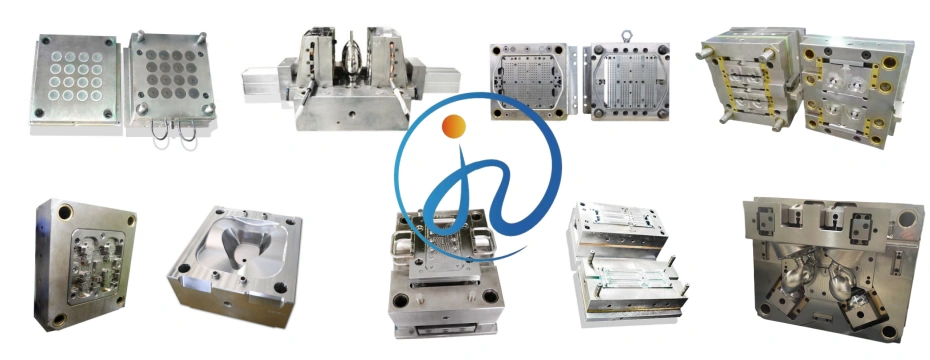
Transformative Effect of Silicone Rubber Tooling Technology
As an expert in the field, I have seen firsthand the transformative effect of silicone rubber tooling technology throughout various markets. This innovation has reinvented the way we approach the development of molds and devices, providing unrivaled versatility, durability, and precision. In this article, we will delve into the vital elements of silicone rubber tooling technology, exploring its fundamental concepts, historical development, and the essential aspects that make it a preferred choice for many professionals.
Revolutionizing Industries
Silicone rubber tooling technology is revolutionizing industries with its exceptional properties. From its remarkable flexibility and heat resistance to its chemical stability and precision, this technology offers unparalleled advantages. We will explore its applications across automotive, aerospace, medical, consumer electronics, and more, while also providing a step-by-step guide to the tooling process and best practices for maintenance. Join us as we uncover the endless possibilities and future advancements of silicone rubber tooling technology.
Introduction to Silicone Rubber Tooling Technology
As an expert in the field, I have seen firsthand the transformative effect of silicone rubber tooling technology throughout various markets. This innovation has reinvented the way we come close to the development of molds and devices, providing unrivaled versatility, longevity, and precision. In this area, we will delve into the vital elements of silicone rubber tooling modern technology, exploring its fundamental concepts, historical advancement, and the essential aspects that make it a recommended option for several specialists.
Essential Principles of Silicone Rubber Tooling
Silicone rubber tooling involves using silicone-based materials to develop molds and devices for manufacturing procedures. The primary particular that sets silicone rubber in addition to various other products is its unique mix of flexibility, warm resistance, and chemical security. These residential or commercial properties make it optimal for developing in-depth and long-lasting molds that can endure the roughness of repeated usage.
Historic Development
The growth of silicone rubber tooling innovation can be traced back to the mid-20th century when the need for even more flexible and resistant mold-making products came to be evident. Originally used in aerospace and auto industries, silicone rubber rapidly gained appeal due to its capacity to duplicate complex details and its resistance to extreme temperature levels. Over the decades, innovations in silicone chemistry and production techniques have actually even more boosted its efficiency, making it easily accessible to a broader variety of applications.
Secret Factors of Silicone Rubber Tooling
Several factors contribute to the performance and appeal of silicone rubber tooling modern technology:
Factor | Description |
---|---|
Flexibility | Permits for easy elimination of complex forms without damaging the mold. |
Heat Resistance | With the ability to catch great information, it is excellent for accuracy tooling. |
Chemical Stability | Resistant to a variety of chemicals, ensuring long life and toughness. |
Information Replication | With the ability to catch great information, it excellent for accuracy tooling. |
By understanding these basic principles and historical context, we can better appreciate the significant duty that silicone rubber tooling innovation plays in modern production and its capacity for future advancements.
Key Advantages of Using Silicone Rubber in Tooling
Remarkable Flexibility and Durability
One of the main advantages of silicone rubber tooling technology is its phenomenal versatility and durability. Silicone rubber can stretch without damaging, which permits it to create complex and comprehensive mold and mildew. This adaptability ensures that the tooling can endure repeated use without shedding its shape or honesty.
Heat Resistance
One more significant benefit of utilizing silicone rubber in tooling is its heat resistance. Silicone rubber can endure extreme temperatures ranging from -60 ° C to 250 ° C (-76 ° F to 482 ° F). This makes it excellent for applications that entail high warm, such as in the auto and aerospace sectors.
Chemical Resistance
Silicone rubber displays superb resistance to a variety of chemicals, consisting of acids, bases, and solvents. This property makes certain that the tooling remains untouched by numerous materials it may come into call with throughout the manufacturing procedure, consequently prolonging its life span and preserving its performance.
Non-Stick Properties
The intrinsic non-stick residential or commercial properties of silicone rubber make it a superb choice for tooling applications. This particular permits the simple release of components from the mold and mildew, lowering the threat of damage to the parts and the mold itself. It likewise minimizes the requirement for extra release representatives, improving the manufacturing procedure.
Accuracy and Accuracy
Silicone rubber tooling’s modern technology provides high precision and precision in mold making. The material’s capability to catch fine details ensures that the end product very closely matches the original style. This accuracy is especially essential in markets such as medical tool production, where precise specifications are critical.
Economical and Time-Efficient
Making use of silicone rubber in tooling can be both cost-efficient and time-efficient. The material’s sturdiness lowers the demand for constant replacements, and its ease of usage can shorten the mold-making procedure. These variables add to lower production expenses and faster turnaround times, profiting manufacturers and end-users alike.
Applications of Silicone Rubber Tooling in Various Industries
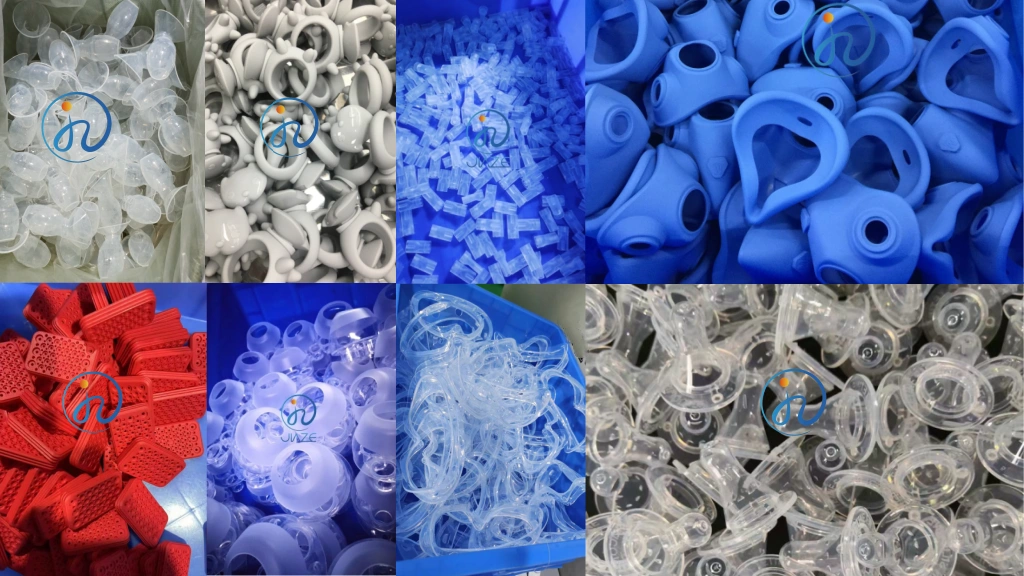
Automotive Industry
Silicone rubber tooling innovation plays a critical duty in the auto sector. It is extensively used for producing prototypes and small-batch production components. The material’s superb thermal security and resistance to chemicals make it ideal for manufacturing gaskets, seals, and hoses that should withstand harsh environments. Additionally, silicone rubber tooling is utilized in the manufacturing of personalized indoor parts, ensuring high precision and high quality.
Aerospace Industry
In the aerospace industry, silicone rubber tooling is critical for establishing lightweight yet sturdy parts. The capability to generate and get rid of complicated geometries and great details is important for aerospace applications. Silicone rubber’s resistance to severe temperatures and its insulating properties make it appropriate for producing mold and mildew for turbine blades, seals, and various other vital parts.
Clinical Industry
The medical industry leverages silicone rubber tooling for its biocompatibility and sanitation capabilities. This technology is used to manufacture medical gadgets, prosthetics, and medical instruments. The accuracy and integrity of silicone rubber molds guarantee that medical elements satisfy rigorous governing requirements. Furthermore, the versatility of silicone rubber enables the creation of intricate forms required for custom clinical options.
Customer Electronics
Silicone rubber tooling is essential in the customer electronic devices field. It is made use of to produce elements such as keypads, gaskets, and rooms. The product’s toughness and flexibility make it ideal for protecting sensitive digital elements from ecological aspects. Moreover, silicone rubber’s capacity to create thorough and elaborate layouts makes certain high-grade surfaces for customer products.
Food and Beverage Industry
In the food and drink sector, silicone rubber tooling is used to create molds for food-grade products. The safe and heat-resistant homes of silicone rubber make it suitable for generating baking molds, ice trays, and cooking area utensils. The material’s simplicity of cleansing and maintenance additionally adds to its extensive usage in this industry.
Industrial Manufacturing
It is extensively used in commercial manufacturing for creating prototypes, custom-made components, and production tools. The flexibility of silicone rubber enables rapid prototyping and the production of high-precision elements. Industries such as automobile, aerospace, and customer products gain from the ability to create little batches of parts effectively and cost-effectively.
Industry | Applications | Secret Benefits |
---|---|---|
Automotive | Gaskets, seals, hoses, personalized inside elements | Thermal security, chemical resistance, high accuracy |
Aerospace | Wind turbine blades, seals, complex geometries | Light-weight, resilient, extreme temperature resistance |
Clinical | Clinical devices, prosthetics, medical tools | Biocompatibility, sanitation capabilities, accuracy |
Consumer Electronics | Keypads, gaskets, units | Longevity, adaptability, in-depth designs |
Food and Beverage | Cooking molds, ice trays, cooking area utensils | Non-toxic, heat-resistant, very easy to clean |
Industrial Manufacturing | Models, custom components, production devices | Convenience, rapid prototyping, high accuracy |
Step-by-Step Process

Prep Work and Material Selection
The initial stage entails detailed prep work and mindful options of materials. It is vital to select the best kind of silicone rubber that matches the details needs of the job. Variables such as firmness, tensile strength, and thermal stability have to be thought about to ensure optimal performance.
Mold Design and Fabrication
When the material is selected, the next step is developing the mold and mildew. This involves creating a detailed plan that describes the measurements and functions of the mold. Advanced software program devices are often utilized to create accurate and reliable molds. Complying with the design phase, the mold and mildew are fabricated using techniques such as CNC machining or 3D printing, relying on the complexity and requirements of the project.
Blending and Degassing the Silicone Rubber
After the mold is prepared, the silicone rubber should be mixed extensively. This procedure entails incorporating the base silicone with a healing representative in the proper ratio. Blending must be done carefully to guarantee a uniform combination. As soon as blended, the silicone rubber is subjected to a degassing process to remove any type of trapped air bubbles, which can endanger the integrity of the end product.
Putting and Curing
The degassed silicone rubber is after that very carefully poured right into the prepared mold and mildew. It is vital to pour the mixture slowly and continuously to prevent introducing air bubbles. After pouring, the mold is placed in a controlled environment where the silicone rubber undergoes healing. The curing time and temperature level can vary based on the sort of silicone made use of and the preferred properties of the end product.
Demolding and Finishing
As soon as the treating process is complete, the mold is opened, and the silicone rubber part is meticulously removed. This step, referred to as demolding, calls for precision to prevent harming the component or the mold. After demolding, the component may undertake added finishing processes such as trimming, fining sand, or coating to accomplish the preferred surface area top quality and measurements.
Top Quality Control and Inspection
The final step in the process is extensive quality assurance and examination. Each component is examined for issues, dimensional precision, and general top quality. Advanced examination methods, consisting of aesthetic examination and dimension tools, make certain that the parts meet the specified requirements and are all set for their designated application.
Ideal Practices for Maintaining Silicone Rubber Tooling Equipment
It is important for ensuring longevity, performance, and efficiency. Appropriate upkeep not only expands the life of the tools but likewise guarantees constant top quality in the production procedure. Below are some of the best techniques to comply with:
Regular Cleaning
Normal cleansing is important to prevent the build-up of deposits that can affect the quality. Use ideal cleaners that do not deteriorate the silicone material. Avoid using unpleasant materials that can cause scratches or other damages.
Inspection and Monitoring
Constant assessment of the tooling tools aids in identifying damage early. Look for signs of wear such as cracks, staining, or deformation. Keeping track of the devices’s efficiency can likewise aid in finding any kind of irregularities that may show the need for maintenance.
Lubrication
Appropriate lubrication of relocating components is vital to lower rubbing and wear. Use lubricants that work with silicone rubber to stay clear of chemical responses that can deteriorate the product. Ensure that the lubricant is applied evenly and in the correct amounts.
Temperature Control
The devices must be run within the recommended temperature level ranges. Extreme heat can trigger the silicone to break down, while low temperatures can make it breakable. Use temperature surveillance gadgets to ensure that the equipment is always within the secure operating variety.
Storage space Conditions
When not in use, dry atmosphere. Stay clear of direct exposure to guide sunlight and extreme temperature levels. Appropriate storage space problems aid in keeping the product’s homes and prolonging its lifespan.
Documents and Training
Keep comprehensive documents of all upkeep activities, including cleaning timetables, assessments, and repairs. This documentation can help in recognizing patterns and preparing for future upkeep activities. Additionally, ensure that all personnel involved in the upkeep of silicone rubber tooling equipment are appropriately trained and familiar with the most effective techniques.
Upkeep Activity | Frequency | Advised Tools/Materials |
---|---|---|
Cleaning | Weekly | Non-abrasive cleaner, soft cloth |
Inspection | Month-to-month | Visual evaluation tools, magnifying glass |
Lubrication | As required | Silicone-compatible lubricants |
Temperature level Monitoring | Constant | Temperature level sensing units |
Storage space | When not in usage | Tidy, completely dry storage space location |
Documents | Continuous | Upkeep logs, training documents |
By sticking to these finest methods, you can ensure that your silicone rubber tooling equipment remains in optimal condition, thus improving the performance and top quality of your manufacturing procedures.
FAQs on Silicone Rubber Tooling Technology
What is Silicone Rubber Tooling Technology?
Silicone rubber tooling technology involves using silicone-based materials to create molds and tools for manufacturing processes. This technology is known for its flexibility, durability, and precision, making it a preferred choice across various industries.
What are the key advantages of using silicone rubber in tooling?
Silicone rubber offers several advantages, including exceptional flexibility, high-temperature resistance, chemical resistance, non-stick properties, precision and accuracy, and cost-effectiveness. These properties make it ideal for creating detailed and durable molds.
What industries benefit from silicone rubber tooling technology?
Silicone rubber tooling is used in several industries, including automotive, aerospace, medical, consumer electronics, food and beverage, and industrial manufacturing. Each industry leverages the unique properties of silicone rubber to meet specific application requirements.
How has silicone rubber tooling technology evolved over time?
The technology has evolved significantly since its inception in the mid-20th century. Initially used in aerospace and automotive industries, advancements in silicone chemistry and manufacturing techniques have expanded its applications to various other sectors.
What are the fundamental principles of silicone rubber tooling?
The primary principles include elasticity, heat resistance, and chemical stability. These characteristics allow for the creation of molds that can withstand repeated use and capture intricate details, making them ideal for precision tooling.
What is the process of silicone rubber tooling?
The process involves several steps: preparation and material selection, mold design and fabrication, mixing and degassing the silicone rubber, pouring and curing, demolding and finishing, and quality control and inspection. Each step is crucial for ensuring the quality and durability of the final product.
How do you maintain silicone rubber tooling equipment?
Maintaining the equipment involves regular cleaning, frequent inspection, proper lubrication, temperature control, appropriate storage conditions, and thorough documentation and training. These practices help extend the life of the equipment and ensure consistent production quality.
What are the key factors contributing to the effectiveness of silicone rubber tooling?
Factors such as elasticity, heat resistance, chemical stability, and detail replication contribute to the effectiveness of silicone rubber tooling. These properties ensure that the molds are durable, precise, and capable of capturing fine details.
Can silicone rubber tooling be used for high-temperature applications?
Yes, silicone rubber can withstand extreme temperatures ranging from -60°C to 250°C (-76°F to 482°F), making it suitable for high-temperature applications in industries like automotive and aerospace.
What are the common applications of silicone rubber tooling in the medical industry?
In the medical industry, silicone rubber tooling is used to manufacture medical devices, prosthetics, and surgical instruments. Its biocompatibility, sterilization capabilities, and precision make it ideal for these applications.
Why is silicone rubber preferred for creating molds in the food and beverage industry?
Silicone rubber is non-toxic, heat-resistant, and easy to clean, making it suitable for creating food-grade products like baking molds, ice trays, and kitchen utensils. Its properties ensure safety and convenience in food-related applications.
How does silicone rubber tooling improve efficiency and cost-effectiveness in manufacturing?
The durability of silicone rubber reduces the need for frequent replacements, and its ease of use can shorten the mold-making process. These factors contribute to lower production costs and faster turnaround times, benefiting manufacturers and end-users alike.
For more detailed information on specific aspects of silicone rubber tooling technology, please refer to the relevant sections in the article above.