Cost of a Liquid Silicone Sample Mold: A Comprehensive Guide
The cost of a liquid silicone sample mold can vary significantly depending on several factors, including the complexity of the design, size, materials used, production method, and additional services required. Understanding these factors can help you plan your budget effectively and make informed decisions when venturing into silicone molding. Below, we explore the nuances of liquid silicone sample mold pricing in detail.
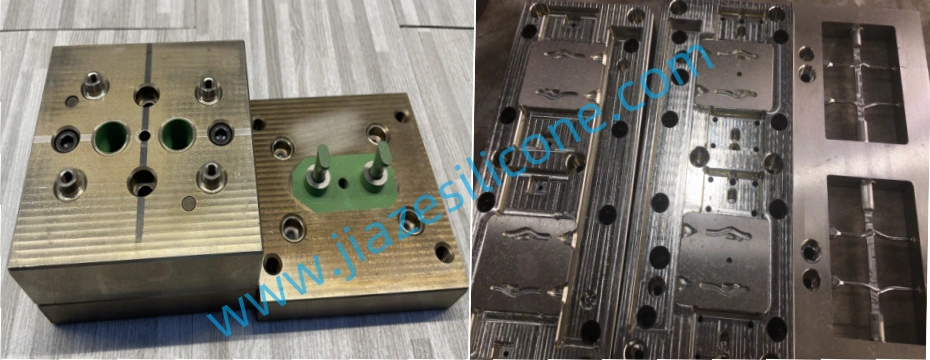
1. Overview of Liquid Silicone Molding
Liquid silicone rubber (LSR) molding is a process used to create high-quality, durable, and flexible components for various industries, including healthcare, automotive, consumer goods, and electronics. A sample mold is typically a prototype tool used to produce a small batch of parts to test design, functionality, and material properties before moving to full-scale production.
2. Factors Affecting the Cost of a Sample Mold
a. Mold Design Complexity
The complexity of your mold design significantly impacts the cost. Simple molds with straightforward shapes and fewer features are less expensive, while intricate designs with tight tolerances, undercuts, or multi-part assemblies require more time and expertise to fabricate, raising the price.
- Simple molds: $500–$1,000
- Complex molds: $1,000–$3,000 or more
b. Mold Size and Material
The size of the mold determines the amount of material and machining required. Larger molds naturally cost more due to the increased material volume and extended production time. The materials used to construct the mold also play a role, with common choices including:
- Aluminum molds: Lightweight and cost-effective, ideal for prototyping.
- Steel molds: Durable and long-lasting but more expensive, often used for high-volume production.
Prices range from:
- Small molds: $5,00–$1,000
- Large molds: $2,000 or more
c. Number of Cavities
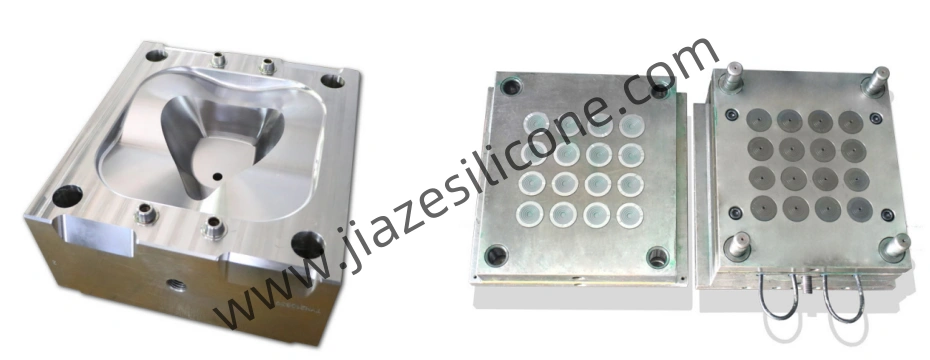
A mold can have one or multiple cavities depending on production needs. Single-cavity molds are less expensive and sufficient for sample molds, while multi-cavity molds increase cost but improve production efficiency for large-scale runs.
- Single-cavity mold: $3,00–$1,000
- Multi-cavity mold: $1,000–$3,000
d. Type of Mold
There are different types of molds depending on the desired features and part requirements:
- Compression molds: Lower cost but less precise; used for simpler parts.
- Injection molds: Higher cost but offer superior precision and consistency.
Injection molds for LSR are typically more expensive due to the precision and automation required for the process.
e. Prototyping vs. Production Tools
Sample molds are often designed as prototype tools and are generally less durable than production molds. These are typically made from less expensive materials and involve simpler construction.
- Prototype molds: $500–$3,000
- Production-ready molds: $3,000–$5,000
f. Production Quantity
Although a sample mold is usually intended for small batches, the expected production volume can influence its design and cost. If your sample mold must replicate production conditions, additional features (e.g., cooling channels, precision alignment) may be required, increasing the cost.
3. Hidden Costs and Additional Factors
a. Design and Engineering Services
Designing a liquid silicone mold requires CAD modeling, simulations, and engineering expertise. These services are often charged separately. Expect to pay:
- Basic design services: $500–$2,000
- Advanced simulations and revisions: $3,000–$5,000
b. Testing and Validation
Before a mold is finalized, manufacturers may conduct tests and validations to ensure it meets design and performance criteria. These processes might incur extra fees.
c. Lead Time and Urgency
Standard mold-making can take weeks to months, but expedited services are available for a premium.
- Standard lead time: No additional cost
- Rush orders: Add 20%–50% to the cost
d. Post-processing and Finishing
Sample molds may require surface treatments, texturing, or polishing to achieve the desired part quality. Post-processing fees can range from $200 to $2,000 depending on the complexity.
e. Manufacturer Location
The geographical location of your mold manufacturer can influence the cost. For instance, molds made in regions with lower labor costs, such as China or India, are often more affordable than those produced in the United States or Europe. However, logistical costs and potential communication challenges may offset these savings.
4. Industry-Specific Costs
Some industries, such as medical or food-grade applications, demand higher-quality molds made from certified materials and processes. These molds may require stricter tolerances, cleanroom manufacturing, and FDA-compliant materials, leading to higher costs.
- Standard molds: $1,000–$10,000
- Medical-grade molds: $10,000–$50,000
5. Typical Cost Breakdown
Below is a general breakdown of costs for a liquid silicone sample mold:
Item | Cost Range |
---|---|
Mold materials (aluminum, steel) | $500–$10,000 |
Design and engineering | $500–$10,000 |
Prototyping and testing | $200–$5,000 |
Post-processing | $200–$2,000 |
Total Estimated Cost | $1,500–$20,000+ |
6. Ways to Optimize Costs
a. Simplify the Design
Reducing the complexity of your part can lower mold costs. Avoid unnecessary features or intricate details unless they are essential.
b. Use Standardized Features
Incorporating standard mold components (e.g., guides, ejectors) instead of custom features can save on fabrication costs.
c. Choose the Right Manufacturer
Work with a manufacturer experienced in liquid silicone molding. They can often recommend cost-saving measures without compromising quality.
d. Plan Ahead
Avoid rush fees by starting your project early and allowing sufficient lead time for mold production.
e. Explore Outsourcing
If budget constraints are significant, consider outsourcing to manufacturers in cost-competitive regions.
Conclusion
The cost of a liquid silicone sample mold depends on numerous variables, from the complexity of the design to the type of material used. While simple molds for basic prototypes may cost as little as $500, more intricate designs and advanced manufacturing processes can drive the price to $20,000 or more. Understanding your specific needs and exploring cost-saving strategies can help ensure you get a high-quality mold within your budget.
Whether you are designing for medical applications, consumer products, or industrial components, investing in a well-made sample mold is crucial for validating your product and ensuring successful mass production.