Liquid Silicone Rubber (LSR) is a versatile material widely used in medical devices, automotive, electronics, and consumer goods due to its flexibility, durability, and resistance to extreme temperatures and chemicals. Designing Liquid Silicone Rubber molds requires careful consideration of its unique properties and the injection molding process. Here are the seven essentials in LSR mold design:
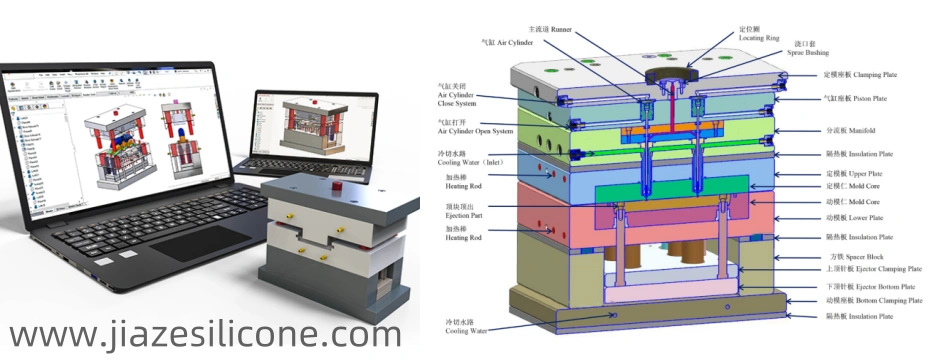
1. Material Flow Behavior and Cavity Design
LSR behaves differently from thermoplastics due to its low viscosity and high flowability. These properties allow LSR to fill intricate geometries making it prone to flash (unintended material seepage). Cavity design should:
- Ensure uniform wall thickness to promote even material flow and minimize internal stresses.
- Incorporate rounded edges instead of sharp corners to avoid flow hesitation and material defects.
- Include venting at strategic points to allow air to escape, reducing trapped air and voids in the final product.
2. Temperature Control System
LSR molds require precise temperature management since the material is cured through heat. Key considerations include:
- Heated molds: LSR cures rapidly at elevated temperatures (typically 160°C to 200°C). Incorporate efficient heating elements, such as cartridges or oil heaters, to maintain consistent mold temperatures.
- Thermal insulation: Prevent heat loss by using thermal barriers or insulation plates between the mold and the machine platen.
- Cooling zones: Although LSR molds are generally heated, specific zones may require cooling to manage thermal gradients and avoid material degradation.
3. Proper Gating and Runner Systems
The gating system in an LSR mold is critical to ensure smooth, defect-free filling. Consider the following:
- Direct gating: LSR molds often use cold runners combined with direct gating to reduce waste and optimize material usage. Cold runner systems maintain LSR in its uncured state until it enters the heated cavity.
- Gate location: Place gates at thick sections of the part to promote efficient material flow. Avoid gating into thin areas to prevent premature curing or flow restrictions.
- Gate design: Utilize valve gates or small pin gates to ensure clean separation and reduce post-molding trimming.
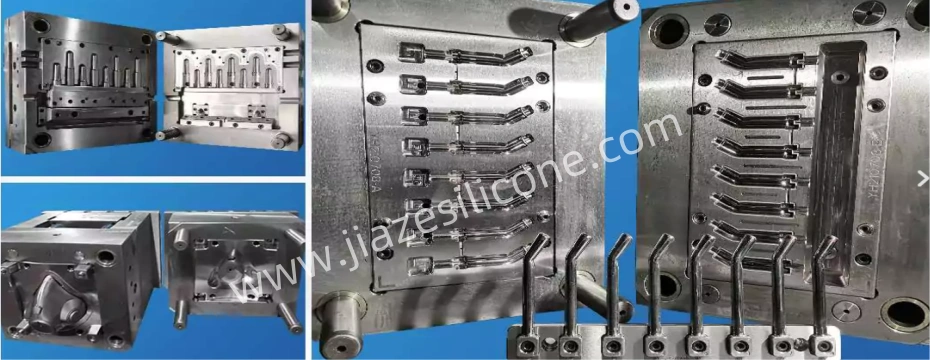
4. Parting Line and Flash Control
Flash is a common challenge in LSR molding due to the material’s flowability and low viscosity. To address this:
- Tight tolerances: Maintain extremely tight tolerances (±0.02 mm or better) at the parting line to prevent material leakage.
- Compression force: Ensure sufficient clamping force to keep the mold halves tightly closed during injection.
- Seal design: Incorporate interlocking features, such as O-ring grooves or stepped parting lines, to further minimize flash.
5. Ejection System and Part Removal
Ejecting LSR parts can be tricky due to their flexibility and potential adhesion to the mold. Effective ejection systems include:
- Air ejection: Using compressed air gently releases parts from the mold without causing damage.
- Stripping plates: Employ stripping mechanisms to peel the part away from the mold cavity.
- Surface finishes: Use polished or textured mold surfaces to reduce adhesion and simplify part removal.
6. Mold Material Selection
The choice of mold material is crucial to withstand the high temperatures and pressures associated with LSR molding. Key considerations are:
- High-strength steels: Materials like S136 tool steels are commonly used for their durability, wear resistance, and thermal expansion resistance.
- Corrosion resistance: Choose materials resistant to chemical attack from the silicone and cleaning agents.
- Coatings: Apply surface coatings like chrome or nickel to enhance wear resistance and reduce sticking.
7. Automation and Production Efficiency
Automation is often essential in LSR molding to achieve high precision and repeatability. Key elements of automation include:
- Robotic handling: Automating part removal and inspection reduces cycle time and labor costs.
- Integrated systems: Incorporate sprue pickers, vision systems, and automated trimming to streamline production.
- Mold design for automation: Ensure mold components, such as ejectors and gates, are compatible with automated processes.
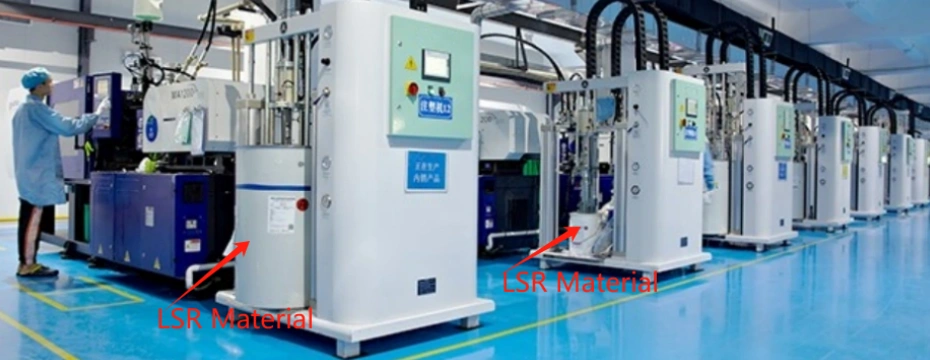
Conclusion
Designing molds for Liquid Silicone Rubber requires an in-depth understanding of the material’s behavior and the molding process. Focusing on flow behavior, temperature control, gating, flash prevention, ejection, material selection, and automation ensures efficient production and high-quality parts. By adhering to these seven essentials, mold designers can optimize their processes and unlock the full potential of LSR in various applications.