Liquid Silicone Rubber (LSR) is a versatile material that has gained widespread popularity due to its unique properties, ease of processing, and adaptability across various industries. This guide delves into the production process of LSR, explores its diverse applications, and highlights the benefits that make it an indispensable material in modern manufacturing.
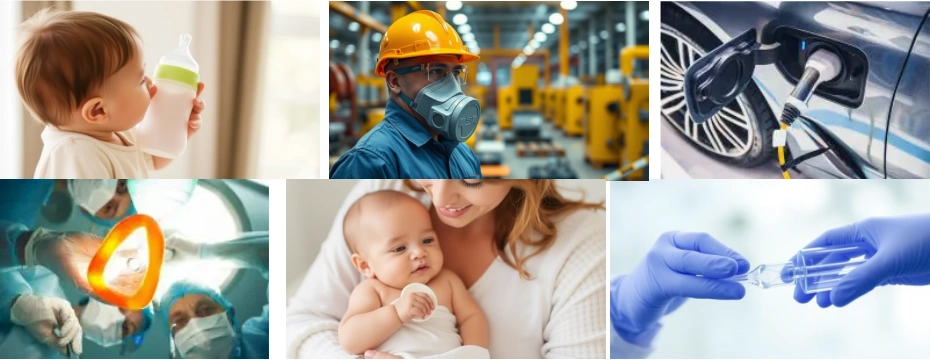
1. What Is LSR (Liquid Silicone Rubber)?
LSR is a high-purity, two-component, platinum-cured silicone that remains in a liquid state until it is cured into a solid form through a molding process. It is known for its exceptional durability, flexibility, and heat resistance. The platinum-cure mechanism allows LSR to cure rapidly when subjected to heat, making it ideal for manufacturing complex parts with precision.
Unlike traditional silicone rubbers that are solid or paste-like before molding, LSR’s low viscosity enables it to be processed using injection molding. This means LSR can be used to produce intricate designs, small parts, or components with tight tolerances, making it particularly advantageous in industries requiring detailed or high-volume production.
2. Production
The production process of Liquid Silicone Rubber involves a combination of advanced chemical formulation and precision molding. Here is an overview of how LSR is produced and processed:
a. Formulation
LSR is made by combining two liquid components: Part A, which contains the silicone polymer, and Part B, which includes the curing agent (usually platinum-based). These two components are mixed in a precise ratio, often 1:1, before being injected into molds.
The platinum-catalyzed curing process results in a cross-linked silicone elastomer, giving LSR its durable and flexible characteristics. Additives such as pigments, fillers, or stabilizers can be included in the mixture to achieve desired properties like color, flame retardancy, or improved strength.
b.Injection Molding Process
LSR is typically processed using injection molding, which involves the following steps:
- Metering and Mixing: The two components (Part A and Part B) are precisely metered and mixed to ensure consistent curing. This is done using an injection molding machine equipped with a metering pump.
- Injection into Mold: The mixed LSR is injected into a preheated mold cavity under pressure. The mold is designed to match the shape and specifications of the desired part.
- Curing: Once inside the mold, the LSR cures (solidifies) rapidly under heat (usually between 150°C and 200°C), forming a solid part. The curing time depends on the thickness and complexity of the part, typically ranging from a few seconds to a few minutes.
- Demolding and Post-Curing: After curing, the part is removed from the mold. Depending on the application, some parts may undergo additional post-curing processes to enhance their mechanical properties and stability.
The injection molding process allows for efficient, high-speed production of LSR components with minimal waste, making it ideal for manufacturing precision parts in large quantities.
3. Uses of LSR
LSR’s combination of flexibility, durability, and biocompatibility makes it suitable for a wide range of applications across various industries:
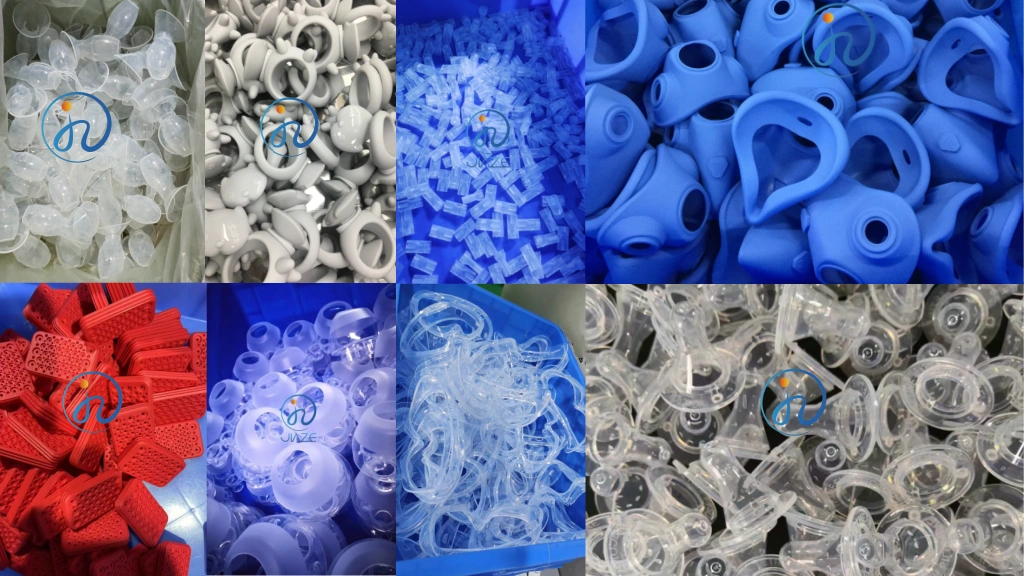
a. Medical and Healthcare Applications
LSR is widely used in the medical and healthcare sectors due to its biocompatibility, non-toxicity, and resistance to bacterial growth. Common applications include:
- Medical Devices: LSR is used to manufacture components for devices such as catheters, stoppers, and syringe seals.
- Implants: It is often used for long-term implants due to their inert nature and compatibility with body tissues.
- Wearable Devices: The flexibility and skin-safe nature of LSR make it suitable for wearable medical devices like fitness trackers and sensors.
- Infant Care Products: LSR is used to produce pacifiers, bottle nipples, and baby teething toys, as it is hypoallergenic and easy to sterilize.
Its resistance to high temperatures and ability to withstand sterilization processes like autoclaving and gamma radiation make LSR ideal for critical medical applications.
b. Automotive Industry
In the automotive sector, LSR is used to produce components that must endure extreme temperatures and vibrations, such as:
- Seals and Gaskets: LSR seals and gaskets maintain flexibility over a wide temperature range, ensuring reliable performance in engine compartments.
- Connectors and Insulators: LSR’s electrical insulation properties make it suitable for manufacturing connectors and cable insulators.
- Light Lenses and Gaskets: LSR is also used in headlight and taillight lenses and gaskets, offering transparency and weather resistance.
LSR’s durability and resistance to automotive fluids make it a reliable choice for under-the-hood components and other demanding environments.
c. Consumer Products
LSR has become popular in various consumer products due to its non-toxic nature and durability, including:
- Kitchenware: Heat-resistant and food-grade LSR is used for baking molds, spatulas, and ice cube trays.
- Wearables: It is used in smartwatches, sports bands, and other wearable electronics for its comfort and flexibility.
- Personal Care Items: Products like toothbrushes, earplugs, and cosmetic applicators often use LSR due to its soft and gentle properties.
Its odorless and tasteless nature, along with the ability to maintain flexibility over a wide range of temperatures, makes LSR a preferred choice in these applications.
d. Electronics and Electrical Components
The electronics industry relies on LSR for applications where insulating properties and thermal stability are crucial, such as:
- Keypads and Buttons: It is commonly used to manufacture flexible keypads and buttons, providing a soft touch and durability.
- Encapsulation and Potting: It is used to protect electronic components from moisture, dust, and vibrations.
- LED Lenses: Transparent grades of LSR are used in the production of LED lenses due to their clarity and ability to withstand high temperatures.
These properties help enhance the longevity and reliability of electronic devices, especially in challenging environments.
4. Benefits
LSR offers several advantages that make it a sought-after material for various applications:
a. Heat and Cold Resistance
LSR can withstand a broad temperature range, from -50°C to 200°C (-58°F to 392°F), without losing its mechanical properties. This makes it suitable for applications that require thermal stability, such as automotive and kitchenware.
b. Biocompatibility and Safety
LSR is highly biocompatible and does not cause adverse reactions when in contact with skin or body tissues. It is hypoallergenic and resistant to microbial growth, making it ideal for medical devices and infant care products.
c. Flexibility and Durability
Even after repeated bending and stretching, LSR maintains its shape and strength. Its durability ensures that it can withstand physical stress, making it suitable for products like seals, gaskets, and wearable devices.
d. Chemical and UV Resistance
LSR is resistant to a wide range of chemicals, including oils, solvents, and cleaning agents. Additionally, it is resistant to UV radiation, making it suitable for outdoor applications where exposure to sunlight is a concern.
e. Precision in Molding
The injection molding process allows it to produce complex shapes and small parts with tight tolerances. This makes it ideal for manufacturing components with intricate geometries that would be difficult or impossible with other materials.
f. Ease of Sterilization
LSR can be sterilized using various methods, including autoclaving, steam, gamma radiation, and ethylene oxide. This makes it an excellent choice for reusable medical and food-grade products.
Conclusion
Liquid Silicone Rubber (LSR) is a versatile material that has transformed manufacturing processes across multiple industries. Its unique properties—such as heat resistance, flexibility, biocompatibility, and ease of molding—make it a preferred choice for applications ranging from medical devices to automotive components and consumer goods. The ability to produce intricate, high-precision parts through injection molding further enhances its appeal. With its broad range of uses and benefits, LSR continues to play a critical role in advancing technology and improving product quality in numerous fields.