Liquid Silicone Rubber (LSR) injection molding project is a specialized process that offers precision, consistency, and efficiency for manufacturing high-quality rubber components. Due to its unique properties and technical demands, ensuring the success of an LSR injection molding project requires meticulous planning, in-depth technical understanding, and effective collaboration across multiple stages. This guide outlines key steps and considerations to achieve a successful outcome for your LSR injection molding project.
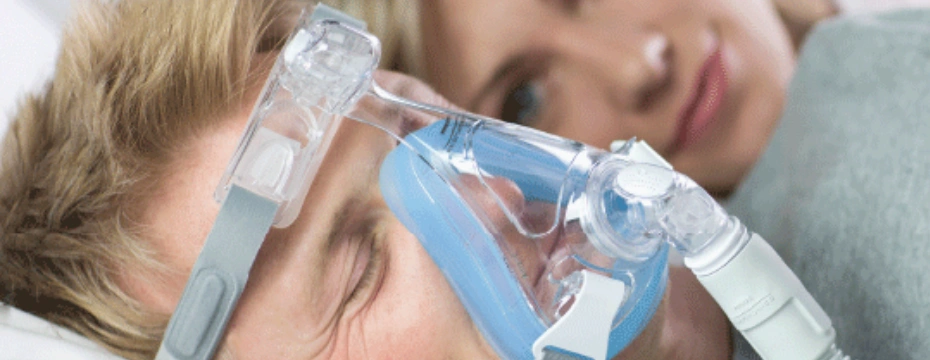
1. Define Project Objectives Clearly
A successful LSR injection molding project begins with a clear understanding of the project goals. Define your objectives, including:
- Product Specifications: Detail dimensional tolerances, material properties, and functional requirements.
- Volume Expectations: Determine production quantities, whether low-volume prototypes or high-volume manufacturing runs.
- Budget and Timelines: Establish cost constraints and delivery schedules to guide project planning.
Clear objectives set the foundation for effective decision-making throughout the process.
2. Select the Right LSR Material
Material selection is critical for meeting performance and regulatory requirements. Consider factors such as:
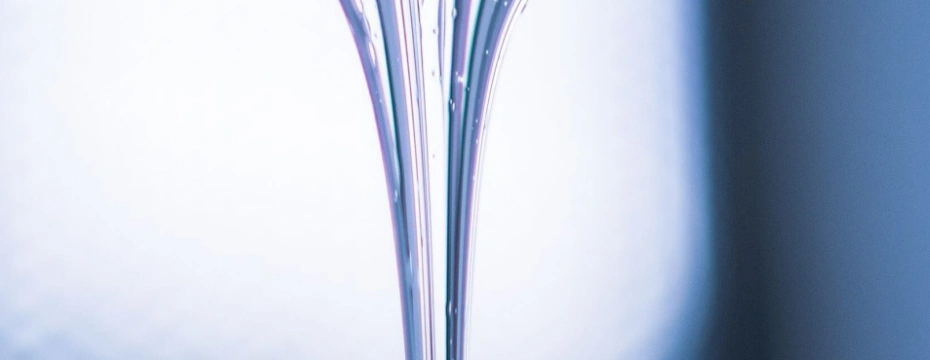
- Mechanical Properties: LSR offers flexibility, tensile strength, and durability. Choose a grade that aligns with the product’s intended use.
- Chemical Resistance: Evaluate the material’s resistance to oils, chemicals, and extreme temperatures.
- Compliance Standards: Ensure compliance with industry standards like FDA, ISO, or RoHS for medical, food-grade, or industrial applications.
- Color Options: If aesthetics matter, consider color consistency and pigmentation compatibility.
Work with your supplier or technical team to select the appropriate LSR grade for the application.
3. Collaborate on Optimized Design for Manufacturability (DFM)
Engage engineers and designers early to refine the product design for manufacturability. Key considerations include:
- Wall Thickness: Ensure uniform wall thickness to reduce defects like warping or sink marks.
- Draft Angles: Include appropriate draft angles to facilitate part ejection and avoid damage.
- Undercuts and Complex Features: Minimize complex geometries that may increase mold costs or complicate production.
- Gating and Venting: Optimize gate placement and venting to ensure smooth material flow and eliminate air entrapment.
DFM efforts minimize production challenges and reduce costs.
4. Choose the Right Equipment
The success of an LSR injection molding project depends significantly on the equipment used. Consider the following:
- Injection Molding Machine: Use specialized LSR injection molding machines with features like cold-runner systems and precise temperature controls.
- Mold Design: Invest in high-quality molds with robust thermal regulation systems and durable materials.
- Automation Integration: Incorporate automated systems for demolding, material feeding, and quality inspection to enhance efficiency and consistency.
Ensure that equipment capabilities align with project requirements and production volumes.
5. Develop a Comprehensive Process Plan
Establish a robust manufacturing process that incorporates:
- Temperature Control: Maintain precise control over barrel and mold temperatures to ensure optimal curing.
- Cycle Time Optimization: Balance productivity and quality by fine-tuning cycle times.
- Injection Pressure Settings: Adjust injection pressures to ensure consistent filling and prevent defects.
- Post-Curing Requirements: If necessary, plan for post-curing processes to enhance mechanical properties or meet compliance standards.
Conduct pilot runs to validate the process and fine-tune parameters.
6. Focus on Mold Quality and Maintenance
The mold is a critical asset in LSR injection molding. Ensure its quality and longevity through:
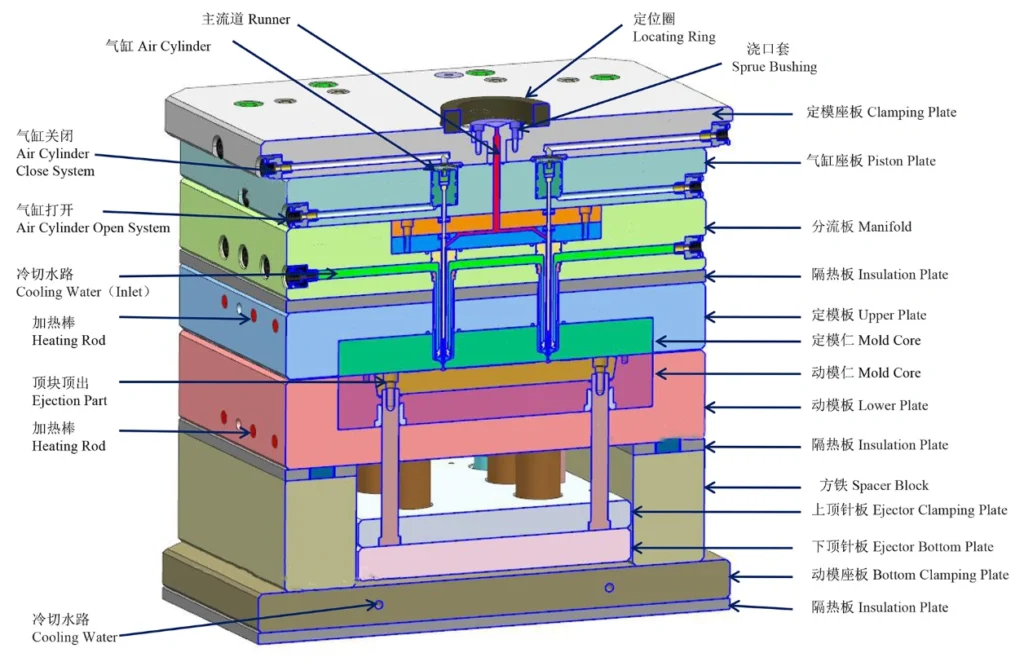
- Material Selection: Use high-grade steel or aluminum for mold construction to withstand LSR’s curing conditions.
- Precision Manufacturing: Work with experienced mold makers to ensure dimensional accuracy and surface finish.
- Regular Maintenance: Schedule routine inspections and maintenance to prevent wear and tear, ensuring consistent production quality.
Proper mold management reduces downtime and prolongs tool life.
7. Implement Rigorous Quality Control Measures
LSR injection molding requires stringent quality control to meet demanding specifications. Key practices include:
- Dimensional Inspections: Use precision measuring tools to verify part dimensions.
- Defect Analysis: Monitor for common issues like flash, short shots, or air entrapment, and address root causes promptly.
- Material Testing: Conduct tests on material properties, including hardness, tensile strength, and elongation, to ensure consistency.
- End-Use Validation: Perform functional tests to confirm that parts meet application requirements.
Leverage automated inspection systems for real-time quality monitoring.
8. Foster Collaboration Among Stakeholders
Effective communication and collaboration among all project stakeholders—designers, engineers, manufacturers, and suppliers—are essential for success. Regular updates, design reviews, and problem-solving sessions can help address challenges early and ensure alignment.
9. Plan for Scalability and Future Needs
Anticipate future demands by designing molds and processes with scalability in mind. Modular mold designs and adaptable equipment can accommodate future variations or higher production volumes without significant retooling costs.
10. Adhere to Regulatory and Safety Standards
Compliance with industry regulations and safety standards is vital, particularly in medical, automotive, and food-grade applications. Work closely with certification bodies to ensure that your products meet the necessary guidelines, avoiding costly delays or rejections.
11. Invest in Skilled Personnel and Training
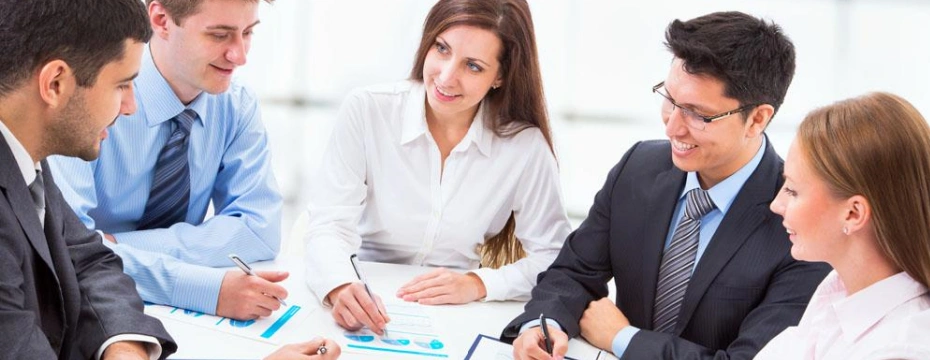
Ensure that your team is well-versed in LSR injection molding techniques. Invest in training programs for machine operators, quality inspectors, and maintenance staff to enhance efficiency and reduce errors.
12. Monitor and Improve Continuously
Post-production, gather data on cycle times, defect rates, and customer feedback. Use this information to identify areas for improvement and implement changes for future projects.
By adhering to these principles and focusing on strategic planning, material selection, design optimization, and process control, you can ensure the success of your LSR injection molding project, delivering high-quality products on time and within budget.