LSR Two-shot injection molding is an advanced manufacturing technique that allows for the production of intricate plastic parts by combining two different materials into a single mold during the same production cycle. This process offers a range of advantages in terms of product functionality, design flexibility, and efficiency, making it a popular choice in various industries, including automotive, consumer electronics, medical devices, and more. This technique involves injecting two different polymers or materials in sequence into a mold, creating parts with varied properties or colors without the need for additional assembly steps.
Overview of the LSR Two-Shot Injection Molding Process
In traditional injection molding, a single material is melted and injected into a mold cavity, where it solidifies to form a part. In contrast, the two-shot injection molding process uses a specialized machine equipped with two barrels (or injectors) that can handle two different materials. The process involves the following steps:
- First Injection: The first material (often a rigid plastic or substrate) is injected into a specific section of the mold. It forms the base or initial layer of the final product. The mold is then rotated or shifted to a second position, while the initial material solidifies in the mold.
- Second Injection: Once the first material is partially or fully set, the second material (which might be a softer polymer, elastomer, or material with different characteristics) is injected into a different cavity of the same mold, over-molding onto or bonding with the initial substrate.
- Cooling and Ejection: After the second material is injected and fills the required spaces, the mold cools to allow the part to solidify completely. The finished part is then ejected from the mold.
This sequence of injections results in a single part composed of two materials with different properties, such as hardness, flexibility, or color. The process is fully automated, meaning it can produce complex multi-material parts efficiently and with high repeatability.
Key Advantages of Two-Shot Injection Molding
The two-shot injection molding process offers a range of advantages over traditional single-material molding or other assembly processes:
- Enhanced Design Flexibility: The ability to integrate two different materials into a single molded part allows for creative designs and product enhancements. For example, it is possible to create parts with different colors, textures, or hardness levels. This can be used to improve both the aesthetic appeal and functionality of the product.
- Improved Product Functionality: Two-shot molding enables the creation of parts that have built-in functions. Such as soft-touch grips, sealing components, or over-molded features like buttons and gaskets. This is particularly useful in products where different parts need to have specific characteristics. Such as a rigid base with a soft, ergonomic outer layer.
- Elimination of Secondary Assembly: Traditional methods often require the separate molding of parts followed by manual or automated assembly. Two-shot injection molding combines two materials directly in the mold, reducing the need for secondary operations like bonding or assembly. This streamlines the manufacturing process, reduces labor costs, and minimizes the chances of assembly-related defects.
- Enhanced Bond Strength: The two materials used in two-shot molding are bonded together during the molding process. This enhances the durability and longevity of the final product.
- Cost-Effectiveness and Efficiency: The initial setup costs for two-shot injection molding are higher. The overall production cost can be lower for high-volume runs. The elimination of additional assembly steps, reduced material waste, and lower labor costs contribute to long-term savings.
Materials Used in LSR Two-Shot Injection Molding
Two-shot injection molding can use a variety of thermoplastic and elastomeric materials, allowing for a broad range of material combinations. Selecting the right materials is critical for ensuring proper bonding and achieving the desired properties in the final part. Common materials include:
- Rigid Thermoplastics: Materials like ABS, PC, PP, and nylon are often used as the substrate in the first injection. These materials provide structural integrity and rigidity to the molded part.
- Elastomers and Thermoplastic Elastomers (TPEs): The second injection often involves softer materials. Like TPEs, silicone, or rubber-like compounds that add flexibility, shock absorption, or a soft-touch feel to the product.
- Polycarbonate/ABS Blends: These materials are often used in electronics and automotive applications due to their toughness and impact resistance. They are frequently combined with TPEs for parts that need both rigidity and a cushioned surface.
- Polyethylene (PE) and Polypropylene (PP): These materials are lightweight and resistant to chemicals. It makes them suitable for packaging, containers, and consumer products.
Applications of LSR Two-Shot Injection Molding
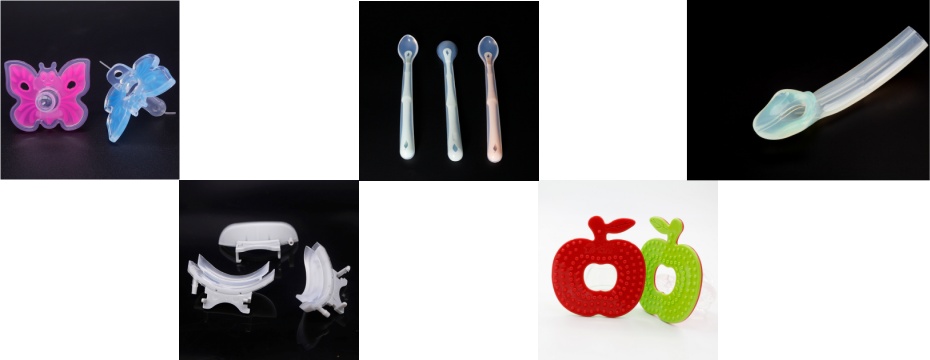
Two-shot injection molding finds applications across various industries where multi-material parts are required. Some common applications include:
- Automotive Components: The automotive industry benefits significantly from two-shot molding for manufacturing parts like knobs, switches, seals, and buttons that require a combination of durability and a tactile feel. For example, car interior components often feature a rigid base with a soft-touch overlay for enhanced user comfort.
- Consumer Electronics: Many electronic devices use two-shot injection molding for components like phone cases, wearable device housings, and remote controls. These products often combine a rigid inner structure with a softer outer shell for improved grip and user experience.
- Medical Devices: Two-shot molding is crucial for creating medical devices that need biocompatible materials with differing hardness or flexibility. For example, surgical handles or tubing connectors may use a rigid plastic base combined with a soft, ergonomic grip made from medical-grade TPE.
- Packaging and Consumer Products: In packaging, two-shot molding allows for the creation of products with built-in seals or grips, such as bottle caps with a rubberized seal to ensure leak-proof functionality. In consumer products, it’s used for items like toothbrushes, kitchen utensils, and personal care products, where comfort and ergonomics are important.
- Power Tools and Industrial Equipment: For tools and equipment that require robust, long-lasting parts, two-shot injection molding is ideal. It allows for the creation of tools with a hard, durable core and a non-slip, comfortable grip.
Challenges and Considerations in LSR Two-Shot Injection Molding
Despite its numerous benefits, the two-shot injection molding process also comes with certain challenges that need to be addressed:
- Tooling Complexity and Cost: Designing and manufacturing molds for two-shot injection molding is more complex than for traditional molding. The mold must accommodate two different materials and sometimes requires moving parts or rotating mechanisms. This complexity increases the cost of mold fabrication, making two-shot molding more suitable for high-volume production.
- Material Compatibility: Not all materials bond well in two-shot injection molding. The materials must be compatible to ensure a strong bond between the first and second shots. If the materials do not bond properly, the final part may delaminate or separate over time. It is essential to perform compatibility tests and consult material suppliers to ensure optimal bonding.
- Process Control: Two-shot molding requires precise control over temperature, pressure, and timing to ensure that each material is injected correctly and that the final part has the desired characteristics. Any variation in these parameters can lead to defects such as warping, poor bonding, or incomplete filling of the mold cavities.
- Cycle Time Management: The cycle time for two-shot molding can be longer than for single-shot processes due to the need for sequential injections and the possible rotation or movement of the mold. Proper cycle time management is necessary to maintain production efficiency.
Conclusion
LSR Two-shot injection molding is a highly effective manufacturing process that enables the creation of complex, multi-material parts with a single molding cycle. By injecting two materials into the same mold, manufacturers can achieve greater design flexibility, improved functionality, and cost savings through the elimination of secondary assembly steps. While the initial investment in specialized tooling and machines can be high, the long-term benefits, especially for large production runs, make it a preferred method in industries like automotive, consumer electronics, medical devices, and more.
The success of a two-shot injection molding project depends on careful material selection, mold design, and process control. When done correctly, this process results in durable, high-quality parts that meet stringent performance and aesthetic standards. As manufacturing continues to evolve, two-shot injection molding remains a key technology for producing innovative, multi-material components.