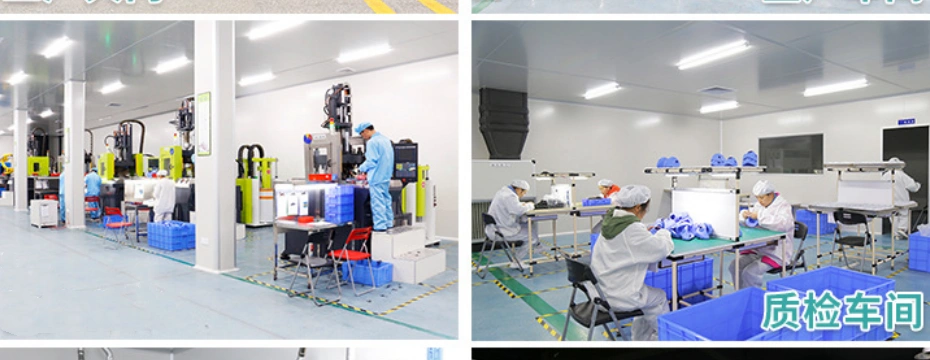
Selecting the Right Materials for LSR Projects
Comprehending Liquid Silicone Rubber (LSR)
When beginning effective LSR Projects, picking the appropriate products is extremely important. Fluid Silicone Rubber (LSR) is a functional product known for its special residential or commercial properties such as high thermal security, chemical resistance, and flexibility. These features make LSR a suitable choice for a vast array of applications, from medical gadgets to automobile components.
Trick Material Properties
To ensure the success of an LSR job, it is critical to think about the following products for residential or commercial properties:
Property | Relevance |
---|---|
Thickness | Figure out the convenience of flow and mold and mildew dental filling. |
Tear Strength | Makes certain durability and resistance to tearing under tension. |
Solidity | Impacts the flexibility and strength of the end product. |
Openness | This is crucial for applications requiring clear or clear parts. |
Biocompatibility | Crucial for medical and food-grade applications. |
Distributor Selection
Selecting a trusted vendor is similarly important. Look for providers who give regular high quality, offer technological assistance, and have a wide variety of LSR grades. Establishing a great partnership with your vendor can lead to better material referrals and troubleshooting aid.
Product Testing and Validation
Prior to waging full-blown production, it is necessary to carry out detailed material testing and validation. This consists of:
- Rheological testing to understand circulation features.
- Mechanical testing to examine homes like tensile toughness and prolongation.
- Environmental screening to guarantee product performance under various conditions.
These examinations aid in verifying that the chosen LSR material meets the details requirements of your project.
Regulative Compliance
For projects in managed markets such as health care or food production, making certain that the selected LSR material adheres to pertinent criteria and policies is crucial. This may consist of FDA, ISO, or various other industry-specific accreditations.
By diligently picking the best materials and performing thorough screening, you lay a solid structure for an effective Liquid Injection Molding project. The next action involves creating efficient molds to match these products.
Creating Effective Molds for LSR Projects
Understanding Material Properties
When developing molds for Liquid Injection Molding (LIM) tasks, it is essential to have a thorough understanding of the material properties of Liquid Silicone Rubber (LSR). LSR is understood for its low thickness, which permits it to flow conveniently into detailed mold designs. This particular requires an exact mold style to guarantee exact part reproduction and to avoid flaws such as flash and air entrapment.
Precision in Mold Design
Precision is the type of mold and mildew layout for LSR projects. The mold and mildew should be designed with tight tolerances to accommodate the product’s behavior during the injection process. This consists of factors to consider for shrinkage, which can differ depending upon the certain kind of LSR used. Additionally, the mold needs to be designed to assist in easy demolding to keep the integrity of the ended-up product.
Air Flow and Temperature Control
Efficient ventilation is vital in LSR mold and mildew style to avoid air entrapment, which can bring about issues. Appropriate venting channels should be included right into the mold to allow trapped air to leave throughout the injection procedure. Temperature control is another critical aspect; the mold and mildew need to be maintained at regular temperature degrees to guarantee consistent treatment of the LSR. This often involves incorporating home heating elements into the mold style.
Gateway and Runner Design
The style of gateways and joggers in the mold and mildew is essential for managing the flow of LSR. Gates must be strategically put to make certain even circulation of the product and to minimize the danger of air pockets. The size and form of the runners need to be maximized to stabilize the circulation rate and stress, making sure that the LSR loads the mold and mildew cavity evenly.
Toughness and Maintenance
Longevity is a substantial consideration in mold layout for LSR projects. The molds should be constructed from materials that can hold up against the high stress and temperature levels included in the shot molding procedure. Routine upkeep is additionally vital to guarantee that the mold and mildew continue to be in optimum problem, which consists of routine cleaning and inspection for deterioration.
Prototyping and Testing
Prior to major manufacturing, it is recommended to develop models of the mold layout. Prototyping enables the recognition and resolution of prospective concerns, ensuring that the final mold style works and is effective. Checking the models under actual manufacturing problems gives valuable understanding and aids in fine-tuning the mold layout for optimum efficiency.
Enhancing the Injection Molding Process
Recognizing the Injection Molding Cycle
To achieve an effective Liquid Injection Molding (LIM) project, it’s crucial to understand the entire injection molding cycle. This cycle normally contains the following phases:
Stage | Description |
---|---|
Injection | The fluid silicone rubber (LSR) is infused into the mold cavity. |
Air conditioning | The material cools and solidifies within the mold. |
Ejection | The strengthened component is ejected from the mold. |
Enhancing Temperature and Pressure
Temperature and stress play an important function in the LIM procedure. Precise control of these parameters makes certain the product moves appropriately and fills the mold and mildew totally. Right here are some essential factors to consider:
Parameter | Optimum Range |
---|---|
Shot Temperature | 20-30 ° C over the material’s melting factor |
Injection Pressure | 100-200 bar |
Cycle Time Optimization
Minimizing cycle time without jeopardizing top quality can significantly enhance efficiency. Concentrate on adhering to aspects to maximize cycle time:
- Cooling Time: Ensure ample cooling to prevent flaws however stay clear of excessive cooling that prolongs the cycle.
- Shot Speed: Adjust the speed to balance between loading the mold and mildew swiftly and avoiding defects.
- Automation: Implement automation to enhance the ejection and take care of procedures.
Material Handling and Preparation
Appropriate material handling and preparation are vital for optimizing the shot molding procedure. Trick steps include:
- Storage: Store LSR materials in a controlled atmosphere to stop contamination and destruction.
- Blending: Ensure thorough mixing of the two-part LSR parts to attain a regular material blend.
- Degassing: Remove air bubbles from the material prior to the shot to stay clear of problems.
Advanced Process Control
Utilizing sophisticated procedure control strategies can additionally enhance the performance and high quality of the LIM procedure. Think about integrating:
- Real-time Monitoring: Employ sensors and software to check crucial specifications in actual time.
- Comments Systems: Implement response systems that automatically change specifications to keep optimal problems.
- Anticipating Maintenance: Use anticipating upkeep devices to minimize downtime and make certain constant production.
Quality Assurance and Testing in LSR Projects
Importance of Quality Control
Quality control is extremely important in Liquid Injection Molding (LIM) to make certain that the final item fulfills the needed specifications and criteria. Implementing a robust quality control system assists in determining issues early in the production procedure, therefore saving time and reducing expenses.
Material Testing
Before beginning the molding process, it is critical to evaluate the raw products for consistency and quality. This includes checking the thickness, purity, and reactivity of the Liquid Silicone Rubber (LSR). Ensuring that the materials meet the required requirements can protect against issues such as incomplete dental filling and inconsistent healing.
In-Process Monitoring
Throughout the injection molding process, constant tracking is essential. Criteria such as temperature level, stress, and injection rate should be very closely viewed. Using advanced sensing units and automation can assist in preserving these parameters within the wanted variety, thus ensuring regular items of high quality.
Post-Molding Inspections
Once the molding process is complete, a collection of examinations should be performed to verify the high quality of the shaped parts. Aesthetic evaluations can help recognize surface area flaws, while dimensional checks ensure that the parts satisfy the specified tolerances. Non-destructive screening approaches, such as X-ray or ultrasonic testing, can be made use of for more essential applications.
Practical Testing
Practical testing is an additional important aspect of top quality control in LSR jobs. This involves testing the molded parts under real operating problems to guarantee they are carried out as expected. For circumstances, if the parts are to be used in medical gadgets, they need to be tested for biocompatibility and sterilization resistance.
Paperwork and Traceability
Maintaining detailed documents throughout the manufacturing process is essential for traceability and conformity with market standards. This consists of taping the batch varieties of resources, process specifications, and assessment results. Proper documents assist in determining the origin of issues and assist in rehabilitative actions.
Constant Improvement
Quality assurance is not a one-time task but a continual procedure. Normal audits and testimonials need to be conducted to determine areas for renovation. Implementing a response loophole where data from high-quality control is utilized to fine-tune the molding process can bring about greater efficiency and far better item top quality with time.
Troubleshooting Common Issues in Liquid Injection Molding
Troubleshooting typical concerns in liquid injection molding (LIM) is vital to guarantee the success of any Liquid Silicone Rubber (LSR) project. Below are some common problems and their solutions, organized by certain areas of the molding procedure.
Material Issues
Issues connected to the product can substantially influence the top quality of the end product. Typical material-related issues consist of:
Problem | Create | Solution |
---|---|---|
Irregular Viscosity | Incorrect blending or storage conditions | Ensure materials are blended completely and stored under recommended conditions |
Contamination | International fragments in the material | Carry out strict material handling and storage methods |
Mold And Mildew Design Issues
Effective mold layout is crucial for effective LIM projects. Some typical mold and mildew design problems include:
Problem | Cause | Service |
---|---|---|
Flash | Incorrect mold securing or worn-out mold parts | Inspect mold securing force and change worn-out components |
Incomplete Filling | Inadequate airing vent or wrong gateway layout | Enhance venting and optimize gate style |
Refine Control Issues
Keeping control over the shot molding process is essential for high-quality manufacturing. Typical procedure control concerns include:
Problem | Cause | Service |
---|---|---|
Variations in Cycle Time | Irregular device settings or material feed | Regularly calibrate equipments and make certain regular product feed |
Temperature Fluctuations | Faulty burner or improper air conditioning | Evaluate and keep burner and maximize cooling system |
Quality Assurance Issues
Quality control is vital to detect and deal with problems early. Usual quality assurance issues consist of:
Problem | Cause | Option |
---|---|---|
Dimensional Inaccuracy | Product shrinking or mold and mildew wear | Represent material shrinkage in style and routinely evaluate molds |
Surface Defects | Incorrect mold and mildew surface area coating or contamination | Make sure mold surfaces are properly ended up and without impurities |
Device Maintenance Issues
Routine upkeep of injection molding devices is essential to avoid malfunctions and ensure constant top quality. Typical maintenance-related issues consist of:
Problem | Cause | Service |
---|---|---|
Equipment Downtime | Lack of regular maintenance | Apply a normal upkeep timetable |
Hydraulic Leaks | Damaged seals or pipes | Regularly evaluate and change seals and hose pipes |
By attending to these usual issues via mindful product selection, efficient mold layout, rigorous procedure control, strenuous quality assurance, and regular device maintenance, you can dramatically enhance the success price of your LSR tasks.
FAQs: Keys to a Successful LSR Project
What is Liquid Silicone Rubber (LSR)?
Liquid Silicone Rubber (LSR) is a versatile material known for its high thermal stability, chemical resistance, and flexibility. These properties make LSR an ideal choice for a wide range of applications, including medical devices and automotive components.
Why is selecting the right material important in Liquid Injection Molding (LIM)?
Choosing the right material is crucial because it directly impacts the quality and performance of the final product. Key properties to consider include viscosity, tear strength, hardness, transparency, and biocompatibility.
How do I choose a reliable supplier for LSR materials?
Look for suppliers who provide consistent quality, offer technical support, and have a broad range of LSR grades. Establishing a good relationship with your supplier can lead to better material recommendations and troubleshooting assistance.
What types of testing are essential before full-scale production in an LSR project?
Essential tests include rheological testing to understand flow characteristics, mechanical testing to assess properties like tensile strength and elongation, and environmental testing to ensure material performance under different conditions.
What are the key considerations in mold design for LSR projects?
Key considerations include understanding material properties, precision in mold design, effective ventilation, temperature control, gate and runner design, and ensuring durability and maintenance of the molds.
How can I optimize the injection molding process for LSR?
Optimizing the injection molding process involves understanding the injection molding cycle, controlling temperature and pressure precisely, minimizing cycle time, proper material handling and preparation, and utilizing advanced process control techniques.
What are the critical aspects of quality control in LSR projects?
Critical aspects include material testing, in-process monitoring, post-molding inspections, functional testing, documentation and traceability, and continuous improvement.
What are some common issues in LSR Injection Molding and their solutions?
Common issues include inconsistent viscosity, contamination, flash, incomplete filling, variations in cycle time, temperature fluctuations, dimensional inaccuracy, surface defects, machine downtime, and hydraulic leaks. Solutions involve thorough mixing, proper storage, improving venting, regular machine calibration, and implementing a regular maintenance schedule.
Why is regulatory compliance important in LSR projects?
Regulatory compliance is crucial for projects in regulated industries such as healthcare or food production. Ensuring that the selected LSR material complies with relevant standards and regulations, such as FDA or ISO certifications, is essential for the project’s success.
How does prototyping help in LSR mold design?
Prototyping allows for the identification and resolution of potential issues, ensuring that the final mold design is effective and efficient. Testing prototypes under actual production conditions provides valuable insights and helps in fine-tuning the mold design for optimal performance.