Creating a liquid silicone injection mold is a multi-step process that typically takes between 4 to 12 weeks, depending on factors such as the mold’s complexity, the manufacturer’s workflow, and the resources available. Here’s a detailed breakdown of the process and factors affecting the timeline.
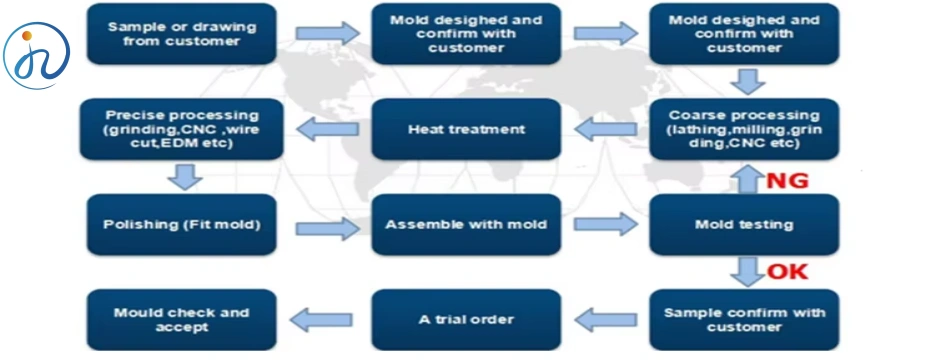
1. Designing the Silicone Injection Mold (1-2 weeks)
The first step in making a liquid silicone injection mold is designing the mold according to the part specifications. Engineers work with CAD (Computer-Aided Design) software to create a 3D model of the desired part, which helps in planning the mold’s cavities, cooling channels, and ejection systems. This phase involves close collaboration with the client, who may request modifications or revisions to the design.
This phase may take:
- 1-2 weeks for standard designs with little complexity.
- 2+ weeks if the design has intricate details or if multiple revisions are needed.
2. Material Selection and Mold Structure Analysis (1 week)
Once the design is finalized, engineers select the materials for the mold, typically high-quality metals like steel or aluminum, chosen based on the production requirements. Steel, for example, is often chosen for high-volume production due to its durability, while aluminum might be selected for lower production volumes or prototyping.
Material analysis includes checking the structural integrity, hardness, and temperature resistance of the chosen material to ensure it can withstand the pressures and temperatures of liquid silicone injection molding. This phase ensures that the mold is capable of producing high-quality parts consistently.
3. Silicone Injection Mold Flow Analysis (1-2 weeks)
A mold flow analysis, using specialized simulation software, evaluates how the liquid silicone will flow within the mold, helping to identify and eliminate potential issues such as air traps, weld lines, and warping. The analysis can reveal areas where silicone might cool too quickly or unevenly, which could lead to defects.
Depending on the complexity of the part, this phase may take 1 to 2 weeks. For very intricate molds or those with complex geometries, this step may take additional time due to the need for iterative testing and adjustments.
4. CNC Machining and Mold Creation (3-8 weeks)

With the design, material, and flow analysis completed, the mold is then created using CNC (Computer Numerical Control) machining. CNC machines precisely cut and shape the metal to form the mold’s cavities and other essential features. This is typically the most time-consuming part of the process, as even a minor mistake can require re-machining.
This phase may take:
- 3-4 weeks for relatively simple designs with fewer details.
- 6-8 weeks for complex or multi-part molds that require high precision.
Factors affecting this timeframe include:
- Machining complexity: High-precision molds with intricate details require more time.
- Machine availability: CNC machines are in high demand, so machine availability can impact production speed.
- Tool wear: As tools wear down, replacements or recalibration can add time.
5. Polishing and Surface Finishing (1-2 weeks)
Once the basic structure of the mold is complete, it undergoes polishing and finishing. The purpose of this phase is to ensure that the mold surface is smooth, which is essential for producing defect-free silicone parts. Surface finishing might include sanding, polishing, or adding specific textures if required by the design.
For standard molds, this phase may take 1 week. If a specific surface finish or texture is required, it may extend to 2 weeks or more, depending on the detail and precision required.
6. Assembly and Fitting Of Silicone Injection Mold (1 week)
The mold is now ready for assembly, where various parts, including ejector pins, cooling channels, and other components, are put together. Each piece is carefully fitted to ensure the mold operates smoothly. This phase involves precision work to guarantee that all components align correctly, preventing issues in the production phase.
7. Testing and Iteration (1-2 weeks)
Before the mold is considered production-ready, it undergoes testing through trial runs to ensure that it functions as expected. This process identifies any last-minute issues that could affect the quality of the final parts. Testing often involves injecting liquid silicone and examining the output for defects like flash, shrinkage, or warping.
This phase can take 1 to 2 weeks, depending on the complexity of the mold.
8. Approval and Final Adjustments (1 week)
After testing, the client usually reviews the test parts and the mold’s performance. If the mold meets all specifications, it is approved for production. However, if adjustments are required, they are made before final approval.
This phase typically takes 1 week. Delays can occur if the client requests additional modifications or if significant alterations to the mold design are needed.
Key Factors Affecting Overall Timeline
- Complexity of the Design: More complex molds, especially those with intricate shapes or fine details, require longer machining and polishing times.
- Material Choice: Steel molds for high-volume production are more durable but take longer to machine compared to aluminum molds.
- Number of Cavities: Multi-cavity molds, which allow for the simultaneous production of multiple parts, are more complicated and take longer to make.
- Availability of CNC Machines: Depending on the manufacturer’s workload, machine availability can impact the timeline.
- Quality Control Standards: High-quality standards may add extra steps to ensure the mold meets strict requirements.
Summary
Here’s a breakdown of each phase and its approximate time requirement:
Phase | Approximate Duration |
---|---|
Design | 1-2 weeks |
Material Selection & Analysis | 1 week |
Mold Flow Analysis | 1-2 weeks |
CNC Machining | 3-8 weeks |
Polishing & Finishing | 1-2 weeks |
Assembly & Fitting | 1 week |
Testing & Iteration | 1-2 weeks |
Approval & Final Adjustments | 1 week |
Total Duration | 4-12 weeks |
Conclusion
Creating a liquid silicone injection mold is a detailed and meticulous process that takes anywhere from 4 to 12 weeks. The timeline varies widely depending on the design’s complexity, required precision, and the production volume anticipated. For high-quality results, each phase must be carefully executed, from initial design to final testing, making patience and precision key factors in successful mold manufacturing.