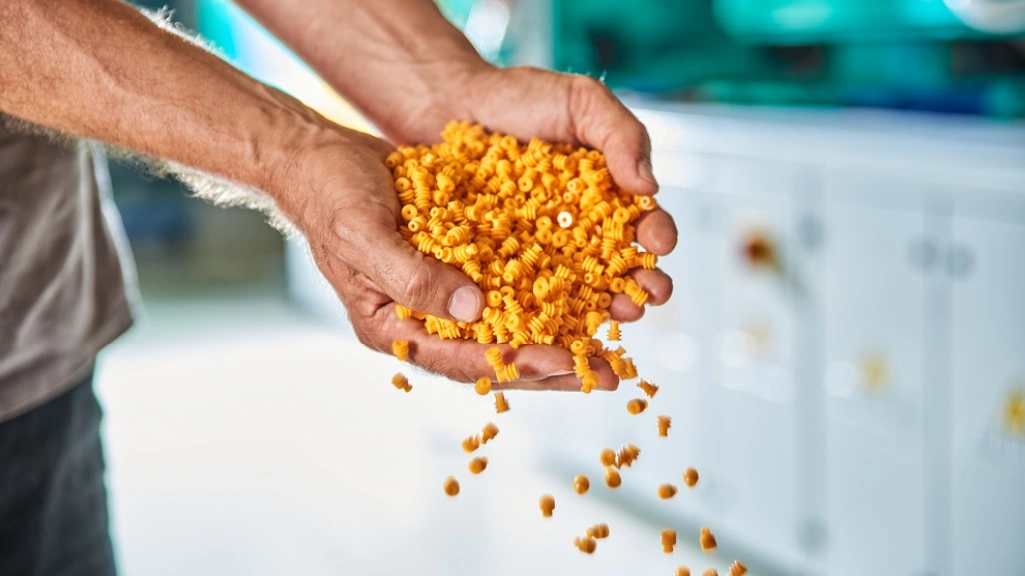
Liquid Silicone Rubber (LSR) is a versatile material used across many industries, from medical devices to automotive components. However, several misconceptions persist about its properties and uses. Let’s debunk some of the most common ones:
1. Misconception: Liquid Silicone Rubber is the same as regular silicone.
- Reality: LSR is a specific type of silicone with a unique liquid consistency before curing, unlike traditional silicone rubbers that come in solid or paste forms. LSR undergoes a different manufacturing process (injection molding), allowing for more complex designs and better precision.
2. Misconception: LSR is only used in medical devices.
- Reality: While LSR is common in the medical industry due to its biocompatibility, it is also widely used in electronics, automotive components, kitchenware, and consumer goods.
3. Misconception: LSR can’t withstand high temperatures.
- Reality: LSR can endure a broad temperature range, from as low as -50°C to as high as 200°C or more, making it ideal for both extreme cold and heat applications.
4. Misconception: LSR products are prone to tearing.
- Reality: LSR has excellent tear resistance, especially when formulated for durability. It is commonly used in products where flexibility and resilience are critical, such as seals, gaskets, and membranes.
5. Misconception: LSR is not environmentally friendly.
- Reality: LSR is considered eco-friendly compared to many other rubbers and plastics. It is free of harmful additives, highly durable, and often recyclable, reducing overall environmental impact.
6. Misconception: LSR molds are too expensive and impractical for small production runs.
- Reality: Though initial tooling costs can be high, advances in mold-making technology have made LSR injection molding more cost-effective, even for smaller production runs. Plus, LSR’s long mold life offers long-term savings.
7. Misconception: LSR has poor chemical resistance.
- Reality: LSR is highly resistant to many chemicals, including water, acids, bases, and oils. Its chemical stability makes it suitable for many industrial and consumer applications.
8. Misconception: LSR products are always transparent or translucent.
- Reality: While LSR is naturally translucent, it can be pigmented in various colors without losing its mechanical properties. Colored LSR is often used in consumer products for aesthetics.
9. Misconception: LSR can’t be used in electrical applications.
- Reality: LSR is an excellent electrical insulator, making it ideal for use in electrical and electronic components. It is also resistant to arcing and corona discharge.
10. Misconception: LSR is difficult to bond with other materials.
- Reality: With proper surface treatment and primers, LSR can be bonded to a variety of substrates, including metals and plastics, broadening its application range in multi-material assemblies.