The medical devices industry continuously seeks materials that meet stringent safety standards while offering design flexibility, durability, and biocompatibility. Liquid Silicone Rubber (LSR) stands out as one of the most versatile materials used in this sector. Its unique properties make it ideal for creating intricate, patient-safe components that ensure high performance in both short-term and long-term medical applications. This detailed exploration delves into the characteristics of LSR, its benefits, common applications in medical devices, and the reasons for its widespread adoption.
Understanding Liquid Silicone Rubber (LSR)
Liquid Silicone Rubber (LSR) is a two-component, platinum-cured elastomer, widely utilized for injection molding. This elastomer consists of a base and a catalyst, which, when mixed, rapidly cures into a flexible and robust rubber. Its liquid nature allows for high precision during molding, making it suitable for producing complex and intricate parts required in the medical device industry. The use of platinum as a curing agent ensures that the final product is free from toxic residues, making it especially suitable for sensitive applications involving human health.
Key Properties of LSR
- Biocompatibility: One of the most critical aspects of LSR is its biocompatibility. LSR is non-toxic, hypoallergenic, and does not cause adverse reactions when in contact with human tissues. This makes it suitable for both short-term and long-term contact with the body, including applications that involve implantation. It complies with rigorous safety standards such as USP Class VI and ISO 10993, which evaluate materials for their safety in medical applications.
- Chemical Inertness: LSR is highly resistant to a wide range of chemicals, including bodily fluids, saline, and pharmaceuticals. This resistance ensures that the material does not degrade or react with substances it may encounter within the body or during sterilization processes. This property makes LSR ideal for components that need to maintain their integrity in environments with varying pH levels and exposure to drugs.
- Thermal Stability: LSR is known for its thermal stability across a broad temperature range, typically from -50°C to 250°C.
- Elasticity and Flexibility: LSR is inherently elastic and retains flexibility over time, even after repeated sterilization. This elasticity is particularly beneficial for products like catheters, tubing, and other applications where softness and comfort are crucial for patient interaction. Its flexibility also facilitates easy integration into devices that require precise and reliable performance.
Advantages of LSR in Medical Devices
- Ease of Sterilization: Sterilization is an essential requirement for most medical devices to prevent infection and ensure patient safety. LSR’s ability to withstand various sterilization methods—such as autoclaving, ethylene oxide (EtO), and gamma radiation—without losing its structural or mechanical properties makes it highly suitable for reusable medical devices. This capability is critical for maintaining product longevity and ensuring that devices meet health standards after multiple uses.
- Precision Molding and Design Flexibility: The liquid form of LSR makes it ideal for injection molding, allowing manufacturers to create complex geometries with tight tolerances. This enables the production of intricate medical device components, such as seals, gaskets, and valves, where precision is paramount. The injection molding process also reduces the need for secondary operations, streamlining production and lowering costs while ensuring consistency across high-volume manufacturing runs.
- Reduced Risk of Contamination: LSR has a low surface energy, which minimizes the risk of contaminants adhering to its surface. This characteristic is vital for devices that require cleanliness, such as syringe components, implantable devices, or respiratory masks. The smooth surface of LSR components further aids in maintaining a sterile environment, reducing the risk of bacterial growth and contamination during medical procedures.
- Durability and Long-term Performance: The chemical stability and physical resilience of LSR contribute to its durability and long-term performance. LSR does not degrade over time, even when exposed to environmental stresses like UV light, ozone, or mechanical strain. This longevity makes it particularly valuable in medical applications that demand consistent performance, such as wearable health monitoring devices or implantable components.
Applications of LSR in Medical Devices
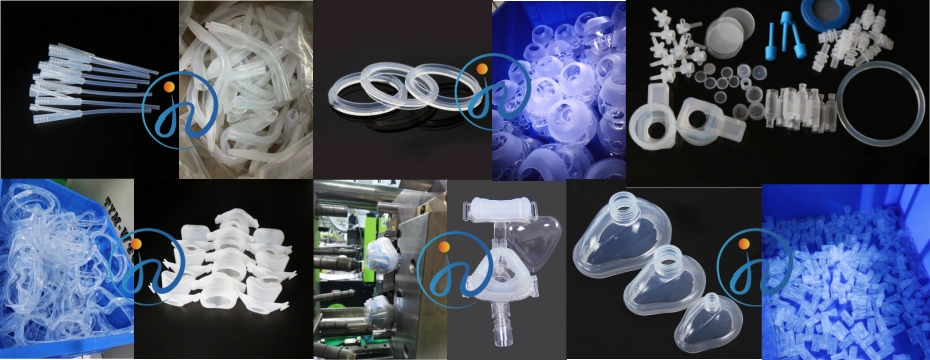
- Catheters and Tubing: LSR’s flexibility, smooth surface, and biocompatibility make it an ideal material for manufacturing catheters, which are inserted into the body for fluid drainage or medication delivery. The smooth surface reduces the risk of tissue irritation, while its flexibility ensures patient comfort. Additionally, LSR tubing is used in various fluid management systems due to its ability to withstand repeated sterilization and resistance to kinking.
- Implantable Devices: LSR is commonly used in components of implantable medical devices, such as pacemakers, defibrillators, and neurostimulators. Its biocompatibility and non-reactive nature ensure that it does not interfere with the body’s functions. Furthermore, LSR can be used as an encapsulating material to protect sensitive electronic components from bodily fluids, ensuring the longevity and reliability of such implants.
- Respiratory and Anesthetic Masks: LSR is widely employed in manufacturing respiratory masks, oxygen masks, and anesthetic masks due to its softness and comfort. Patients can wear these masks for extended periods without discomfort, reducing the risk of skin irritation. The elasticity of LSR ensures a snug, airtight fit, which is essential for maintaining proper function in breathing assistance devices.
- Seals and Gaskets: LSR’s ability to form tight seals makes it an excellent choice for gaskets, seals, and valves in medical devices such as insulin pumps, IV connectors, and syringes. The precision molding process allows for the creation of small and complex components that prevent leaks, ensuring the safe and effective delivery of fluids and medications.
- Wearable Medical Devices: The rise of wearable health technology, such as continuous glucose monitors and heart rate sensors, has also benefited from LSR. Its lightweight nature, flexibility, and skin-friendly properties make it ideal for components that must remain in contact with the skin for extended periods. LSR’s resistance to environmental factors like moisture and sweat ensures that these devices remain functional and comfortable.
The Future of LSR in Medical Devices
As medical devices become more advanced and personalized, the demand for materials that can meet rigorous safety and performance standards continues to grow. LSR’s versatility and adaptability make it a frontrunner in this evolving field. Innovations in 3D printing with LSR, for example, are opening up new possibilities for custom medical device components tailored to individual patient needs.
The medical device sector also places a strong emphasis on minimizing environmental impact, and LSR contributes positively in this regard. The long lifespan and reusability of LSR components can reduce waste, and ongoing research into more sustainable production processes continues to enhance its appeal.
Conclusion
Liquid Silicone Rubber (LSR) has become a cornerstone material in the medical device industry. It provides a combination of biocompatibility, chemical stability, flexibility, and precision moldability that few other materials can match. Its ability to be sterilized and molded into complex shapes ensures that medical devices meet the highest standards of safety and functionality. As technology advances, LSR’s role in creating safer, more effective, and patient-friendly medical devices is only expected to expand, making it an invaluable resource for medical device manufacturers striving for innovation and excellence.