Liquid Silicone Rubber (LSR) molding is a widely used process for manufacturing silicone components, especially in medical, automotive, and consumer product industries. Among the critical parameters that influence the molding process, the lsr Shore hardness of the material plays a significant role, particularly in determining the cycle time. Shore hardness, a measure of the material’s resistance to indentation, directly affects molding dynamics, curing behavior, and post-mold processing. Understanding the relationship between material Shore hardness and cycle time is crucial for optimizing production efficiency, product quality, and cost.
Understanding Shore Hardness in LSR
Shore hardness is expressed on a scale (typically Shore A ), with lower values indicating softer materials and higher values denoting harder ones. LSR compounds are available in a wide range of Shore hardness values, from ultra-soft grades (0 Shore A) to very hard formulations (70 Shore A or higher). The hardness is determined by the crosslink density of the silicone network, which influences its flow characteristics, curing behavior, and final mechanical properties.
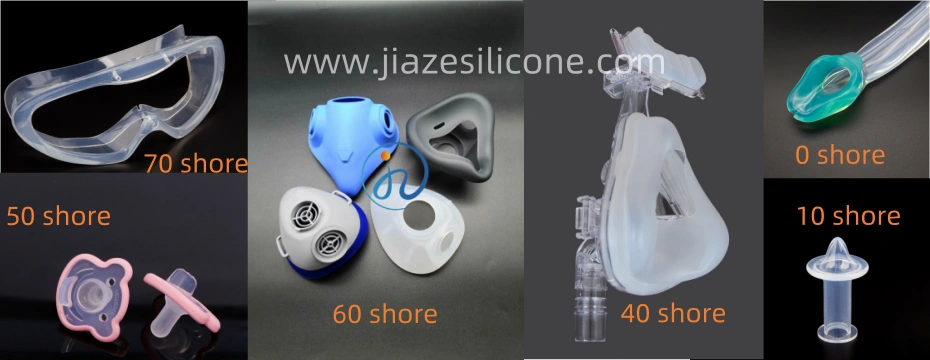
Impact of Shore Hardness on LSR Molding Cycle Time
Cycle time in LSR molding is the total duration required to complete one molding cycle, including the phases of material injection, curing, and demolding. Shore hardness impacts each of these phases as follows:
1. Material Flow and Injection Time
Shore hardness affects the viscosity of the uncured LSR. Softer grades (lower Shore A) generally have lower viscosity compared to harder grades. This difference in viscosity influences the material’s flow behavior during the injection phase:
- Softer LSR (Low Shore A):
- Lower viscosity enhances flowability, allowing the material to fill complex mold geometries more quickly.
- Reduced injection pressures are required, potentially shortening the injection time.
- Harder LSR (High Shore A):
- Higher viscosity slows down the flow, especially in intricate molds with thin walls or small cavities.
- Increased injection pressure and time may be necessary to ensure complete cavity filling.
While Shore hardness affects injection time, this phase is typically a minor contributor to overall cycle time compared to curing.
2. Curing Behavior and Cure Time
The curing process, where the LSR transitions from a liquid to a solid, is the most time-intensive phase in the cycle. Shore hardness significantly influences curing because it is related to the chemical formulation of the LSR:
- Softer LSR:
- Requires fewer crosslinking reactions due to lower crosslink density.
- Typically cures faster, reducing the required dwell time in the mold.
- Harder LSR:
- Requires a higher degree of crosslinking to achieve the desired hardness.
- Slower curing reactions result in longer mold dwell times.
However, curing time also depends on the mold temperature, catalyst concentration, and part thickness. Harder materials often require higher mold temperatures or optimized catalysts to accelerate curing, mitigating the impact on cycle time.
3. Demolding Characteristics
Shore hardness directly affects the ease of demolding:
- Softer LSR:
- Higher flexibility makes it easier to de-mold parts, especially those with undercuts or intricate designs.
- Reduced risk of tearing or deformation during demolding allows for quicker part removal.
- Harder LSR:
- Increased stiffness and reduced elasticity can make demolding more challenging.
- Additional time may be needed to release the part, particularly in complex mold designs or where automation is used.
Demolding aids, such as mold coatings or release agents, can help reduce cycle time for harder materials.
4. Thermal Conductivity and Mold Temperature
Shore hardness can also influence thermal conductivity and heat transfer during the molding process. Harder LSR grades may have slightly different thermal properties, affecting how heat is distributed during curing:
- Softer materials often heat and cure more uniformly, which can reduce cycle time.
- Harder materials might exhibit slower heat absorption, requiring longer dwell times to ensure full curing.
Optimal mold design and temperature control are essential to counteract these differences and maintain consistent cycle times.
Optimizing Cycle Time for Various Shore Hardnesses
Despite the inherent differences, manufacturers can take several steps to optimize cycle times for both soft and hard LSR materials:
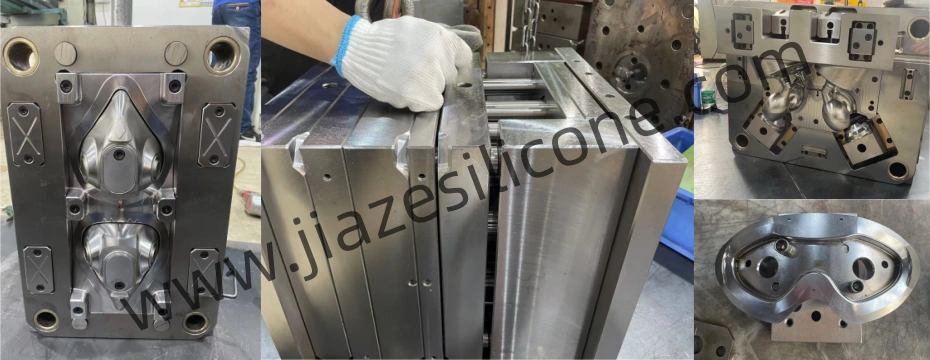
1. Mold Design Optimization
- Incorporate features like uniform wall thickness, streamlined flow paths, and venting to accommodate the flow characteristics of different hardnesses.
- Use ejector pins or automated demolding systems to speed up part removal for harder grades.
2. Temperature Control
- Implement precise mold temperature control to accelerate curing while maintaining product quality.
- For harder grades, increase mold temperature within safe limits to shorten curing time.
3. Catalyst Formulation
- Use optimized catalyst concentrations to adjust the curing rate for materials of varying Shore hardness.
- Consider fast-curing formulations for harder grades to balance curing time.
4. Injection Parameters
- Fine-tune injection speed and pressure based on material viscosity to minimize injection time without compromising cavity filling.
5. Automation and Demolding Aids
- Automate demolding to reduce variability and speed up the process, especially for harder materials.
- Apply mold coatings or release agents to facilitate demolding for stiff components.
Challenges and Considerations
While softer LSRs offer faster cycle times, they may lack the mechanical strength required for certain applications. Conversely, harder LSRs provide durability but require longer cycles. Balancing these trade-offs is essential:
- Application Requirements: Choose Shore hardness based on the mechanical and functional needs of the final product.
- Cycle Time vs. Quality: Shortening cycle time should not compromise the quality, such as dimensional accuracy or surface finish.
- Material Costs: Faster cycles for softer materials may reduce production costs, but higher material costs for premium formulations could offset these savings.
Conclusion
The Shore hardness of LSR has a profound impact on the cycle time of the molding process, influencing injection, curing, and demolding phases. Softer materials generally enable faster cycles due to better flowability and shorter curing times, while harder grades often demand longer cycles to accommodate their higher crosslink density and rigidity. By understanding and optimizing the interplay between Shore hardness and process parameters, manufacturers can achieve efficient production without sacrificing quality. Strategic adjustments in mold design, curing conditions, and material selection are essential for tailoring the cycle time to specific production goals.