In the rapidly evolving automotive applications, Liquid Silicone Rubber (LSR) and LSR-Multishot technologies are revolutionizing the way components are manufactured. Known for their durability and flexibility, these materials offer exceptional resistance to extreme conditions, making them ideal for automotive applications. With advancements in LSR-Multishot, manufacturers can now integrate various materials into a single component, enhancing performance and reducing production costs.
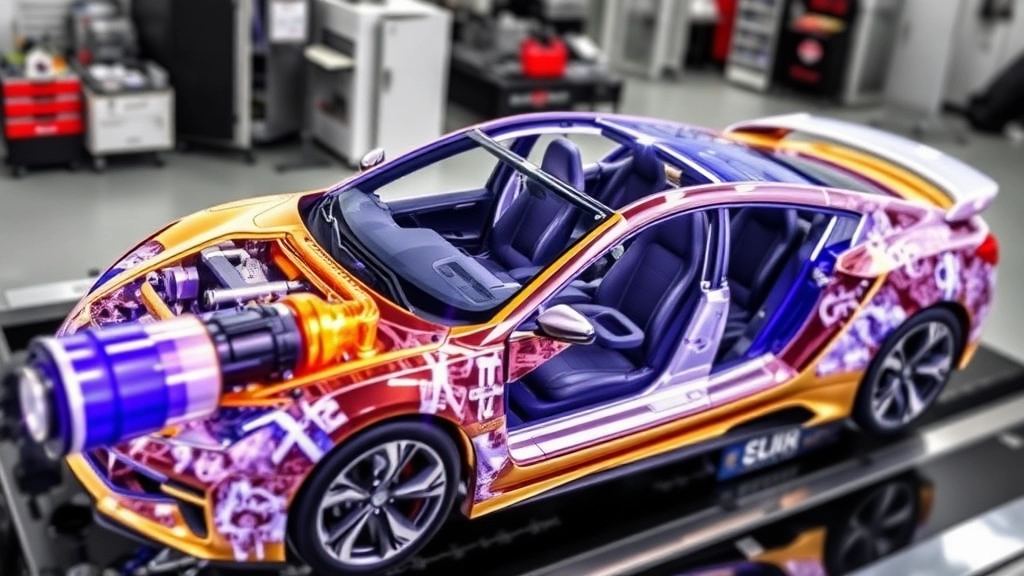
Our exploration of LSR and LSR-Multishot in automotive applications delves into their unique properties, highlighting their ability to withstand harsh environments while providing design flexibility and cost efficiency. From seals and gaskets to connectors and insulators, these technologies are paving the way for more reliable and sustainable automotive components. Join us as we uncover the future prospects and challenges of implementing these groundbreaking technologies in the automotive sector.
Review of LSR (Liquid Silicone Rubber) and LSR-Multishot Technologies
Intro to LSR
Liquid Silicone Rubber (LSR) is a functional material recognized for its outstanding buildings, making it extremely suitable for auto applications. LSR is a two-part platinum-cured elastomer that can be injected right into mold and mildews, enabling the production of complex and specific elements. Its usage in the automotive market has actually grown significantly due to its sturdiness, flexibility, and resistance to severe temperatures.
Characteristic of LSR
LSR supplies numerous key buildings that are particularly beneficial for vehicle production:
- High thermal stability: LSR can hold up against temperature levels varying from -60 ° C to 200 ° C. Excellent electric insulation: Ideal for parts that call for electrical seclusion.
- Resistance to chemicals and UV radiation: Ensures longevity and performance in harsh settings.
- Biocompatibility: Safe for usage in applications that enter contact with human skin.
Introduction to LSR-Multishot Technology
LSR-Multishot innovation is an advanced production procedure that integrates various products in a solitary molding cycle. This procedure allows for the integration of LSR with various other thermoplastics, creating elements with numerous material buildings. The LSR-Multishot process entails the consecutive shot of various materials right into the exact same mold and mildew, causing a natural and durable final product.
Advantages of LSR-Multishot
The usage of LSR-Multishot modern technology in auto applications supplies numerous advantages:
- Enhanced style flexibility: Enables the production of complicated geometries and intricate designs.
- Enhanced part efficiency: Combines the very best buildings of different products.
- Decreased setting up time: Integrates several parts right into a single element, minimizing the demand for additional setting up.
- Price efficiency: Reduces worldly waste and reduces production prices.
Automotive Applications
LSR and LSR-Multishot modern technologies are widely utilized in the automobile market for various applications, including:
Component | Product | Advantages |
---|---|---|
Seals and gaskets | LSR | Offers excellent securing homes and longevity |
Connectors and insulators | LSR | Guarantees electric insulation and resistance to ecological variables |
Keypads and switches | LSR-Multishot | Offers tactile feedback and combination with other materials |
Real estates and covers | LSR-Multishot | Integrates durability with visual appeal |
Trick Benefits of LSR and LSR-Multishot in Automotive Applications
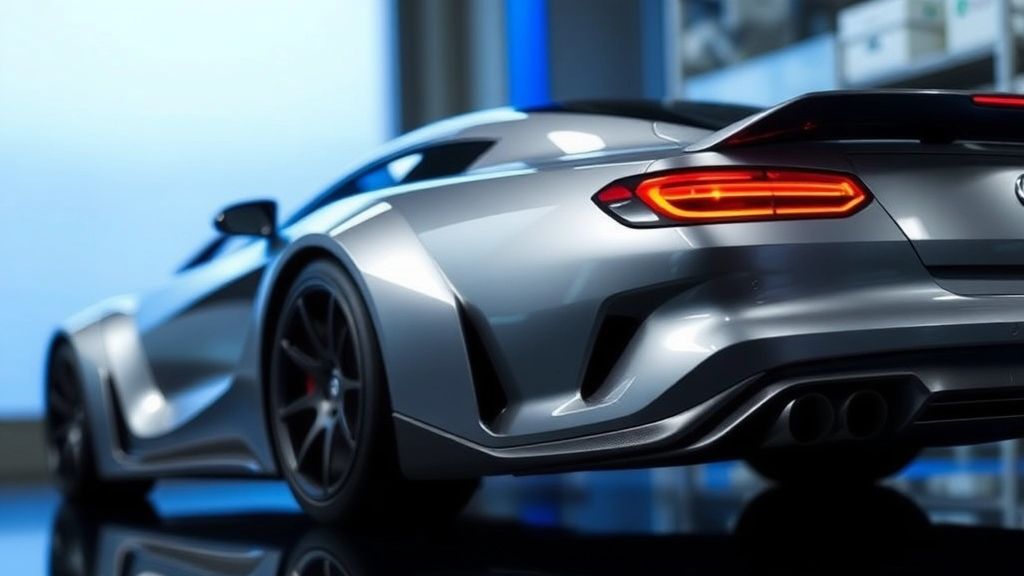
Enhanced Durability and Performance
Among the main advantages of LSR (Liquid Silicone Rubber) and LSR-Multishot technologies in automobile manufacturing is the boosted sturdiness and performance of the components generated. LSR is understood for its superb resistance to severe temperature levels, UV light, and different chemicals, making it an excellent material for auto components that are subjected to severe atmospheres. In addition, LSR keeps its mechanical homes over a large temperature variety, guaranteeing regular performance and longevity.
Layout Flexibility
Making use of LSR and LSR-Multishot innovations permits substantial style adaptability. LSR can be formed into complicated shapes and complex styles, which is specifically advantageous for producing components with detailed functions. The LSR-Multishot process further improves this capacity by allowing the combination of numerous materials right into a single part, allowing for the production of multifunctional parts that combine the most effective properties of each material utilized.
Price Efficiency
Applying LSR and LSR-Multishot technologies can set you back financial savings in vehicle manufacturing. The high precision of LSR molding minimizes product waste and decreases the requirement for second procedures, such as cutting or assembly. Moreover, the capacity to create multi-material parts in a single molding cycle with LSR-Multishot modern technology improves the manufacturing process, reducing labor expenses and production time.
Boosted Safety and Comfort
LSR and LSR-Multishot technologies add to enhanced safety and convenience in auto applications. LSR’s exceptional securing properties and flexibility make it ideal for producing gaskets, seals, and other elements that prevent leakages and ensure the proper functioning of numerous automobile systems. Additionally, the soft-touch surfaces and ergonomic designs attainable with LSR-Multishot innovation enhance the comfort and user experience for lorry residents.
Ecological Benefits
The ecological advantages of using LSR and LSR-Multishot innovations in automotive production are notable. LSR is a sustainable material that can be reused, and its long solution life lowers the demand for frequent replacements, consequently lessening waste. In addition, the efficient manufacturing procedures connected with LSR and LSR-Multishot innovations lead to lower power usage and decreased carbon discharges, contributing to an extra sustainable vehicle market.
Usual Automotive Components Made with LSR and LSR-Multishot
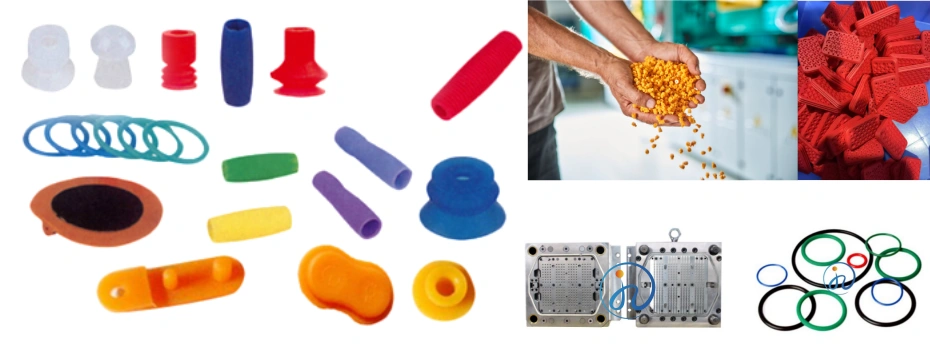
Seals and Gaskets
One of the most prevalent applications of LSR and LSR-Multishot technologies in the auto industry is the manufacturing of seals and gaskets. These parts are essential for avoiding leakages and ensuring the honesty of numerous vehicle systems. The fundamental versatility and longevity of LSR make it a perfect product for these applications.
Connectors and Insulators
In the world of auto electronics, adapters and insulators made from LSR and LSR-Multishot are extremely valued. These parts profit from the product’s outstanding electrical insulation properties, resistance to heat, and capability to maintain performance under harsh ecological conditions. This ensures dependable connection and security of electronic circuits.
Lights Components
Automotive light systems usually include LSR for lenses and real estate parts. The transparency and UV resistance of LSR adds to the longevity and performance of front lights, taillights, and other lighting components. In addition, LSR-Multishot modern technology enables for the integration of several products in a solitary component, improving capability and style flexibility.
Exterior And Interior Trim
LSR and LSR-Multishot are additionally used in the production of various interior and external trim components. These consist of buttons, knobs, and various other tactile elements that profit from the soft-touch feel of LSR. In addition, the product’s resistance to wear and tear ensures that these components keep their appearance and functionality over time.
Hoses and Tubing
The automotive market counts on LSR to manufacture tubes and tubing made use of liquid transfer systems. The product’s chemical resistance and adaptability make it suitable for handling a variety of liquids, consisting of oils, coolants, and fuels. LSR-Multishot innovation even more improves these elements by integrating various products to satisfy particular performance needs.